Introduction
A heat pipe is a passive device that can be used to transmit heat over a considerable distance with minimal temperature drop. A heat pipe has a straight or bent cylindrical geometry with an internal wick structure and working fluid. It has three sections, namely: evaporator section, adiabatic section, and condenser section. In the evaporator section, the working fluid is evaporated into vapor as a result of the heat supplied. These vapors move into the condenser section due to a pressure difference and condense there. This condensate returns to the evaporator due to the capillary force of the wick structure present in the evaporator section. Thus, the purpose of the wick structure is to create a capillary force so that working fluid can return to the evaporator. The wick structure is made of various materials, depending on the method used (Khalid et al., Reference Khalid, Babar, Ali, Janjua and Ali2021; Midiani et al., Reference Midiani, Septiadi, Winaya, Sucipta and Putra2019). In the current study, wick materials were developed from zeolite and kaolin through conventional sintering methods. Conventional sintering is performed at high temperatures with or without the application of pressure. This method is also called the “two-step sintering technique” (Sutharsini et al., Reference Sutharsini, Thanihaichelvan and Singh2018).
Zeolites are a group of minerals with a unique crystalline structure due to the presence of pores and channels. They are hydrophilic, capable of adsorption–desorption and ion exchange, thermally and chemically stable, highly porous with interconnected channels, non-toxic, and have a large specific surface area. Because of these properties, zeolites have been used as adsorbents, catalysts, and detergents in various fields such as oil refinement, agriculture, wastewater treatment, and petrochemistry (Koohsaryan & Anbia, Reference Koohsaryan and Anbia2016). Low-cost zeolite is used in many ceramic bodies due to its modest hardness and cation exchange capacity, which improve the sintering and grinding properties. Moreover, the combination of sintered metal fiber and zeolite is a good adsorber for the removal of volatile organic compounds (VOC) because of their porous structure and large surface area.
Ceramic-like kaolin is also an aluminosilicate with a large surface area and with an ability to adsorb water which is many times greater than that of natural zeolite. Zeolite and kaolin, therefore, can be used to form the wick structure in heat pipes, due to their thermal stability and high capillarity deriving from their porous structure (de’ Gennaro et al., Reference de'Gennaro, Cappelletti, Cerri, de'Gennaro, Dondi, Guarini, Langella and Naimo2003; Midiani et al., Reference Midiani, Septiadi, Winaya, Sucipta and Putra2019; Nikolajsen et al., Reference Nikolajsen, Kiwi-Minsker and Renken2006).
A number of different methods have been used to carry out the sintering process. Microwave sintering uses electromagnetic radiation as the source of heat energy, and can produce ceramics with high density, a fine grain size, and enhanced mechanical strength. Many traditional and advanced ceramics and composites have been fabricated using this technology and it has the potential for large savings in time and energy, as well as an overall improvement in quality. For example, Li2TiO3 ceramic pebbles are manufactured using conventional and microwave sintering. The phase transformation from α-Li2TiO3 to β-Li2TiO3 was observed by Yang et al. (Reference Yang, Wang, Chen, Gong, Huang, Ran, Chen, Lu and Xiao2018) who found that the transformation occurred more quickly in microwave sintering compared to conventional sintering.
Another type of sintering process is known as ‘spark plasma sintering’ (Gu et al., Reference Gu, Zhang, Wang, Gan, Shen and Jiang2015), but its main drawback is that a temperature gradient is created in both the radial and axial directions, which causes cracks to appear.
Laser sintering is another promising way to produce ceramics with non-equilibrium phase assemblages and hierarchical heterogeneity, which are difficult to achieve by conventional sintering approaches (Oghbaei & Mirzaee, Reference Oghbaei and Mirzaee2010; Qian & Shen, Reference Qian and Shen2018). Adsorbents based on zeolite-polymer composites have been developed by the laser sintering process, which provides better accessibility to the open pores compared to adsorbents prepared by microwave sintering (Wudy et al., Reference Wudy, Hinze, Ranft, Drummer and Schwieger2017). Similarly, the zeolite-based wick structure in various materials used for heat-pipe applications is prepared using the sintering method.
Controlling the ceramic properties of kaolinite, pure zeolite, and ion-exchange zeolites during the sintering process is challenging. For example, the sintering heating rate can alter the properties of the product. A heating rate of 3°C/min in the sintering of zeolite or Ca-exchanged zeolite synthesized from kaolinite increased their expansion, porosity, and water adsorption capabilities and decreased their density, whereas a heating rate of 1°C/min yielded products in which no shrinkage occurred, water adsorption was small, and the density was high (Chandrasekhar & Pramada, Reference Chandrasekhar and Pramada2001; Midiani et al., Reference Midiani, Septiadi, Winaya, Sucipta and Putra2019). The sintering temperature of zeolite is usually between 700 and 1000°C, but greater temperatures result in greater density, more shrinkage, lower porosity, and less water adsorption. Sintering temperatures in the range of ~700–900°C achieve the best water adsorption, porosity, and density. Holding time is another factor that affects the ceramic properties, ceramic undergoes process of densification during the holding time which cause the reduction in porosity and increment in strength.Therefore,holding time during sintering is set according to desire properties of final product, composition of materials and sintering condition being used. Therefore, the sintering temperature, heating rate, and holding time are three critical parameters that determine the properties of sintered kaolinite, zeolite, and various types of zeolites (Respati et al., Reference Respati, Soenoko, Irawan and Suprapto2016b, Reference Respati, Soenoko, Irawan, Suprapto, Saputra and Purwanto2017). These parameters also influence the mechanical properties, such as bending strength, Young’s modulus, and densification of sintered samples (Yang et al., Reference Yang, Wang, Chen, Gong, Huang, Ran, Chen, Lu and Xiao2018).
Rice husks are another material that can increase the porosity and macro pores of sintered zeolite, but compressive strength and density are decreased significantly. The lack of strength in ceramics such as zeolite combined with rice husks can be improved by adding austenitic stainless steel 316 (SS316), a type that contains Ni, Cr, and Mo. It has good strength and toughness and excellent corrosion and heat resistance. This combination yields a product with high interfacial shear strength tested at 850°C.
The sintering temperature is also important for the production of ceramics used in glassy membrane technology. Increased sintering temperature means a greater bending strength, a less hydrophilic nature, and a larger water-contact angle (Mopoung et al., Reference Mopoung, Namahoot, Sriprang, Naudom, Sittijanda, Sriaphai, Pengpajon, Kammee, Rakharn and Baosaree2018; Respati et al., Reference Respati, Soenoko, Irawan and Suprapto2018).
Ceramics from zeolite lose their hydrophilicity when treated at high temperature but their stability depends on the amount and type of extra-framework cations, Al/Si ratio, presence/absence of water, and the heating rate. (Bish & Carey, Reference Bish and Carey2001; Ondruška et al., Reference Ondruška, Húlan, Sunitrová, Csáki, Łagód, Struhárová and Trník2021) Many zeolite structures maintain their original structure when dehydrated and some undergo a complex structural transformation on heating and dehydration (Bish & Carey, Reference Bish and Carey2001; Ondruška et al., Reference Ondruška, Húlan, Sunitrová, Csáki, Łagód, Struhárová and Trník2021). Cruciani (Reference Cruciani2006) found that a Si/Al ratio > 3.80 introduced thermal stability in the zeolites.
Several important processes occur in zeolite and kaolin during heating. Above 100°C, water molecules escape from pores and surfaces of the zeolite. During heating to 900°C, the infrared spectra show the formation of structural defects. Above 1000°C, the zeolite structure is destroyed (Bish & Carey, Reference Bish and Carey2001; Ondruška et al., Reference Ondruška, Húlan, Sunitrová, Csáki, Łagód, Struhárová and Trník2021). Kaolin consists mainly of the mineral kaolinite, a phyllosilicate with a theoretical formula of Si2Al2O5(OH)4. During heating to 1100°C, three important reactions take place in kaolinite. The first process is dehydration that occurs between 35 and 250°C, and involves the escape of physically bound water from the crystal surfaces and pores. The second process is dehydroxylation, which occurs at temperatures between 450 and 700°C, and in which chemically bound water escapes from the surface and kaolinite is transformed to metakaolinite. Metakaolinite crystallizes into mullite and γ-Al2O3 at ~ 950°C. At temperatures above 700°C, solid-state sintering occurs whereby ceramic particles compact entirely into a solid-state body (Ondruška et al., Reference Ondruška, Húlan, Sunitrová, Csáki, Łagód, Struhárová and Trník2021; Sunitrová & Trník, Reference Sunitrová and Trník2018).
Sintered zeolite has much less porosity and water-adsorption capability than unsintered zeolite. To enhance these properties, kaolin is added because it has greater bulk density, porosity, and thermal diffusivity and conductivity at high temperatures than does zeolite (Ondruška et al., Reference Ondruška, Húlan, Sunitrová, Csáki, Łagód, Struhárová and Trník2021). Zeolites synthesized from kaolin have better properties than zeolites synthesized from pure sodium silicate and sodium aluminate (Chandrasekhar & Pramada, Reference Chandrasekhar and Pramada2004). Thermogravimetric analysis and differential scanning calorimetry analysis can be used to perform the thermal analysis of such material (Akalin et al., Reference Akalin, Oztuna Taner and Taner2021).
The purpose of the current study was to determine the contribution of clay minerals to heat transfer in solids and to check the behavior of wick structures obtained from zeolite and kaolin after heating at various temperatures and pressures. The hypothesis was that the wick structure formed from zeolite and from a mixture of zeolite and kaolin through conventional sintering was altered depending on the applied pressure. Characteristics such as porosity, water adsorption, permeability, and shrinkage of both types of wick structures were expected to play an important role. Depending on these properties, the wick inserted inside a heat pipe is expected to generate less or more capillary force to circulate the working fluid.
Materials and Methods
This research focused on the fabrication and testing of wick structures resulting from submitting zeolite and kaolin to two conventional sintering methods known as’loosely packed sintering’ and ‘pressurized sintering.’ In the first method, loose material was subjected to high temperature in order to compact it into solid material, whereas pressurized sintering required high temperature accompanied by high pressure to make a solid.
Loosely Packed Sintering
Natural zeolite with a mesh size of 135–140 µm and kaolin with a mesh size of 35–40 µm from Nitto-Funka kogyo K.K., Tokyo, Japan, were used as the powder materials and a two-stage conventional sintering method was applied. A sintering temperature of 950°C was chosen for the zeolite and the zeolite-kaolin mixture, taking into consideration the melting points for both minerals (Sutharsini et al., Reference Sutharsini, Thanihaichelvan and Singh2018). First, zeolite and mixtures of zeolite:kaolin with various compositional ratios (100% zeolite, 90% zeolite 10% kaolin, and 80% zeolite 20%Kaolin) were prepared and heated at 120°C for 2 h to remove moisture. Then the materials were placed in a mold (Fig. 1) to develop a wick structure. Complete molds included an inner rod to make holes in the wick structure, a base plate, and a stainless-steel shell. Due to its low thermal conductivity and fewer problems with adhesion, a stainless-steel mold housing was preferred. The assembly of the molds is shown in Fig. 1b. Then zeolite and mixtures of zeolite and kaolin were placed in the mold and the powders loosely packed by shaking well. The sintering process was carried out in a programmable, high-temperature furnace (Ultra Fine Technologies, Inc., Model UF-D3FS-200*200*200, Taoyuan, Taiwan).
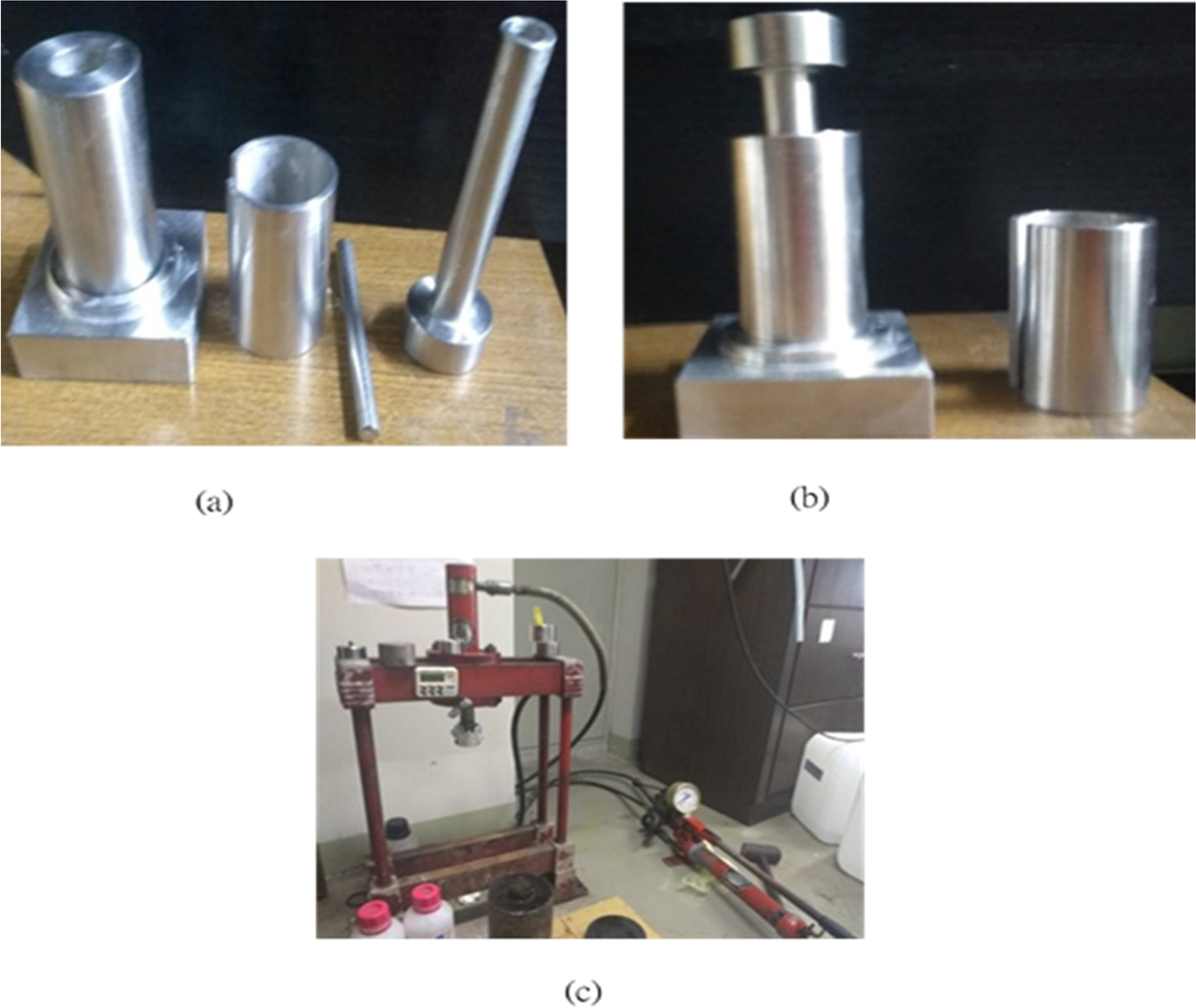
Fig. 1 a Parts of the mold used for holding the powders, b assembly, and c device for applying pressure to the powder
The temperature program called for heating the sample to 950°C with a holding time of 5 h, then the sample was allowed to cool to room temperature either naturally or under controlled conditions. The controlled cooling involved decreasing the oven temperature to 550°C in increments of 100°C and then holding at each increment for either 1 h or 30 min. After holding at 550°C, the oven was turned off and the sample cooled naturally to room temperature (Demirkiran et al., Reference Demirkiran, Artir and Avci2008; Padmavathi et al., Reference Padmavathi, Upadhyaya and Agrawal2011).
Some minor cracks and uneven shrinkage were found on the outer surfaces of the sintered sample when using the natural cooling program; however, controlled cooling minimized the cracks on the outer surface. The holding time at maximum temperature and at each temperature increment was also a key variable for the sintering process. By reducing the holding time from 1 h to 30 min at each temperature increment, fewer cracks were observed on the surface of the wick structure (Fig. 2).
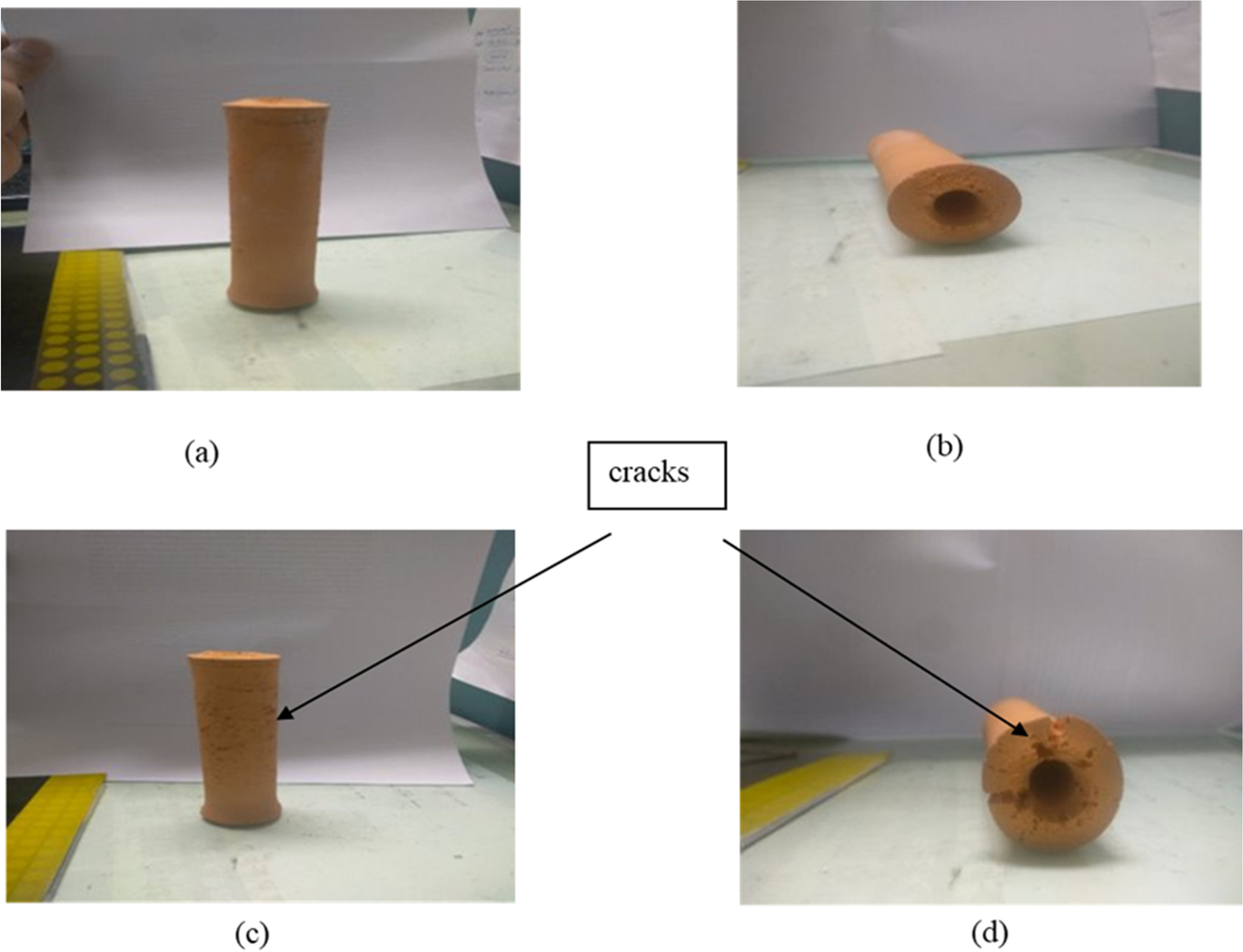
Fig. 2 a Front view of a wick structure prepared using a holding time of 1 h at each temperature interval, b bottom view. c front view of a Wick structure prepared using a holding time of 30 min at each temperature interval, and d bottom view
Pressurized Sintering
In pressurized sintering, external pressure is applied to the powder material during or before heating. Numerous studies have been conducted on sintering behavior under pressurized conditions, whereby the sintering temperature decreases with a corresponding increase in pressure under either oxidizing or reducing environments (Jing et al., Reference Jing, Wang, Cheng, Luo and Cen2013). A very limited amount of research, however, has been conducted into pressurized conventional sintering processes in which pressure is applied before heating begins. Experiments were conducted here using pressurized sintering to avoid major drawbacks such as uneven shrinkage in loosely packed sintering. The material was first pressed into a mold at various pressures ranging from 20 to 40 MPa for 1 min, measured using an Enerpac-GF-120P (New Jersey, USA) hydraulic pressure gauge, and then the sample was transferred from the mold to a programmable oven and heated at 750, 800, 850, or 900°C with a holding time of 5 h. Only natural cooling was used in the pressurized sintering method because the sample was already uniform. Moreover, holding time also played a vital role in both types of sintering (Sabahi Namini et al., Reference Sabahi Namini, Ahmadi, Babapoor, Shokouhimehr and Shahedi Asl2019; Şan et al., Reference Şan, Abalι and Hoşten2003; Sutharsini et al., Reference Sutharsini, Thanihaichelvan and Singh2018; Watanabe et al., Reference Watanabe, Ikoma, Suetsugu, Yamada, Tamura, Komatsu, Tanaka and Moriyoshi2006). The shape and color of the wick structure before and after pressurizing are presented in Fig. 3a and b, respectively.
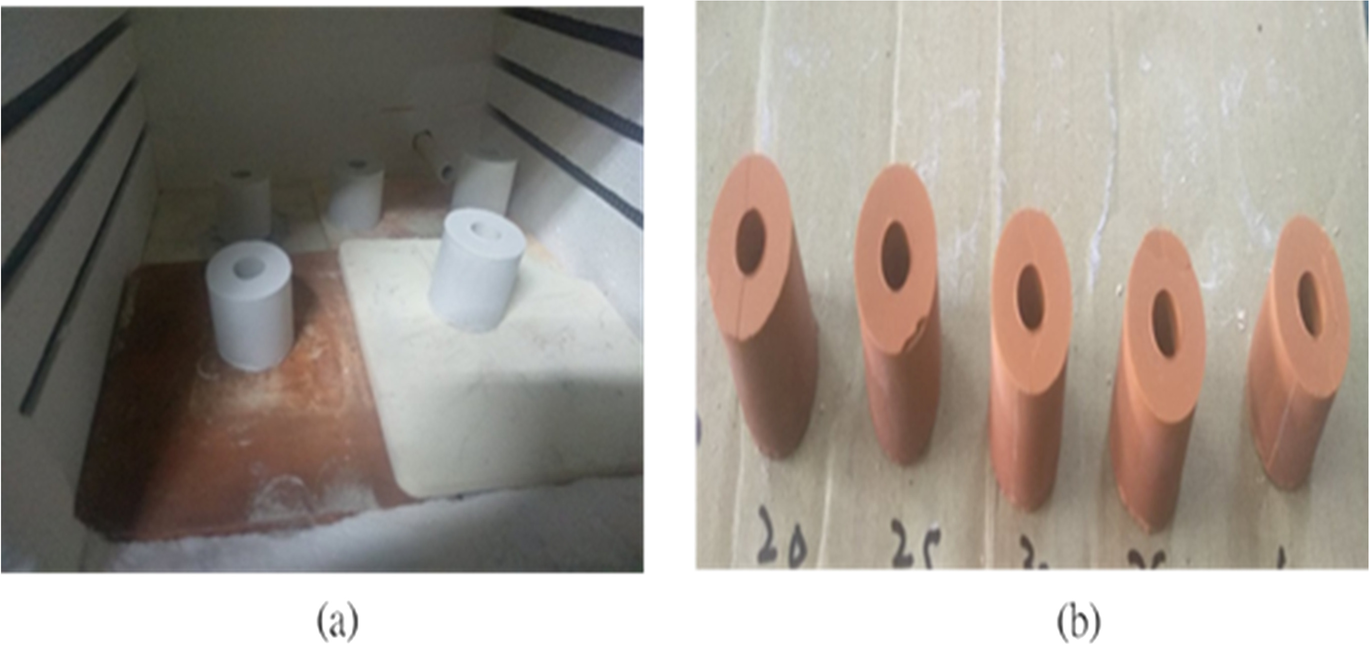
Fig. 3 a The wick after pressurizing and before sintering, and b the same wick after sintering at 900oC
The pore roughness and morphology of the sintered sample were investigated using scanning electron microscopy (SEM) images (Figs. 4a, 5a, and 6a). Further study of the structure of sintered samples was performed using X-ray diffraction (XRD) over the range 10–55°2θ (Figs. 4b, 5b, and 6b).
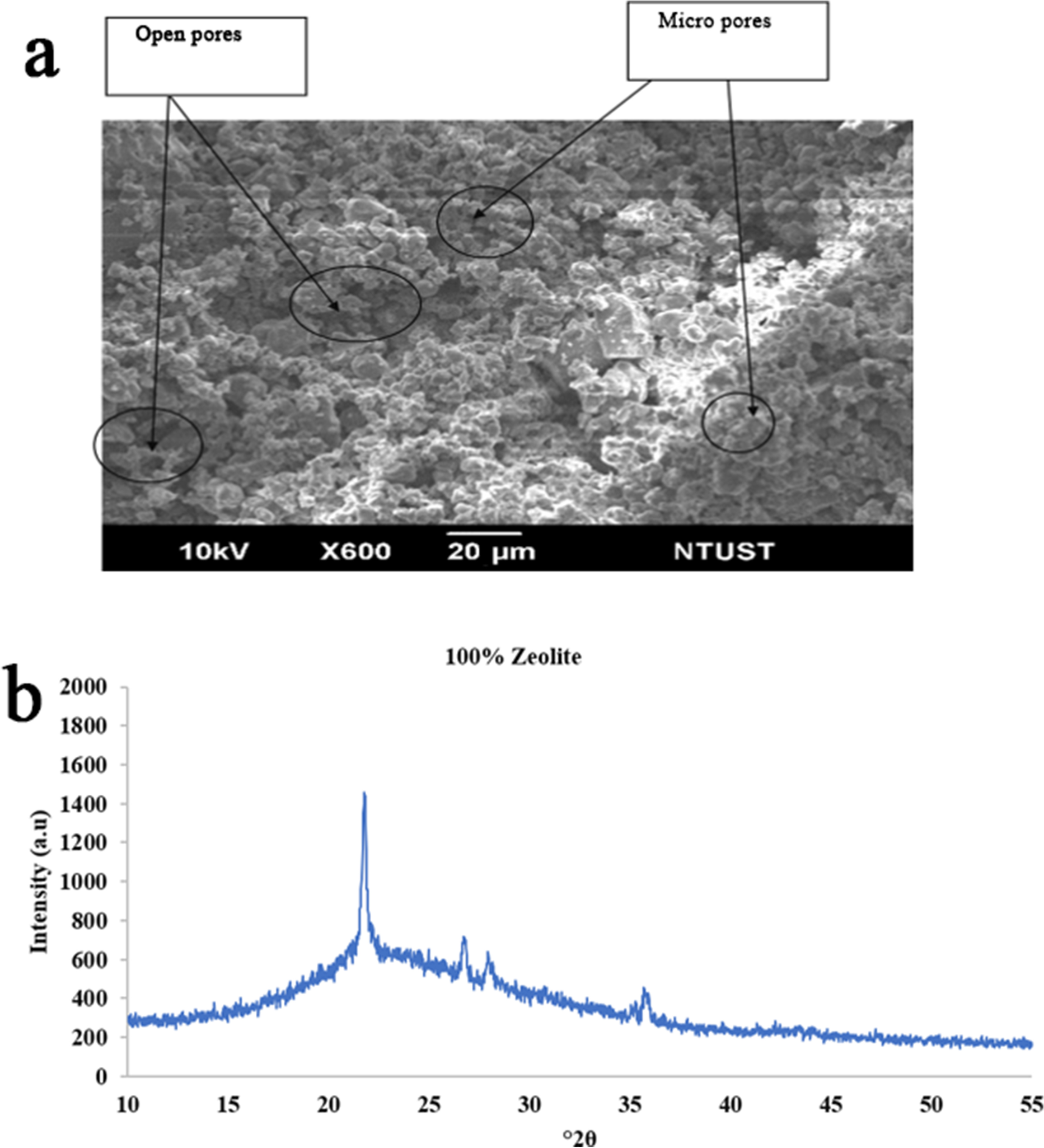
Fig. 4 a Morphology (SEM) and b XRD pattern of pure zeolite sintered at 950°C with no pressure applied
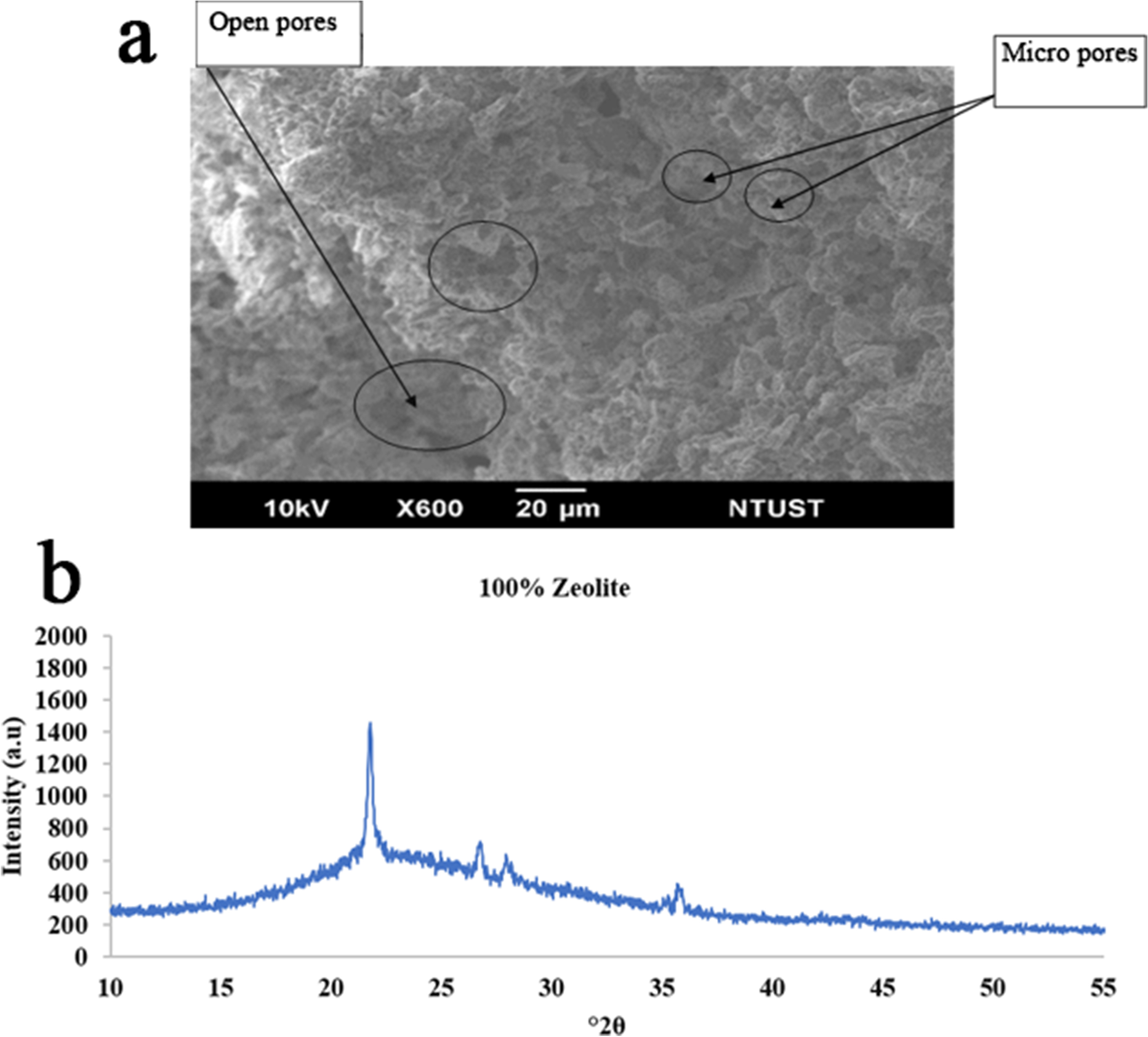
Fig. 5 a Morphology (SEM) and b XRD pattern of a 90/10 zeolite/kaolin mixture sintered at 950°C with no pressure applied
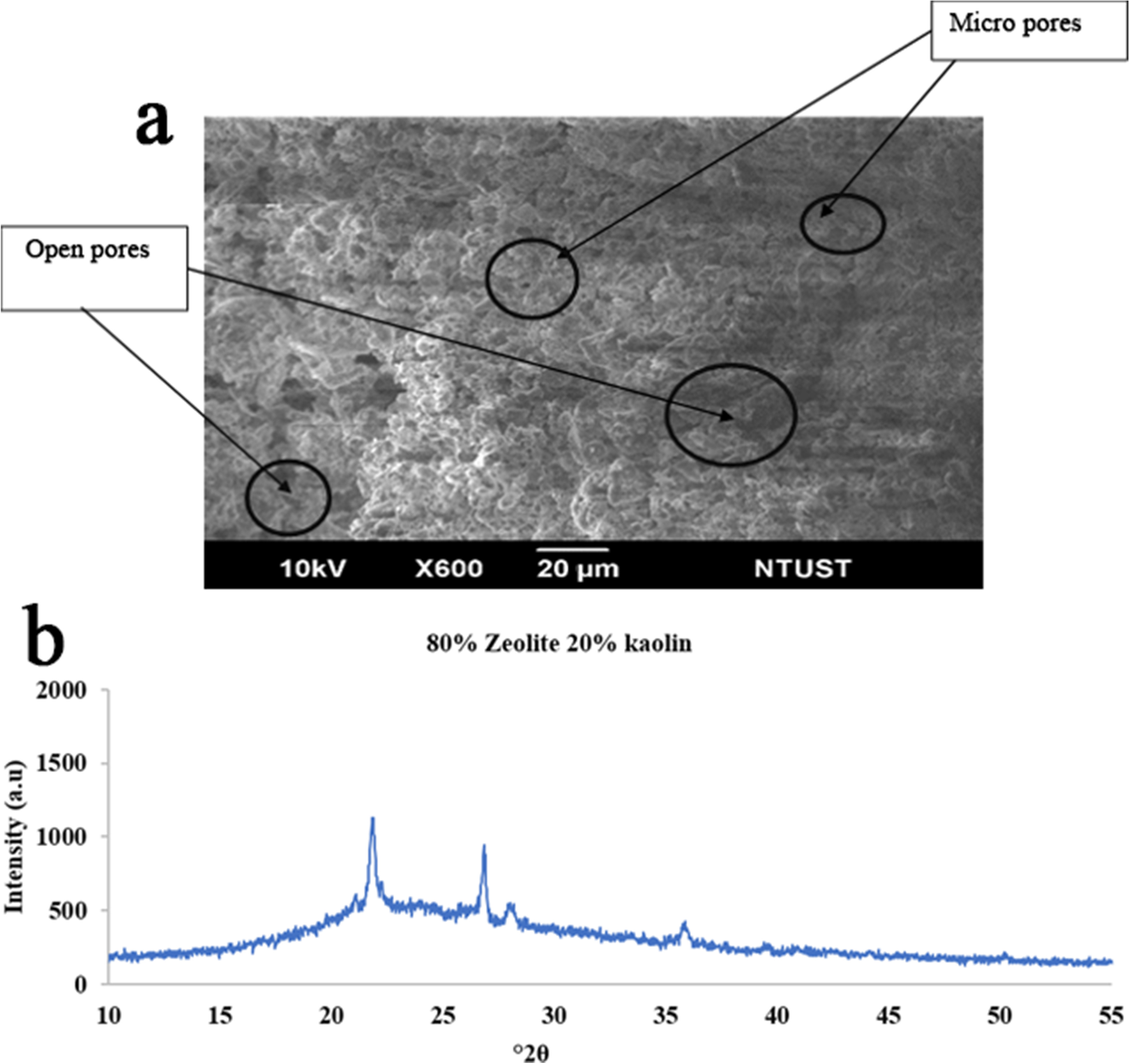
Fig. 6 a Morphology (SEM) and b XRD pattern of an 80/20 zeolite/kaolin mixture sintered at 950°C with no pressure applied
Results and Discussion
Characterization of the sintered products included porosity, water adsorption, shrinkage (linear and radial), and permeability. Sintered samples with the best properties were characterized using SEM and XRD.
Porosity and Water Adsorption
Ceramic materials are more porous than many other materials, such as plastics and metals, due to their open pores. The porosity of sintered zeolite depends heavily on sintering temperature but is less dependent on pressure, which is measured using the Archimedes method where the mass and volume of sample is measured before and after it is immersed in fluid (Mostafa et al., Reference Mostafa, Shaltout, Abdel-Aal and Elmaghraby2010; Respati et al., Reference Respati, Soenoko, Irawan and Suprapto2016a). In the present study, the porosity of zeolite, which was packed loosely before sintering, was ~ 45%. This can be increased through the addition of kaolin (Ondruška et al., Reference Ondruška, Húlan, Sunitrová, Csáki, Łagód, Struhárová and Trník2021). The porosity and water adsorption of samples prepared by sintering of loosely packed material increased with the addition of kaolin (Table 1). Sintered samples of zeolite with 30% kaolin have a maximum porosity of 65% and 63% water adsorption. On the other hand, shrinkage of the product decreased with the addition of kaolin. Thus, sintered zeolite with 30% kaolin has minimum radial shrinkage of 10.5% and linear shrinkage of 9.5%.
Table 1 Porosity, water adsorption, and shrinkage variations in zeolite and zeolite-kaolin mixture wick structures (%) prepared through conventional sintering of loosely packed material
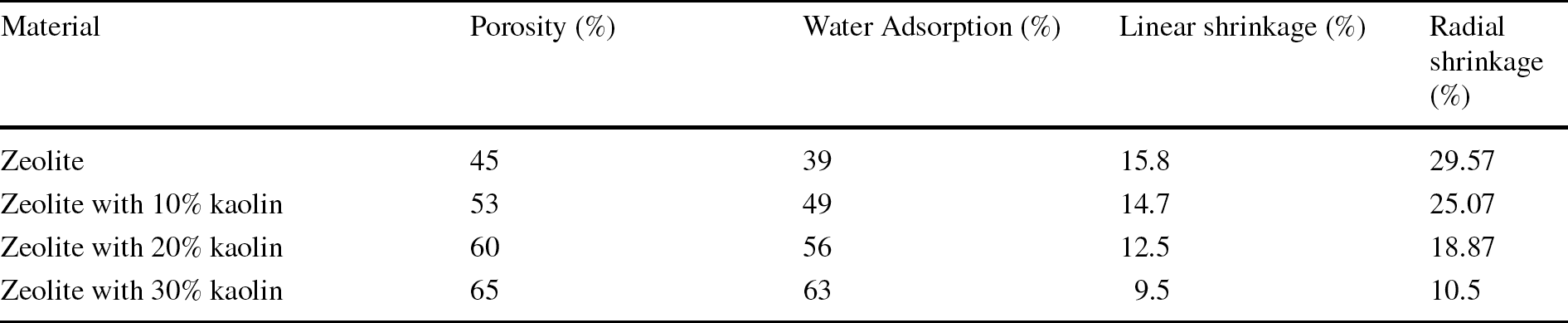
Furthermore, variation in the porosity of sintered zeolite-kaolin with the application of pressure is also decreased with increasing temperature. The porosity of the sintered samples decreased with increased pressure and sintering temperature (Fig. 7). The maximum porosity and water adsorption in the case of pressurized sintering was obtained for a temperature of 750°C and with 30% added kaolin. In this case, however, the wick structure was not very strong. Although kaolinite loses the hydroxyl group at a temperature of ~550°C, the super-hydrated phase of kaolinite broke down as pressure and temperature approached ~19 GPa and 800°C (Hwang et al., Reference Hwang, Seoung, Lee, Liu, Liermann, Cynn, Vogt, Kao and Mao2017). The porosity of four sintered samples (100% zeolite, 90/10 zeolite-kaolin, 80/20 zeolite-kaolin, and 70/30 zeolite-kaolin) was measured after preparation using the pressurized sintering method at various temperatures and pressures (Fig. 7).
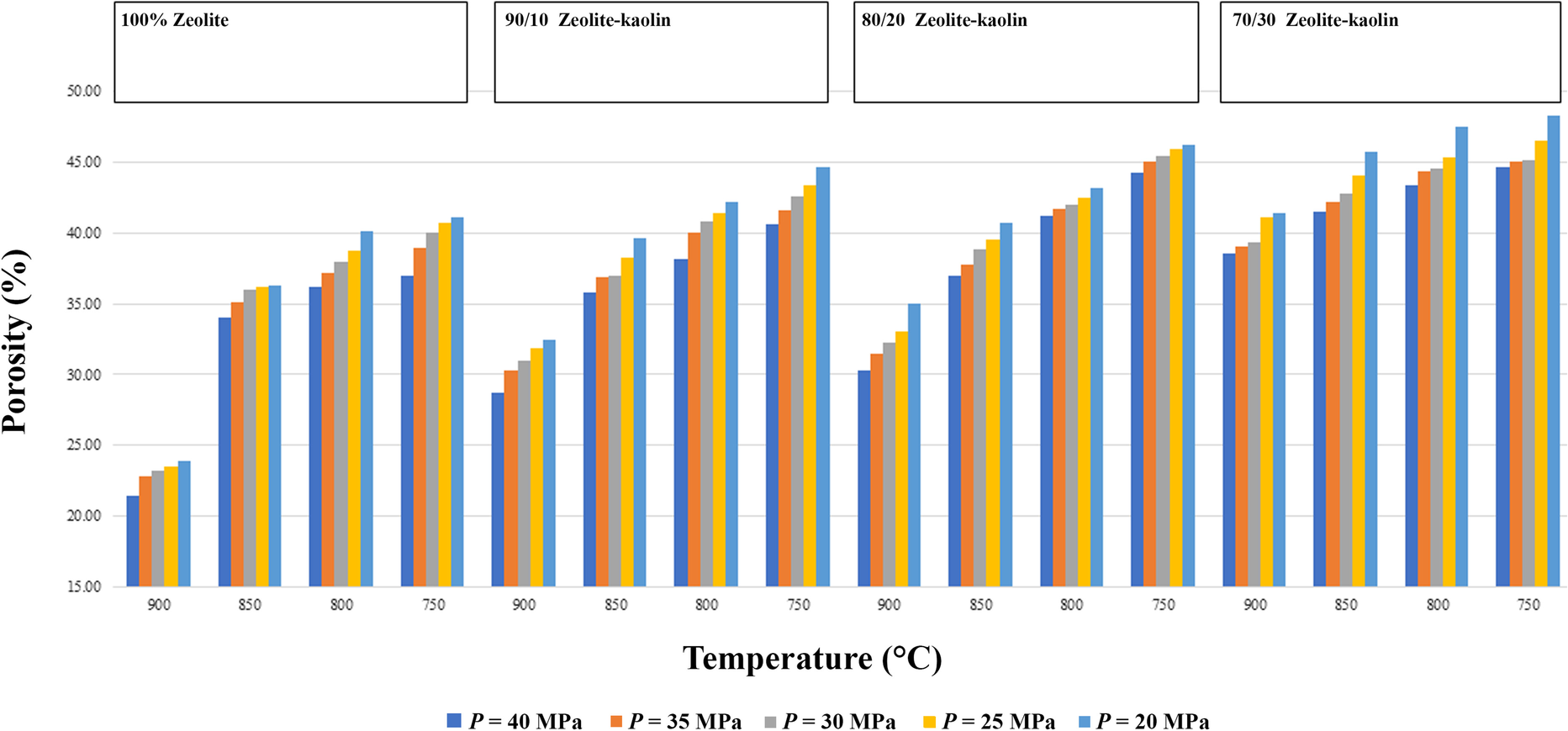
Fig. 7 Porosity variation of zeolites and hybrid zeolite-kaolins in pressure-assisted sintering
The percentage of porosity is determined using a standard method known as the immersion technique (Anovitz, 2015 #240). Sintered samples were weighed in air and then immersed in water under a vacuum. The densities of dry and wet samples were measured and porosity calculated from Eq. 1 (Mopoung et al., Reference Mopoung, Sriprang and Namahoot2014).
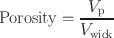
where V p and V wick are the volume of the pore and wick structure, respectively.
Like porosity, water adsorption is an important property of ceramics. Water adsorption indicates the proportion of open pores in the samples and is a function of the firing temperature (Mostafa et al., Reference Mostafa, Shaltout, Abdel-Aal and Elmaghraby2010). The porosity of polymer-based materials decreased due to water adsorption and enlargement of fibers. However, for ceramic-based materials, water adsorption varies linearly with porosity. The thermal behavior of natural zeolites is temperature- and pressure-dependent, especially zeolite-water equilibria. This zeolite-water pair adsorb less volatile material in the presence of water molecules. Therefore, zeolite is treated at high temperatures before application (Bish & Carey, Reference Bish and Carey2001). The water-adsorption capabilities of natural zeolite and of sintered zeolite are quite different as the zeolite loses its structure due to evaporation of water at high temperatures. Based on the current application in a heat pipe, the sintered wick structure is in common use. The more hydrophilic ceramic material, kaolin, is added, therefore, to improve its water-adsorption capacity. Kaolin has more adsorption capacity than zeolite in some cases due to a smaller particle size, interconnected pores and channelsand a different morphology. The present study confirmed that porosity and water adsorption of the wick structure depended linearly on each other (Figs. 7 and 8). The trend of water adsorption variation for all four sintered samples (100% zeolite, 90/10 zeolite-kaolin, 80/20 zeolite-kaolin, and 70/30 zeolite-kaolin) was the same as for porosity (Figs. 7 and 8). Water adsorption is usually calculated with the following formula (Mopoung et al., Reference Mopoung, Namahoot, Sriprang, Naudom, Sittijanda, Sriaphai, Pengpajon, Kammee, Rakharn and Baosaree2018):

where W and D are the weights of the wet and dry wick, respectively:
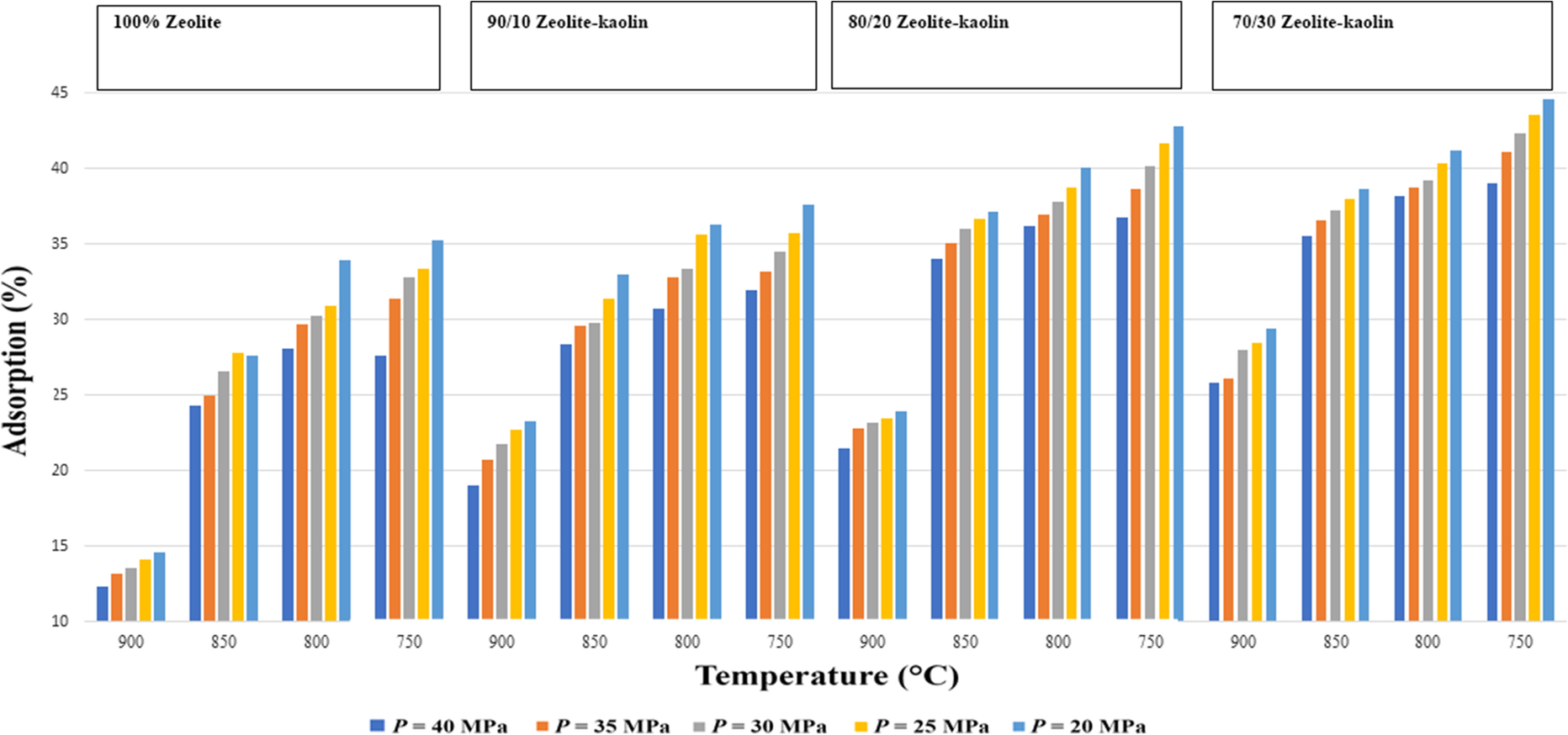
Fig. 8 Water-adsorption variation of zeolites and hybrid zeolite-kaolins in pressure-assisted sintering
Shrinkage
Generally, shrinkage depicts a reverse trend to that of porosity. Shrinkage increases with increasing sintering temperature. Both linear and radial shrinkage are large in samples sintered at 900°C compared to 700°C. On the other hand, samples containing more kaolin showed minimum shrinkage in the radial and linear directions (Mostafa et al., Reference Mostafa, Shaltout, Abdel-Aal and Elmaghraby2010). Uneven shrinkage in the linear and radial directions is the main problem in loosely packed sintering. However, these shrinkage problems can be overcome with the application of pressure. Moreover, radial shrinkage depends only on temperature; it remains unaffected by pressure, however. Results from the present study revealed that shrinkage (linear and radial) was at a minimum at lower pressures and sintering temperatures (Figs. 9 and 10). Sintered sample 70/30 zeolite-kaolin had minimum shrinkage at a pressure of 20 bar and temperature of 750°C (Figs. 6, 7). On the other hand, shrinkage was at a maximum in the case of 100% zeolite sintered samples at 40 bar of pressure and 900°C sintered temperature. Linear and radial shrinkages were calculated using Eqs. 3 and 4 (Mopoung et al., Reference Mopoung, Sriprang and Namahoot2014, Reference Mopoung, Namahoot, Sriprang, Naudom, Sittijanda, Sriaphai, Pengpajon, Kammee, Rakharn and Baosaree2018).

where
are the lengths of wick before and after sintering, respectively;

where
are the diameters of wick structure before and after sintering, respectively.
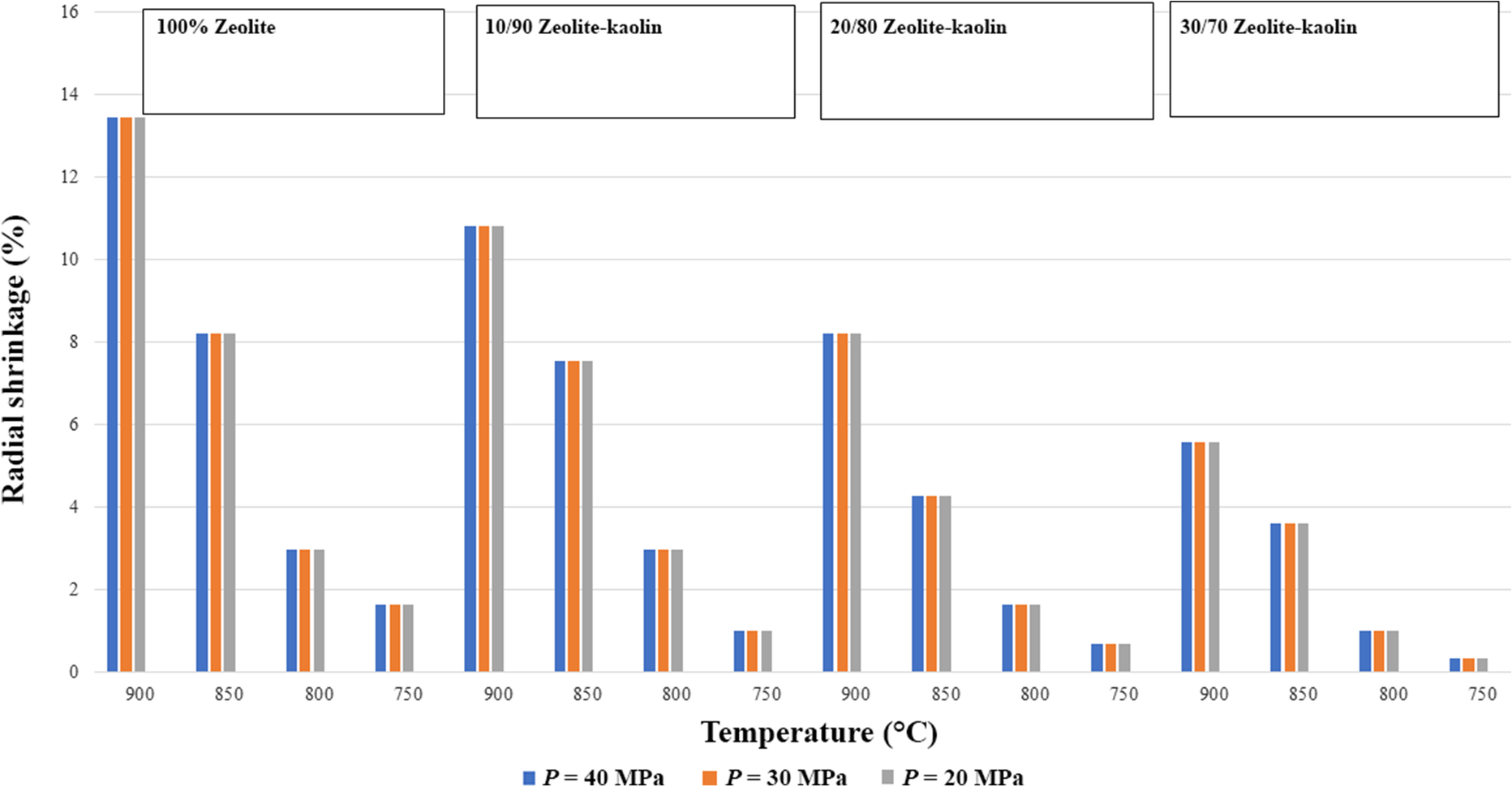
Fig. 9 Radial-shrinkage variation of zeolites and hybrid zeolite-kaolins in pressure-assisted sintering

Fig. 10 Linear-shrinkage variation of zeolites and hybrid zeolite-kaolins in pressure-assisted sintering
Permeability
Darcy’s Law is one of the fundamental laws used to determine the permeability of wick structure. However, the inertial effect is not considered in Darcy’s Law, so permeability varies with the pressure of the working fluid (Innocentini & Pandolfelli, Reference Innocentini and Pandolfelli2001). The permeability of sintered zeolite is much less than that of self-setting particles, which destabilizes zeolite, and of self-setting particles of zeolites without additive. A large compressive strength and large pore-size distribution were observed in the case of sintered zeolite (Ha et al., Reference Ha, Jung, Ahmad and Song2014). The permeabilities of zeolite wick structures of various compositions were determined with various mass flow rates in the longitudinal direction because the results of permeability determinations were better in the case of longitudinal flow than for transverse flow (Zarandi et al., Reference Zarandi, Pillai and Barari2018). The pure zeolite sintered at 900°C under pressure had maximum permeability (Fig. 11). In contrast, permeability was reduced with the addition of kaolin and heating at lower temperature. In addition, zeolite and zeolite-kaolin sintered without the application of pressure showed less permeability than samples which were sintered and pressurized. The Kozeny–Carman equation (Scheidegger, Reference Scheidegger2020) shows a linear relation between pressure drop, pore size, and porosity. As a result, the general trend is that increasing the porosity increases the permeability. Permeability and porosity depend on several factors, including pressure drop, pore size, grain size, packing, and compaction. In the present study, the zeolite and kaolin had grain sizes of 135 and 35 μm, respectively; The relationship among grain size, permeablity, and porosity depend on various factors such as shape, compactness, and sorting of the grains. The 100% zeolite sintered sample had maximum permeability at a pressure of 40 bar and at a sintering temperature of 900°C (Fig. 12). The permeability of the samples was calculated using the Darcy formula (Eq. 5). The apparatus used to determine the permeability is shown in Fig. 13.
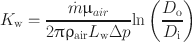
where
is the pressure drop across the wick structure; K w is the permeability of the wick structure; L w is the length of the wick structure;
is the mass flow rate across the longitudinal direction of wick structure; and D i and D o are the inner and outer diameters of the wick structure, respectively.

Fig. 11 Permeability variation of pure zeolite sintered at various temperatures and pressures

Fig. 12 Permeability variation of 90/10, 80/20, and 70/30 zeolite-kaolin sintered at various temperatures and pressures

Fig. 13 Apparatus used to determine the permeability of a wick structure
Wick Structures and SEM Analysis
Heat pipes have many applications in terms of improving the efficiency of various heat-transfer systems and fuel cells. The efficiency of a fuel cell, in particular, can be improved by using a heat pipe-based cooling system and by regulating the pressure, flow rate, and voltage (Taner, Reference Taner2018, Reference Taner2021). The thermal performance of heat pipes and thermosiphon heat pipes depend heavily on the type of wick and working fluid (Khalid et al., Reference Khalid, Babar, Ali, Janjua and Ali2020; Nugraha & Putra, Reference Nugraha and Putra2019). Optimum parameters for wick structures depend on types of liquid used, operating temperatures, porosity, grain/bead size and height, and rate of evaporation (Beyhaghi et al., Reference Beyhaghi, Geoffroy, Prat and Pillai2014). The wick structures used in heat pipes generate capillary forces to circulate the working fluid. Both homogeneous and composite wick structures are used in heat pipes; composite wicks show better performance than homogeneous wicks (Berti et al., Reference Berti, Santos, Bazzo, Janssen, Hotza and Rambo2011; Nemec, Reference Nemec2018). A composite structure consists of two or more wick structures in the form of layers with each layer performing a specific function. Furthermore, a composite wick heat pipe has less thermal resistance than a homogeneous wick heat pipe (Kumaresan et al., Reference Kumaresan, Vijayakumar, Ravikumar, Kamatchi and Selvakumar2019). Based on the results above, wick structures with high porosity and high permeability are best suited for thermosiphon heat pipe applications. Therefore, loosely packed material and sintering offer the best results for the present application. With the addition of kaolin (especially >20%), wick structures become weak and cannot be used for long time periods.
The SEM image in Fig. 4a shows that pure zeolite has more macropores than micro pores, whereas Figs. 5a and 6a indicate that zeolite-kaolin mixtures have more uniform micropores than macropores. This is because the particles of kaolin combined well with zeolite particles. Although zeolite has more macropores, thus indicating greater water adsorption and porosity, because of the more hydrophilic nature of kaolin, zeolite-kaolin mixtures suggest greater porosity and water adsorption than pure zeolite.
In general, the mineral phase and crystalline structure of both zeolite and kaolin can be altered under certain conditions including increasing temperature. Thermogravimetric analysis and differential thermal analysis showed that zeolite is stable at temperatures up to ~1300ºC (Musyoka et al., Reference Musyoka, Petrik, Hums, Kuhnt and Schwieger2013). X-ray diffraction did likewise (Sanhoob et al., Reference Sanhoob, Muraza, Yoshioka, Qamaruddin and Yokoi2018).
Conclusions
In the present study, zeolite and hybrid zeolite-kaolin wick structures were sintered both with and without (loosely packed) pressurization, and then underwent natural and controlled cooling. Their properties were analyzed in terms of porosity, shrinkage, water adsorption, and permeability. Natural cooling of sintered, loosely packed material reduced the time of the sintering process, but some minor open cracks were observed on the outer and bottom surface of the wick structure. In contrast, controlled cooling results yielded no cracks on the outer surfaces of the wick. The following conclusions were reached:
• The cooling process has no effect in pressurized conventional sintering.
• Despite uneven linear and radial shrinkages, loosely packed sintering yields greater porosity and better water-adsorption and permeability properties.
• Porosity can be increased with the addition of kaolin and the shrinkage problem can be minimized. However, adding >20% of kaolin to the wick structure weakened it. Therefore, zeolite with 10–20% kaolin gave promising results.
• The permeability of the wick structure with the addition of kaolin is reduced due to the small grain size of kaolin and compactness. No exact relation was observed between porosity and permeability for these porous ceramic materials.
Acknowledgements
The authors thank the Ministry of Science and Technology, Taiwan.
Author Contribution
Muhammad Aon Ali: Methodology, Design and conduct of the experiment, preparation of the original draft; Tzong-Shyng Leu: Conceptualization, supervision; Chih -Yuan Weng: Investigation and methodology; Hafiz Muhammad Ali: Writing, reviewing and editing.
Funding
The funding source is Ministry of Science and Technology, Taiwan, Grant MOST 107–2218-E-008–008.
Data Availability
The dataset generated during current study are available from the first author on reasonable request.
Declarations
Ethics Approval and Consent to Participate
Not applicable.
Consent for Publication
Not applicable.
Conflict of Interest
The authors declare that they have no conflict of interest.
Competing Interest
Authors declare that they have no competing interests.