1 Introduction
The development of complex products relies on progressive design iteration that moves the design forward, but also frequently results in corrective iteration and/or suboptimal product designs (Wynn & Eckert Reference Wynn and Eckert2017). Components or systems are designed in parallel and require multiple rounds of convergent iteration (Yassine et al. Reference Yassine, Joglekar, Braha, Eppinger and Whitney2003) before an integrated product is ready. Unexpected problems during design or even in service can lead to additional corrective iteration rounds. For example, when the gas temperature in a jet engine is increased and adjacent components are redesigned. Vibration is suddenly detected in a helicopter and an interface between two components has to be redesigned. The actual operation of the product results in a higher load than first expected. A component is considered too expensive and is targeted for cost saving redesign. A frequent warranty case forces a recall and redesign of a system. All of these seemingly very different problems might have a common cause: they can be expressed as the design and management of ‘design margins’. However, while the concept of a margin seems intuitive, it has so far not been formally defined and therefore the common aspects of the problems have been missed. This paper develops the concepts of ‘design margins’ and presents a definition of the concept of margins that underlies many related terms. It thereby formalizes a concept that designers intuitively understand but rarely use in precise terms.
Many complex products, such as jet engines, our case study example, are highly integrated designs that have been optimized over generations of development by pushing technologies, materials and geometry to their limits (Wynn & Eckert Reference Wynn and Eckert2017), so that components have little margin. Their design processes involve the collaboration of multiple teams often across organizations working in parallel on integrated systems under conditions of uncertainty while working to tight time and budget constraints. To manage the risks, teams sometimes keep margins that they do not disclose to others, to be able to respond to potential future changes. The design process typically runs through multiple pre-planned rounds of convergent and progressive iteration, where the results from the parallel teams are integrated. During these iteration rounds key requirements and key parameters can still change significantly requiring other teams to accommodate these changes. Such iterative design processes can involve costly design churn, where the number of problems is not reduced and the designers do not get (much) nearer a solution during a design cycle (Yassine et al. Reference Yassine, Joglekar, Braha, Eppinger and Whitney2003). Another major risk lies in being pushed inadvertently into an additional corrective iteration round. One of the potential reasons is that components do not have enough margin and therefore require a redesign. This is a real risk as many complex products like aircraft engine are highly optimized because of weight restrictions, so that margins above what is required are seen as a problem. Past research has addressed the relationship between engineering change and iteration from the perspective of engineering change prediction (e.g. Clarkson et al. Reference Clarkson, Simons and Eckert2004) or managing the dependence between activities in design processes (e.g. Cho & Eppinger Reference Cho and Eppinger2005). In contrast, the argument presented here is that managing the iteration loops is practically a matter of managing margins and can be improved if margins are modelled explicitly to assess the risk of needing to move to a new solution late in the process. The paper draws on a case study from the aerospace industry where additional and unplanned corrective iteration rounds put project deadline in jeopardy. Corrective iteration is seen differently in the design of less complex products, such as many consumer products, where the consequences and cost of corrective iteration can be limited. This rarely applies for complex products in aerospace, where the cost of unplanned and corrective iterations may be high due to either the effort to evaluate what is ‘good’ and/or the often substantial cost to create prototypes.
This paper focuses on complex and often highly optimized products, where margins are deliberately reduced. However, other products contain elements of significant overdesign, which is also a form of margin. Products where weight and size are less critical are less sensitive to overdesign in some key parameters, for example many production machines are sold based on the reliable quality of the products they produce, rather than (within reason) their own size or weight. Some products, in particular consumer products are often subject to huge margins against their expected requirements, because users cannot be trusted to treat the product as expected, for example a washing machine might have an indicated load of 7 kg, but some users are likely to overload anyway. Products that are designed based on product platforms are also often overdesigned relative to their specific requirements, because the components need to stand up to the stiffest demands of the products made from the platform (Isaksson et al. Reference Isaksson, Lindroth and Eckert2014). The economy of scale in production might also justify a higher margin, which is cheaper for both the manufacturer and consumer than a custom-made one without margins. Where the cost trade-off lies depends on the individual product. Buildings can also be subject to high cumulative overdesign; for example Jones et al. (2017) report on a boiler house that is overdesigned by 500% of normal load.
This paper argues that design margin is a common phenomenon, for which the paper offers a theoretical definition, but which is played out in different ways in different products and across different phases of the design process. As Section 2 on methodology explains, the paper is therefore a combination of theory development and reporting on industry practice. Section 3 sets the context for the research by giving a brief overview of research on engineering change and iteration before going into more detail about concepts which are related to margins. Section 4 defines margins in relation of the capability of a component or system, the requirements regarding the margin and the constraints placed on it. As a margin usually arises from the desire to cater for potential uncertainties, Section 5 discusses a split of the margin into buffer and excess to handle uncertainty and introduces the terminology for margins across the design process. Section 6 applies the concept to the example of jet engine design before conclusions are drawn in Section 7.
2 Methodology
This paper originates from a project shared between the authors, a manufacturer of trucks and a supplier of components for jet engines.
The project started with interviews in the truck company to understand the range of terminology used to describe margins. A total of 10 engineers were interviewed, the interviews were transcribed and the results played back to the company (see Isaksson et al. Reference Isaksson, Lindroth and Eckert2014), and discussed in detail in steering committee meetings with experts involved in the project.
This paper focuses on the theoretical work to formalize the concept of margins, identifies classes of margins and analyses how margins can be calculated and in what way the concept of margins can contribute along the design process.
This paper draws in particular on component design in a jet engine company, where the second author worked for over 20 years as a technical specialist. When formalizing the margins the authors discussed the role that margins play in the processes of the organization with numerous engineering specialists informally. It became clear that margins play a fundamental role in how the iteration cycles worked in the company and how they interact with their customers, the jet engine system manufacturers (OEMs). The case presented here is a simplified example based on a real design situation, which is using fictional values for parameters and does not disclose the names of the materials, as the details are highly confidential. The real cases would be concerned with multiple margins at the same time, which would make an example unnecessarily complex.
The formalization of margins was presented back to experts both in the engine and the truck company for validation.
3 Related concepts in the literature
The term margin is often used in industry especially within aerospace or ship building (Stratmann Reference Stratmann2006). It is also used in conjunction with engineering change, where it is not formally defined. However, this research highlights margins as the link between product properties and processes by arguing that when margins are used up, changes can propagate; and in the worst case lead to entire iteration loops. After a brief introduction to engineering change and iteration the section will pull different concepts related to margins together to show the breadth of concepts that are considered margins.
3.1 Engineering change
Engineering change can be defined as ‘an alteration made to parts, drawings or software that have already been released during the product design process. The change can be of any size or type; the change can involve any number of people and take any length of time.’ (Jarrett et al. Reference Jarratt, Eckert, Caldwell and Clarkson2011). Understanding change plays a fundamental role in limiting the risk and effort involved in evolving a complex product, which is usually based on a previous design. Meeting new requirements or introducing innovation requires engineering change just as much as dealing with problems emerging in the product development process. Change to a product are only required, if the product has no margins to absorb the required alteration to the requirements.
Any modification, in the iteration or a formal engineering change, can have a knock-on effect onto other parts of the design if margins are exhausted (Eckert et al. Reference Eckert, Clarkson and Zanker2004), which in turn have to be modified making planning difficult. Each proposed change or modification can be expressed as changes to one or more parameters of a component or system. Each parameter might become critical if small, required changes (or combinations of changes) initiate significant changes in other components. Components can act as (i) change absorbers, receiving change without passing it on, (ii) change carriers passing the same degree of change on as they have received, or (iii) change multipliers, which pass more changes on to other parts of the system, which will in turn need to be redesigned (Eckert et al. Reference Eckert, Clarkson and Zanker2004). Change becomes problematic when change absorbers turn into change carriers or change multipliers and becomes critical when changes avalanche. In this context designers talk of the change absorbers as margins that are being used up.
Consequently, there is a clear link between margins and processes, as changes in such critical situations may be brought under control given sufficient design resources and time, but companies might need to abandon these projects. From the perspective of an individual change, there might be several knock-on effects; some that can be dealt with directly and others that require detailed analysis, which leads to ripple effects with the magnitude of changes decreasing over time. Griffin et al. (Reference Giffin, de Weck, Bounova, Keller, Eckert and Clarkson2009) identify typical patterns of change propagation while Pasqual & de Weck (Reference Pasqual and de Weck2012) observed ripple patterns, with the number of change requests increasing towards deadlines.
Designers need to do several things in managing change. These include; making explicit decisions about how to implement a change (Earl et al. Reference Earl, Eckert and Clarkson2005), understanding product connectivity, and analysing the ability of the component to absorb a specific change (Keller et al., Reference Keller, Eckert and Clarkson2009). Various tools have been developed to predict the impact of change, through probabilistic links (Clarkson et al. Reference Clarkson, Simons and Eckert2004) anticipating changes (Cohen et al. Reference Cohen, Navathe and Fulton2000) or underlying functional models (Grantham et al. Reference Grantham Lough, Stone and Tumer2006; Hamraz et al. Reference Hamraz, Caldwell, Ridgman and Clarkson2015). More recently change prediction has been integrated with visualizing other aspects of the product (Kocar & Akgunduz Reference Kocar and Akgunduz2010) and integrating product based change prediction with process models (Ahmad et al. Reference Ahmad, Wynn and Clarkson2013). It is evident that there is a need to understand design margins as a link between engineering change and iteration, to be able to manage and plan iterations efficiently.
3.2 Iteration
Iteration has mainly been considered from the perspective of how design processes can be planned so that products can be delivered with the least number of iteration cycles (see Wynn & Eckert Reference Wynn and Eckert2017 for a comprehensive review). This perspective focuses on information dependency between tasks, which have to be repeated if the correct information is not available, rather than on the properties of the product that lead to iteration. Iteration is recognized as a fundamental part of most design processes and reflected in many models of design processes (Wynn & Clarkson Reference Wynn and Clarkson2018), either as part of exploration and convergence or as feedback loops in a stage-based process. Iteration is often seen as something to be minimized or avoided by defining design problems more clearly or confining iteration to the early phases of design processes (Suh Reference Suh1990) in what Safoutin (Reference Safoutin2003) calls the ‘zero-iteration ideal’. Unger & Eppinger (Reference Unger and Eppinger2011) argue for risk management through ‘controlled, feedback-based redesign’ governed by design reviews. Iteration can be characterized in terms of cyclic dependencies among overlapping, sequential and parallel tasks. Iteration occurs because new information becomes available or new goals need to be addressed (Chusilp & Jin Reference Chusilp and Jin2006; Jun & Suh Reference Jun and Suh2008). Parallel iteration is the mechanism through which convergent iteration takes place (Cho & Eppinger Reference Cho and Eppinger2005). However, the predominant mode of iteration is overlapping, as many tasks are not carried out completely in parallel. Thus decisions about planning when to start a specific task are critical (Krishan et al. Reference Krishnan, Eppinger and Whitney1997). Unplanned iteration occurs because of ‘unexpected failure of a design to meet specifications’ (Yassine & Braha Reference Yassine and Braha2003) and when new requirements come up (Ahmad et al. Reference Ahmad, Wynn and Clarkson2013). It can lead to significant delays in process duration, increases in cost due to additional work and unproductive periods for engineers. This can lead to churn, where the design is not advanced, but the designers still cannot be redeployed to other tasks.
3.3 Design margins
Austin-Breneman et al. (Reference Austin-Breneman, Yu and Yang2015) discuss the information bias in negotiations between design teams in complex systems design, referring to the buffer or margin that designers add to their own estimated values. They draw on game theory to model complex design processes to run simulations of the effect information bias has on finding an optimal design solution. They argue that engineers have envelopes of parameter values in which they negotiate. The paper identifies three bias strategies, namely, no bias, constant bias and decreasing bias as the design process progresses. They simulate a measure of the number of iterations in a small-scale artificial problem. The results show that a fixed bias to more likely to result in ‘suboptimal’ solutions than no bias or a decreasing bias; however, decreasing bias requires significantly more iterations. A similar theme is picked up in the work of Dawson et al. (Reference Dawson, Fixson and Whitney2012), who look at design safety factors as the amount by which properties, such as strength, exceed their requirements, which they see as a means to mitigate against misalignment between the product architecture and the organizational structure. Through a game theory inspired simulation they propose faster information sharing, and temporary acceptance of suboptimal partial solutions as a way to improve product performance. They conclude that projects in which the all participants are incentivized to manage safety factors, converge much more successfully, whereas wild swings in the safety factors have seriously detrimental effects. Fernandes et al. (Reference Fernandes, Henriques, Silva and Moss2014) make a similar point based on an analysis of a large body data about change requests for jet engine design in order to study the evolution of requirements over the course of a project. They identify the effect of imprecision of the value of key parameters as one of the key causes of design iteration in design processes and propose better analysis of the parameter values and communication of this imprecision more clearly to different design teams.
Canbaz et al. (Reference Canbaz, Yannou and Yvars2014) use an agent based approach to model design convergence through negotiation between design agents in collaborative complex systems design. Collaborative design requires both accommodating the needs of others and the uncertainties that the design process is subject to. Other authors adopt a set-based design approach (Sobek et al. Reference Sobek, Ward and Liker1999; McKenney et al. Reference McKenney, Kemink and Singer2011) where design options are represented through ranges of parameters that are narrowed over the course of a product development process. Within these sets of potential values considering all the constraints the agents have to negotiate feasible solutions which more or less meet the requirements of each agent. More recently they turned their attention to manage rework using Set-Based Design (Kennedy et al. Reference Kennedy, Sobek and Kennedy2014). Canbaz et al. (Reference Canbaz, Yannou and Yvars2014) use Monte Carlo simulation to find the best solution based on a wellbeing indicator for each agent. They express margins as min–max values of ranges of acceptable values.
Margins are also used to provide flexibility, as they contribute to the adaptability of an existing product to particular requirements. Such adaptability is designed into an individual product at the beginning to allow for changes in the course of the product life cycle or during the design of the follow-on product (Ross & Hastings Reference Ross and Hastings2005). Both Ross & Hastings (Reference Ross and Hastings2005) and Qureshi et al. (Reference Qureshi, Murphy, Kuchinsky, Seepersad, Wood and Jensen2006) advocate assessing the flexibility of a product by systematically anticipating and rating the potential future changes to ‘future proof’ the design, which will inevitably introduce a degree of redundancy into the product. In Ross & Hastings (Reference Ross and Hastings2005) this assessment is achieved through mapping out the tradespace, i.e. the range of possible parameter values that provides potential solutions. Where the design sits within this tradespace indicates margins on the product. In the design of a specific product the designers can trade the form, the material and the function off against each other. Only by realizing a specific form in a specific material it is possible to fulfil a particular function. Eckert et al. (Reference Eckert, Isaksson and Earl2012) argue that margins therefore lie in the relationship of these three elements. De Neufville et al. (Reference De Neufville, Scholtes and Wang2006) introduce design options as a form of deliberate planning for a small number of potential changes that will be carried out to the product including calculations of the cost of planning in these options and the savings made in using a design option as opposed to making a change from scratch. Martin & Ishii (Reference Martin and Ishii2002) assess whether a system can meet changing requirements through its lifetime. Guidelines and principles for design of products for future evolution are brought together by Tilstra et al. (Reference Tilstra, Backlund, Seepersad and Wood2015) and extended by recent work of Tan et al. (Reference Tan, Otto and Wood2016) which aims to assess the impact of margins on systems performance and develop a composite margin index.
The ideas of margins enabling redesign is also picked up by Tackett et al. (Reference Tackett, Mattson and Ferguson2014), who address margins in terms of excess, as ‘the quantity of surplus in a system once the necessities of the system are met’ and capacity as ‘the ability of a system to meet future performance objectives using existing system excess’. Their study on refurbishment of ships concentrates on system level properties as excess factors such as volume and show how these values can be calculated to understand how new functionality could be added without prohibitively expensive changes to the structure of the ship. This is based on a functional basis approach (Hirtz et al. Reference Hirtz, Stone, McAdams, Szykman and Wood2002), which offers a set of general functions through which systems can be described. It differentiates between excess in these functions such as excess flows, and excess in the emergent physical properties of the system, like volume, with which the functions are realized.
4 Definition of margins
Margins is an underlying concept that encompasses both the notions of excess and room for a negotiation. Margins occur when a product has not been optimized and therefore has a surplus of some kind. In Eckert et al. (Reference Eckert, Isaksson and Earl2012) a design margin is defined as ‘the extent to which a parameter value exceeds what it needs to meet its functional requirements regardless of the motivation for which the margin was included’.
4.1 Formal definition of margins
This definition is now refined using the following related concepts, where both requirements and constraints come with a ‘must exceed’ and ‘must not exceed’ view.
(i) Requirements ( R ): the values parameters need to reach. These are usually external to the problem coming from the customer or business units, although many requirements are also generated internally. Requirements can be of ‘must exceed’ or ‘must not exceed’ type.
(ii) Constraints ( Const ): values a parameter must reach or not exceed, which can be intrinsic or extrinsic to the problem.
(iii) Capability ( Cap ): the values a parameter could reach regardless of specific constraints or requirements.
(iv) Buffer ( B ): The portion of parameter values that compensates for uncertainties.
(v) Excess ( E ): The value over, and above, any allowances for uncertainties.
Requirements can be stated independently of solutions, whereas constraints are associated with how specific solutions, and surroundings, actually are defined. Constraints can arise from the problem, from the emerging solution, for example carry-over components, or from the process by which it is designed, such as frozen components (see Eckert & Stacey Reference Eckert and Stacey2014).
For example, we want to add weight to a shelf consisting of a board and a bracket, see Figure 1. Initially, the shelf was required to carry 50 N (R), but the board of the shelf has the capability of carry 90 N before failure (Cap) (assuming that the cantilevered board is rigidly fixed at both ends).
Margins can be thought about from different but interrelated perspectives:
(i) Margins on a simple parameter, e.g. for the board only Cap board.
(ii) Margins on a performance parameter, that may be based on the combined effect of multiple parameters, i.e. the margin of the entire shelf, Cap shelf.
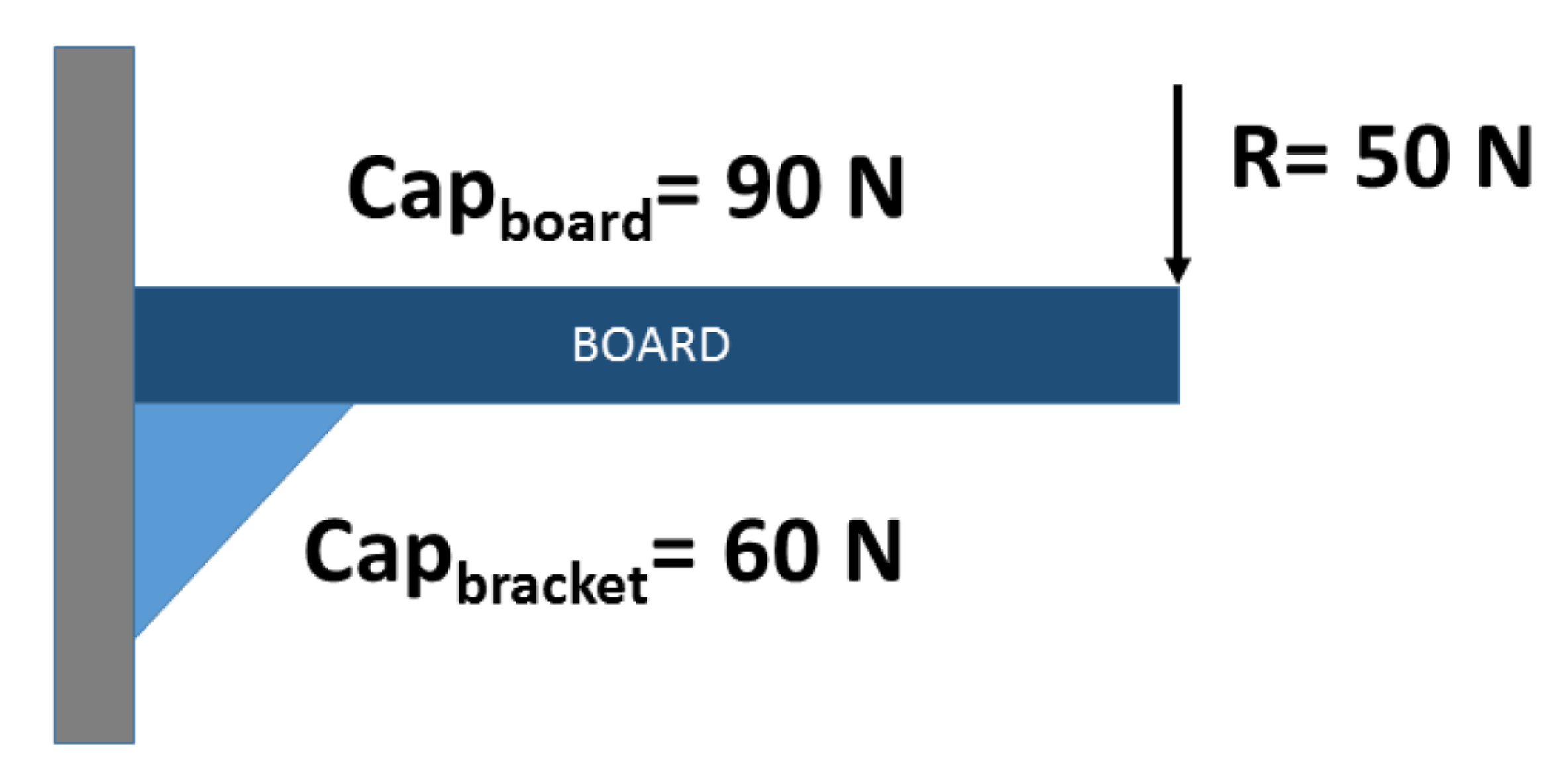
Figure 1. Shelf with capabilities, constraint and requirement.
Margins can refer to single parameters p or vectors of parameters
$\boldsymbol{P}=\langle p_{1},p_{2},\ldots ,p_{n}\rangle$
. Figure 2 shows the margin
M
(
P
) (Eq. (1)) as the difference between the capability
Cap
(
P
) of the component with parameters
$\boldsymbol{P}$
and requirements
R(P)
and constraints
Const(P)
. The margin is therefore the componentwise difference between the capability for a parameter and the requirement for the parameter. For the purpose of the paper it is assumed that margins can be expressed as numerical values. A margin is the useable difference between capabilities, requirements and constraints.
If there is no constraint the margin is the difference between the requirement and the capability.
In a must exceed case Eq. (1) applies,

for a must not exceed case Eq. (2) applies,

In the general case, margins are the minimal difference between the capability and either the requirements or the constraints. The general notion of margins can thus be stated as in (3) covering the four situations as shown in Figure 2.

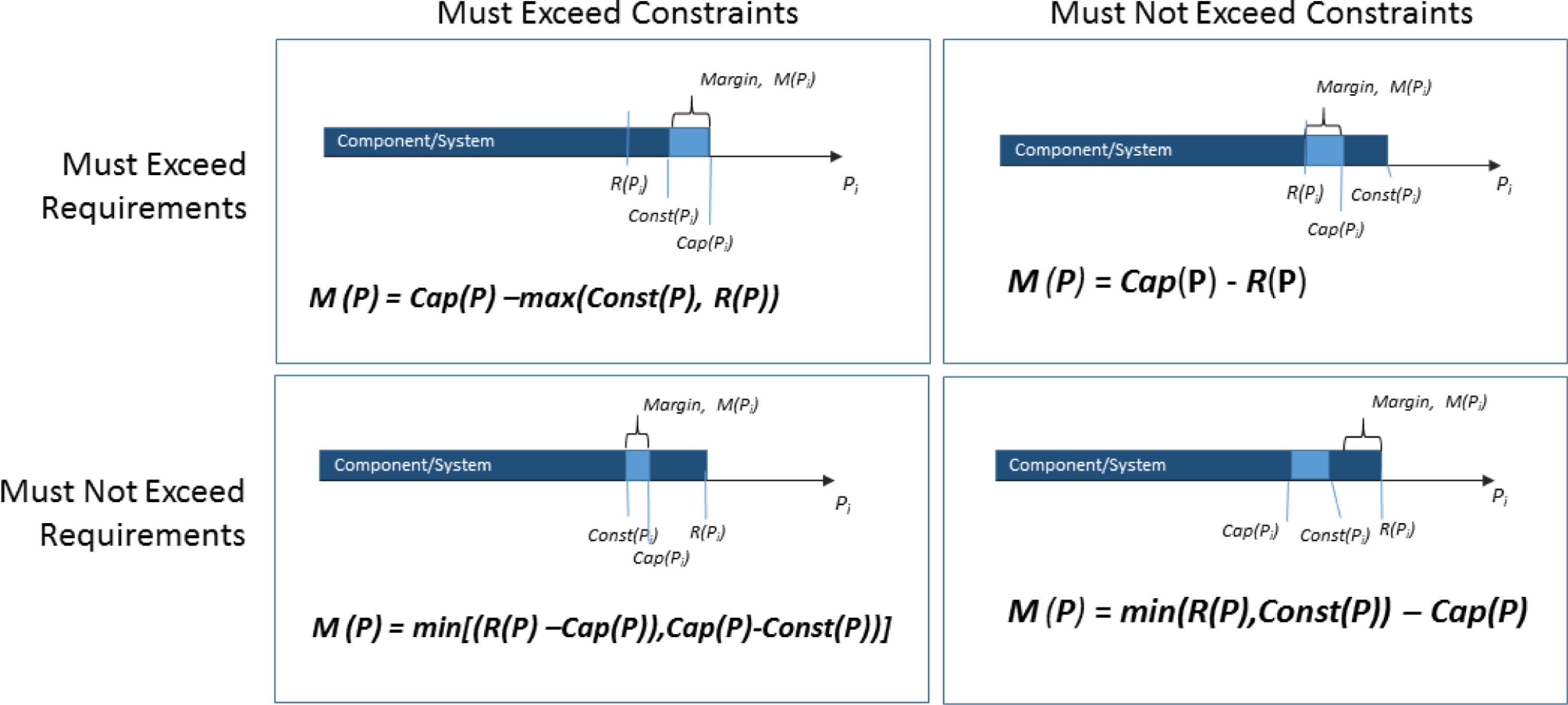
Figure 2. Margin (light blue bar) between requirements and capabilities for a component or system.
In the shelf example, we are in the top right corner in Figure 2. If we only look at the components in isolation, the board has a margin of Mboard = Cap(board) - R(board) , i.e.
Mboard = 90 N - 50 N = 40 N. If we look at the entire shelf, we need to include the constraint of the bracket which has a ‘must not exceed’ constraint. Mbracket = R(bracket) - Cap(bracket ), i.e. Mbracket = 60 N - 50 N = 10 N.
In a design situation we can therefore accept a 10 N change to shelf without a change. For a change of <40 N we need to only change the bracket, but for >40 N we need to rework the board and the bracket.
Many parameters in a product are practically constrained by their physical and functional location in a product. Research on engineering change propagation has shown, that engineers often overlook the constraints arising from other parts of the system, that are not functionally or mechanically linked to them (Jarratt et al. Reference Jarratt, Eckert and Clarkson2004). For example, the size of a component is constrained by the space between the neighbouring components. Another example is the temperature that a component needs to withstand is constrained by the operating temperature of neighbouring components. Adjacent components might heat up and therefore impact the allowable space due to thermal expansion.
In practice it is rarely enough to look at the margin on a single parameter and groups of margins have to be looked at together. The way different parameters combine depends on the nature of their relationship, most of which will be governed by the underlying physics in the product. However, recurring patterns of margins can be detected:
(i) Min/max margins, where the overall relationship is governed by the smallest or largest parameter. This applies for example to clearances, where one would intuitively think of the clearance of a component or system as the smallest values. We could also look at the shelf as a Min/Max relationship and argue that 10N as the smallest margin is the margin on the system.
(ii) Additive relationships, where all the parameters accumulate and only the total is interesting. This applies, in particular to weight, but also to the stack-up of geometrical tolerances.
(iii) Key equations, where while many parameters influence the final design, relatively simple equations express relationships among the small number of key parameters. For example, the fuel consumption in a car mainly depends on the engine and the weight of the car, but is also affected by tyres, aerodynamics etc., which might be neglected in some calculations. In our shelf example we have ignored the link between the bracket and wall, which is assumed to be sufficiently strong.
In any system the margins are interrelated, as the parameters that define the system are dependent on each other. Component or system margins, as the result of components and systems being put together, in turn have their own margins defined on a systems level. This is the case for the shelf, bracket and board example where the components have their margins, and the shelf has a system margin. However, the margins do not decompose or aggregate in a linear fashion within or across a system. Components with large margins can be part of a system that itself has no margins or a subsystem can have margins while many individual components do not. In particular, as margins are hierarchically composed or decomposed, margins can be gained or lost through the way they are combined. As the shelf example illustrates it can be a matter of interpretation whether a part of the system is seen as constraint or an element of the system; this usually depends on the sphere of influence of the designers.
4.2 Margins and uncertainties
At the beginning of a design process many requirements, constraints and capabilities of components or systems are still uncertain. This could be conceptualized as ranges of parameter values; however, in practice designers tend to pick a value that they know from experience would cover most of the range and try to use analysis and testing to firm up the value. For example, for a reused component the capabilities are known from the last version, whereas the requirements and constraints are only emerging, so designers might start off with working on the worst case scenario of the last design episode. For a new development, the requirements and the capability might be given from the outset, while the constraints are emerging as other components are developed.
4.3 Margins as buffer and excess
As illustrated in Figure 3 margins can be conceptualized of as having two elements,
(i) a buffer B , which is used to cater for uncertainties; and
(ii) an excess E , which is the surplus versus the known requirements.
Since the parameter value
$p_{j}$
of a component or system is seldom exactly known, the range of uncertainty needs to be accounted for in design. The precise capability is not known, and therefore the buffer is a range to cater for the expected variation of the component or systems capability. In the same way, the constraints are not known precisely either. As an example, designing a circular tube that needs to have a diameter of 50 mm, may in practice vary in diameter once produced. The required diameter may also need to be changed due to new or refined knowledge in the requirements and loads. Both contribute to an uncertainty justifying a buffer to be assigned, say 2 mm. Assuming standard tube diameters are preferred, a designer may already pick a diameter of 55 mm. This leaves the designer with a buffer of 2 mm and an excess of 3 mm and a combined margin to the nominal design of 5 mm. This situation is shown in Figure 3 and is defined in Eq. (4). As the requirements may either increase or decrease they are drawn as a distribution around the nominal value the requirement. The margins are the surplus above the requirements, which is part of the buffer. In the case of reduction of requirements, this results in an increased excess.

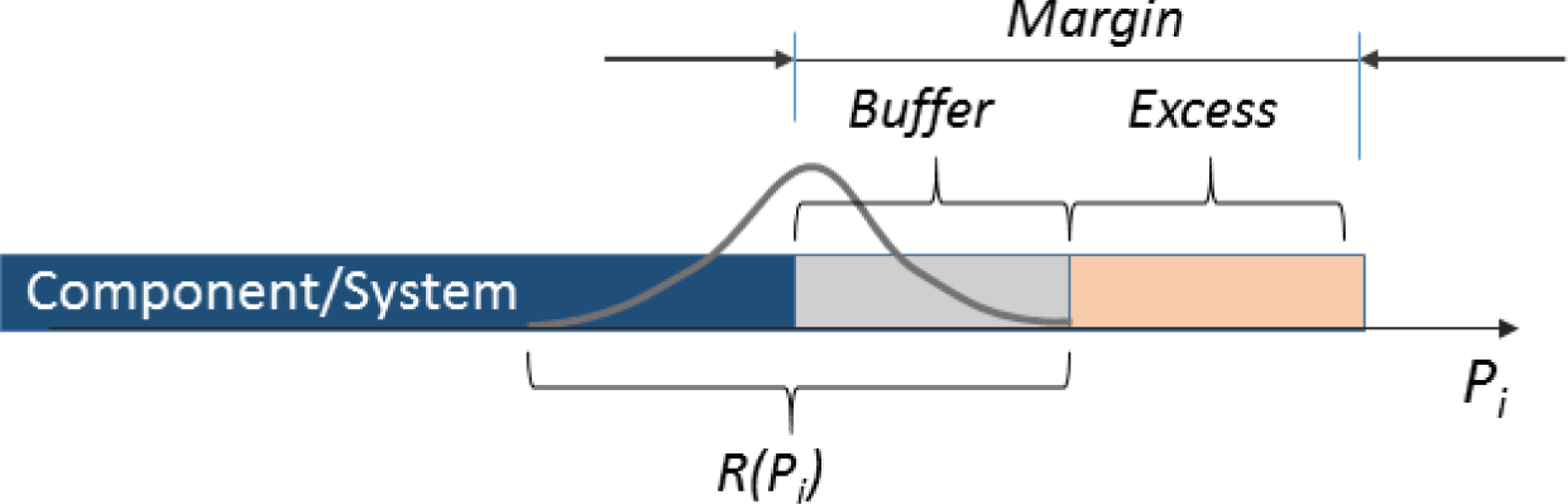
Figure 3. Margins as the sum of the buffer and the excess, accounting for a range of uncertainty.
By reducing the uncertainties on a component, for example by conducting tests and understanding the capabilities better or by understanding the use profiles better, designers can reduce the uncertainty a component is subject to and therefore increase the excess on the component. Note that the reduction of uncertainty can come from firming up requirements, or by testing the precision of the manufacturing method, unless the new requirement consumes the entire buffer. The excess is the part of the margin that designers can make use of, for example to deal with future requirements, product upgrades or subsequent optimization. For a case having both ‘must exceed’ constraints and requirements (top left in Figure 2) combining Eqs. (4) and (1) gives

For other cases, how the excess can be calculated depend on the nature of the uncertainty.
This view of margins relates it to the concept of excess presented in Tackett et al. (Reference Tackett, Mattson and Ferguson2014), but acknowledges that designs are subject to uncertainties by using the concept of a buffer. Product parameters may have buffers, which are not immediately usable in design but offer the potential that they can be reduced and thus release tangible and usable margins. Reducing uncertainty and releasing buffer offers additional options for meeting higher levels of functional requirement or optimizing product parameters against existing functional requirements. However, the reality lies in between. Functional requirements can ‘increase’ taking up some of the parameter margins released but at the same time some of the newly available margins are retained allowing for further future evolution of functional requirements.
Another scenario occurs when one parameter is ‘frozen’ and the design objective is to maximize performance by varying other parameters within their limits. For example, maximizing performance from a newly developed material whilst geometric parameters remain unaltered. Product performance is the measure of function and behaviour, i.e. how well the product performs what it is designed to do. Margins fall into two categories, margins on performance parameters and margins on physical properties of a product. The latter are typically geometric and material property margins, which describe how much the form or material properties of a product or component can be changed before the complete satisfaction of requirements of specific component or sub-system is affected. Note that cliff edge effects come into play, where small changes can lead to the redesign of an entire system. An important type of geometric parameter margin are clearances surrounding a component. These allow the component to grow or to be moved and can therefore absorb potential changes to the product. Clearances can be difficult to handle, because they are not explicitly represented with a particular component but rather deduced from relationships between the components.
If requirements unexpectedly increase, the designer can choose between reducing the excess or by finding means to reduce uncertainty and thereby moving buffer into excess. This is an important insight for industry, as a change can be absorbed by the existing design if its capabilities are better understood by improved testing or improved mathematical modelling.
In many cases it is not possible to determine exactly the division between buffers and excess, since the uncertainty buffers are seldom fully quantifiable because people consider different uncertainties to be relevant. As Van Bossuyt et al. (Reference Van Bossuyt, Dong, Tumer and Carvalho2013) point out the attitude to risk varies. However, some industry sectors, like the aerospace industry, have well developed processes to capture the risks. What was found in interviews with the truck company, is that in practice engineers use ‘worst case scenarios’ that state maximum values rather that ranges. In particular as the demarcation between buffer and excess might be subjective, the concept of buffer and excess provide a useful vocabulary to discuss how much of a component can be repurposed.
5 Different margins across the development process
As the multitude of connotations on margins found in the literature in Section 3, the term margin is used in the English speaking aerospace industry as an informal, but fairly universal term. Other languages and industry sectors use different vocabulary to express margin concepts. This section gives a brief overview over the terminology used in the truck company. The terminology might be different in other companies, but has been included to draw attention to the fact that margins are everywhere, if one looks for them.
5.1 Different terms for margins across the design process
In the truck company different groups of engineers used different words to talk about the same underlying phenomenon of margin, so that designers in one group are often not aware of margins being added by another group. Figure 4 illustrates how the different margins can be accumulated. The findings were also presented to engineers in the jet engine company during validation interviews, who instantly related to the fact that margins are hidden under divergent terminology.
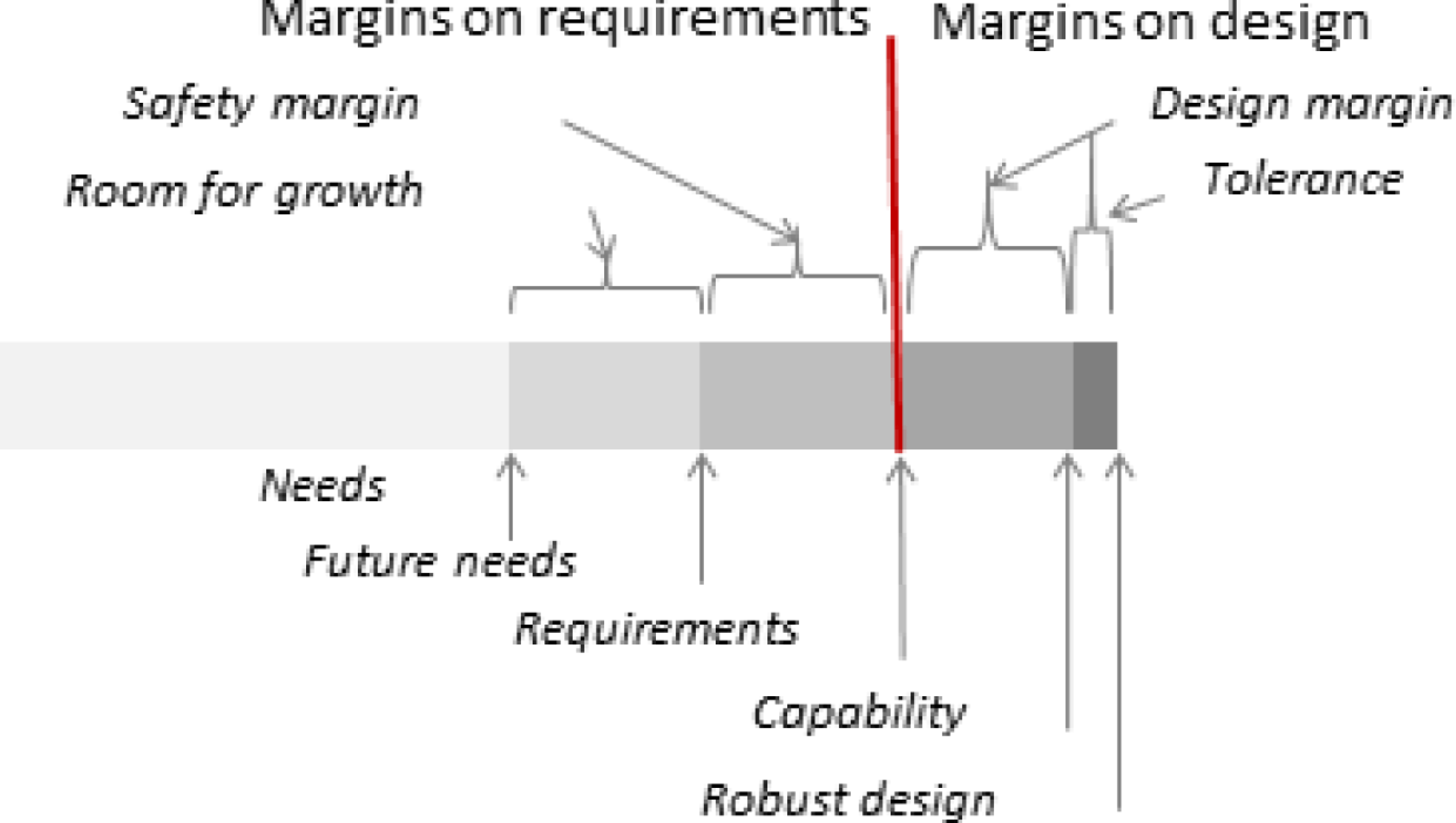
Figure 4. Cumulative effect of margin concepts.
Design teams may add safety margins to the requirements of the components to cater for uncertainties in use include serious misuse of the product as well as emerging requirements and uncertainties during the development process. As trucks have large safety margins on the requirements, it is possible to push the worst case scenarios applications to their very limits.
Companies are however, not just considering the current product, but often have future generations of the product in mind. They aim to redesign major systems every few generations and therefore need to plan in margins against the predicted requirements of future product. For example, if the latest generation system needs 12 electronic ports, but the company expects that each subsequent generation will add 2 ports and therefore designs a system with 16 ports, so that they do not have to redesign the ports for another two generations. Incorporating this room for growth arising from product planning comes at a cost, because the current system is overdesigned. However, it is not only allowing for future generations of the product that might lead to overdesign, but also developing versions of the same product. Therefore, there is a tension between the optimization of an individual product and the flexibility which margins can give an organization (see Isaksson et al. Reference Isaksson, Lindroth and Eckert2014).
Overdesign is also the way the margins are described from a value engineering perspective. For example, the shelf board that can carry 90 N rather than the required 50 N might be heavier or more expensive than one that only carries 50 N. Therefore, the component might be targeted in cost saving activities, for example when a company is thinking of bringing out a cheaper product that is targeting another market. Overdesign is also an issue when companies are trying to synchronize service intervals on a product. For example, jet engines are maintained at regular intervals and any component that is likely to cause problems during the next service intervals is repaired or replaced. Unless the condition of the engine components are known, there needs to be a sufficient margin to failure at any state of operation. Typically, many components are designed to be serviced at scheduled major overhauls only, and individual components may be replaced or repaired pre-maturely with their real capability (Thomsen et al. Reference Thomsen, Kokkolaras, Månsson and Isaksson2017). This is seen as an overdesign issue and a candidate for optimization.
Safety margins cater against risks and are allocated to assure that the product is safe and reliable to use, whereas design margins buffer against various uncertainties such as propagated changes coming from other components. Safety margins (value) or safety factors (percentage) typically denote the margin for safety critical failure, whereas design margins have a more general meaning. Aerospace companies often talk about safety margins because certification requirements include safety margins or safety criteria.
When designers focus on safety rather than a cost, they often speak of system redundancy or back-up solutions in the products that enable the product to deal with unexpected situations. This is typically the case with a redundancy system in case of failure, such as enforced in aerospace by the certification requirement that no single failure must lead to a catastrophic failure of the system.
Margins in the form of tolerances are also added from a manufacturing and assembly point of view to ensure that a product will be safe and reliable for a given manufacturing variability. This is considered in robust design (Chen et al. Reference Chen, Allen, Tsui and Mistree1996). Also geometrical tolerances can be seen as a form of margin, that can impact both functionality of the product (gaps, fittings, etc.) and product quality (noise, vibrations). Geometrical tolerances need to be taken into account during design, since they directly affect the margin that can actually be used in a context. If margins become critical, tolerance may become critical in this respect.
Another concept used in practice, are clearances. Clearances are a special form of margin, were the empty space between components can be treated like a component. Clearances are affected by design configuration. Examples are harnessing that has to fit into a passage or the packaging components in a physical space such as an engine compartment of a car. Clearances are also needed to be considered in the detailed definition of designs such as where tolerances stack up and affect both perceived product quality and manufacturing clearances for assembly (Söderberg et al. Reference Söderberg, Lindkvist, Wärmefjord and Carlsson2016).
5.2 Knowing margins
While a component margin is an intuitive concept, it is in practice difficult to know what the margin on a component actually is. For a finished product, margins can be established through testing or potentially through simulation. However, in current industrial practice most products are tested to establish that they are capable of meeting their requirements in the specified way (Tahera et al. Reference Tahera, Earl and Claudia2014). The actual margins of the component can be revealed through expensive destructive testing. However, many margins can be elicited through computer simulation.
The margins on a component under development are not well defined. Typically designers of a complex product such as the truck in the case study start from an existing design by identifying the excess on major systems against the new requirements. While companies are usually not aware of all component margins, they often know the component margins that have become critical in a previous project. For example, if a clearance has been nearly used up and a real effort was needed to fit everything in when fitting cables through a clearance. The designers now know that it is very unlikely that they can push this component (or clearance) further. Such knowledge of margins when evaluating previous designs gives designers an understanding of high risk areas for the new design.
Designers start with some awareness of critical margins from the previous design. They look for excess and critical margins because they know that margins on components can absorb change, while margins that are exceeded can become change multipliers. At the beginning of a design process the designers therefore evaluate the previous design as to where they can make improvements and which parts of the product might be overdesigned and therefore could absorb higher requirements. However, often different teams look simultaneously at the possibility of change in a product and target the same components or areas. For example, the electronics team identifies a clearance for another cable and the design team is planning to increase the size of an adjacent component and wants to fill up this space. This might be picked up at a formal design review, but between reviews it requires somebody to stop the potential problem before it leads to unintentional rework. This is a typical case where an explicit tracking of margins could avoid problems.
Throughout the design process both the requirements and the capabilities of the product are subject to uncertainties which are reduced throughout the design process. Requirements are set and parameter values are frozen at particular points in the process. This affects both the overall value of the margin and the distribution of the buffer and excess over time in the design process.
As the example in the following section will illustrate, besides mitigating product risk and adding to product cost, margins also play a significant role in managing the process risk through reducing the risk of unplanned iterations. In the following example the company has to decide which material to pick based on the cost of the material and two risk factors: that of delaying the design process by needing to adapt a solution late in the process and therefore potentially risking delays to the product delivery; and the risk to product quality from using a less mature solution.
6 A case on temperature margins in jet engine design
A typical situation is where a component supplier to an engine system integrator needs to decide on a material to use, in a phase where the required engine gas temperature is still not determined. The design temperature is set by an initial estimate from the engine integrator (OEM) but is likely to change. The proposed notion of margins is applied to the case to demonstrate how an explicit knowledge of margins can aid the design decision process by articulating and visualizing effects related to margins of material selection strategies.
In the following case we have a ‘must exceed’ requirement that evolves during product development, and three alternative design options, each with different capabilities.
The case selected is the design of a jet engine component, see Figure 5, located in the turbine section which is exposed to high temperature gas flows and has to transfer mechanical loads between the shaft-bearing and the engine mount. Principally, the higher gas temperature the component can operate under, the better. This is why the OEM is interested in allowing higher gas temperatures to offer more efficient engines to their customers. However, higher gas temperatures reduce the life expectancy of the component and is a key reason for cost increase since more advanced designs and materials are needed. The gas temperature is a key design requirement R t and a real design is also heavily constrained by the capabilities of other systems that cannot be influenced by the design team. These capabilities are is set by the OEM in dialogue with the end user (Airline) and in compliance with certification authorities.
The materials available have a capability ( Cap it) that is determined by complex relationships between the material composition and the actual design solution. To withstand a higher gas temperature, either more advanced materials, smart thermally robust designs or even cooled design concepts are explored by the component design team. A relevant but simplified design trade-off is therefore the trade-off between three alternative materials, equivalent to three alloys at different cost.
In the case, the company prepares for anticipated change of requirements and considers the selection of one of three alternative alloys for three potential gas temperature updates.
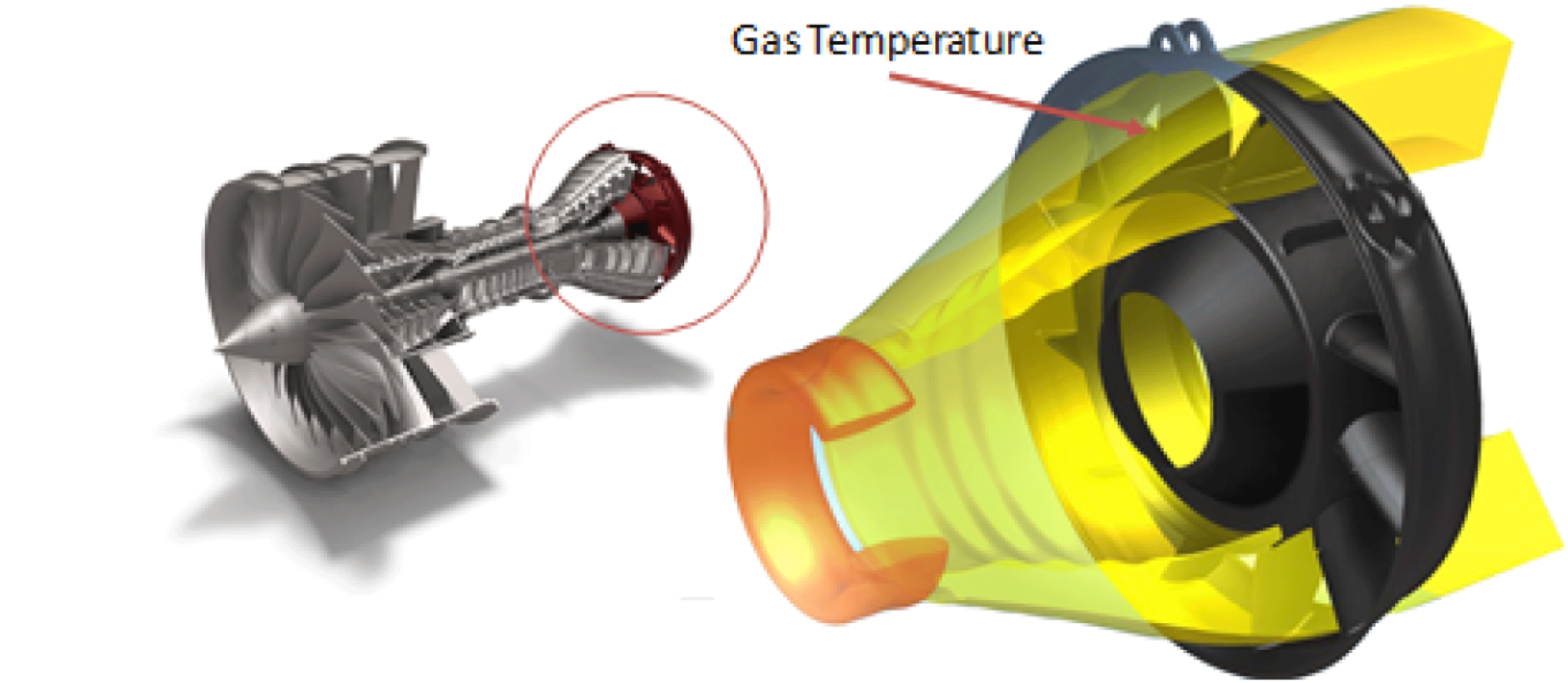
Figure 5. A turbine rear structure (TRS) of a jet engine exposed to hot gases.
At the beginning of the design process, the baseline design temperature, R 1 is agreed with the OEM based on the initial system architecture of the engine. This value might vary in course of the design process by as much as 10%. Therefore, the company needs to leave a margin for this change. Later the temperature is likely to be updated to, R 2, as the OEM is gaining confidence about the new design. Again this might have a margin, however, a smaller one as the temperature is firmed up, say 5%. The company is also aware that the OEM is working on an alternative on whole engine level that may imply an even higher temperature as a worst case scenario, R WC . This worst case scenario has no further margin. The three temperatures are shown in Table 1.
Table 1. Temperature Requirement (Gas Temperature)
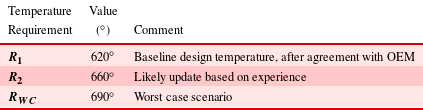
Table 2 shows the capability of three candidate design solutions with alternative materials, Material A, B and C, each with different capabilities
$\mathit{Cap}_{i}$
. We assume the material is the only difference between these design concepts, and the cost associated with the materials are known. Minimized cost is by default the best option, but the cost of failing to meet the requirement is far greater than the cost of selecting a more advanced material. The company would prefer to use Material A as it is the most mature and cost-efficient option.
Table 2. Capability of alternative design options

This gives us the following margins with buffer and excess for the three materials, as presented in Table 3. Note that Material A has not enough margin against the first required temperature, and has no excess. Material B has a small excess against the worst case scenario, which is flagged up since it may need an additional design margin.
Table 3. Margins against the materials for the different requirements

In practice, as required temperatures are updated at discrete times,
$t_{i}$
, that is reflected in Figure 6. The worst case scenario, R
WC, is only kept as an option early in the design process, and is actively dropped as a scenario during the development process by the OEM. It is still relevant to consider for the component supplier as a possible scenario for future upgrades and derivatives. At
$t_{2}$
,
$R_{2}$
becomes the required temperature, with reduced uncertainty (5%). The company also conducts its own activities to reduce the buffer, e.g. by reduced uncertainty through higher fidelity testing and refined analyses.
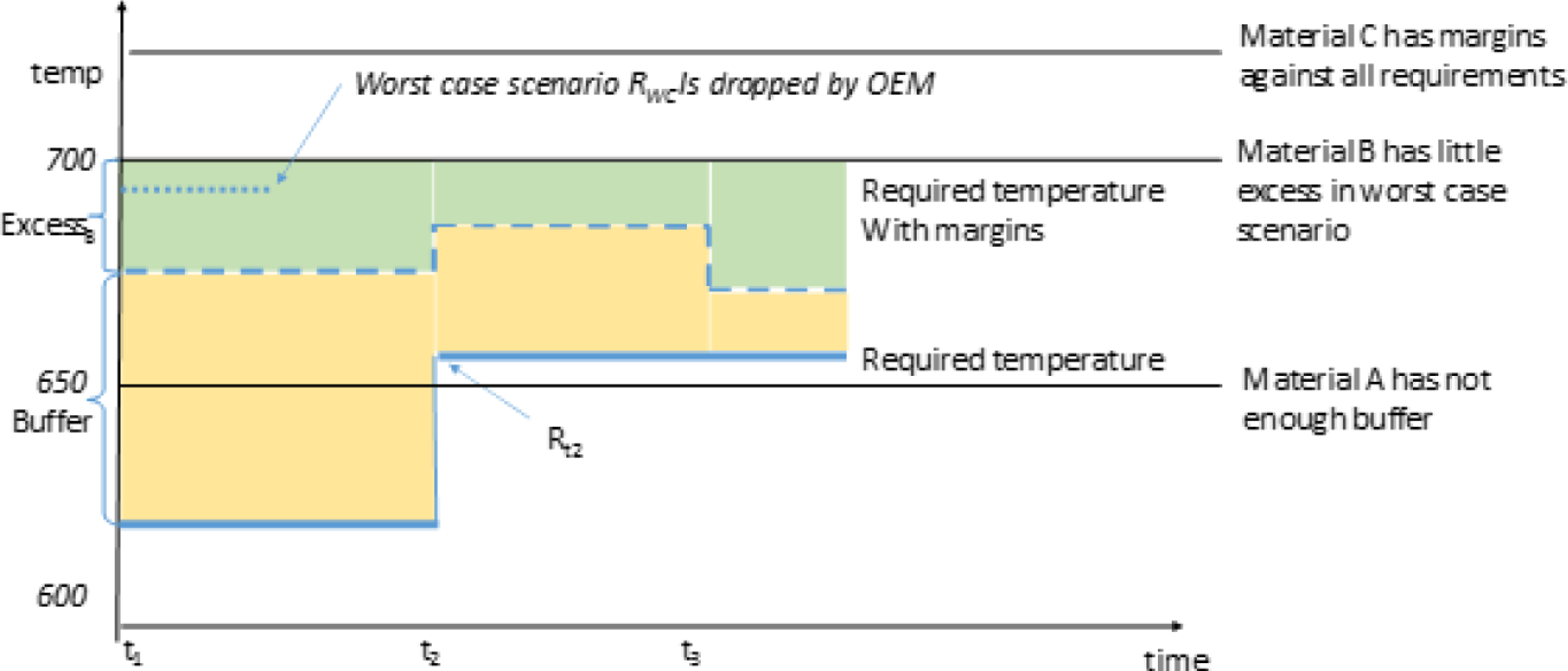
Figure 6. Margins profile along the development process.
Figure 6 shows the buffer and excess for material B as they change over time. In a real project, changes are more frequent, making it difficult for engineers to keep track of the current margin. Material A does not have sufficient margin, but the company may still pursue the material in the beginning by reducing the uncertainty associated with the buffer. In practice, this is a common reason for dialogue with the OEM. If the company would rely on Material A only, this may push them into an unwanted iteration. Material C has a huge excess and would potentially be an option that would allow a firm decision in an early phase, yet it has not been fully validated and would consume additional time and resources before selected. Material C is ‘the material of the future’, and the company needs to gain knowledge of this option. In aerospace, this would be characterized as a material with insufficient technology readiness (TRL) (Mankins Reference Mankins1995). To reach a high enough TRL level for use in products it needs to be assessed in product realistic conditions.
At any given time, the designers assess the buffer and excess for the design alternatives. Where there is buffer, they aim to reduce the buffer through testing, refined analysis or any other means to reduce the uncertainty requiring buffer. Excess can be targeted for optimization, or kept strategically as room for growth. The buffer and excess for a given design option (in this case the materials) form a margins profile that is used for planning the development process and as a means to selecting materials.
Given the margins profile, the company can articulate a design strategy based on margins such that a design team can assess the impact of alternative design strategies and match with the most appropriate design alternatives.
Initially, all three options are worked on in parallel, since all might actually be required. Material C can be dropped once the worst case scenario can be eliminated. Material A becomes obsolete as the temperature update is released by the OEM.
The margin on the temperature is at the heart of important trade-offs, which the company could benefit from sharing internally to inform decision making and process planning:
(i) Capability against maturity, i.e. product risk, where the mature option, material A, has too little margin to handle the uncertainty in the gas temperature, and material C is too new and therefore seen as risky.
(ii) Internal against external reduction of uncertainty: internal measures to reduce uncertainty and therefore reduce the buffer are expensive, but provide design freedom, compared to waiting for the OEM to adjust the temperature.
However, an explicit understanding of margins could also aid managing the design process and the iteration loops with the customer. In a similar way to the Dawson et al. (Reference Dawson, Fixson and Whitney2012) study, the company is faced with two interconnected iteration loops: the internal loop of preparing a solution and the convergent iteration loop with the customer company. In both cases parallel iteration occurs, one within the design team of the company focusing on the component design options, and the other in the OEM on the system level.
Also in the same company Larsson et al. (Reference Larsson, Larsson, Bylund and Isaksson2008) studied such parallel design processes and the company’s collaborative design work with an OEM. They highlighted the importance of shared understanding of capabilities of the component vs. the requirements originating from the evolving system level behaviour. In this situation, an explicit representation of margins and their relation to the evolving requirements was lacking and put the design teams into situations where design decisions had to be made based on their own predictions rather than on shared understanding between the system level and the component level design. A margins profile in such design situations would provide the design teams with a means to
– Differentiate between margins due to uncertainties (buffer) and the margins due to design choices (excess).
– Integrate the heterogeneous set of design aspects into a single representation, something that allows gathering of contributing information more easily.
– Communicate the design options with the integrator (OEM) for a richer exchange of design information.
Design iteration is inevitable, yet what is critical to avoid are the unplanned corrective iterations that often occur as a consequence of parallel iteration where the margins are not understood or shared (Larsson et al. Reference Larsson, Larsson, Bylund and Isaksson2008). In this particular case going with material A only at the beginning, would have required the company to take up a second material, either B or C, at a later date in a corrective iteration, which would lead to significant risk of delays. Starting with material B at the beginning might seem like a good option, as it is much cheaper than material C. From hindsight it would be a workable choice. However, one that would carry significant risk through the process. The excess would also be small, so that material B is likely not to be sufficient in the next product generation. In the ‘real world’ underlying case, the engineers at present consider multiple materials but without numerical means to systematically justify selections with margins profiles. Material C come out as a strategically interesting choice, due to its high capability. Investing in improving the confidence in the material, e.g. raising the TRL level through materials development and testing, can thus be seen as a means to reduce buffer and thereby gain excess.
There is further evidence that margins are not communicated across the supply chain. Design requirements are imprecise within a particular range (Fernandes et al. Reference Fernandes, Henriques, Silva and Moss2014). However, they are frequently represented as crisp values, whose range needs to be estimated and added as buffer based on past variation as in the example of the gas temperature. This is probably amplified across organizational boundaries between the supplier and the customer, who have different expertise (Bucciarelli Reference Bucciarelli1994). Effective communication requires that designers achieve a degree of shared understanding about the whole product and each other’s tasks (Kleinsmann & Valkenburg Reference Kleinsmann and Valkenburg2008) as well as finding representations that can be understood by the different groups (Star Reference Star2010). Stacey & Eckert (Reference Stacey and Eckert2003) point out that to communicate information with less unambiguity several dimensions ought to be considered: precision, typicality, commitment to the value, sensitivity, input confidence, understanding, and confidence in the stability of the value. The aim is to avoid misunderstanding of specifications. The same categories could complement margin information to communicate parameter values.
While this openness could contribute to reducing the risk of the iteration cycle, it is questionable whether designers are fully willing to reveal the exact state of information or whether they withhold information with a certain bias as proposed by Austin-Breneman et al. (Reference Austin-Breneman, Yu and Yang2015). However, the decision on how and when to reveal margins should be taken strategically rather than being forced through lack of awareness. Having margins that companies can draw on enables firms to respond quickly to changes proposed by the customer. This enables them to present themselves as collaborative and responsive. In case of changes beyond what was previously negotiated to be expected, companies might also have the chance to charge for work that they do not need to be carry out. The business rationale of individual actors in a supply chain might override the benefits that could be gained by sharing margins.
7 Conclusion and discussion
The paper argues that in industry, margins occur under many different names throughout the product development process; and introduces a common terminology in terms of margins consisting of buffer against uncertainties and excess which can be used in the next product generation. Excess can therefore be increased by reducing uncertainty and moving parts of the buffer to usable excess.
Margins are at the heart of many design decisions throughout the product development process. When designers can separate the excess and buffer components of the margin, two essentially different ways to improve the design occur. Improving design means moving parts of the buffer into excess. This can be done either by improving the capability of the design alternative or by reducing the level of uncertainty associated with the design alternative.
This paper has set out to define a generic vocabulary for margins that allows people in industry to nuance the talk about margin. This gives raise to several streams of research that we are hoping to pursue in the future. The margin profile diagrams in Figure 6 can form the core of a margin tracking tool, which records margins and requirements and the rationale associated with changes to margins or requirements. This paper focuses on identifying margins, but this raises the question about what margins should be designed into a system when it is designed. A method for setting suitable margins is also further work.
Setting margins is critical to product and process trade-off. Reducing the uncertainty of design alternatives require additional analysis and testing activities, that come with additional process cost during development.
Let us revisit the examples from the beginning of the paper in terms of margins:
– The situation where vibration was suddenly detected in a helicopter and an interface had to be redesigned. This example arose in the case study reported in (Eckert et al. Reference Eckert, Clarkson and Zanker2004). Here clearances were used up and components were pushed together until they were so close that they touch if they expanded due to heat expansion.
– The case where the actual operation of the product resulted in a higher load than first expected. This can be seen as having excess left at the end of the product development process, which can be used when the craft is recertified.
– When the component was considered too expensive and was targeted for cost saving redesign. The company looked for an excess in product that it can optimize. It is possible to move buffer to excess by reducing uncertainty. The company can reduce uncertainty, e.g. by testing or reducing uncertainty in requirements by negotiating with its customer and thereby release margin.
– A frequent warranty case forces a recall and redesign of a system. In this case the safety margin was not big enough or it had been inadvertently compromised by design changes.
In all of these cases, the notion of margins would have improved the companies’ ability to communicate and address the problems. We propose to capture and record margins from the beginning and throughout the development process, and manage margin profiles.
Future research will address the role of design margins in different kinds of design activities, and develop mathematical models to support the effective management of design margins and creating margin profiles.
Acknowledgments
The authors wish to acknowledge Volvo and GKN for funding the research contributing to his paper and Safaa Lebjioui participating in interviews on design margins, and Chalmers via the Wingquist laboratory and Area of Advance Production.
Nomenclature