Introduction
The term kaolin applies to ores composed mainly of kaolinite and, therefore, it could be defined as any massive rock, with a variable percentage of clay minerals, of a composition equal to or close to kaolinite (Bartolomé, Reference Bartolomé1997). Kaolinite is an aluminum silicate hydrate, with an approximate composition of 2H2O·Al2O3·2SiO2. Structurally, it comprises octahedral aluminum oxide sheets and tetrahedral silica sheets stacked alternately. It presents the following theoretical structural formula: Al2(Si2O5)(OH)4, and its centesimal composition includes 46.54% SiO2; 39.50% Al2O3, and 13.96% H2O (Mathur, Reference Mathur2002; Prasad et al., Reference Prasad, Reid and Murray1991).
Kaolin can be extracted from two types of deposits: primary and secondary. Primary deposits are formed by residual weathering or hydrothermal alteration of crystalline rock (granite) and, as is the case with the kaolin used in this study (mine Caobar SA, Poveda de la Sierra, Guadalajara, Spain), are located in the place where they were formed. Secondary deposits are sedimentary in nature and are formed by erosion of primary deposits. Primary clays are generally thick and contain much less iron oxide than secondary ones (Prasad et al., Reference Prasad, Reid and Murray1991).
The main applications of kaolin are:
(1) The paper industry, as kaolin provides good opacity, white color, high brightness, and good print quality in paper.
(2) The ceramics industry, as the products require kaolin to produce a white color for the pieces after firing and have high mechanical strength before and after firing. Contamination by oxidation of iron compounds affects the final quality of the product when present in the form of particles, producing stains when the piece is fired, or adsorbed into kaolinite, contributing to the loss of whiteness after firing.
(3) Kaolin is also used as filling in rubber products, added to paints to provide desirable flow properties, used in polyvinyl chloride (PVC) coatings, and it is a main component in the production of fiberglass, among other applications (Murray, Reference Murray1961).
The red-to-yellow pigmentation seen in many kaolin samples is due mainly to the presence of oxides and hydroxides associated with iron(III), such as the red of hematite (Fe2O3), the reddish brown of maghemite ((Fe3+0.67-0.33)Fe3+2O4), the brownish yellow of goethite (α-Fe3+O(OH)), the orange of lepidocrocite (γ-Fe3+O(OH)), or the red-brown of ferrihydrite (Fe3+10O14(OH)2). These oxides and hydroxides are present as coatings on individual grains or as discrete fine particles throughout the clay mass (Ambikadevi & Lalithambika, Reference Ambikadevi and Lalithambika2000). The iron content of a clay determines the quality of raw materials in the manufacture of porcelain and ceramics, because iron(III) impurities reduce the refractability and whiteness of ceramic products. Amounts as small as 0.4% iron(III) may be sufficient to affect the quality (Ambikadevi & Lalithambika, Reference Ambikadevi and Lalithambika2000). Elimination of iron(III) can increase the value of the kaolin so it can be used to make porcelain items and ceramics where there are strict demands for whiteness (Pavlov & Meshcheryakova, Reference Pavlov and Meshcheryakova1983).
The processes used to improve the brightness and whiteness of the kaolin can be classified into physical or chemical (or a combination of the two) (de Mesquita et al., Reference de Mesquita, Rodrigues and Gomes1996). Physical methods generally include separation by flotation, magnetic separation, selective flocculation, and size separation by hydrocyclones (He et al., Reference He, Huang and Chen2011). Chemical methods consist of leaching with inorganic acids and reducing agents, such as sodium dithionite (Na2S2O4) with aluminum sulfate (Al2(SO4)3), sulfur dioxide with aluminum powder, and sulfur dioxide with zinc powder. With these latter methods, a greater degree of iron elimination can be achieved compared with that in the previous ones, but they are more expensive (they involve complex processes) and are hazardous to the environment (de Mesquita et al., Reference de Mesquita, Rodrigues and Gomes1996). Organic acids such as citric (C6H8O7) or oxalic (H2C2O4), the latter showing a greater ability to leach the ferric oxides associated with a kaolinitic clay, can also be used as an alternative (Arslan, Reference Arslan2021; Panias et al., Reference Panias, Taxiarchou, Paspaliaris and Kontopoulos1996; Shao et al., Reference Shao, Ji and Yu2020). This chemical methodological variant is considered less harmful to the environment than the use of inorganic acids (Hernández et al., Reference Hernández, García, Cruz and Luevanos2013; Musiał et al., Reference Musiał, Cibis and Rymowicz2011). Response surface methodology (RSM) for iron leaching from kaolin using oxalic acid solutions of moderate concentration and high reaction temperature (77°C) was reported by Taran and Aghaie (Reference Taran and Aghaie2015).
Another option that has been employed in this type of deterioration is the development of biotechnological processes that involve the use of microorganisms. Bioleaching is a method that has been shown to be effective for the reduction/removal of impurities in various mineral raw materials.
In bioleaching processes, if good efficiency is achieved, the environmental damage is expected to be reduced significantly when compared with that caused by chemical methods. In addition, investigations performed in this sense indicated that this methodology does not require a great deal of energy nor high upfront or operating costs, and the crystalline structure of the clay is not altered during the process (Hosseini & Ahmadi, Reference Hosseini and Ahmadi2015; Lei et al., Reference Lei, Gong and Yuan2000; Mockovčiaková et al., Reference Mockovčiaková, Štyriaková, Škvarla and Kozáková2008; Musiał et al., Reference Musiał, Cibis and Rymowicz2011). Bioleaching procedures are based on the metabolic activity of certain microorganisms, which can transform solid compounds into soluble elements that can be extracted and recovered (Hosseini & Ahmadi, Reference Hosseini and Ahmadi2015; Nguyen et al., Reference Nguyen, Won, Ha, Nguyen and Kang2021; Štyriakova & Lovás, Reference Štyriakova and Lovás2007). Research into bioleaching of iron has been carried out mainly using fungal and bacterial species (Eisele & Gabby, Reference Eisele and Gabby2014; Peng et al., Reference Peng, Zhou, Liu, Yu, Qiu and Zeng2019; Štyriaková et al., Reference Štyriaková, Bekéniová and Štyriaková2017). In some cases, the removal of iron oxides from kaolin is achieved by reducing iron(III) (oxidized and insoluble form) to iron(II) (reduced and soluble form) by the effect of metabolic products or microbial processes (Guo et al., Reference Guo, He, Li, Lu and Chen2010a; Guo et al., Reference Guo, Lin, Xu and Chen2010b; Nealson & Saffarini, Reference Nealson and Saffarini1994; Zegeye et al., Reference Zegeye, Yahaya, Fialips, White, Gray and Manning2013). A decrease or removal of ferric impurities from kaolin in bacterial trials can be achieved by various mechanisms (Mueller, Reference Mueller2015). Under anaerobic conditions, production of organic acids by anaerobic bacteria, generates a reducing environment causing the dissolution of iron (Štyriaková et al., Reference Štyriaková, Styriak and Malachovsky2007, Reference Štyriaková, Mockovčiaková, Štyriak, Kraus, Uhlík, Madejová and Orolínová2012). Other types of strict anaerobic bacteria could be employed in bioleaching processes because they use the various iron(III) forms present in kaolin as final electron acceptors, reducing them to iron(II) (Kostka et al., Reference Kostka, Wu, Nealson and Stucki1999; Luu & Ramsay, Reference Luu and Ramsay2003).
The current study investigated chemical leaching of iron from kaolin using citric and oxalic acids, and the microbial removal of Fe(III) present in kaolin, using pure cultures of a bacterial strain. The experimental conditions under which the bacterial cultures showed the greatest efficiency during the tests developed at laboratory scale have been studied. A bacterial strain belonging to the Bacillus genus, isolated from the biological reactor of a wastewater treatment plant, was investigated and this bacterium was checked for comparison purposes with the two kaolin samples, the high-iron kaolin with 3.06 wt.% iron content, and the low-iron kaolin with 0.34 wt.%.
Materials and Methods
Materials and Equipment
Kaolin samples were supplied by Caobar SA from their mine waste dumps located at Poveda de la Sierra (Guadalajara, Spain; Figs S1–S2 in the Supplementary Material show the geological background). The waste came from beds that were not exploited due to the high levels of iron impurities. All the reagents and solvents used were of analytical grade (Scharlau, Barcelona, Spain). They were used without further purification and contained only traces of iron. All analytical determinations were carried out in triplicate and the values reported are the means of the measurements.
Before the biological leaching experiments, the kaolin samples were sterilized by autoclave at 121°C for 20 min to eliminate any natural microbial community that could interfere with the results from the selected bacterial strain. Two bacterial strains coded as no. 37 and no. 91 were chosen initially for experimental work. Both were isolated from a biological reactor of a wastewater treatment plant located in Madrid. The strains were identified as Bacillus cereus AH-2 and Bacillus thuringiensis EB63, respectively, according to GenBank (an open access, annotated collection of all publicly available nucleotide sequences and their protein translations). The bacteria had been stored in Eppendorf tubes at –80°C in cryo-balls immersed in a cryo-conservation solution (protease, 5 g L–1; casein, 15 g L–1; dextrose, 1 g L–1; glycerol, 1 g L–1; yeast extract, 2 g L–1; sodium chloride, 5 g L–1; sodium citrate, 1 g L–1; sodium bicarbonate, 0.1 g L–1; deionized water, 850 mL L–1). The first strain was discarded later and not used for further experimental work.
The sterile culture medium for bacteria leaching experiments was prepared following the protocol of Šuba et al. (Reference Šuba, Danková, Štyriaková, Doušová, Bekényiová and Štyriaková2018): 2 g L–1 of dipotassium hydrogen phosphate, 1 g L–1 of ammonium sulfate, 0.1 g L–1 of calcium chloride, 0.75 g L–1 of disodium EDTA, 0.2 g L–1 of sodium chloride, 0.085 g L–1 of sodium nitrate, 0.2 g L–1 of urea, 0.1 g L–1 of yeast extract, and 20 g L–1 of glucose.
Powder X-ray diffraction (XRD) analyses were carried out using a Miniflex 600 instrument from Rigaku (Tokyo, Japan), using CuKα radiation (λ = 0.154 nm) from an X-ray tube set at 40 kV and 15 mA, scanning from 4 to 60°2θ at a rate of 5°2θ/min with a divergence slit of 2 mm. X-ray fluorescence analysis (XRF) was carried out with a portable Niton XL3t GOLDD instrument from Thermo Scientific (Chelmsford, Massachusetts, USA) with energy dispersive detection.
Atomic absorption spectrometry analyses (AAS) were carried out in an Analytik Jena ContraAA 700 spectrophotometer (Jena, Germany), selecting the Kα iron line at λ = 248.3 nm, using an acetylene-air flame and iron calibration solutions of 1, 2, 5, 7.5, and 10 mg L–1.
Iron(II) ultraviolet-visible spectroscopy (UV-Vis) analyses were carried out in a double-beam Specord 200 Pins instrument from Analytik Jena (Jena, Germany), controlled by the software WinAspect Plus v 4.2.0.0., with 1 cm quartz cuvettes.
Gas chromatography-mass spectrometry (GC-MS) analyses were carried out using an Agilent 6890 series II instrument with a mass selective detector MSD 5973 (Santa Clara, California, USA). The GC column was HP-5MS of 5% methyl phenyl siloxane (25 m×0.25 mm×0.20 μm), with constant He flow (1 mL /min). The chromatographic conditions were: initial temperature, 60°C; rate, 6°C/min; final temperature, 300°C; final time, 20 min; injector temperature, 275°C. Conditions of the mass detector were: electronic impact, 70 eV; m/z scan from 50 to 800 Da, resolution, 1000. The chromatograms and mass spectra of compounds were analyzed by the MSD Chem Station Data Analysis application software of Agilent and the spectral library from NIST.
Dissolved oxygen concentration measurements were carried out with an instrument HI 98198 opdoTM from HANNA Instruments (Smithfield, Rhode Island, USA). Eh-pH measurements were carried out using a Crison GLP21 device from HACH (Ames, Iowa, USA).
The software used to construct the Eh-pH diagrams was HSC Chemistry 5.0 from Outukumpu, (Pori, Finland).
Experimental Design for Chemical Leaching
The independent variables chosen for the chemical leaching experiments were the kaolin pulp concentration (g/100 mL), the time (days), and the citric and oxalic acids concentrations (mM), and the only dependent variable was the iron leached from the kaolin (Table 1). Experiment 9 was duplicated as it was the only experiment of 30 days’ duration.
Table 1 Independent variables of the RSM study. –1: low values, 0: medium values, 1: high values

1mM = mmol L–1
Each experiment was prepared by mixing 50 mL of citric acid solution, 50 mL of oxalic acid solution, and the corresponding amount of high-iron kaolin to reach the pulp concentration (Table 1). The suspensions were hand-shaken at the beginning and once a day for 1 min for the duration of the experiment; thus trying to reproduce the conditions that could be applied at a mining site, where mechanical moving of the leaching piles could be carried out once a day. After the experiment, the solid kaolin was filtered and the solution was analyzed by AAS for total iron determination.
Biological Leaching Experiments
Procedure. Double experimental analyses were carried out in all cases. Cultures used as inoculum for each replica were prepared independently. Then, three assays were performed simultaneously: (i) high-iron kaolin with bacteria; (ii) low-iron kaolin with bacteria; and (iii) high-iron kaolin without bacteria. First, 25 mL of 0.9% mass saline serum was inoculated in two sterile 50 mL Falcon tubes, with the selected strain of Bacillus, until an optical density of 0.1 was reached. Note that in both homogenized cultures, bacterial clumps were observed at different depths of the tubes due to cellular aggregation; therefore, assayed inoculated biological aliquots should be considered comparable but not identical. The optical density measured was equivalent to a concentration close to 5×104 Colony-forming Units (CFU) mL–1 (value obtained after counting of CFU in LB agar Petri dishes inoculated with 100 μL of the suspension). The pH was adjusted to 7.5 and sterile kaolin was added at a concentration of 50 g L–1.
The experiments were carried out for up to 14 days, and data were obtained at 0, 3, 7, and 14 days. In summary, three sets of samples were prepared, all in duplicate:
(1) High-iron kaolin with bacteria: 250 mL of culture medium, 12.5 g of high-iron kaolin (3.06% mass of iron(III) oxide) and 1.0 mL of inoculated bacterial strain.
(2) Low-iron kaolin with bacteria: 250 mL of culture medium, 12.5 g of low-iron kaolin (0.34% mass of iron(III) oxide) and 1.0 mL of inoculated bacterial strain.
(3) High-iron kaolin without bacteria: 250 mL of culture medium and 12.5 g of high-iron kaolin (3.06% mass of iron(III) oxide).
At the end of the time set for each experiment, the samples were filtered first through 0.45 μm and later through 0.22 μm to ensure the elimination of bacteria and most of the kaolin particles. The filtrates were stored in sterile 50 mL Falcon tubes. A vacuum pump N86 KN18 from KNF was used for the filtration and all procedures were carried out in a laminar flow cabin.
Analytical procedures. Eh-pH, iron(III), and iron(II) were analyzed directly in the filtrates, which were stored in the Falcon tubes and kept in a fridge. The speciation of iron in the samples was carried out analyzing the iron(II) by the colorimetric method of 1,10-phenantroline (Bridgewater et al., Reference Bridgewater2012; Stucki, Reference Stucki1981; Stucki & Anderson, Reference Stucki and Anderson1981) and calculating the iron(III) concentration as the difference between the total iron concentration in solution determined by AAS and the iron(II) analyzed by this colorimetric method. For the colorimetric determination of iron(II), 4 mL of calibration solutions of 0.5, 1, 2, 5, and 10 mg L–1 of iron(III) nitrate in distilled water were placed in 50 mL beakers. 1 mL of 10% hydroxylamine chlorhydrate (to reduce the iron(III) to iron(II)), 1 mL of 1,10-phenantroline reagent (0.03 g L–1) and 2 mL of 5 M ammonium acetate solution were added to each iron(III) standard solution. The pH was adjusted to values between 3.0 and 5.0. The samples were prepared in the same way as the standards, except that any hydroxylamine chlorhydrate was added, because the objective was the determination of iron(II). Standards and samples were analyzed at 510 nm for 10 s. As the bacterial culture medium has a yellowish color that could interfere with the colorimetric iron(II) determination, an iron(III) nitrate standard solution of 1 mg L–1 was prepared in the culture medium instead of distilled water. The absorbance of the blank prepared in distilled water was 0.0005, the absorbance of the 1 mg L–1 standard solution in the culture medium was 0.1192, and the absorbance of the same 1 mg L–1 standard in distilled water was 0.1078. Thus, the absorbance of the culture medium was calculated in 0.0114 absorbance units that were subtracted from the absorbance measurements of all samples.
Carboxylic acid determination was done by passing an aliquot of the filtrates through SupelTM Select SPE cartridges (Supelco, Pennsylvania, USA), previously conditioned by passing through 3 mL of Millipore water and 1.5 mL of methanol. Later, 100 mL of the filtrate was passed at constant flow avoiding the cartridges’ dryness, and 2 min later, the cartridges were eluted with 2 mL of methanol, and the solvent was evaporated to dryness. The dry samples were re-dissolved in 0.1 mL of methanol and 25 μL of 2 M solution of trimethylsilyldiazomethane (Kühnel et al., Reference Kühnel, Laffan, Lloyd-Jones, Martínez del Campo, Shepperson and Slaughter2007) in n-hexane was added, stirring for 20 min in an ultrasound bath. Finally, the samples were dried in a nitrogen atmosphere and re-dissolved in 1 mL of dichloromethane. 1 μL of this solution was injected into the GC-MS.
Results and Discussion
Characterization of Kaolin Samples
From the mineralogical composition of the kaolin samples determined by XRD (Table 2), the most abundant mineral phase in all samples was kaolinite, with minor amounts of quartz and muscovite (Figs. 1 and 2 show the XRD patterns of the original high-iron kaolin and the kaolin sample from RSM experiment 4, while Fig. 6 shows the XRD pattern of the kaolin validation experiment). Analysis of the kaolin samples by XRF (Table 3) showed that the chemical composition of the samples after the bioleaching experiments were roughly the same as the original ones (although they are not shown in the table).
Table 2 Mineralogical composition of kaolin samples

1Kaolin from RSM experiment 4: 32.2% iron removal
2Kaolin from RSM experiment 7: 31.7% iron removal
3Kaolin from validation experiment, negligible iron removal

Fig. 1 XRD of high-iron kaolin

Fig. 2 XRD of kaolin sample from RSM 4 experiment
Table 3 Chemical composition of kaolin samples by XRF (mass %)

1LOI: Loss on ignition
2Kaolin from RSM experiment 4: 32.2% iron removal
3Kaolin from RSM experiment 7: 31.7% iron removal
4Kaolin from validation experiment; negligible iron removal
5Molar ratio Si/Al
Characterization of the Bacterial Strains
The reactivation of the selected bacterial strain was carried out in aseptic conditions; placing the sterile cryo-balls on the surface of the LB agar medium in Petri dishes, cultures were maintained at 30°C for 24 h. After reactivation, mass cultures of the two strains were obtained at the same culture conditions. The Gram staining allowed the purity of the culture to be checked, showing Gram positive bacteria (Fig. 3). Strain no. 91 was selected for the bioleaching experiments because of its optimal growth in the conditions mentioned above (Liu et al., Reference Liu, Du, Lai, Zeng, Ye, Xu and Shao2017).

Fig. 3 Photomicrographs (clear field microscopy) of the gram stain of the no. 91 strain. The green scale bar represents 10 μm
Chemical Leaching Results
An experimental design was developed (Table 4) to determine the influence of the independent variables on the elimination of iron (dependant variable) from kaolin with RSM, for 1% (Fig. 4a), 4% (Fig. 4b), and 7% (Fig. 4c) pulp concentrations. The amount of iron leached from the kaolin into the solution was calculated (Eq. 1):

Table 4 Results of the RSM study of chemical leaching experiments

1mM = mmol L–1

Fig. 4 Response Surface Methodology (RMS) curves for 1, 4, and 7% pulp concentrations. The z-axis represents the Fe reduction (%) after Eq. 1; the y-axis represents the oxalic acid concentration (mM); and the x-axis represents the time (days)

From Eq. 1, the model was represented in Fig. 4: the z-axis represents the Fe reduction (mass %), the y-axis represents the oxalic acid concentration (mM) and the x-axis represents the time (days). The model did not give any influence to the citric acid concentration,
The largest amount of Fe eliminated is slightly >30% (samples 4 and 7), and this was accompanied by a significant pH decrease to <1.0 (0.7 and 0.8, respectively). Sample 1 showed an iron elimination of 30%, but in this case, the pH did not decrease, being 1.4. A further refinement of the statistical model revealed that the most influential variable was the leaching time (Eq. 2), whereas the pulp concentration and the oxalic acid concentration had only residual influence (Fig. 5):

where t is the duration of the experiment (days). This equation means that the model represents a linear optimization, where iron elimination from kaolin depended only on time; although the acidic medium of oxalic acid is essential for the leaching process, the acid concentration and the amount of pulp are irrelevant. With these results, a confirmation experiment extended in time was carried out, suspending 14 g of high-iron kaolin in 200 mL of 20 mM oxalic acid solution (7% m/v pulp concentration), and maintaining the experiment for 218 days with occasional stirring. The experiment was intended for 208 days, which would be time enough to lixiviate all iron from this kaolin after the RSM model, but the filtration was delayed for 10 additional days due to extenuating circumstances. During this long period, the supernatant solution took on a yellowish color, indicating that some iron leaching had taken place (see Fig. S3 in the Supplementary Material). At the end of the experiment, coinciding with an extraordinarily cold period (the laboratory temperature was <5°C), kaolin was filtered and analyzed by XRD and XRF, and the filtrate was analyzed by AAS. The AAS analysis showed that only traces of iron were present in the leaching solution, and the XRF showed an iron(III) oxide concentration in the solid kaolin of 3.42% mass, practically the same as the starting kaolin when considering uncertainty. The XRD analysis resulted in an identical XRD pattern to that of the initial, high-iron kaolin, showing the presence of kaolinite, quartz, and muscovite (Fig. 6).

Fig. 5 Experimental model showing the time dependence of the Fe leaching from kaolin

Fig. 6 XRD of high-iron kaolin after 218 days of chemical lixiviation in 20 mM oxalic acid solution
The low temperatures prevalent in the laboratory during the final week of the validation experiment caused the re-precipitation of iron species that were the same as found in the starting kaolin, as confirmed by XRD. Temperature was shown to be a very influential parameter in the iron leaching from granite slabs with 20 mM oxalic acid solutions, whereas the experiments carried out at 5°C showed no iron leaching at all. In contrast, the same experiments carried out at 30°C showed quantitative iron elimination results. The influence of the temperature on the iron leaching from kaolin with oxalic acid solutions has been observed previously in stirred-tank reactors (Arslan, Reference Arslan2021; Taran & Aghaie, Reference Taran and Aghaie2015), leading to the conclusion that high reaction temperatures (77 to 85°C, respectively) greatly favor iron leaching. In the present study, however, a temperature greater than ambient was unaffordable for economic reasons. There was no limit on how much iron(III) could be leached; because in a repeated 218-day experiment, the amount increased linearly with time.
Bacterial Leaching Results
Bacteria belonging to the genus Bacillus have been related previously to the bioleaching of kaolin. Several Bacillus species were isolated (mostly of the Bacillus cereus group) in kaolin deposits from where the mineral was extracted in Slovakia (Horna Prievrana, Banska Bystrica, and Rudnik Haadec Kralove (Šuba et al., Reference Šuba, Danková, Štyriaková, Doušová, Bekényiová and Štyriaková2018)) and in China (Longyan and Fujian (Guo et al., Reference Guo, He, Li, Lu and Chen2010a; Guo et al., Reference Guo, Lin, Xu and Chen2010b; He et al., Reference He, Huang and Chen2011).
In the present study, the bacterial strain used was isolated from the biological reactor of a wastewater treatment plant and identified as Bacillus thuringiensis, which is considered to be in the Bacillus cereus group. A reducing environment was expected as a result of the bacterial metabolic activities which could generate organic acids and, therefore, favor iron dissolution. The bacteria were inoculated in a culture medium specifically formulated for this bioleaching process (Šuba et al., Reference Šuba, Danková, Štyriaková, Doušová, Bekényiová and Štyriaková2018), mixed with the kaolin samples, and incubated within certain temperature and oxygen limitation conditions. Their viability was checked periodically by the corresponding inoculation into LB agar solid medium plates and the counting of CFU/mL grown.
The dissolved oxygen values were ~0.4 mg L–1 in both duplicates from the 3rd day of experiment, when these values should range between 7.0 and 8.0 mg L–1 in a fully oxygenated medium (Roldán, Reference Roldán2012). The zero values were slightly different: 3.64 mg L–1 for the high-iron kaolin plus bacteria samples, 3.49 mg L–1 for the low-iron kaolin plus bacteria samples, and 2.74 mg L–1 for the high-iron kaolin without bacteria samples. The tendency related to oxygen concentration of all samples was an initial decrease that was kept at low values (<0.4 mg L–1) during all experiments.
Other parameters of bioleaching studied in this work were: (1) Eh-pH; (2) concentration of total Fe, Fe2+, and Fe3+; and (3) concentration of lauric acid. As already mentioned, all the bioleaching experiments were carried out in duplicate, as were the corresponding analyses, which have been marked as D1 (first replicate) and D2 (second replicate) in the results reported below.
Eh-pH
In all the experiments, the pH remained almost neutral (between 6.0 and 7.0) (pH evolution during the bioleaching experiments is shown in Fig. 7), with the exception of replicate D2 (high-iron kaolin) on day 7, which was <6, a circumstance that was later related to greater iron bioleaching; see below.
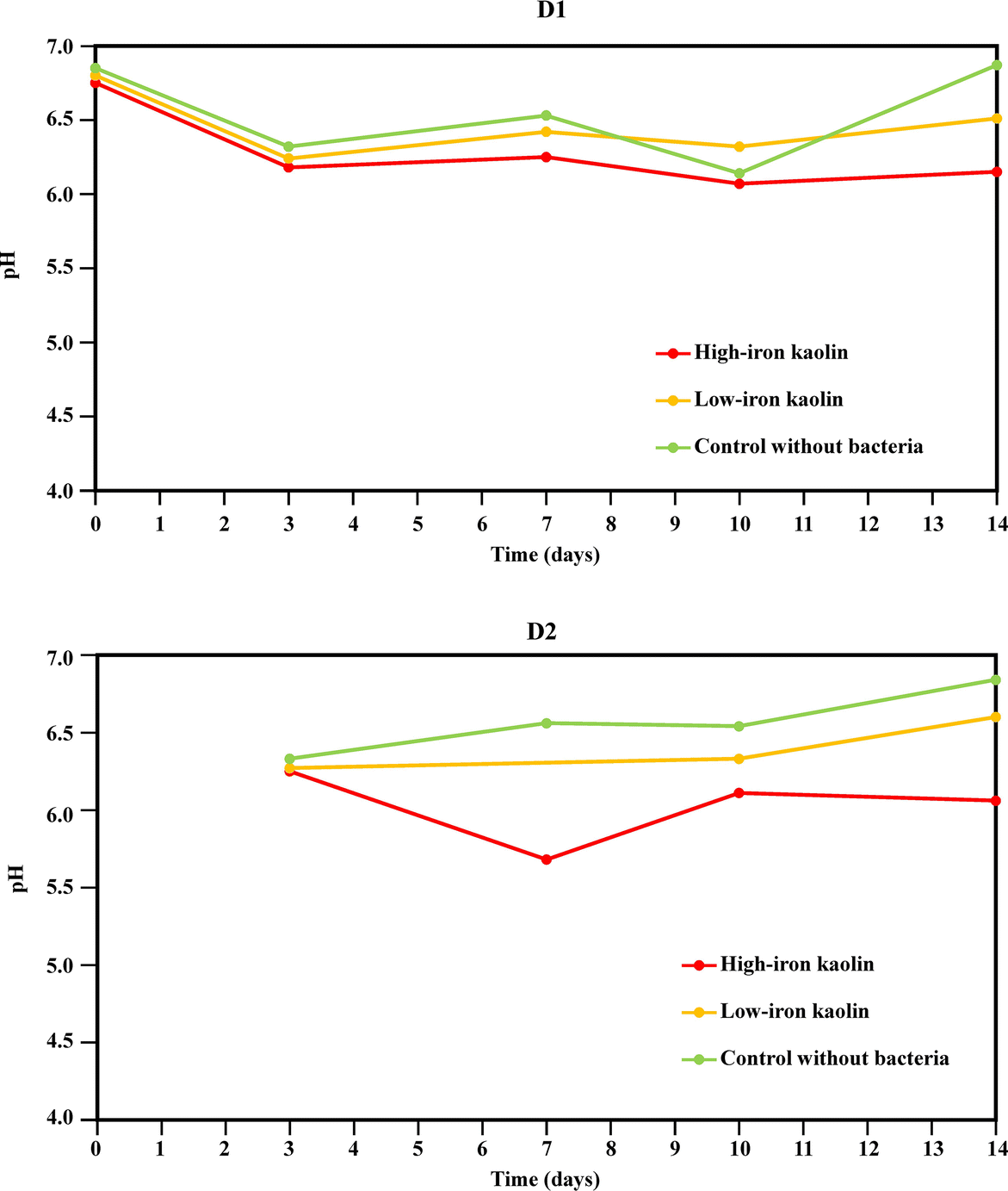
Fig. 7 Changes in pH values throughout the bioleaching experiments with the Bacillus strain
A significant decrease in pH was observed firstly during group (i) experiments (high-iron kaolin plus bacteria), but from day 7 the pH values reached 6.0. These pH values were high when compared with the works of Štyriaková and Štyriak (Reference Štyriaková and Štyriak2000), Štyriaková et al. (Reference Štyriaková, Styriak and Malachovsky2007), Štyriaková et al. (Reference Štyriaková, Mockovčiaková, Štyriak, Kraus, Uhlík, Madejová and Orolínová2012), and Šuba et al. (Reference Šuba, Danková, Štyriaková, Doušová, Bekényiová and Štyriaková2018), in which the authors reported pH values as low as 4.0.
On the other hand, the evolution of Eh during the experiments was measured for both duplicates D1 and D2 (Fig. 8). In the duplicate D2, the measurement of this parameter started after the 3rd day of experiments.
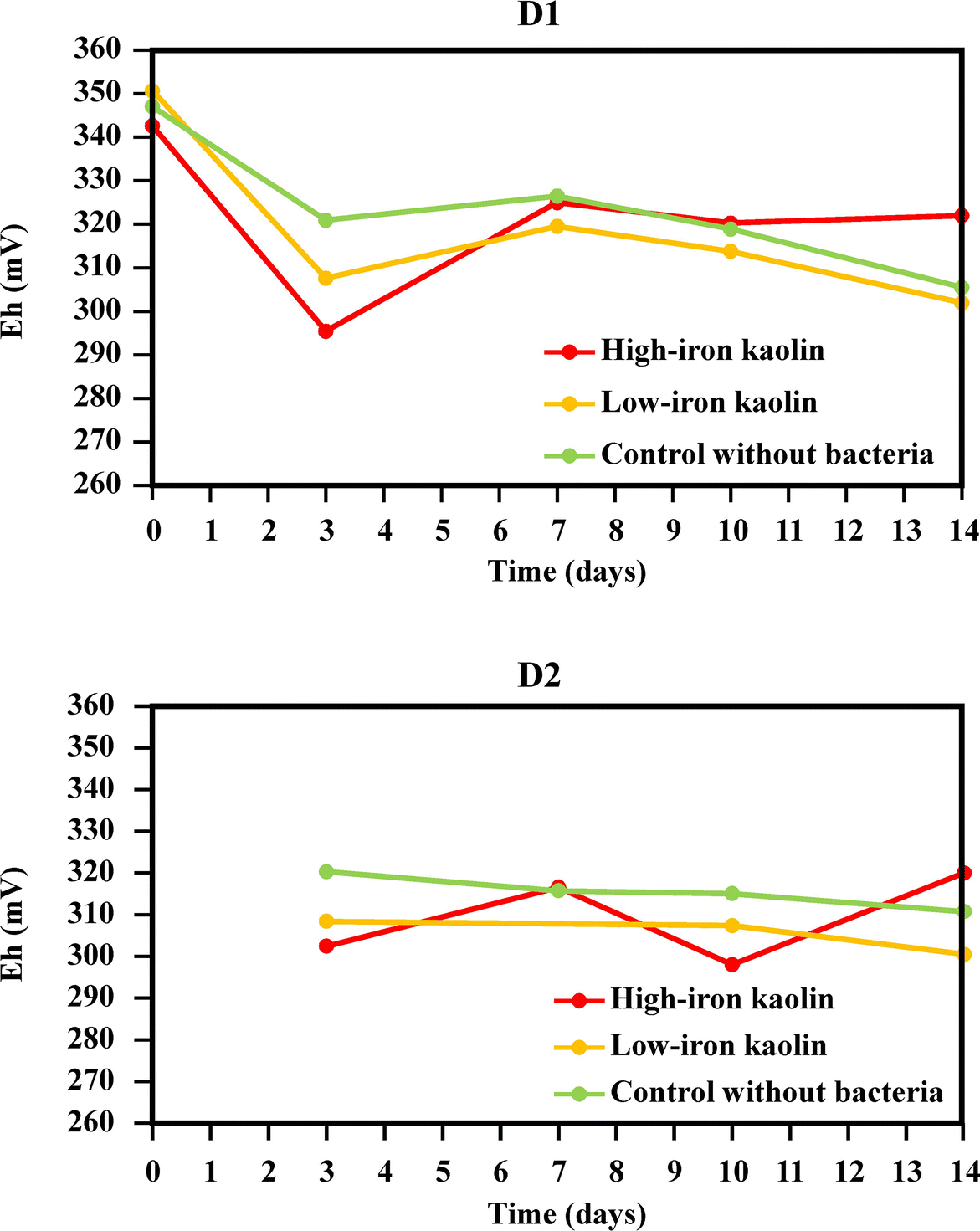
Fig. 8 Eh measurements during the bioleaching experiments with the Bacillus strain
The conclusion from these Eh data is that the samples with high-iron kaolin showed higher Eh values at the end of the experiment, probably due to the bioleaching of iron from the sample. The Pourbaix Eh-pH diagrams were constructed for two selected samples: the 0th day of the group (ii) (low-iron kaolin + bacteria, duplicate D1) and the 7th day of the group (i) (high-iron kaolin + bacteria, duplicate D2) (Fig. 9).

Fig. 9 Upper: Eh-pH diagram of the sample at the 0th day of group (ii) (low-iron kaolin + bacteria, duplicate D1). Lower: Eh-pH diagram of the sample at the 7th day of group (i) (high-iron kaolin + bacteria, duplicate D2). The conditions of these Eh-pH diagrams were ambient temperature (~22°C) and atmospheric pressure (~1013 hPa), and total iron concentrations were: 0.05 mg/L (upper diagram) and 14.9 mg/L (lower diagram). These diagrams took into account the possible coexistence of all the iron species
The predominant chemical species were the iron (oxyhydr)oxides, as can be observed from Fig. 9, although the samples were close to the area delimited by the chemical iron(II) species. This fact could be related to the bacterial activity, which could result in the establishment of a more reducing environment and a lower pH.
Concentration of Iron Species
From the results of iron solubilization during the bioleaching experiments with the Bacillus strain (Figs. 10 and 11) the concentration of total iron in solution increased steadily throughout the duration of the experiment. As observed (Fig. 10) from the comparison of red bars (high-iron kaolin with bacteria) with green bars (high-iron kaolin without bacteria), the effect produced by bacteria was only moderate, as in the sample lacking bacteria, iron was also lixiviated.

Fig. 10 Fe total concentration (mg/L) and pH during the bioleaching experiments with the Bacillus strain
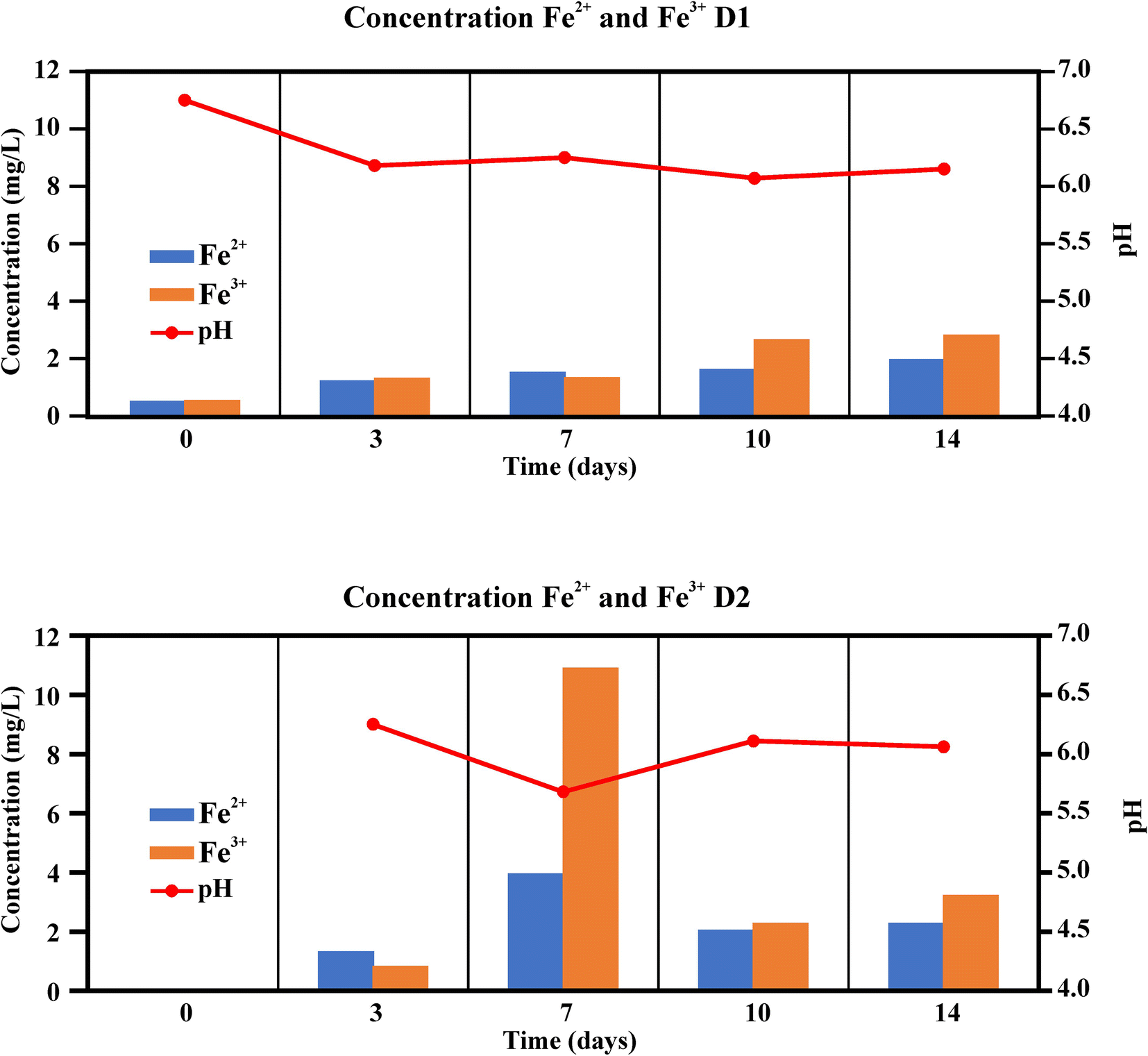
Fig. 11 Fe2+ and Fe3+ concentrations (mg/L) and pH during the bioleaching experiments with the Bacillus strain
Almost the same amounts of Fe2+ and Fe3+ were measured during the experimental period, slightly larger amounts of Fe3+ being detected especially at the end (Fig. 11). In the replicate D2, on the 7th day of experiment, there was a sharp increase in the iron in solution, for both iron species and total iron. This was the same point which showed the lower pH value in all experiments, thus relating greater iron bioleaching with a value of pH of <6.0.
The maximum amount of iron eliminated during incubation was 0.83%, which represents a very low yield when compared with the results of Štyriaková and Štyriak (Reference Štyriaková and Štyriak2000). Those researchers reported, in a 28-day experiment, 43% and 15% iron elimination in two kaolin samples using two strains of Bacillus cereus. Iron eliminations of 51.1 and 53.4% in a 10-day experiment, using a mixed culture of Bacillus sphaericus and two other species of the Bacillus cereus group were reported by Guo et al. (Reference Guo, He, Li, Lu and Chen2010a). In all these works, the kaolin samples were not sterilized prior to the experiments, as was done in the present work, so any influence of natural microbiota was not taken into account.
The low bioleaching efficacy observed in the present work could be attributed to the mild reducing environment in the samples. The previously exposed Pourbaix Eh-pH diagrams (Fig. 9) showed that in the two selected samples (with the highest and the lowest iron concentrations in solution), the major iron chemical species were the iron (oxyhydr)oxides, FeO*(OH), an insoluble iron form, and also the most frequent contaminant form of iron in kaolin (Ambikadevi & Lalithambika, Reference Ambikadevi and Lalithambika2000; Guo et al., Reference Guo, He, Li, Lu and Chen2010a; Nealson & Saffarini, Reference Nealson and Saffarini1994). This does not mean that other iron species could not coexist, although their concentration diminished when moving away from the equilibrium lines (as it enters the zone of the solid species). The experimental results showed that, in one of the 7th day samples, an environment near the equilibrium line with the iron(II) species, which could be explained by the bacterial activity, supplied a reducing environment favoring the reduction of FeO*(OH) to Fe(II).
Lastly, worth noting is the leaching in the samples of group (iii), high-iron kaolin without bacteria. This fact could be explained by three chemical processes by which the solid iron(III) oxides can leach iron in an aqueous solution giving Fe3+, Fe2+, and their complexes:
Protonation: FeO*(OH) + H+→ Fe(OH)2 +
Reduction: FeO*(OH) + 3H+ + e– → Fe2+ + 2H2O
Complex formation: FeO*(OH) + 3H+ + nL– → [FeLn](3–n) + 2H2O (L = ligand).
These reactions produce polarization and weakening of the Fe–O bond (Borggaard, Reference Borggaard1997; Schwertmann, Reference Schwertmann1991). In the composition of the culture medium specifically formulated for this bioleaching process (Šuba et al., Reference Šuba, Danková, Štyriaková, Doušová, Bekényiová and Štyriaková2018), Na2EDTA was found, and this compound can act as a ligand for the iron leaching from kaolin, which can result in the observed (and similar) leaching rates of both (i) and (iii) groups, although the latter was not inoculated with bacteria; the iron elimination was always greater in the samples where bacteria were present, however.
Concentration of Lauric Acid
To conclude, also worth mentioning is that the main organic acid identified in the samples was lauric acid C12:0. The concentration of the lauric acid during the bioleaching experiments using the Bacillus strain is shown in Fig. 12.

Fig. 12 Lauric acid amounts and pH during the bioleaching experiments with the Bacillus strain
As was shown in the replicate experiment D1, a clear increase in the amount of lauric acid with time was noted when bacteria were present (red and yellow bars), whereas the samples lacking bacteria (green bars) showed no significant amounts of this acid. Lauric acid seems to be produced by bacteria in larger amounts when more iron is available, as in the high-iron kaolin (red bars). The replicate experiment D2 emphasized again the 7th day of experiment, during which a lower pH and much greater iron bioleaching were observed, which agreed also with the sharp increase in the lauric acid concentration detected (Fig. 12). Many Bacillus species are effective at secreting metabolites especially in media containing high concentrations of glucose and amino acids, as was the case. These conditions, together with low concentrations of dissolved oxygen, can favor a fermentative metabolism that includes, among other products, fatty acids (Abdel-Shafi et al., Reference Abdel-Shafi, Reda and Ismail2017; Nakano et al., Reference Nakano, Dailly, Zuber and Clark1997; Ramos et al., Reference Ramos, Hoffmann, Marino, Nedjari, Presecan-Siedel, Dreesen, Glaser and Jahn2000).
Despite the low bioleaching efficiency found with the selected strain, a methodology was established in the laboratory that could be employed with other microorganisms such as Shewanella, a bacterial genus which is able to use iron(III) species as final electron acceptors (Zegeye et al., Reference Zegeye, Yahaya, Fialips, White, Gray and Manning2013).
The rates of iron elimination reached in the current study, either by chemical methods (30%) or by biological methods (<1%), do not permit contemplation of an industrial implementation at present, and, thus, any discussion about operating costs or its practical use is beyond the scope of the work, as the chemical leaching would produce a kaolin with ~2 wt.% of iron(III) oxide, still far from commercial quality. This does not diminish our interest in the work, however, as the company Caobar SA in Spain has waste kaolin dumps worth ~€30 M (~US$ 32 M) if they could be treated until the iron contents were sufficiently small; this would be a huge potential source of raw material and would eliminate an environmental problem at the same time.
Conclusions
Kaolin waste dumps represent an environmental and economic problem in the European Union and elsewhere because the iron minerals present as contaminants make them, currently, commercially unviable. In the present study, leaching of an iron contaminant from kaolin was investigated using chemical and biological approaches.
The chemical leaching of iron in kaolin was performed with RSM, using oxalic and citric acid concentrations (20, 60, and 100 mM), kaolin pulp amounts (1, 4, and 7%), and time (7, 30, and 60 days) as the independent variables and the amount of iron eliminated (%Fe Reduced) as the only dependant variable.
The RSM confirmed that the most influential variable was the leaching time. Although oxalic acid must be present in the medium, citric acid had no influence regardless of its concentration. The amount of iron removed by chemical leaching reached 32% in the RSM experiments.
A confirmation experiment over an extended period (218 days in 20 mM oxalic acid with 7% kaolin pulp concentration) which was expected to eliminate all iron from the kaolin, did not achieve the desired results. The low temperatures (~5°C) prevalent in the laboratory during the final week of validation experiment caused the re-precipitation of iron species leaving the ‘leached’ kaolin samples unchanged from the starting kaolin, as confirmed by XRD and XRF.
The biological leaching experiments were carried out by incubating samples with a strain of Bacillus in a low concentration of dissolved oxygen, during an experiment lasting 14 days, and taking samples at the 3rd, 7th, 10th, and 14th days.
Although this bacterial species showed good results in similar experimental designs described in the literature, in the present study the amount of iron leached from kaolin reached only 0.83%.
The influence of bacteria was apparent, however, because the samples with the microbial inoculum showed concentrations of lauric acid increasing with time, although the presence of this fatty acid seemed not to favor greatly the solubilization of the iron from the kaolin samples.
More studies are in progress with other bacteria which are able to use iron as a final electron acceptor.
Supplementary Information
The online version contains supplementary material available at https://doi.org/10.1007/s42860-022-00192-7.
Acknowledgments
The authors thank the company Caobar SA for the gift of kaolin samples; Laura Benito Broncano, Jerónimo-Emilio García-González, and Héctor Mateos from UPM for technical work; Julio César Arranz-González from Instituto Geológico y Minero de España (IGME); and Fredy Guzmán-Martínez from Servicio Geológico Mexicano for the XRF analyses. The authors dedicate this paper to their co-author Professor Juan F. Llamas on the occasion of his retirement.
Author Contributions
Yolanda Sánchez-Palencia, X-ray diffraction analysis, software, validation; David Bolonio, methodology, formal analysis, supervision; Marcelo F. Ortega, response surface methodology, data curation, software, validation, supervision; María-Jesús García-Martínez, resources, methodology, supervision; José Eugenio Ortiz, visualization, formal analysis, data curation, supervision, writing (review and editing); Fernando Rayo, investigation, methodology, validation; Lucía Arregui, methodology, investigation, data curation, supervision, writing (review and editing); Susana Serrano, methodology, investigation, data curation, supervision, writing (review and editing); Juan F. Llamas, methodology, investigation, data curation, supervision; Laureano Canoira, methodology, investigation, data curation, supervision, writing (original draft preparation), writing (review and editing).
Funding
Open Access funding provided thanks to the CRUE-CSIC agreement with Springer Nature. This research was funded by the European Union through program EIT Raw Materials from Horizon 2020 (Project 18259, BioLeach: Innovative Biotreatment of Raw Materials)
Declarations
Conflicts of Interest
On behalf of all authors, the corresponding author states that there are no conflicts of interest.
Consent to Participate
All authors consent to participate in this publication.
Consent for Publication
All authors have read and agreed to the submitted version of the manuscript.