Background
Digital information is doubling in size every two years.1 Enabled by faster computers, improved connectivity, and expanding mobility, we created, saved, and transferred nearly 2 petabytes (PBs) of information every minute (1 PB = 1015 bytes) over the Internet in 2016. This explosion of “big data” and ever-present computation is rapidly migrating to the “Cloud,” thereby enabling augmented reality, deep learning, and perhaps artificial intelligence. The oncoming Internet of Things (IoT) will broadly monitor and animate the world around us to generate even more data. A recent study by the International Data Corporation (IDC) forecasts that total stored data will grow by an order of magnitude from ∼16 zettabytes (ZBs) (1 ZB = 1021 bytes) in 2016 to near 160 ZB by 2025.Reference Reinsel, Grantz and Rydning2 Although much of this data is transient, a substantial fraction must be retained—stored locally in personal computers (PCs), media players, game boxes, and security systems; on servers and local networks; and in the public and private Clouds. Hard-disk drives (HDDs) are the core of this storage.
HDDs will continue to be the highest capacity, low access-time storage technology for the foreseeable future. To keep up with demand, HDD storage capacities have steadily increased for the past 60 years. HDD capacity has mostly grown by increasing the areal density (AD) of the data stored on the disk. AD has increased by a million-fold in the past 60 years, with a compounded annual growth rate (CAGR) of about 30%. Figure 1 shows that AD growth has occurred through a steady progression of technological and materials innovations. Recently, AD CAGR has been slowing as perpendicular magnetic recording—in which the magnetization in the recorded bits points perpendicular to the plane of the disk—approaches its practical limit near 1.5 Tbpsi (terabits/in2).
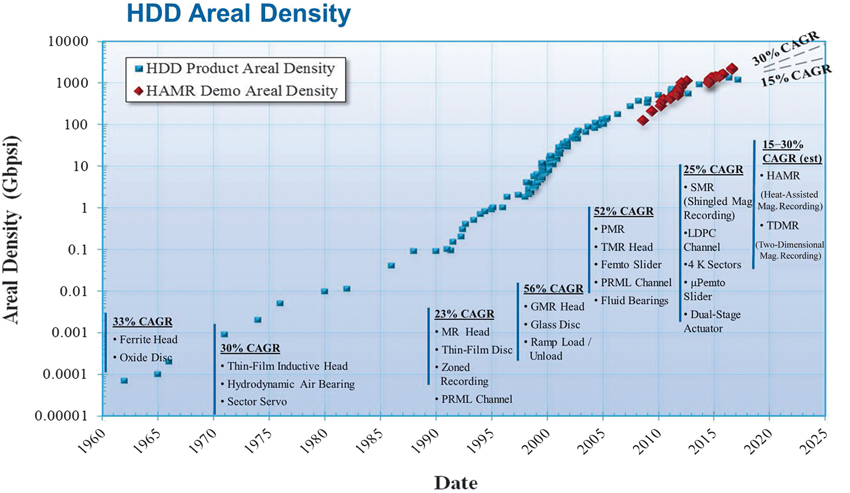
Figure 1. Hard-disk drive (HDD) areal density (AD) has grown at an average rate of 30% for more than five decades. This remarkable trend has been enabled by a steady progression of materials and technological breakthroughs, which have triggered periods of even higher compounded annual growth rates (CAGRs). Recent heat-assisted magnetic recording (HAMR) demonstrations (red diamonds) show AD entitlement above conventional perpendicular magnetic recording (PMR, blue rectangles), which is crucial to enable future growth.
Figure 2 charts the future HDD technology roadmap with a steady progression of storage technologies from today’s perpendicular magnetic recording (PMR) to heat-assisted magnetic recording (HAMR) to heated-dot magnetic recording (HDMR). (See the Hono et al.Reference Hono, Takahashi, Ju, Thiele, Ajan, Yang, Ruiz and Wan3 article in this issue for details.) Like Moore’s Law for integrated circuit density, HDD AD is enabled by dimensional scaling and ongoing materials and device engineering. However, scaling inevitably reaches limits—as PMR has today. To continue to increase AD, a new paradigm such as HAMR is required.
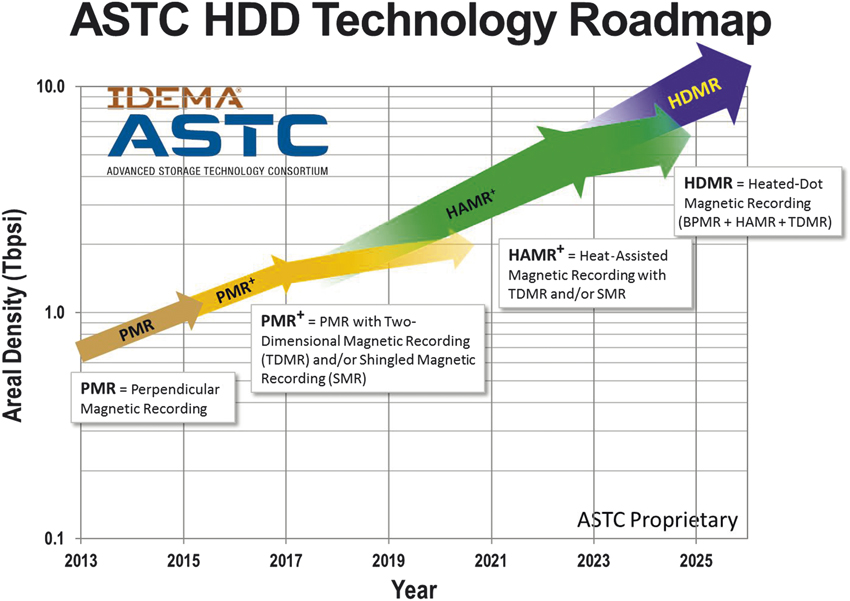
Figure 2. The Advanced Storage Technology Consortium (ASTC) issues the technology roadmap for the hard-disk drive (HDD) industry. Technologies often follow an s-curve trajectory with performance increasing slowly in early development, rapidly as it matures, and slower again as it reaches physical limits. Perpendicular magnetic recording (PMR) is reaching its limit near 1.5 Tbpsi. The next technology S-curve is heat-assisted magnetic recording (HAMR), with product introduction in 2018. HAMR is followed by heated-dot magnetic recording (HDMR) around 2023. Note: BPMR, bit patterned magnetic recording.
HAMR breaks the PMR constraint by locally heating the media near 450°C (to make it easier to write data) and then rapidly cooling it (to ensure long-term data retention). At 1 Tbpsi, heating must be localized within a 10 nm × 60 nm bit to avoid compromising neighboring data. The new technology poses challenges that require new media, new heads, and a new head–disk interface (HDI), all of which demand new materials. Figure 3 illustrates this wide range of new HAMR materials and requirements.
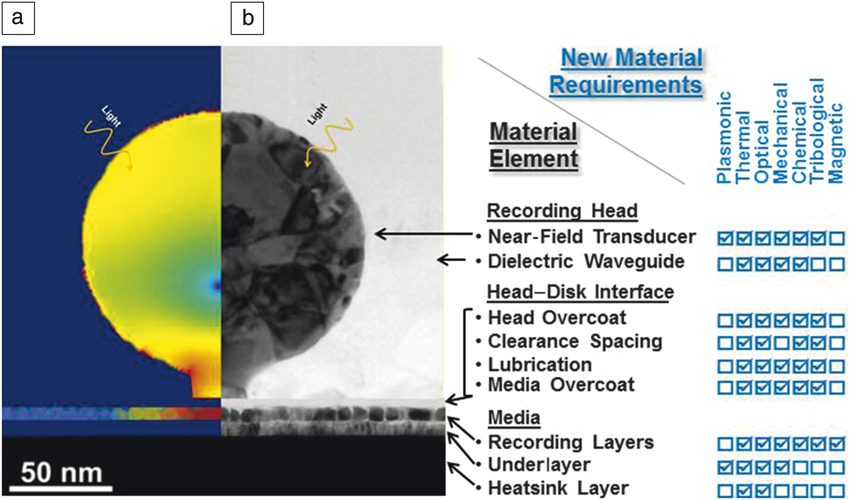
Figure 3. The recording head, head–disk interface, and media require new materials, new structures, and a wide range of new material properties. (a) Temperature profile during operation, with blue being cool temperatures and red being hot ones. (b) Electron micrographs of head and media.
This article introduces materials that address these challenges. For in-depth reviews, see the HAMR articles in this issue that cover media, heat-assisted writers, advanced readers, HDI, and thermal engineering.
Recording physics
Magnetic recording differs from most digital technologies in two distinct ways. First, each bit of information is stored on multiple grains, with grain structures that differ substantially from bit to bit. This avoids the need for expensive lithography specific for each bit, but places obvious demands on materials engineering because grain-to-grain nonuniformities lead to noise in the data. The second, perhaps more obvious distinction, is that magnetic recording involves physical movement of the head over the disk. This again reduces the lithographic demands because only one dimension of the recording head requires tight definition for the two-dimensional data on the disk. The other dimension is set by the head movement and the rate at which the head magnetic field reverses. However, this physical movement means that the materials must be able to withstand frictional forces and respond quickly for a high data rate. Therefore, the strengths of magnetic recording, very high density, and low cost lead directly to many of its materials issues.
Conventional PMR uses only a magnetic field to write the media. The field is confined to a small area with dimensions of ∼60 nm in order to write small bits (more bits per area = higher density) and not overwrite neighboring bits. The quality of the recording therefore depends substantially on the quality of the magnetic field gradient produced by the write head.
The ability of PMR to progress to ever higher ADs is now limited by the simultaneous need for smaller media grains (to preserve signal-to-noise ratio [SNR]), higher media magnetic anisotropy (to protect against thermal fluctuations that inadvertently switch the grain), and sufficient head field (to switch the high anisotropy grains). Unfortunately, the saturation magnetization of known materials limits the head field available at small dimensions. Overall, this combination of constraints is labeled the magnetic recording “trilemma” and has posed the primary obstacle to continued progress in recent years. The most likely solution is HAMR, which breaks the trilemma by recording information at a high temperature, where anisotropy is small, but storing information at room temperature where anisotropy returns to a large value.Reference Kryder, Gage, McDaniel, Challener, Rottmayer, Ju, Hsia and Erden4
The bit size in HAMR is determined by the optical spot size that must be well below the diffraction limit.Reference Challener, Peng, Itagi, Karns, Peng, Peng, Yang, Zhu, Gokemeijer, Hsia, Ju, Rottmayer, Seigler and Gage5 In other words, recording occurs in the optical near field, and the quality of the bit edges will depend on the quality of the thermal gradient, which is determined by a combination of optical spot size and thermal properties of the media. The requirement of high gradient means that the peak temperature in the center of the typically Gaussian-shaped spot must substantially exceed the write temperature, but the tip (narrowest part) of the Gaussian has unworkably low gradients. Therefore, multiple parts of the recording system, including lubricant, recording media layer, and the head near-field transducer (NFT) that focuses the beam must be composed of materials that can withstand temperatures around 450°C, an issue that has already absorbed many years of academic and industrial research.
High-quality bits demand many additional material properties. The media cools quickly (nanoseconds), implying that the Zeeman energy (product of moment and applied field) must substantially exceed thermal energies to avoid freezing in the wrong magnetization direction. (The physics is the same as annealing a molten liquid: fast anneals do not allow sufficient time for the lowest energy state—a crystal—to form.) This requirement demands high magnetization materials. Bit boundaries must be accurately placed to the extent allowed by the inherent grain structure—this demands uniformity among grains, particularly with respect to writing temperature. However, the writing temperature is highly proportional to the Curie temperature (T C), which is the temperature at which ordered magnetization is lost. Thus, low noise requires narrow T C distributions. It is important for high data rates that the energy be quickly transferred from the spins to the lattice: this rapid energy transfer is accommodated by materials that have capability for rapid ferromagnetic relaxation (high damping), still another material requirement.
HAMR media
In some respects, the most fundamental single component of a magnetic recording system is the magnetic recording medium, because this material will store the information. The requirements for the material are both numerous and diverse.Reference Weller, Parker, Mosendz, Champion, Stipe, Wang, Klemmer, Ju and Ajan6 At a simplified level, the media comprises (1) a heatsink, perhaps Au, to control heat flow; (2) a soft underlayer, such as multilayered FeCo, to magnify the field from the recording head; (3) a recording layer; and (4) a protective layer (see Figure 3). While all of these will be examined in this issue, the recording layer probably has the most demanding set of requirements.
By a substantial margin, both research and commercialization efforts have mostly been directed toward the crystallographic L10 phase of FePt because it offers the potential for high anisotropy and suitable Tc. Other materials examined include CoPt, CoPd, and less promising rare-earth compounds such as SmCo5 and Nd2Fe14B. However, the high anisotropy is obtained through a high degree of chemical ordering that is usually attained only at high processing temperatures. These temperatures are not conducive to growth of small grains, leading to intensive efforts by materials scientists to alleviate this tension. Furthermore, recording media require a columnar microstructure with magnetic isolation of each grain, yet the media must also have adequate mechanical strength and surface smoothness. These diverse requirements imply that the grain boundaries must be carefully engineered.
The recording layer is usually grown by sputtering. Growth of high-quality FePt in the proper perpendicular orientation requires an MgO seed layer (See Hono et al.Reference Hono, Takahashi, Ju, Thiele, Ajan, Yang, Ruiz and Wan3 on HAMR media for discussion), which poses several additional problems, including poor thermal conductivity of the MgO and the tendency of MgO grain boundaries to yield FePt grains with longitudinal (i.e., not perpendicular) anisotropy.Reference Pandey, Wang, Shiroyama, Varaprasad, Sepehri-Amin, Takahashi, Perumal and Hono7,Reference Ho, Zhu, Kulovits, Laughlin and Zhu8 In addition, growth naturally produces a distribution of grain sizes and, most alarmingly, a distribution of Tc, possibly caused by each grain having variations in stoichiometry and local ordering.
As HAMR advances, there will be increasing interest in more sophisticated material structures. For example, current perpendicular products use an exchange coupled composite media consisting of many layers of different materials that promote better thermal stability, better switching field distributions, and an altered dependence of switching on applied field angle. Similarly, researchers are already studying multilayer HAMR media that can mitigate problems such as Tc distribution.Reference Liu, Jiao and Victora9 Successful implementation will require integration of multiple materials, most likely incorporating the L10 FePt as the layer nearest the bottom of the stack.
The ultimate recording media would represent each bit by a single lithographically formed magnetic island instead of an assembly of grains. This HDMR combines HAMR with bit patterned mediaReference Albrecht, Arora, Ayanoor-Vitikkate, Beaujour, Bedau, Berman, Bogdanov, Chapuis, Cushen, Dobisz, Doerk, Gao, Grobis, Gurney, Hanson, Hellwig, Hirano, Jubert, Kercher, Lille, Liu, Mate, Obukhov, Patel, Rubin, Ruiz, Schabes, Wan, Weller, Wu and Yang10 and potentially offers densities more than an order of magnitude greater than today’s products, but will require advanced materials and techniques such as the formation of a master disk (from which duplicates are produced) by guided self-assembly of block copolymers. The unusual mechanical requirements of stiffness and extreme smoothness will likely require major advances in nanoimprint technology. The economics of disk drives, essentially low cost per bit, will place severe financial restrictions on useful processes.
In their article in this issue, Hono leads a broad group of authors from the Advanced Storage Technology Consortium in examining HAMR and HDMR media microstructures, media design, magnetic distribution, and thermal design for high densities in the range of 1–10 Tbpsi.Reference Hono, Takahashi, Ju, Thiele, Ajan, Yang, Ruiz and Wan3
Recording heads
The standard PMR head is comprised of three functional components—writer, reader, and thermal fly height controller. HAMR heads require an additional capability to locally heat the media using two additional functional elements—light delivery and NFT. Typically, the material properties of the head components are strongly influenced by their fabrication method. The roughly one billion recording heads fabricated each year must satisfy tight materials requirements using high-yield wafer processing techniques such as sputtering, evaporation, electroplating, atomic layer deposition, chemical vapor deposition, chemical–mechanical polishing, etching, ion milling, and photolithography. Subsequently, the head and materials must be compatible with high-volume micromachining and microassembly techniques to form the head assembly, which is then integrated into the drive.
In simple terms, the magnetic writer is a micrometer-scale electromagnet with a nanometer-scale pole tip and gap. For an illustration, see Figure 1 in the Kautzky and Blaber article in this issue.Reference Kautzky and Blaber11 To produce the highest field and gradient, the write pole funnels magnetic flux down to ∼50 nm × 50 nm using materials with maximum saturation magnetization (Msat) (e.g., FeCo with Msat ∼ 2.4 T).
In HAMR, the writer must be closely juxtaposed to the thermal spot since the write field sets the bit polarity, but the thermal spot must define the bit dimension. To produce such a small thermal spot below the diffraction limit, a NFT is used in conjunction with the light delivery system which consists of a diode laser, a waveguide, and suitable couplers. (See Figure 1 in the Kautzky and Blaber article in this issue.Reference Kautzky and Blaber11) Typically, a diode laser with λ ∼ 800 nm is used. The waveguide must efficiently transmit and focus the laser light upon the NFT. Typical waveguides require a high index core and a low index cladding. The high index core must also have low absorption (e.g., extinction coefficient k < 0.001) and minimal scattering to mitigate losses and unnecessary heating. Common choices include Al2O3 cladding and a Ta2O5 core, but higher index contrast materials are desired.
Focusing the light to a nanoscale spot requires efficient plasmonic designs and materials. Diffraction theory predicts that a simple 150-nm aperture has an optical transmission efficiency of <0.1%. To improve the efficiency, HAMR focuses light from the waveguide onto a nanoscale NFT formed of a plasmonic material. Surface plasmons in the NFT convert the optical energy to a deep subwavelength heat spot in the media.Reference Challener, Peng, Itagi, Karns, Peng, Peng, Yang, Zhu, Gokemeijer, Hsia, Ju, Rottmayer, Seigler and Gage5 Current NFTs have coupling efficiencies in the range of 3–6%, but higher efficiencies are needed. Noble and alkali metals typically have good plasmonic properties. However, most are not compatible with device processing or environmental conditions. For these reasons, Ag and Au have been the most extensively explored. Ag has excellent plasmonic properties, but can readily corrode. Au is perhaps the most common choice with good plasmonic properties and good processing and environmental compatibility, but its thermal-mechanical properties are problematic.Reference Zhou, Xu, Hammack, Stipe, Gao, Scholz and Gage12
NFT reliability is largely driven by operating temperature, which is strongly dependent upon the NFT material and those of the surrounding head and media. Modeling indicates NFT temperatures can reach up to 300°C. At such temperatures, materials such as Au can display significant thermal and mechanical instabilities. As a result, standard sputtered Au appears inadequate. Inevitably, there is a tradeoff between thermal power and reliability. Materials and microstructures with both satisfactory plasmonic and thermal-mechanical properties must be suitably engineered.
In their article, Kautzky and BlaberReference Kautzky and Blaber11 review integrated thin-film optical waveguides, focusing optics, and plasmonic nanostructures employed in the head and NFT. They examine the challenges for plasmonic and other functional materials to balance performance and long-term reliability demands.
To obtain ADs of 1 Tbpsi, a constant clearance of a few nanometers must be maintained between the flying head and disk. To maintain constant spacing, the head uses embedded nanoscale resistive heaters to monitor and dynamically control the head profile and spacing. NFT and waveguide heating further alter the head profile and can result in increased, highly localized protrusions. These profile changes must be mitigated through engineering of materials and local heat dissipation.
HAMR solves the competing requirements of writeability and stability for higher AD—naturally, reader capability must be similarly improved. The recording head reader is the first and highest volume spintronic device ever manufactured, and reader sensitivity has increased 1000× in the past 20 years. Higher AD has been accomplished in part by scaling of the device dimensions and head–disk spacing. In addition, increased sensitivity has required great improvements in the thin films that make up the reader (called the “reader stack”) and the head materials. Going forward, the current tunnel magnetoresistance spin-valve stack is challenged to maintain a suitable SNR and meet low resistance-area (RA) product requirements. To support AD above 2 Tbpsi, and depending upon the extendibility of MgO tunnel barriers, which are the critical feature of current tunnel magnetoresistance stacks, a transition to giant magnetoresistance stacks, Heusler alloys, and new spintronic materials may be required.Reference Nakatani, Li, Sakuraba, Furubayashi and Hono13 Significant material gaps remain to sustain reader SNR while shrinking reader widths below 20 nm, but steady progress is being made.
Nakatani et al.Reference Nakatani, Gao and Hono14 review the evolution of nanoscale magnetic sensors in their article in this issue. They explore recent spintronic materials developments, including high-spin polarization, Heusler alloys, and low-RA spacer layers in giant magnetoresistance and lateral spin-valve devices.
Nanoscale heat transfer
HAMR nanoscale heat transfer is a complex interplay of phenomena that depends upon the optical, thermal, and mechanical properties of the head (especially the NFT and waveguide), HDI, and media. Nanoscale radiative heat transfer occurs from the NFT to the media, with a return through back-heating from media to head. However, these radiative processes are just beginning to be explored. Also, conduction through the transmission, reflection and, possibly, tunneling of interfacial phonons is not well understood. In the media, heat localization is improved using a plasmonic layer such as Au in the media stack to image the NFT electric field. Heat transfer perpendicular to the media with good thermal gradient is provided by a heatsink layer such as Cr, which provides a good thermal gradient, and lateral heat transfer is reduced by an isolated, columnar FePt microstructure (see Figure 3 for illustration).
Heat transfer from the NFT largely bounds its temperature. Simple estimates show the NFT radiation energy density is near 1011 W/m2—approximately 100× the radiation density on the surface of the sun. The NFT temperature must be reduced by very efficient heat dissipation. Given the nanometer scale of the NFT and its encapsulation by a dielectric waveguide, it is vital to efficiently conduct heat across dissimilar materials such as noble metals (e.g., Au, Ag) and high index dielectrics (e.g., Al2O3, Ta2O5). Interlayers 1–3-nm thick have been shown to significantly improve this interfacial conduction. Stability will be strongly dependent upon the materials’ thermal, mechanical, and chemical properties. Successful materials will enable higher NFT power and increased AD.
In their article in this issue, Bain et al.Reference Bain, Malen, Jeong and Ganapathy15 connect many of HAMR’s challenges through the application of thermal engineering at the nanometer scale. They discuss critical materials issues, including the role of the interface thermal conductance in the NFT and the importance of thermal anisotropy in the medium due to its granular microstructure.
HDI
The HDD recording and readback processes are highly sensitive to the head-media spacing, as noted previously. HMS is near 10 nm at 1 Tbpsi, and will scale to <5 nm by 10 Tbpsi, if the historic trend continues. Since HDDs are frequently not sealed systems, sensitive head and media materials are at risk of exposure to environmental air, temperature, and humidity. Corrosion and mechanical interactions are mitigated by nanometer-thick coatings. Typically, multiple nanometer-thin coatings on the head and media are required to provide corrosion protection, control tribology, and—for HAMR—contribute to the near-field heating.
Media and heads typically have a thin carbon overcoat (COC) for corrosion protection and a lubrication layer for tribology. Since HAMR media temperatures exceed 400°C and the NFT can be near 300°C, the COC and lubrication layer must be compatible with this high-temperature exposure. Studies have shown that the diamond-like carbon commonly used for the COC can undergo structural changes from sp 3 to sp 2-bonding and oxidation near 400°C. The carbon sp 2 phase significantly degrades the protective properties of the COC, so more stable coatings must be engineered. Nanometer-thick, high molecular weight polymers are used as lubricating layers on the disk. Common ones such as commercially available Z-dol and Z-tetraol have been shown to desorb and decompose at HAMR temperatures. This can produce depletion zones, head buildup, and contamination. High-temperature compatible lubricating layers are critical to HAMR tribology for drive reliability. In addition, the HDI coatings also contribute to the HAMR optical near-field interaction and heat transfer. This challenging environment makes studies difficult, but ideally, one seeks materials that can improve the optical coupling efficiency while impeding the direct heat transfer. At a minimum, one must consider these factors in the performance and reliability of the HAMR HDI system.Reference Marchon, Guo, Pathem, Rose, Dai, Feliss, Schreck, Reiner, Mosendz, Takano, Do, Burns and Saito16
Literally in the middle of the HAMR system, Kiely et al.Reference Kiely, Jones and Hoehn17 explore this unique operating environment that combines nanoscale spacings, high shear rates, high-temperature gradients, and high optical fluxes in their article in this issue. They discuss nanometer-thick coatings, high-temperature lubrication, and the performance-reliability tradeoffs needed to satisfy the tribological and environmental requirements for operating at extreme temperatures and pressures.
Outlook
The demand for information storage is accelerating. To meet this demand, HDD technology must continue its six decades of AD growth and deliver the next cost-effective, reliable recording system. HAMR has demonstrated AD in excess of 2 Tbpsi and lifetimes longer than 1000 write power-on hours (the number of hours the writer is powered to record data),Reference Granz, Zhu, Rea, Ju, Thiele, Rausch and Gage18 equivalent to two full drive writes per day for five years.
The commercialization of HAMR technology is well under way. The first commercially available HAMR HDD should be released in 2018. To a substantial degree, HAMR technology has been enabled by progress toward improved materials. L10 FePt media development has produced small grain size, low roughness, and narrow switching field distributions. Head NFT with plasmonic materials can heat media near 400°C in <1 ns with gradients of ∼10 K/nm. Coatings on head and media provide protection and tribology within extremely harsh environments.
Beyond the first generation of HAMR, continued materials improvements for increased AD and reliability will be essential, including developing new composite media stacks, more efficient plasmonic NFTs, high-SNR/ highly sensitive readers, directed self-assembly for ∼5-nm patterned media, and more reliable subnanometer coatings. Many challenges remain. It is hoped that this issue of MRS Bulletin provides a good introduction to HAMR technology, especially its challenges and opportunities, and thereby promotes continued advances in HDD materials.
Acronyms
HDD hard-disk drives
HAMR heat-assisted magnetic recording
HDMR heated-dot magnetic recording
HDI head–disk interface
HMS head–media spacing
PMR perpendicular magnetic recording
AD areal density
COC carbon overcoat
DLC diamond-like carbon
NFT near-field transducer
RA resistance-area product
T C Curie temperature

Mark T. Kief is a technologist in the Recording Head Group at Seagate Technology. He is Chair of the Technical Committee for the IDEMA Advanced Storage Technology Consortium. He received his BS degree in engineering physics from the University of Illinois and his PhD degree in physics from The Pennsylvania State University. His research focuses on recording head development with an interest in magnetic materials, spintronics, and nanotechnology. He has more than 65 publications and more than 40 issued patents. He served as general chairman of The Magnetic Recording Conference in 2015 and 2017. Kief can be reached by email at [email protected].

Randall H. Victora is professor and head of Electrical and Computer Engineering at the University of Minnesota. He received BS degrees in physics and mathematics from the Massachusetts Institute of Technology and his PhD degree from the University of California, Berkeley, in 1985. His research focuses on magnetism and magnetic materials, with particular emphasis on applications such as magnetic recording and spintronics. His contributions to recording media include a composite structure used in modern disk drives. He served as general chairman of the 50th Magnetism and Magnetic Materials Conference (2006) and as the president of the IEEE Magnetics Society in 2009 and 2010. He received the 2014 Achievement Award of the IEEE Magnetics Society and is a Fellow of the American Physical Society and the IEEE. Victora may be reached by email at [email protected].