1. INTRODUCTION
Over the past few years, cloud computing and cloud-based technologies, software, and services have been increasing. According to a new forecast from International Data Corporation, it is estimated that public cloud services spending will grow to more than $127 billion in 2018 as the market enters a critical innovation stage (Gens, Reference Gens2016). For example, the advent of cloud-based software and services in the field of digital design and manufacturing has begun to transform the way in which engineering companies around the world perform engineering design, manufacturing, and production activities. As engineering design and manufacturing become increasingly digital, the digital thread that integrates cloud computing, physical objects, sensor networks, and the Internet has the potential to significantly reduce product time to market and cost associated with product development and manufacturing as well as improve product quality and reliability (Bruner, Reference Bruner2013; Brettel et al., Reference Brettel, Friederichsen, Keller and Rosenberg2014; Zhang et al., Reference Zhang, Li, Liu, Xie and Schaefer2014, Reference Zhang, Liu, Jiang and Chen2015).
With industry increasingly embracing cloud computing in the field of digital product creation, cloud-based design and manufacturing (CBDM) has become one of the key pillars to enable Industry 4.0, Industrial Internet, Internet of Things, and Cyber-Physical Manufacturing/Production Systems (Wu et al., Reference Wu, Thames, Rosen and Schaefer2012; Schaefer, Reference Schaefer2014). Due to its key characteristics, CBDM has the potential to serve as a backbone of the industrial digital thread because it allows for a variety of modeling, simulation, and manufacturing software packages and services to be connected on demand. CBDM enables scalable, ubiquitous, seamless, and instant access to remote advanced digital design and manufacturing resources including, among others, finite element analysis and computational fluid dynamics (CFD) software packages as well as high-performance computing (HPC) resources for simulation (Wu et al., Reference Wu, Rosen, Wang and Schaefer2015). In a broader sense, CBDM can be used to build entire highly customized and agile information and communication technology infrastructures that integrate application software, digital models, sensors, machines, and big data analytics applications for product creation.
More specifically, the unique capabilities and benefits of CBDM are as follows (Wu et al., Reference Wu, Greer, Rosen and Schaefer2013):
• Enhanced functionality: CBDM allows users to solve large-scale and complex design and engineering analysis problems (e.g., finite element analysis, computational fluid dynamics, optimization, visualization, and photorealistic rendering) that typically require high-performance processors and very large memory.
• Anytime, anywhere access: CBDM enables users to acquire access to any computer-aided design/computer-aided engineering/computer-aided manufacturing (e.g., ANSYS and AutoCAD) software packages and state-of-the-art HPC computing infrastructures (e.g., central processing unit cores, graphics processing units, memory, and high-speed interconnects) via a web portal and/or application program interfaces anytime, anywhere.
• Cost efficiency: CBDM fundamentally changes the way manufacturers implement digital design and manufacturing from a business perspective by offering various pricing models such as pay-per-use, subscription, and auction-based pricing plans. For example, AutoCAD and ANSYS implemented the subscription pricing model by charging a fixed price in advance for a predefined period of time (e.g., per month or per year).
• Secure and high volume data storage: CBDM provides manufacturers with reliable, secure, scalable, and economical storage of massive static and dynamic data. The advantage of cloud storage is that it delivers high-performance, low-latency communication for input/output intensive workloads such as high-speed data collection and processing.
• High flexibility: CBDM enables users to scale up and down computing capacity on demand and transform dedicated HPC clusters into flexible HPC clouds that can be shared and adapted for rapidly changing customer requirements through private, hybrid, and public clouds.
• High throughput: CBDM can significantly increase the utilization of computing resources as opposed to dedicated on premise services by allowing globally dispersed engineering teams to perform complex engineering analysis and simulations concurrently and collaboratively.
The objective of this paper is to provide an overview of the cloud-based design and manufacturing-related software and services that have already become readily available and thus to serve as a technology guide for decision makers in their efforts to select suitable cloud-based resources as alternatives to existing in-house resources. Key gaps in capabilities and research needs are also identified. Toward this end, a repository of existing cloud-based software and services as well as service providers that support the various phases of the product creation process has been compiled and is presented. Specifically, we analyze the key capabilities and benefits of existing cloud-based software packages and services available in the market.
The remainder of the paper is organized as follows: Sections 2, 3, 4, and 5 present cloud-based software and services for engineering design, engineering analysis, manufacturing, and production, respectively. Section 6 provides directions for future research in the field of cloud-based design, engineering analysis, manufacturing, and production. Section 7 provides conclusions and the contributions of this research.
2. ENGINEERING DESIGN ON THE CLOUD
Table 1 lists the primary phases of a typical engineering design processes, including product planning, conceptual design, embodiment design, and detail design. The first phase, product planning, refers to a process of identifying market or customer requirements that define the product concept and associated product features. The essence of product planning is to study the market, identify the preferences and requirements of customers and users, and define associated product life cycles. Traditional tools for product planning include customer surveys and/or market research questionnaires, which could be very time consuming and inaccurate. In the context of contemporary 21st-century product development, Salesforce Market Cloud is a provider of cloud-based digital marketing automation and analytics software and services. Salesforce Market Cloud delivers market analytics using a dynamic visualization engine and massively parallel computing infrastructure. However, Salesforce Market Cloud cannot yet automatically collate customer reviews from online review sites and social media platforms such as Amazon, Google, Twitter, Epinions, CNET, Sazze, Retrevo, or Social.com. In the second design phase, conceptual design, product ideas are generated, evaluated, and selected. Traditional tools for conceptual design include brainstorming, reasoning, modeling, representation, the use of morphological matrices, Pugh's method, and other aids of decision making. Although decisions made at the conceptual design stage have significant influence on costs, performance, and reliability of a product, to date only few cloud-based tools for conceptual design support exist due to a lack of mechanisms and techniques for automating product ideation. The third and fourth phases of traditional systematic engineering design are embodiment design and detail design in which system configuration, layouts, and geometries are generated. The natural choice of tool for both embodiment and detail design has been and still is the utilization of computer-aided design (CAD) systems. Due to the high degree of automation and digitalization inherent to the embodiment and detail design phases, various cloud-based CAD tools and services for low-, medium-, and high-end customers have been developed. Table 1 represents a snapshot of the current state. It is by no means meant to be complete or conclusive. Rather, we acknowledge that new CBDM solutions and services are being developed as we conduct this survey. More detailed discussions of the existing cloud-based tools, software, and services as well as their key capabilities and benefits follow in subsequent sections. Table 2 lists the leading CAD services on the cloud, service providers, deployment models, key capabilities and features, and cloud infrastructure providers.
Table 1. Cloud-based tools and services supporting the product creation process

Table 2. CAD services on the cloud

Note: See Distler (Reference Distler2015), IntelliCAD (2015), Onshape (2015), Siemens (2015b), SOLIDWORKS (2015), and Windchill (2015).
Autodesk 360 is a cloud computing platform that provides cloud-based design services that enable engineers to conduct engineering design and share digital documents anytime, anywhere through cloud computing platforms. The key capabilities and benefits of AutoCAD 360 include
• cloud-based data management using cloud storage services such as Dropbox, Box, Egnyte, and Buzzsaw and
• remote access to two-dimensional (2-D) drawings in the DWF and DWG formats on multiple devices using a web browser, smart phone, tablet, and desktop computer.
As shown in Figure 1, the free version of AutoCAD 360 enables users to view drawings; draw simple lines, rectangles, and circles; save drawings with AutoCAD 360 or third-party cloud storage; and move, scale, rotate, erase, and copy objects via a web browser or a mobile device. The Pro version of AutoCAD 360 offers more advanced functionality, including creating new drawings, drawing arcs and arrows, and advanced layer management.

Fig. 1. AutoCAD 360 interface (Dobrzynski, Reference Dobrzynski2013).
The other cloud-based three-dimensional (3-D) CAD tool offered by Autodesk is Fusion 360. Fusion 360 can run on both Mac and Windows operating systems. The key capabilities and benefits of Autodesk Fusion 360 include
• cloud-based rendering,
• cloud-based distributed design,
• cloud-based mobile viewing, and
• cloud-based part libraries.
For example, as shown in Figure 2, Fusion 360 enables users to create smooth and precise surfaces with T-Splines technology or with sketch curves, patches, and extrusions via a web browser. Designers can take advantage of virtually unlimited computing power to create photorealistic and high-resolution images on the cloud.

Fig. 2. AutoCAD Fusion 360 interface (Fusion360, 2015).
PTC PLM Cloud offers cloud-based Creo and Windchill that can accelerate product development and help design teams minimize information technology complexity and cost with a secure cloud infrastructure. PTC PLM Cloud's functionality is equivalent to Windchill PDMLink and ProjectLink. Similar to AutoCAD 360 and Fusion 360, the key features of Creo and Windchill on the cloud include
• cloud-based product data management,
• cloud-based product analytics, and
• cloud data storage.
Both PTC Creo and Windchill offer cloud and on-premise versions. PTC offers three PTC PLM Cloud packages, including standard, premium, and enterprise. The standard package allows for multitenant and preconfigured Windchill and Creo instances that support up to 15 CAD seats. The premium package allows for dedicated virtual PTC Windchill and Creo instances that support customer-specific system configuration with more than 15 CAD seats. Similar to the premium package, the enterprise package allows for dedicated virtual PTC Windchill and Creo instances that support integrations to corporate systems in addition to customer-specific system configuration. PTC Creo is currently only available via Amazon Web Services (AWS) in North America. Figure 3 shows the interface of Willchill on the cloud. PTC Windchill is available through AWS and Microsoft Azure.
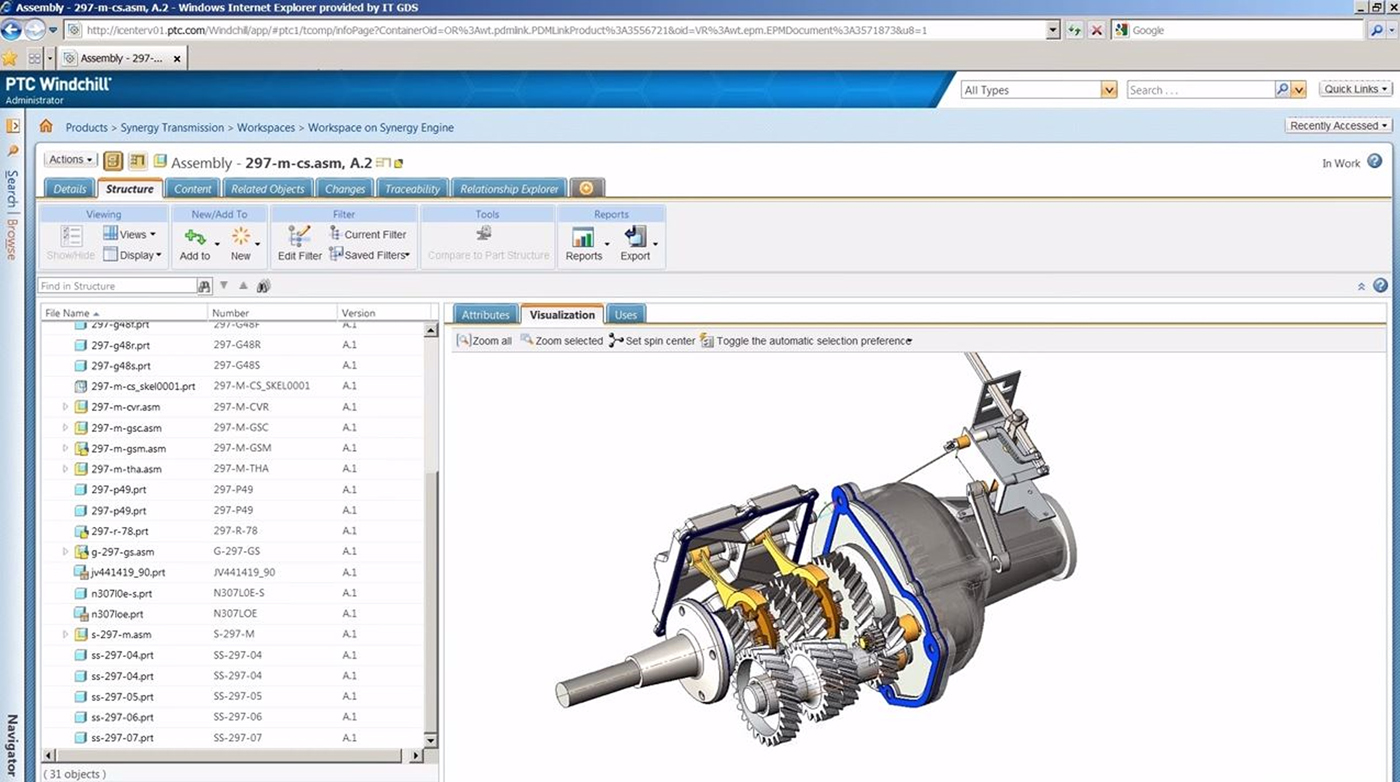
Fig. 3. View and edit three-dimensional model using Willchill on the cloud (Willchill, 2015). Copyright 2015 by PTC, Inc. Reprinted with permission.
Teamcenter developed by Siemens PLM Software is delivered through the Infrastructure as a Service (IaaS) platform. Teamcenter on the cloud enables users to move some or all of their computing infrastructure to a third-party cloud service provider without heavy upfront investments on information and communication technology infrastructure and resources. Currently, Siemens supports Teamcenter on three of the leading cloud service providers: Microsoft Azure, IBM SmartCloud, and AWS. Teamcenter on the cloud provides fast and flexible deployment of virtual Teamcenter environments with the ability to dynamically scale infrastructure up and down based on customers' needs. In addition to Teamcenter, Siemens PLM offers the NX 3-D design software in a private cloud environment by partnering with NVIDIA, as shown in Figure 4. Specifically, with NVIDIA GRID vGPU, Siemens NX enables users to conduct 3-D graphics-intensive applications such as 3-D rendering via virtual desktop infrastructure.

Fig. 4. Cloud-based Siemens NX software using NVIDIA GRID's virtual desktop (Siemens, 2015b). Copyright 2015 by Siemens Product Lifecycle Management Software, Inc. Reprinted with permission.
Dassault Systèmes has developed a portfolio of cloud-based solutions such as cloud-based SOLIDWORKS, CATIA, and SIMULIA via the 3DEXPERIENCE platform. Specifically, the features of SOLIDWORKS on the cloud include CAD animation, revision control, part and assembly modeling, tolerance analysis, CAD library, and interference check. In particular, SOLIDWORKS Conceptual Designer (SWCD) is at present perhaps the only cloud-based concept design tool for the rapid creation, manipulation, and modification of designs for mechanical components. Figure 5 depicts the interface of SWCD on the cloud. Specifically, sketch motion enables designers to evaluate design concepts in the early design phase using trace paths and area sweeps. Deformable 3-D geometry enables designers to conduct instant performance verification for 3-D mechanical components. Mechanism synthesis enables designers to define a dimensioned layout of a mechanism before embodiment design and detail design. Concept management allows designers to easily compare a number of design concepts. Similar to SOLIDWORKS Mechanical concept, SOLIDWORKS Industrial Design (SWID), as shown in Figure 6, is another cloud-based tool available on the 3DEXPERIENCE platform. SWID allows industrial designers to quickly create shapes and forms that will help promote product satisfaction, brand identify, and loyalty using native and imported geometry. SWID provides a virtual sketchpad as well as rendering, surface modeling, and parametric modeling capabilities. In addition to SWCD and SWID, CATIA is also available on the cloud, as shown in Figure 7. The key feature of CATIA on the 3DEXPERIENCE platform is real-time visualization and photorealistic rendering.

Fig. 5. Cloud-based SOLIDWORKS mechanical conceptual (SOLIDWORKS, 2015a). Copyright 2015 by Dassault Systèmes. Reprinted with permission.

Fig. 6. Cloud-based SOLIDWORKS industrial designer interface (SOLIDWORKS, 2015b). Copyright 2015 by Dassault Systèmes. Reprinted with permission.

Fig. 7. CATIA on the SIMULIA cloud-based solutions 3DEXPERIENCE platform (CATIA, 2015).
Onshape is a cloud-based CAD system developed for collaborative design. As shown in Figure 8, Onshape can be run in a web browser on any mobile devices on the Windows, Mac, and Linux operating systems. The key capabilities and benefits of Onshape include
• the ability to modify a model simultaneously by several users,
• version control,
• WebGL rendering, and
• data management.

Fig. 8. Onshape on the cloud (Onshape, 2015a).
Specifically, Onshape claims that the architecture of the Onshape system is significantly different from traditional CAD systems in which users work on files. In the Onshape system, users do not work on files but on compound documents, which are stored on the cloud as database entities. These database entities consist of a part or assembly. In addition, users do not need to be concerned about version control anymore. Another unique characteristic of Onshape is that it enables multiple users to create new features on existing 3-D models or modify existing features. A more important feature is that Onshape is developed using WebGL, which is a JavaScript application program interface for rendering interactive 3-D graphics via a web browser. WebGL is widely supported by various web browsers such as Mozilla Firefox, Google Chrome, Safari, and Internet Explorer.
GrabCAD, acquired by Stratasys in 2014, was founded in 2009 with the goal of building an online community for mechanical engineers to manage and share CAD models. Users can upload and download 3-D files from a free, open-source CAD library created by GrabCAD. The GrabCAD library has more than 910,000 open-source CAD models. GrabCAD released Workbench, which is a free cloud-based collaboration tool that enables multiple users to view and edit the same CAD models simultaneously. Workbench is hosted on Amazon Simple Storage Service. Particularly, Workbench is completely free. There are no limits on data storage, number of projects, and number of users. In addition, GrabCAD provides 3-D model interrogation, inspection, and visualization within the Workbench by partnering with Siemens' Parasolid software. Figure 9 shows the interface of GrabCAD on the cloud.

Fig. 9. GrabCAD on the cloud (GrabCAD, 2015).
3. ENGINEERING ANALYSIS ON THE CLOUD
Computer-aided engineering (CAE) refers to the use of application software to aid engineering analysis tasks, including structural analysis, thermal and fluid flow analysis, multibody dynamics, kinematics, process simulations, and optimization. Specifically, CAE application packages support a wide range of engineering disciplines or phenomena, including
• finite element analysis,
• mechanical event simulation,
• multibody dynamics,
• manufacturing process simulation,
• process optimization,
• computational fluid dynamics,
• product optimization, and
• multiphysics solutions.
Table 3 lists the leading CAE services on the cloud, their service providers, deployment models, key capabilities and features, and cloud infrastructure providers. More detailed discussions of the CAE services on the cloud follow in subsequent sections.
Table 3. Computer-aided engineering services on the cloud

The ANSYS Enterprise Cloud is an enterprise-level engineering simulation platform on the cloud, hosted by the ANSYS dedicated corporate account on the AWS platform. Currently, ANSYS Mechanical, Electronics, Fluent, CFX, CFD, and LS-DYNA have been implemented on both public and private clouds. Figure 10 shows the interface of ANSYS on the Nimbix Cloud. In addition, ANSYS partners with multiple cloud service providers, including CADFEM, CPU24/7, Fujitsu, GOMPUTE, Nimbix, and Penguin Computing, to provide users with ubiquitous access to HPC in multitenant or single-tenant environments. For example, Nimbix delivers ANSYS applications as a service in both batch and interactive modes. Users have on-demand access to the Nimbix cloud securely from any browser, device, or network.

Fig. 10. ANSYS on the Nimbix Cloud (Nimbix, 2016).
CD-adapco provides cloud-based CFD software by partnering with multiple cloud infrastructure providers such as Gompute, Nimbix, and Rescale. Specifically, CD-adapco STAR-CCM+ is one of the most comprehensive simulation products for solving problems involving flow, heat transfer, and stress. Gompute is a cloud infrastructure provider who delivers HPC resources over the Internet. Gompute provides computing power, remote visualization, storage, and applications provided by third-party software providers such as CD-adapco. MSC Nastran is a multidisciplinary structural analysis application that help engineers perform static, dynamic, and thermal analysis across the linear and nonlinear domains as well as structural optimization and fatigue analysis. LS-DYNA is a general-purpose multiphysics simulation software package developed by the Livermore Software Technology Corporation. Figure 11 shows the interface of LS-DYNA on the Nimbix Cloud. Crunch CFD is a multiphysics simulation tool for solving complex flow problems. Crunch CFD can run on Amazon EC2 for scalable, large-scale computing. OpenFOAM is an open-source CFD software developed by OpenCFD at ESI Group under the GNU General Public License. OpenFOAM is available on several public clouds, including Sabalcore, Amazon EC2, Microsoft Azure, and Rescale.
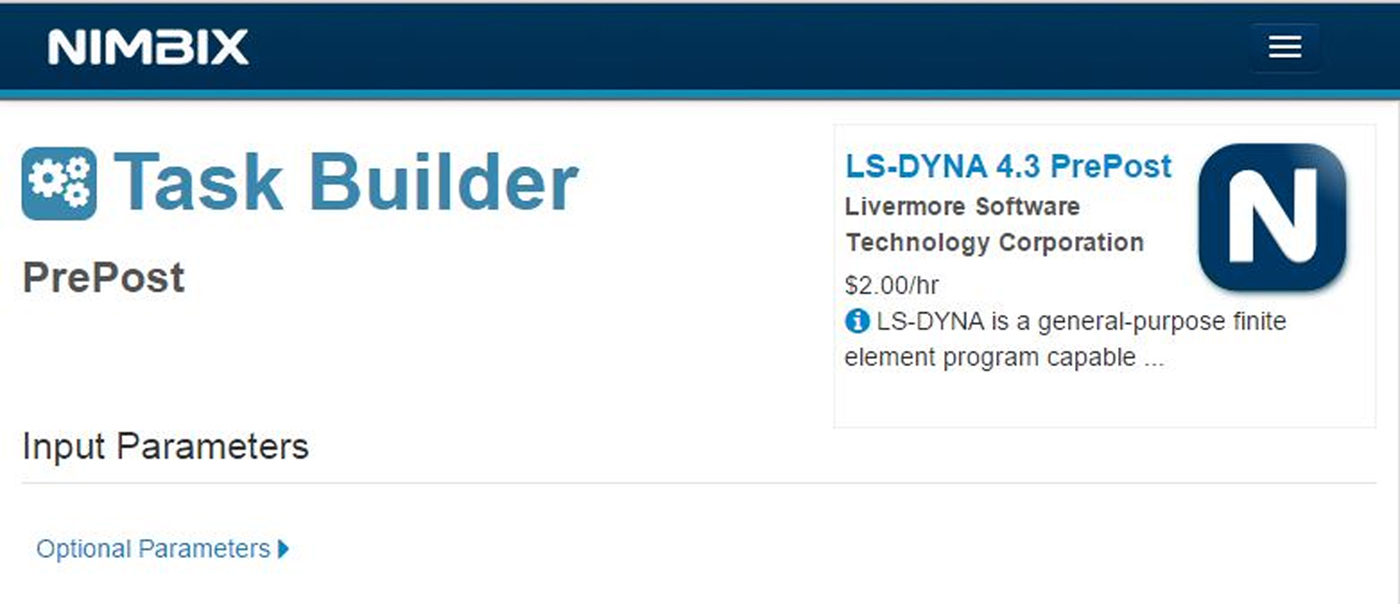
Fig. 11. LS-DYNA on the Nimbix Cloud (Nimbix, 2016).
The key capabilities and benefits of aforementioned cloud-based engineering analysis software tools include
• high-performance cloud computing infrastructure and data visualization,
• cloud-based parallel and distributed computing,
• cloud-based data management and data security via encryption and disaster recovery services,
• flexible pricing models, and
• remote hardware accelerated graphics for pre/post operations to minimize data transfer.
4. MANUFACTURING ON THE CLOUD
Computer-aided manufacturing (CAM) refers to the use of numerical control (NC) computer software applications to create detailed instructions (G-code) that drive computer NC (CNC) machine tools for manufacturing parts. Manufacturers in a variety of industries depend on the capabilities of CAM to produce high-quality parts. A broader definition of CAM can include the use of software applications to define a manufacturing plan for tooling design, NC programming, coordinate measuring machine inspection programming, machine tool simulation, or postprocessing. The plan is then executed in a production environment, such as direct numerical control, tool management, CNC machining, or coordinate measuring machine execution. Table 4 lists the leading manufacturing services on the cloud, the service providers, deployment models, key capabilities and features, and cloud infrastructure providers. More detailed discussions of the manufacturing services on the cloud follow in subsequent sections.
Table 4. Manufacturing services on the cloud

Similar to CAD on the cloud, several CAM software vendors have developed cloud-based CAM solutions. Specifically, CAM in Fusion 360 enables users to conduct CNC programming and toolpath simulation for 2-D and 3-D milling operations, 3-D printing, and three-axis machining. For example, Fusion 360 allows users to preview a mesh structure, make preprint refinements, and automatically create optimized support structures for 3-D printing. Fusion 360 on the cloud enables 32 physical cores and 72 threads on a single machine. Figure 12 shows the interface of Fusion 360 on the cloud for toolpath simulation.

Fig. 12. Toolpath simulation in Fusion 360 (Autodesk360, 2015).
Similar to Fusion 360, Siemens PLM NX CAM enables toolpath generation, CNC programming, postprocessing, and toolpath simulation. NX CAM has parallel-processing capability using multiple cores. Multiple operations can be processed by multicores, while CAM programmers create other operations or postprocess calculated programs. Siemens NX CAM provides cloud-based NX via virtual desktop by partnering with NVIDIA.
DELMIA® multiaxis surface machining enables users to develop NC programs for machining multiple surfaces and curves in the multiaxis mode. Figure 13 shows the interface of DELMIA multiaxis machining services on the cloud. The unique characteristic of DELMIA is that it offers five-axis simultaneous surface machining operations and a variety of tool axis strategies including dynamic tool axis inclination for collision avoidance. For example, with DELMIA's NC Prismatic Programmer, users can create, optimize, and validate milling programs in a virtual environment. According to DELMIA, the key capabilities and benefits of DELMIA include
• multiaxis machining of multiple surfaces with full collision avoidance using various tool path styles,
• multiaxis machining of multiple curves using various tool path styles, and
• various tool axis strategies including dynamic lead/lag and tilt angle.

Fig. 13. Computer-aided manufacturing in DELMIA (Inceptra, 2015). Copyright 2015 by Inceptra. Reprinted with permission.
ESPRIT offers cloud-based digital tooling services that allow users to have access to up-to-date tooling product data by partnering with Machining Cloud and Kennametal. Machining Cloud provides users with access to product data from the leading cutting tool suppliers such as Kennametal. By creating a repository of digital tooling data such as milling, turning, holemaking, and toolholders, Machining Cloud enables users to select cutting tools, analyze cutting tool and machine usage, recommend optimized feeds and speeds, and optimize the usage of cutting tools. Figure 14 shows the interface of digital tooling services on the cloud.

Fig. 14. Cloud-based digital tooling (Kennamental, 2015). Copyright 2015 by Kennamental Inc. Reprinted with permission.
5. PRODUCTION ON THE CLOUD
In addition to cloud-based engineering design, analysis, and manufacturing services described in the previous sections, Table 5 lists several leading cloud-based production and operations management software packages as well as the key features, operating systems, and databases of these software packages. Specifically, the production and operations management tools offer supply chain management, material management, production management, sales and order management, and customer relationship management. The leading production management software vendors include Acumatica, Netsuite, Epicor, Plex Systems, IQMS, SYSPRO, and Microsoft. Because the key capabilities and features of the leading production and operations management software applications on the cloud are very similar, more detailed discussions of the cloud-based production and operations management software developed by Acumatica and Netsuite follow in subsequent sections.
Table 5. Production management software on the cloud

Acumatica was founded in 2008, headquartered in Kirkland, Washington. Acumatica provides cloud-based solutions for wholesale distribution, discrete manufacturing, customer relationship management, project account, and enterprise resource planning. For example, Acumatica's cloud-based solution allows multilocation retailers to have access to real-time status of orders, inventory, and profitability by location and product.
NetSuite was founded in 1998, headquartered in California. SuiteCloud developed by NetSuite is a comprehensive offering of cloud development tools, applications, and infrastructure that enables users to manage customer information, manufacturing operations, inventory, and supply chain. The key capabilities and features of SuiteCloud include the following:
• flexible digital dashboards;
• role-based application navigation and security;
• a native thin-client solution designed for on-demand internet delivery; and
• a partner relationship management module that can provide joint forecasting, commission management, and partner performance metrics.
We have provided a state-of-the-art review of cloud-based tools, software, and services that are available in the market. In addition, the key capabilities and benefits of these tools, software packages, and services are discussed. In the next section, a number of selected research issues associated with CBDM are identified.
6. SELECTED ISSUES FOR FUTURE RESEARCH
6.1. Performance evaluation and benchmarking
As listed in Tables 1–5, a number of computationally intensive software providers such as ANSYS and OpenFOAM have developed cloud-based software and services in HPC cloud environments. However, due to potential significant performance penalties caused by virtualization, high resource utilization, and high latency in cloud computing environments, it is crucial to systematically evaluate and assess the performance of public, private, and hybrid clouds for running large-scale complex programs. These performance metrics include speedup, scalability, reliability, and latency. In addition, the actual performance of cloud computing environments should be compared with that of workstations and supercomputers in traditional settings. Providing such benchmarks is particularly important to users and developers in order to understand trade-offs in migrating to cloud computing. For example, Jackson et al. (Reference Jackson, Ramakrishnan, Muriki, Canon, Cholia, Shalf, Wasserman and Wright2010) evaluated the performance of HPC applications in a cloud environment to compare HPC clusters to the Amazon EC2 platform. Based on their results, the Amazon EC2 is 6 times slower than a typical midrange Linux cluster and 20 times slower than a modern HPC cluster. In addition, their results show that there is a strong negative correlation between the percentage of time an application spends on communications and its overall performance. In addition, Iosup et al. (Reference Iosup, Ostermann, Yigitbasi, Prodan, Fahringer and Epema2011) investigated the performance of cloud computing services for multitask scientific computing on four commercial cloud platforms: Amazon EC2, GoGrid, ElasticHosts, and Mosso. The selected performance metrics included wait time, response time, and bounded slowdown. Their results show that the performances of the four tested cloud platforms are worse than those of selected scientific computing infrastructures.
Considering uncertainties about computing performance on the cloud, two important research questions that need to be answered are as follows:
• Is the performance of HPC clouds sufficient for solving large-scale modeling, optimization, and simulation problems in digital design and manufacturing?
• How does the performance of cloud computing for solving large-scale modeling, optimization, and simulation problems in digital design and manufacturing compare with that of workstations and in-house supercomputers in traditional settings?
6.2. Usability evaluation
In addition to the assessment of cloud computing performance, it is also very important to evaluate the usability of cloud-based software and services because users access cloud-based software and services through a web browser and/or a mobile device remotely rather than download and install a software package locally. Potential bandwidth constraints and different workflows may have significant impacts on usability. In general, usability refers to how satisfied users are with a product or a process. In the context of cloud-based design, analysis, manufacturing, and production, usability refers to the quality of a user's experience when interacting with the cloud computing environment, including graphical user interfaces (GUIs), workflow, ease of learning, efficiency of use, and error frequency. For example, ANSYS provides users with access to their cloud-based software packages through both interactive remote desktop and batch processing modes. In the interactive remote desktop mode, users can access ANSYS products through a GUI that is exactly the same as that of in-house ANSYS products. However, user experience might be significantly degraded because of a slow Internet connection and a large amount of time spent on transferring data from a local desktop to a cloud remotely. In the batch processing mode, although users can execute a series of jobs without manual intervention on the cloud, users can not interact with software through a GUI.
Considering the research gap identified above, two key research questions that need to be answered as are follows:
• What factors influence user experience in solving modeling and simulations problems in cloud-based design and manufacturing?
• What are the effects of the factors affecting user experience in solving modeling and simulations problems in cloud-based design and manufacturing?
6.3. Cybersecurity
As factories are increasingly interconnected in cyberspace, cloud manufacturers are more and more often targeted by not only hackers and cyber criminals but also competing companies and nations. It is important to address the confidentiality, integrity, and availability of data on the cloud to ensure the success of cloud-based design and manufacturing. Specifically, data confidentiality focuses on limiting access to data to authorized parties. Encryption is one of the primary techniques for ensuring data confidentiality. Data integrity focuses on protecting data from being changed inappropriately by unauthorized parties. As with data confidentiality, cryptography plays an important role in ensuring data integrity. Data availability focuses on ensuring that authorized parties are able to access data when needed. Similar to organizations in all other sectors, manufacturers are concerned with the confidentiality, integrity, and availability of data on the cloud. More important, it is also necessary to identify emerging threats and risks associated with design and manufacturing on the cloud. For example, it is necessary to conduct systematic vulnerability assessment of cloud-based design and manufacturing systems and evaluate the impact of various cyber-attacks on software, cloud infrastructures, and manufacturing systems and processes.
Considering the research gap identified above, two key research questions that need to be answered are as follows:
• What are the effects of malicious software or malware such as viruses, worms, and Trojan horses affecting software, cloud infrastructures, and manufacturing systems and processes in CBDM settings?
• What generic cybersecurity framework is required to identify and assess CBDM-specific vulnerabilities?
7. CONCLUSION
This paper has provided an overview of cloud-based software and services in the areas of engineering design, analysis, manufacturing, and production as well as the nationally and internationally well-established providers. A survey was conducted to assess to what extent engineering design, engineering analysis, manufacturing, and production across all phases of the product development lifecycles can already be performed based on the software and services accessed through the cloud. The key features and benefits of the digital design and manufacturing software and services on the cloud are also analyzed. Specifically, with respect to engineering design, cloud-based design software packages and services enable designers to perform 2-D and 3-D modeling, photorealistic rendering, and collaborative design remotely via a web browser or a mobile device. With respect to engineering analysis, cloud-based engineering analysis software packages and services enable engineers to significantly accelerate computationally intensive workloads such as finite element analysis and CFD by partnering with public clouds such as Amazon or Microsoft or offering private cloud infrastructures. With respect to manufacturing, cloud-based manufacturing software packages and services enable manufacturers to conduct CNC programming, tool path simulation, and cutting tool selection on the cloud via virtual desktop. The computationally intensive manufacturing tasks such as tool path generation and simulation can be accelerated by cloud-based parallel computing. With respect to production, cloud-based production software packages and services enable engineers to perform data-intensive workloads such as supply chain management, customer relationship management, and financial management via cloud-based databases. Based on the assessment and analysis of these cloud-based software and services, the main conclusion to be drawn from the state-of-the-art review is that a significant portion of the entire product realization process is already partially or fully supported by cloud-based software and services. The state-of-the-art review serves to provide a technology guide for decision makers in their efforts to select suitable cloud-based software and services as alternatives to existing in-house resources. In addition, to bridge research gaps, this review recommends the directions of future research on the evaluation of cloud computing, usability, and security.
ACKNOWLEDGMENTS
Certain commercial equipment, instruments, suppliers, tools, services, and software are identified in this paper to foster understanding. Such identification does not imply recommendation or endorsement by the authors, nor does it imply that the materials or equipment identified are necessarily the best available for the purpose.
Dazhong Wu is a Postdoctoral Research Fellow in the Harold & Inge Marcus Department of Industrial and Manufacturing Engineering at Penn State University and the NSF Center for e-Design. He received his PhD in mechanical engineering from the Georgia Institute of Technology. Dr. Wu's research is focused on the investigation and development of digital design and manufacturing technologies using high-performance cloud computing.
Janis Terpenny is the Peter & Angela Dal Pezzo Chair and Department Head of the Harold & Inge Marcus Department of Industrial & Manufacturing Engineering at Penn State University. She is also the director of the Center for e-Design, an NSF industry–university cooperative research center. Dr. Terpenny's research interests are focused on engineering design and include process and methods of early design, knowledge and information in design; product families and platforms, obsolescence in products and systems, complexity of products and systems, and cloud computing for design and manufacturing integration.
Dirk Schaefer is an Associate Professor of engineering design in the Department of Mechanical Engineering at the University of Bath. Prior to joining the University of Bath, he was an Assistant Professor of mechanical engineering at the Georgia Institute of Technology and a Lecturer in digital enterprise technology at the University of Durham. He obtained a PhD in computer science with a focus on computer-aided product development systems from the University of Stuttgart, an MS in mathematics with a focus on computer-aided geometric design from the University of Duisburg, and an Advanced College Certificate in mechanical engineering. Dr. Schaefer has more than 20 years of experience in academia and industry in computer-aided design and engineering, product development, and manufacturing.