1 Introduction
There is an intuitive connection between ‘design’ and ‘innovation’. However, this seemingly straightforward link is not at all easy to explain, given the deep and manifold implications underlying both terms. In fact, we have found that very few authors have made rigorous attempts to explore this relationship and to provide a unifying perspective on Design and Innovation – an outcome that we think could be very valuable, since it would stimulate research and improve practice in both of the two fields.
Quite often, papers positioned at the frontier between Design and Innovation are influenced by the specialist background of their authors, who generally have been academically trained in one of the two fields, but whose relatively limited knowledge about the other domain prevents them from providing more than elementary – if sometimes not even flawed – contributions to the discussion. Among the few exceptions, Luo (Reference Luo2015) provided a sound and groundbreaking discussion of the relationship between Design and Innovation by proposing what he termed a ‘united innovation process’ (hereafter UIP).
The UIP is a two-dimensional integrated model that considers on one axis Science, Design and Entrepreneurship as subprocesses of the overall innovation process. The innovation process occurs – and can therefore be studied and supported – at different levels, which are represented on a second dimension, with the four layers made of individuals, organizations, local ecosystems and global networks. The main message that emerges from Luo’s model is that design can be viewed under two perspectives. If one looks ‘inside out’, design is a cognitive and social process characterized by a remarkable technical and knowledge content, within which such knowledge is used to generate technically feasible and economically sustainable solutions addressing societal problems. Conversely, by looking ‘outside in’, design is the process that enables and powers the socioeconomic phenomenon called innovation, which we can quite narrowly define as ‘the economic exploitation of an invention’ (Roberts Reference Roberts1987) or – more broadly – the ‘act or process of introducing new ideas, devices or methods’ (Merriam Webster dictionary).
In our view, Luo’s UIP suffers from a few shortcomings that are probably due to the author’s objective of providing a simple representation of a highly complex phenomenon. Specifically, one can identify three main limitations in the UIP. The first one is the reliance on the traditional – albeit obsolete – ‘linear’ model of innovation, in which innovation flows unidirectionally from research to business activities (Kline Reference Kline1985; Kline & Rosemberg Reference Kline, Rosemberg, Landau and Rosenberg1986; Edgerton Reference Edgerton, Grandinand and Wormbs2004). The second is the declared focus on radical and groundbreaking innovation activities, which is certainly a too narrow view if one considers the many and more frequent design and innovation activities that do not fit in this category. Finally, Luo somewhat forcedly uses the concept of ‘entrepreneurship’ to encapsulate an even more various set of business activities and processes that may occur in firms and organizations of many different types.
Despite these limitations, Luo’s contribution can be considered as a key starting point for a deeper discussion, which we think can be highly useful to an Engineering Design community that is starting to debate about this theme in different occasions (see for instance the ‘organizing innovation’ workshop held at the ICED17 conference). Consequently, this paper attempts to provide an additional contribution by ‘unpacking’ the body of knowledge that originated in the Innovation Management literature and by discussing the implications and the relevance of its key components on design processes. This will allow providing a high-level synthesis of the innovation management domain, which exhibits specific integration elements that may be relevant for scholars and practitioners operating in the design domain. Moreover, this discussion will lead to the proposal of an original integration framework that associates the typologies of innovation activities along the technology lifecycle to their business implications and to their technical and organizational implications on the design process. Thanks to this framework, scholars and practitioners from both domains may identify the typical design challenges that are inherent to each type of innovation activity and evaluate the suitability of specific support methods and tools (or, conversely, gain a better understanding of the situations in which method and tools are applicable). Specifically, the framework demonstrates how the textbook description of design processes must quite significantly be adapted to the specific ‘situation of innovation’ that is taking place, in order to avoid the risk of ‘one size fits none’.
Specifically – and differently from the UIP – this paper is based on the tenet that innovation activities are not all the same, and that the significant variations that can be observed cast a strong influence on the ensuing design activities. From a methodological perspective, the paper can be framed as a theoretical systematic analysis that rigorously progresses from the typologies of innovation activities alongside the technology lifecycle, to their business implications and – finally – to the identification of the technical and organizational implications that these differences have on the design process.
The structure of the paper covers and mirrors this three-step narrative. Section 2 of the paper presents the fundamentals of Innovation Management and its main – and most relevant to the design domain – reference models. Specifically, this section presents a two-dimensional analysis, in which one axis allows identifying three main lifecycle phases that occur along the lifetime of a technology. While this classification can be considered to be fairly independent of industry sector and underlying technology, the following discussion will follow the hypothesis of working on discrete products. In the case of continuously manufactured products and/or services, the analysis may therefore be carried out in a similar way, but eventually leading to slightly different details and conclusions. The second axis then discusses the impact of these phases of the innovation lifecycle on both the side of supply (i.e., on the value chain that provides the innovation) and demand (i.e., on the potential customers and – more broadly – on the sociopolitical system). This dual attention to supply and demand allows understanding how innovation – and later on, design activities – are deeply shaped by the interplay and by the evolutionary dynamics that occur on both sides of producers and customers/consumers.
The discussion in Section 2 recognizes that meaningful innovations are systemic in nature (Smith & Browne Reference Smith and Browne1993). Therefore, this discussion on the supply side must be further disaggregated at three different levels, differentiating between the focal system, its subsystems (i.e., the key components) and its suprasystem (i.e., the ensemble of the focal system and of the complementary systems that allow its operation). Different types of innovations in fact will occur at the intersection between a lifecycle phase and a given system level. For instance, and perhaps counterintuitively, radical innovations (e.g., ABS systems) may occur within a mature technology (i.e., the car architecture) and without generating disruption, if they are localized within a given subsystem. Additionally, the systemic perspective allows a stronger understanding of the implications cast on vertical integration choices occurring within the value chainFootnote 1 (Baldwin & Clark Reference Baldwin and Clark2000) and the resulting distribution of design activities among firms. If one considers the case of electric cars, for instance, as the focal system, batteries will be a key subsystem, while recharging stations will be a key complementary system. Architectural design choices about both components and complementary systems lead to ‘make or buy’ choices, as well as to evaluations on agreements with technology providers, such as partnerships, alliances or acquisitions.
In the following Section 3 of the paper, the analysis is extended in order to understand the implications that each of the three lifecycle phases casts on the technology- and product-development process. The analysis will borrow from Luo’s UIP by distinguishing among the three phases of basic research, applied research and product design and development. Product design and development will be further broken down in four subphases, in order to show how each is affected by the various types of innovation. Of the four, the former three subphases will coincide with the customary and widely accepted distinction between conceptual, embodiment and detailed design (Pahl & Beitz Reference Pahl and Beitz1988; Ulrich & Eppinger Reference Ulrich and Eppinger1995). The fourth and latter subphase will be associated to manufacturing process design, which is of course integral to new product development in the previously stated hypothesis of discrete manufactured products. Manufacturing process design could also be integrated with the other design subphases. However, while this concurrency would be justifiable from an operational perspective, we prefer keeping product and process design apart, because they are conceptually different and – most of all – because they operate differently depending on the type of innovation that is being pursued.
Finally, Section 4 of the paper attempts to shed some light on emerging and somewhat still unexplored approaches to innovation and design. Specifically, the increasing role of digital technology and its inherent flexibility enables completely new approaches to design and innovation, and the discussion will be aimed at reflecting on implications for the Engineering Design community, trying to highlight and list relevant research directions.
2 Technology lifecycle and innovation dynamics
The main starting point for the current discussion is that innovation is not a linear phenomenon, but follows distinct phases of revolutionary and evolutionary progress (Tushman & O’Reilly Reference Tushman and O’Reilly1997; Iansiti Reference Iansiti2000).
According to this perspective, the evolution of a technology can be described by looking at the evolution of performance indicators, whose behavior usually follows a sequence of s-curves. When a technology first emerges, its performance is usually quite low, until a sufficient degree of maturity is reached. At this point, the technology evolves and performance increases at a significant speed, until it eventually reaches a technological limit, i.e., a performance level that cannot be overcome due to intrinsic technology limits. When progressing along the s-curve, it is common to define these three main phases respectively as incubation, diffusion, and maturity. Figure 1 depicts this evolution.

Figure 1. The S-shaped evolution of technology.
Once the technological limit has been reached, firms that want to improve their products will have to embrace new technical solutions by choosing among a number of new candidate technologies available, many of which will have been developed independently of and outside of the industry. This revolutionary phase will involve significant experimentation, until players are able to identify which competing technology is able to perform adequately with respect to existing or emerging customer needs (Anderson & Tushman Reference Anderson and Tushman1990).
Within these phases, innovation is usually considered to be determined by two different phenomena. During revolutionary phases, one usually refers to technology push, whereby innovation occurs because firms are forced to ‘scout around’ for new technological solutions that may overcome the technological limit that characterizes the current technology, find them in developments that have been generated independently from the industry, and deploy them in order to match an explicit or latent demand. Conversely, during evolutionary phases, one generally refers to demand pull, whereby firms observe the explicit demand for improved products that emerges from the market, and direct the evolution of the technology (and of the underlying science) in order to effectively respond to these needs.
Insight 1 for the toolbox: S-curves represent a fundamental instrument in the toolbox of those who deal with technological innovation, since they in some cases can be used to assume the state of evolution of a specific technology (Becker & Speltz Reference Becker and Speltz1983). For this kind of applications, as it will be later discussed, readers can generally refer to contributions in Technology Foresight and Forecasting. The topic should be treated with some cautions that concern the choice of performance indicators as proxies for technological progress, and the use of time as the independent variable (Cantamessa & Montagna Reference Cantamessa and Montagna2016).
If one adopts a broader perspective, s-curves associated to a given technology imply a broader concept, or technological paradigm. A technological paradigm can be considered to be a mixture of supply-side and demand-side elements that blend together in a coherent whole and give birth to a technological trajectory (i.e., the s-curve) that is at the same time viable for producers and appreciated by the market (Dosi Reference Dosi1982). From the side of supply, a paradigm is made up of theories, knowledge, tools, and methods that allow transforming a given technology into an actual offering of products and services, and around which sustainable business models can be established. In order for a new paradigm to emerge, industry must be capable of mastering the new technology so that products, their key subsystems and complementary systems may effectively be produced. In turn, this implies the possibility for producers, suppliers and complementors to define profitable roles within a supply chain. From the side of demand, instead, a technological paradigm is defined by beliefs, needs, objectives, rules and meanings (Norman & Verganti Reference Norman and Verganti2014) that customers – and society as a whole – attribute to the product. If these are met by the technology, customers will choose it and the paradigm will actually emerge. Conversely, if the features of the product conflict with what customers and society need and value, the paradigm will be unable to emerge or – at the least – its emergence will be delayed.
Insight 2 for the toolbox: The concept of technological paradigm, and the interplay between the bundle of supply-side and demand-side elements that define this dynamic equilibrium, can help to frame the environmental conditions in which both revolutionary and evolutionary innovation might occur. The emergence of an innovation implies considering the equilibrium in the innovation ecosystem, considering the technological system not as an isolated entity, but involving elements that are located ‘supra’ or ‘sub’ the system itself (recalling the systemic nature of innovations proposed by Smith & Browne (Reference Smith and Browne1993)).
For instance, the cloud computing paradigm has overcome the client–server paradigm that dominated computer systems since the ‘80s. This success is tied to the convergence of supply-side and demand-side factors. Among the former, the economies of scale that can be achieved by centralizing data processing and storage, and the widespread availability of cheap and reliable bandwidth for connecting servers with clients. Concerning the latter, users have valued the possibility of accessing online services through multiple devices, both fixed and mobile. Moreover, users have been confident that an Internet connection will always be with them, while they have been quite unconcerned of privacy issues associated to the personal data they entrust to service providers. Similarly, the technology that will power the car of the future will depend on technological progress, but will also depend on users’ attitudes. Specifically, one can wonder whether users will really be ‘range anxious’, as many current surveys suggest, or whether they will realize that driving electric cars that have a limited range perfectly suits most driving patterns (or, whether they will value ownership of vehicles instead of looking for mobility services).
Table 1 therefore clearly distinguishes between these two components: the supply side that comprehends all the levels of the system and the demand side that instead looks at customer.
Technological paradigms evolve following dynamic patterns that scholars have attempted to understand and represent with a variety of models (e.g., Utterback & Abernathy Reference Utterback and Abernathy1975; Anderson & Tushman Reference Anderson and Tushman1990; Tushman & Rosenkopf Reference Tushman and Rosenkopf1992; Christensen Reference Christensen1997; Rogers Reference Rogers1962). For the sake of brevity, we will focus on a very limited selection of models, chosen because of their relevance and widespread acceptance. The following subsection will concentrate on a perspective that mainly looks at technology evolution and at the supply side of the innovation process as a possible explanation of the distinct way with which s-curves evolve in time. The subsequent subsection will then discuss a demand-side perspective that looks at the heterogeneity of markets along the technology lifecycle.
Table 1. Supply and demand sides of innovation process

2.1 Supply-side variations along the technology lifecycle
According to Utterback & Abernathy (Reference Utterback and Abernathy1975) and the many other authors that have contributed to comprehend the dynamics of innovation, these can be explained by simultaneously monitoring technical performance, adoption sales,Footnote 2 the number of firms in the industry and, finally, the rates of product and process innovation (see Figure 2). At the onset of a technology revolution, i.e., at the beginning of an s-curve, one can witness a growing number of firms that enter the industry, because they are ‘gold-rush like’ attracted by its future potential. Each firm that enters the market carries a stock of prior competencies and assets that it believes will be useful, and this leads to an extremely diversified range of competing and alternative technical solutions. The rate of product innovation is very high, but this does not lead to significant progress, since firms are not concentrating their efforts in the same technical direction and cannot therefore generate cumulative progress based on the imitation and improvement of competitors’ inventions. As a consequence, this growing number of firms compete on a demand that remains stubbornly low. This initial phase is termed fluid. Within this fluid phase, technology is often subject to hype, i.e., to exaggerated expectations of its potential (Fenn & Raskino Reference Fenn and Raskino2008). On the one side, the hype effect stimulates investment and research on the emerging technology, but it also might lead to a phase of disillusionment and retrenchment (often called ‘trough of disillusionment’ by practitioners) when the market realizes that the potential of the technology is more limited than what previously thought.

Figure 2. The Abernathy and Utterback’s model.
The industry exits the fluid phase and enters the transition phase when one product architecture emerges as the front runner, and becomes widely recognized as the dominant design. The dominant design encapsulates the product concept, the technical solutions, the components and the features (i.e., the architecture) that become widely accepted as the ‘normal product’ in that industry and market, overcoming other competing designs.Footnote 3 The emergence of the dominant design also clarifies what is the real potential of the emerging technology and the actual customer needs it can practically fulfil, and this helps drag the technology out of the previously mentioned ‘trough of disillusionment’. At this point, a sort of avalanche effect is determined, and the growth segment of the s-curves can start: product performance takes off, since technical knowledge is now focused on the dominant design, thus allowing imitation among competitors and cumulative progress. Thanks to improved product performance and a clearer identity, adoption sales start picking up as well. At the same time, the number of active firms starts to decline (i.e., the industry experiments a so-called ‘shakeout’), either because some companies’ assets and competencies do not match the dominant design, or because required growth rates are too high to be sustained by the firms that are managerially or financially weaker. Increasing industry sales and a dwindling number of competitors imply even higher growth rates for the surviving firms, and this exacerbates their need to endure such growth.
At this point, the technology lifecycle enters the so-called specific phase. During this last phase, firms strive to compete over cost and quality in a scenario characterized by increasing demand. Companies shift their focus from product to process innovation, since the now stable product architecture makes it technically possible and strategically important to innovate the process, in order to improve quality and reduce costs. Firms therefore develop optimized and capital-intensive machineries that are specific to the dominant design, which allow higher quality and significant economies of scale. In turn, this leads to lower product cost, lower prices and an ever increasing demand. This furthers the shakeout, because the new processes determine a minimum efficient scale, and this generally leads the industry into an oligopoly.
Insight 3 for the toolbox: The Abernathy and Utterback model can represent a valuable contribution to the framing of the different innovation typologies that occur along the lifetime of a technology. In particular, the concept of dominant design, which specifically represents the emergence of an established architecture, acts as a watershed between the fluid and specific phases. As discussed in the text, during the fluid phase, one can envisage radical innovation at all levels (focal system, subsystem, suprasystem). During the transition phase, one can expect architectural innovation. Finally, during the specific phase one can expect architectural or modular innovation (which can well be viewed as radical at subsystem level).
The phases proposed by the Abernathy and Utterback model are used as rows in Table 1.
During the three phases identified by Abernathy and Utterback, innovation follows distinct patterns, and defines the way design is carried out within each. In the fluid phase, products are typically subject to significant change in both the underlying technology and in product architecture. Following the taxonomy proposed by Henderson & Clark (Reference Henderson and Clark1990) and depicted in Figure 3, one can speak of radical innovation. The fluid phase actually might also imply the need for significant change in subsystems and in elements of the suprasystem that allow the structuring of a sustainable paradigm around the innovation. This need for change at levels other than the focal system is obvious when subsystems or suprasystems are core to the innovative technology underlying the innovation. In other cases, firms will instead tend to carry over technical solutions from the past or from other fields, even though this might be suboptimal with respect to developing them anew and specifically for the new application. For instance, firms currently working on electric cars must choose whether to use batteries based on the same technology that is already used for portable electronics, or whether to develop new solutions. Thinking about suprasystems, a similar dilemma holds for recharging stations. The choice between carryover and redevelopment of components and systems is quite significant, since the former option requires less investment, but might lead to suboptimal technical solutions, whereas the latter might not only require greater investment, but also the need to increase the degree of vertical integration of the firm.
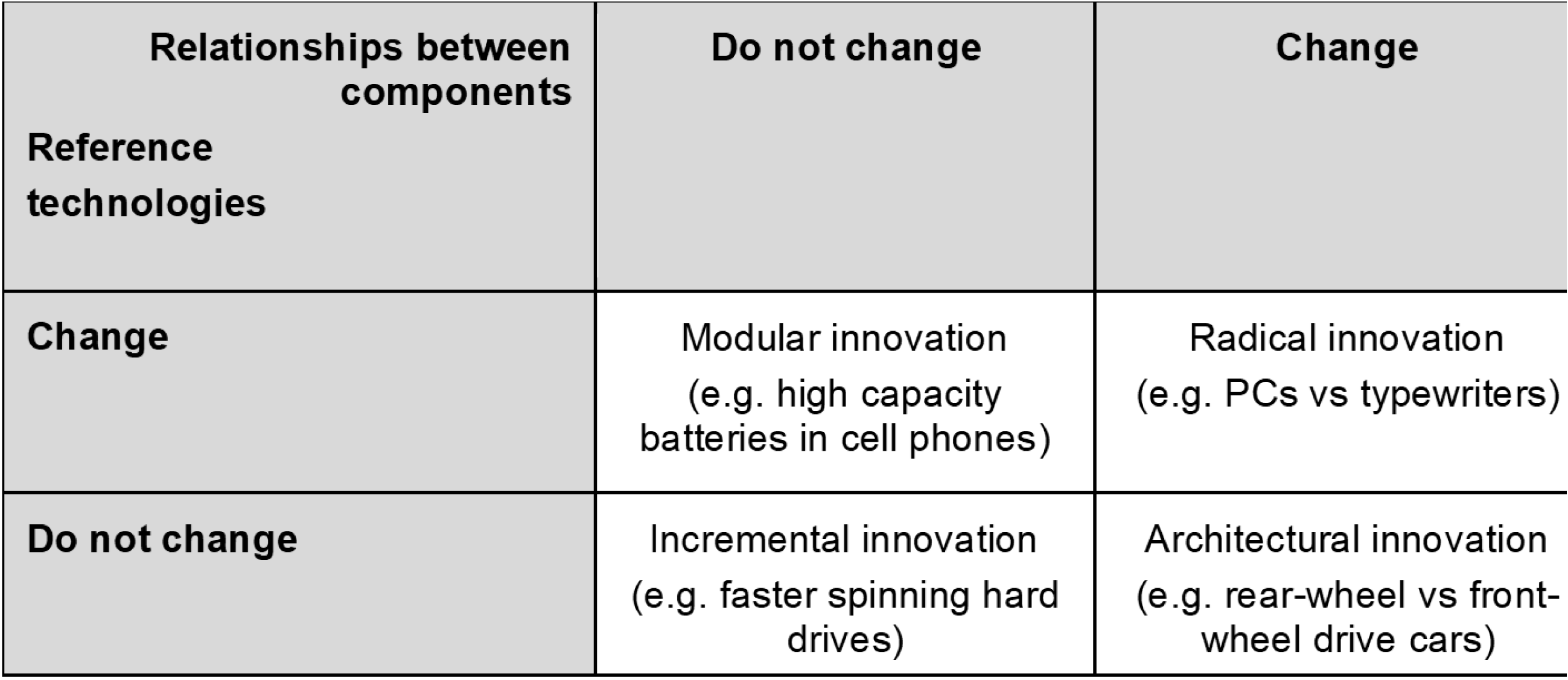
Figure 3. The innovation taxonomy proposed by Henderson & Clark (Reference Henderson and Clark1990).
In the transition phase, and once the dominant design is established, innovation will typically not lead to significant change in either the underlying technology or product architecture, and will therefore shift to an incremental type. In some cases, the dominant design may be subject to some further revisions or optimizations, usually without significant change in the underlying technology (e.g., one can think of the shift to monocoque car bodies and front wheel drive powertrains in the 1930s). This implies architectural innovations. The freezing of a dominant design enables the design and diffusion of complementary and specific subsystems and suprasystems. Given that both producers and complementors make substantial investments in physical and intangible assets that are dominant design-specific, this will enhance the stability of the design itself, increasing the costs of switching to other alternatives (one can therefore say that the industry experiments ‘lock in’).
In the specific phase, innovation will mostly be incremental at all levels (product, subsystems and suprasystems). Due to the length of the specific phase, which often spans decades, it is likely to witness the integration of radically new technology within the dominant design, as long as it is possible to localize this change within subsystems and integrate them without too much effort in the overall product architecture. In this case, what appears to be a radical innovation at component level can be considered to be a modular innovation at system level.
Insight 4 for the toolbox: A unique taxonomy for classifying innovations does not exist and above all each classification in the literature provides a different perspective, a different layer of analysis and refers to a different domain (see for instance seminal contributions from Dutton & Thomas (Reference Dutton and Thomas1984); Tushman & Anderson (Reference Tushman and Anderson1986); Christensen (Reference Christensen1997); etc.). However, the classification proposed by Henderson & Clark (Reference Henderson and Clark1990), which observes the two axis of underlying technology on the one side, and of product architecture on the other, results particularly valuable to highlight the underlying links between the technological changes occurred during the lifecycle and the design choices from which they have been generated. It consequently is useful to identify the kind of innovation that might occur given a specific lifecycle phase and technical change.
Table 1 specifically highlights in its cells these innovation typologies at each level of the system.
2.2 Demand-side variations along the technology lifecycle
Demand-side issues are central to innovation and design, because the gap between invention and innovation is precisely due to market attractiveness and the adoption process that might ensue. In other words, what matters is the degree to which the new technical features of an invention are able to address market needs, so that customers’ willingness to pay is higher than producers’ costs, which will grant utility to the former and profit to the latterFootnote 4 (Rogers Reference Rogers1962). When an invention does not make it to the market (i.e., it does not become an innovation at all) – or when it reaches the market but fails to diffuse (i.e., it becomes an unsuccessful innovation) – it is likely that the design process has failed in the effort to integrate the technology into a product. In other words, it has been unable to convey the features of the technology into a clear and economically sustainable value proposition for its customers. While the above statement might seem fairly obvious, the matter is strikingly difficult to tackle in practice, because of the two following main reasons.
One first reason is that, in the case of radical innovations, the needs being addressed are often latent and not explicit. This means that producers must progressively build adoption processes and lure potential customers not by simply marketing their products as better versions of something they already are familiar with, but as something completely new, that will allow them to perform acts or satisfy needs they were not even able to conceive.
The second reason is that the rather difficult process of fostering adoption of an innovation cannot be carried out indiscriminately to all customers that make up the potential market, but must exploit the existence of distinct market segments defined by different degrees of propensity toward the innovation. Therefore, marketing efforts and diffusion will start from the most favorable segment and progressively spread to the rest of the population. Following the widely accepted segmentation by Rogers (Reference Rogers1962) and Moore (Reference Moore1991), it is possible to identify four typical segments, and namely innovators, early adopters, early majority and laggards, who sequentially adopt the technology.Footnote 5 These segments are not only different because of their propensity to adopt, but also because of their reasons for adoption and – therefore – of the type of product they look for. As a consequence, producers must not only ensure that the technology evolves along the performance s-curve in absolute terms, but also that the products they develop and market are precisely addressed to the customer segment that is appearing along the adoption s-curve. Transitioning from one segment to the next can be quite difficult – especially when moving from the early adopters to the early majority segments (Moore Reference Moore1991) – because the needs of the latter are still unknown to the producer.
At this point, it may be interesting to attempt to draw a connection between the four demand-side segments proposed by Rogers and the three supply-side phases proposed by Abernathy and Utterback. We are not aware of prior works having attempted a rigorous empirical analysis of this topic, and our discussion will be somewhat rough-cut, because each historical case will exhibit a slightly different timeline.
Insight 5 for the toolbox: Product-development scholars and practitioners have studied success factors in product development (e.g. Cooper Reference Cooper1979; Calantone, Di Benedetto & Divine Reference Calantone, Di Benedetto and Divine1993; Griffin & Page Reference Griffin and Page1996; Sivadas & Dwyer Reference Sivadas and Dwyer2000; Troy, Hirunyawipada & Paswan Reference Troy, Hirunyawipada and Paswan2008; Kam Sing Wong & Tong Reference Kam Sing Wong and Tong2012), and many contributions from engineering design have embraced the idea that products should be developed with a clear focus on customer needs (e.g. Akao Reference Akao2004; Weber Reference Weber2008; Cascini, Fantoni & Montagna Reference Cascini, Fantoni and Montagna2013). A variety of techniques have been proposed for this purpose, ranging from market research techniques, to methods whose objective is the translation of needs into product requirements and specifications (e.g. Cooper & Wootton Reference Cooper and Wootton1988; Darlington & Culley Reference Darlington and Culley2002). The rationality that is inherent to the customer-driven approach might make it inapplicable to so-called design-driven innovations (Verganti Reference Verganti2009). In general, Norman & Verganti (Reference Norman and Verganti2014) state that in the case of radical innovations customer-driven approaches may prove unable to elicit latent customer needs; this perspective results instead more valuable in the case of incremental changes.
The segmentation proposed by Rogers is a strong call to focus on effective – albeit hidden – customer needs and to be wary of the difficulty of translating needs into requirements. This is particularly true for products, whose needs are difficult to be identified and for complex purchasing processes (e.g., in the case of B2B sales) in which multiple actors interact.
In general, the fluid phase occurs within the Innovators market. The specificity of Innovators’ needs suits quite well the technological immaturity typical of this phase, but also adds to the chaotic competition between technologies, since it is possible that each technical alternative may fit the idiosyncratic needs of a portion of Innovators. The transition phase, in which one dominant design emerges over the competing alternatives, is then likely to occur when the market is transitioning from the Innovators to the early adopters segment. This is a crucial point since – while the dominant design will remain the same throughout the diffusion process and lock in for a very long time – the selection will be determined by the choices made by the final portion of Innovators and the first of early adopters. This implies a strategic imperative for firms operating at this time, since by making the right technology and design choices they will not only be successful in selling their products to the current customers, but ‘buy themselves a ticket’ for survival throughout the technology lifecycle. For instance, one can revisit the way with which the smartphone dominant design, pioneered by Apple (i.e., multifunctional, touch-screen based, running applications offered by massive amounts of third party developers), emerged by defeating application-oriented and keyboard-based devices proposed by Nokia (which were respectively aimed at business users and gamers) and RIM (aimed at business users). This dominant design emerged because Apple’s products provided a better fit with the needs of new segments of adopters, who did not want a ‘specialist’ device, valued flexibility, and were not bothered by the lack of a physical keyboard.
Finally, during the specific phase, demand will switch to the early majority, late majority, and finally Laggards segments of the market. These customers will be led into adoption if they view products as technologically mature and their price is correctly balanced against the utility they convey. Moreover, after adoption sales have peaked, the majority of sales will switch to replacement and additional sales, which will call for a different value proposition. Customers will in fact buy products if these reach the end of their operating life and/or if firms are able to offer a sequence of product generations that deliver incremental but clear advantages over their predecessors.
Insight 6 for the toolbox: Customer needs do change along the lifecycle. Moore’s segmentation can be useful to identify the orientation that design activities should have along the technology lifecycle. Otherwise, a product that is highly successful with early adopters risks to be likely unsuccessful when the early majority segment kicks in, since designers in the early phases of the technology lifecycle may fail to understand the new user requirements that characterize the early majority segment.
Table 1 provides a high-level synthesis of the previous discussion, showing the way by which innovation dynamically evolves on both the supply side and the demand side of the market, and along the three phases of the technology lifecycle. The following section of the paper will build on this discussion in order to identify the specific role that – within each phase – designers and the design process have in enabling the innovation phenomenon.
3 Innovation process, technology and product-development process
This section of the paper is grounded on the previous high-level description of the different phases of innovation process, with the aim of highlighting their implications on the technology and product-development process. The structure of this discussion will build on Luo’s ‘united innovation process’ (2015). Luo proposed a broad perspective that spanned the spheres of ‘science’, ‘design’ and ‘entrepreneurship’. Luo’s perspective is coherent to the traditional ‘linear model of innovation’ (Ames Reference Ames1961; Godin Reference Godin2006). The linear model is quite simple, though it must be remembered that it has often been challenged by scholars who developed deeper insights on the phenomenon (Kline Reference Kline1985; Kline & Rosemberg Reference Kline, Rosemberg, Landau and Rosenberg1986; Edgerton Reference Edgerton, Grandinand and Wormbs2004). Alternative models of innovation highlight the iterative nature of the process, and especially the key role of technical knowledge developed independently of scientific endeavor in supporting both design and science. It is in fact quite apparent that many innovations (especially incremental) arise independently of basic research, just as many outcomes of ‘upstream’ activities never actually reach the market. Moreover, the model is not unidirectional, since scientific and technological outcomes ‘push’ downstream, but can also be ‘pulled’ by market demand. In the end, the model can be considered not as much as a process (in its strict sense). Rather, it can be considered as a classification of activities, ordered according to their nature, to their possible linkages and to their distance from the market. For the sake of simplicity, and with this caveat in mind, we will continue using the linear model, with a few differences with respect to Luo’s proposal.
First, we will distinguish between basic and applied research. Second, and in order to create a deeper linkage with the design literature, we will divide the design process according to the well-known phases of conceptual, embodiment, detailed and process design (Ulrich & Eppinger Reference Ulrich and Eppinger1995; Pahl & Beitz Reference Pahl and Beitz1988). Finally, we will not consider an ‘entrepreneurship’ phase, in the recognition that entrepreneurship (or, more broadly, business activity) is one of the environments in which the previous activities can be performed, but it would be quite hard to recognize it as a distinct process phase.
Therefore, here and as shown in Figure 4, the linear process of innovation starts with basic research, which is responsible for purely scientific activity and whose aim is discovery, i.e., the generation of knowledge pertaining to phenomena (physical, social, or other). Basic research is sometimes developed out of pure intellectual curiosity (i.e., ‘blue sky research’), and sometimes might have quite clear practical implications (Stokes Reference Stokes1997). However, in neither case, the outcomes of basic research consist in a solution to a specific problem. At the most, these outcomes can consist in a relevant body of knowledge that may serve as the basis for subsequent problem solving efforts. So, basic research can be considered as a purely scientific endeavor, which sets it clearly apart from a design activity.Footnote 6 Distinction does not imply separation, and one can conceive areas of overlap and cooperation where scientists inform designers of the practical potential of their discoveries and – conversely – the latter inform the former about the specific needs and questions that they encounter in dealing with technology or – more broadly – in solving problems in the market and in society.

Figure 4. A simplified ‘linear’ process of innovation.
Following basic research is applied research, whose aim is the development of a technological solution that may solve a given – and usually quite broad – problem. One can say that the most significant and far-reaching inventions occur at this stage. Invention occurs by drawing from knowledge created within basic research, as well as from knowledge that is generated within the domain of technology. The practical deliverable of this phase is generally a demonstrator, which is an artifact whose purpose is to show that a technology is technically viable. At this phase, the main focus is technical and rests on showing the viability of the individual technology per se. Inventiveness required is also at its foremost, and at the heart of this inventive process is the capability to design new technological concepts. Attention paid to potential application areas and target markets is present, but still relatively fuzzy. Demonstrators are therefore quite far from commercial products, and do not include those adaptations and/or the complementary technology that will enable them to actually fulfil the needs required by specific applications on the field.
When moving into product development, the focus shifts quite dramatically, since the firm will start dealing with commercial attractiveness (thus defining value propositions, business models and ultimately prices) and industrial viability (thus defining cost and margin). Product development also implies dealing with seemingly menial and often neglected aspects such as usability, safety, manufacturability, product certifications, writing users’ and field service manuals, and so on. From a business and legal perspective, it is customary to split product development in a pre-competitive and a competitive (or industrialization) stage. The discriminating element is that the former stage leads to prototypes that do not have commercial value (i.e., they cannot be sold), while the latter leads to the actual product that will be launched on the market.Footnote 7 A prototype is clearly different from a demonstrator, because the focus is no longer on an underlying technology, but on the full range of features and technical choices that the future product will incorporate.
From a technical perspective, one might opt for a different subdivision of the product-development process and adopt the phases suggested by engineering design literature. The process can therefore be divided according to conceptual, embodiment, detailed, and then process design. While process design often occurs in parallel with the prior phases, it makes sense to leave this chronological simultaneity aside, given the fact that the conceptual aims of process design (and its allocation within the firm’s organization and supply chain) are different from the ones that characterize product design.
3.1 Implications on the phases of the technology lifecycle
A key proposition being set forward in this paper, is that the innovation process described above (from basic research to product development) is significantly impacted by the historical, social and economic setting, that is – namely – by the current position in the technological lifecycle as described in Section 2. It will therefore be possible to extend Table 1 up to Table 2, in order to describe the way with which each process phase is carried out during each lifecycle phase. We will therefore comment on Table 2 by reading it by rows and columns.
Table 2. The entire framework

During the fluid phase, technology-push forces are predominant: radical and paradigm-changing innovations typically emerge. Previous technology has reached its limit, it is unable to address emerging or increasing customer needs, while advances in basic research create new opportunities and prospectively enable previously unimaginable functions or performance in a variety of products and opportunities in industries. During this phase, designers may actively engage with researchers in order to carry out technology foresight activities, by understanding the practical (i.e., technical and business) potential emerging from research results and match it with current or prospective needs arising in the market and society.
Insight 7 for the toolbox: Qualitative approaches like scenario analysis (e.g. Clarke Sr. Reference Clarke Sr.2000) or expert opinions (e.g. Okoli & Pawlowski Reference Okoli and Pawlowski2004) are frequently proposed, because of the uncertainty that characterizes these radically new situations. Nevertheless, quantitative methods could be employed to estimate the market adoption of technically superior new products (Sahlo & Cuhls Reference Sahlo and Cuhls2003).
Moving to applied research, the effort of matching technological potential with market needs becomes more focused and application-directed, and allows the definition of more definite strategies (namely, Technology Roadmapping, Firat, Woon & Madnick Reference Firat, Woon and Madnick2008) in which designers can provide a significant contribution.
Moreover, the development of technology demonstrators often sees an interesting interplay between the efforts of applied researchers, who provide a scientifically grounded perspective, and that of designers, who provide an application-oriented one. At this phase, creativity has a key role. From designers’ perspective, this implies a high-level version of conceptual design, which allows radically new solutions to emerge. This creative thinking is made possible by the fact that one is still quite far away from the constraints cast by a product aimed at a specific and narrow application, while being in the fluid phase allows ample freedom from any technical and architectural constraint.
Moving to product development, conceptual design becomes the most important design phase. Though designers must now take charge of the constraints arising from a specific application domain and market segment (usually that of innovators and then early adopters), being in the fluid phase ensures ample degrees of freedom and technical and architectural design decisions are still open. Given the uncertainty on customer needs and the impossibility of deriving them from users who have not yet adopted and experienced the new and radically innovative product, designers will mainly have to operate based on their vision of the emerging technology and product. Therefore, user-centered design techniques (Norman & Draper Reference Norman and Draper1986) will be difficult to be applied and will not provide significant insight to designers, if compared to what occurs during the subsequent transition and specific phases.
Depending on the degree with which one must (or decides to) deal with supra- and subsystems (something that runs in parallel to decisions on vertical integration of both the system and the firm), the scope of conceptual design becomes narrower or broader. Dominant design is still not established and design choices are known and accepted to be transitory and non-optimized. This implies that relatively less effort will be placed on embodiment and detailed design, since the aim will be that of bringing the product to the initial market, and not striving for perfection. Finally, process design will not have a significant role in this phase; low volumes, early customers’ higher willingness to pay, and the lack of a stable product architecture do not justify significant investments in this area.
Insight 8 for the toolbox: Many methods and tools from the Engineering Design literature can be thought to have a key role when dealing with product development in the fluid phase. From brainstorming (Osborn Reference Osborn1953; Sutton & Hargadon Reference Sutton and Hargadon1996) to TRIZ (Altshuller Reference Altshuller1984; Cascini Reference Cascini2012), from biomimicry (Macnab Reference Macnab2012; Goel, McAdams & Stone Reference Goel, McAdams and Stone2014) to morphological tables (Ritchey Reference Ritchey2006), this literature provides a wealth of tools with which this process can be supported. Specifically, by referring to the TRIZ method, one can realize that it is mostly during the fluid phase of the technology lifecycle that designers can enjoy the freedom not to simply manage contradictions, but to remove them outright thanks to breakthrough ideas enabled by new technology.
In this context, Conceptual Design allows the definition of functions the artifact must fulfil, and the identification of an innovative combination of principles and processes that will allow the artifact to behave accordingly. It therefore follows that the traditional Engineering Design literature (Rodenacker Reference Rodenacker1971; Pahl & Beitz Reference Pahl and Beitz1988; Ulrich & Seering Reference Ulrich and Seering1988) can provide a clear frame of reference and a rigorous support to concept creation, screening and selection, using a wide variety of tools and methods. In some cases (or industries), in which product value is more tied to cultural aspects and beliefs rather than to performance, the functional perspective that characterizes the engineering design approaches may appear to be somewhat forced and the Design-driven Innovation perspective (Verganti Reference Verganti2009) and design thinking (Brown & Kātz Reference Brown and Kātz2009) can be adopted in order to support the deployment of innovative technology into radically innovative products.
During the transition phase, basic research does not have a particularly strong role given that – following the emergence of a dominant design – the main technological choices have been already made. Functional and performance requirements arising in the newly defined and rapidly increasing market start to dictate an applied research agenda, according to a typical demand-pull perspective. The role of the designer here is to translate maturing user needs into performance requirements and then into well-defined demands on technology development, thus enriching the outcomes of the Technology Roadmapping activity. In these still-early phases of the product lifecycle the real challenge lies in the correct understanding of the user requirements that characterize the early majority segment, and designers are required to move progressively their focus from purely functional features to technical performances, usability and user experience.
During this transition phase, the latitude of conceptual design becomes much more constrained, and the scope of inventiveness narrower. Creativity processes are bounded by the now-stabilized architecture and system (engineering) design approaches become prevalent (Ramo & St. Clair Reference Ramo and St. Clair1998). At the most, conceptual design consists in making the dominant design evolve before it freezes, by introducing architectural innovations and adjustments to the product system, in order to enable improved fit with user needs. The ‘vertical’ scope of conceptual design will also become narrower, given that suprasystems and subsystems will tend to freeze quite rapidly and – quite often – their development will be allocated to other firms in the value chain, following a process of vertical disintegration. With respect to user needs, it becomes easier to elicit them from current users, who now are belonging to the early adopters segment. These users have already gained some experience with the products, and their needs are closer – though not perfectly aligned – to those of the mainstream population. Designers can therefore look for support from user-centered approaches (Norman & Draper Reference Norman and Draper1986), though the outcomes must still not be taken at face value, but interpreted with the consciousness that – when moving toward the early majority – these needs might be different.
Insight 9 for the toolbox: The ‘customer need’ concept in engineering design has been quickly broadened considering the role of interaction (Norman Reference Norman1988) and emotions (Fukuda Reference Fukuda2016), up to seeking a deeper understanding of customers’ perception of value, given the cultural and usage context in which they live (e.g. Kim & Hwang Reference Kim and Hwang2011). Regarding the tools and the methods for need identification and requirement definition, a number of approaches have been proposed in the Engineering Design literature and are implemented in industry (for a survey, readers can refer to Darlington & Culley (Reference Darlington and Culley2002)). Quality Function Deployment is probably the most popular (Clausing, 1998; Akao Reference Akao2004), but other methods that aim at including into the design process customer value (e.g. Donaldson, Ishii & Sheppard Reference Donaldson, Ishii and Sheppard2006) or users’ inputs are also frequent (e.g., Redstrom Reference Redstrom2006; Miaskiewicz & Kozar Reference Miaskiewicz and Kozar2011; for a review, Ortiz, Juan & Aurisicchio Reference Ortiz, Juan and Aurisicchio2011).
In order to handle architectural complexity, engineering design community refers to consolidated methods, such as DSM-based techniques (Eppinger & Browning Reference Eppinger and Browning2012), functional block diagrams (Stone, Wood & Crawford Reference Stone, Wood and Crawford1998) and platform-based practices (Meyer & Lehnerd Reference Meyer and Lehnerd1997). Modular function deployment (Ericsson & Erixon Reference Ericsson and Erixon1999), has gained some diffusion in industry, and other methods – such as the ones that originated from the seminal value analysis (Miles Reference Miles1989) or variety reduction program (Kōdate & Suzue Reference Kōdate and Suzue1990) – can also play a role in supporting the management of costs and variety.
Finally, detailed design is nowadays carried out mainly by using widely diffused computer-aided engineering (CAE) technologies. CAE allows to model and test the behavior of engineering systems under different functional and physical perspectives. Within CAE technologies, design optimization techniques (e.g., Gero Reference Gero1985) allow seeking the best design solution to maximize system performance. Optimization may concern (Kicinger et al. 2005) different aspects, such as
– Topology, i.e., the layout or material distribution
– Shape, when the optimization seeks the optimal contour or shape of a structural system whose topology is fixed
– Size, when the optimization searches for optimal cross-sections, or dimensions of elements of a structural system whose topology and shape are fixed.
Optimization mainly makes use of analytic methods for continuous design variables and integer programming for discrete ones, and linear and nonlinear programming are used for investigating the relations among the design variables. Gradient based methods or heuristic algorithms are also often used because of their computational performance. When a unique goal cannot be identified, Multicriteria analysis may be used to substitute the other optimization methods (Eschenauer, Koski & Osyczka Reference Eschenauer, Koski and Osyczka1990).
Finally, design of experiments is used to specify the test plans allowing the validation of hypothesized solutions. Tests are carried out both on physical and simulated models, while Multivariate Statistics is used to perform the tests, the sensitivity analysis and determine model robustness.
Finally, the freezing of technological choices at all levels allows the design and development of production processes that are specific to the dominant design and its underlying technologies. It is therefore time for (re)designing production processes, in order to support growing demand and reduce production costs by achieving economies of scale.
During the specific phase of the technology lifecycle, which can often last decades, basic and applied research follow an interesting interplay between demand-pull and technology-push forces. Concerning demand pull, an established industry often dominated by large players and serving a well-known and stable market can determine a clear (and well-funded) research and development agenda, with the aim of improving technology in order to fulfil progressively growing user needs. On the technology-push side, it often occurs that radical innovation arises at component level, in such a way that it can be easily incorporated in the dominant design, albeit without disrupting it (which would be termed ‘modular innovation’, according to Henderson and Clark’s taxonomy). This complexity, and the often significant amount of money involved, calls for an important role of Technology Roadmapping.
During the specific phase, and given that the dominant design is now frozen, conceptual design at system level ceases to be significant. However, conceptual design becomes particularly important at the level of subsystems and components, which from time to time witness radical innovations and – therefore – the introduction of completely new concepts. Given that the specific phase often leads to growing vertical disintegration of the value chain, the locus of component-level inventive activity involving conceptual design will tend to shift from the producer of the system to its suppliers.
The specific phase will instead lead to an even more grown importance of embodiment and detailed design, whose main task will be the progressive Design Optimization within the framework of the dominant design, in order to improve performance and reduce cost. Moreover, given that during the specific phase the diffusion process has been well exhausted, sales will nearly entirely be associated with the replacement of the installed base. It follows that embodiment and detailed design will be entrusted with the objective of stimulating replacement sales, by providing an endless stream of incremental innovation, new features (often involving modular innovations as described above) and minor adjustments and facelifts. Process innovation will also be quite important, in order to further improve product quality and reduce cost.
3.2 Implications for strategic vertical integration decisions
As already hinted above, the progressive emergence of a dominant design, and therefore the design choices that generated it, do not only have effects on the product (along with its suprasystem and subsystems), but also affect the firm’s business model. More specifically – and relevantly for the discussion – the technical choices made on the product will impact the organization and the degree of vertical integration. In turn, these will have a significant impact on the allocation of design activities, which will either occur within the firm, or span organizational boundaries.
In particular, upstream vertical integration decisions have to do with the development and/or production of subsystems and components. Downstream vertical integration decisions are instead concerned with the role to be covered in the development of the ‘suprasystem’ in which the product will operate. Downstream vertical integration therefore implies the decision to develop complementary products and – sometimes – to change the firm’s business model from the sale of a product to the provision of a service.
The discussion can start looking at the fluid phase, and at upstream vertical integration. In the case of products with a relatively low degree of modularity (i.e., components are significantly coupled to one another, so that the design of each strongly depends on the design of the others), it is likely to observe a high degree of vertical integration until the dominant design has emerged (Christensen, Verlinden & Westerman Reference Christensen, Verlinden and Westerman2002; Argyres & Bigelow Reference Argyres and Bigelow2010). In fact, it is unlikely that other firms may enter the business of becoming a specialist supplier of an architecture-specific component, unless there is sufficient certainty that this architecture is indeed going to become the dominant design. Therefore, firms working on the final product will have to take up responsibility on component development as well. The opposite may happen for highly modular products (i.e., products whose components are functionally uncoupled from one another, so that the design of each does not significantly influence the design of the others). In this case, components may be developed and produced by independent companies, and simply selected and assembled by the firms that are working on the final product.
A higher degree of vertical integration gives a tighter control on components from both a technical and business perspective. However, it also requires a much greater amount of investment, which can make this choice impossible, unless the company is sufficiently well funded. This strategic choice is always difficult and risky, and requires a deep understanding of the product being developed. In some cases, firms might try to develop a ‘dominant design’ out of off-the-shelf components, only to discover that the performance they achieve falls short of what the market requires. On the other side, other firms might undertake the costly road of developing specific components and vertical integration, simply to discover that other firms were able to operate successfully by using available components.
Still during the fluid phase, if one now looks at downstream vertical integration, the main problem lies in the value that complementary goods and/or the suprasystem provide to customers, therefore driving diffusion. If this value is significant, the issue cannot be neglected. However, a firm may decide not to have an active role, assuming that a market for these complementary goods will emerge independently thanks to ‘complementors’ who are technically able to develop these goods and who expect to gain adequate profits. Of course, this leads to a typical chicken-and-egg problem, which may leave diffusion stranded (i.e., complementors will wait for the focal product to diffuse, but customers will not adopt the product because of the lack of complementary goods). Alternatively, the firm may engage in partnerships with complementors or decide for full vertical integration and provide these goods directly. The choice between the three alternatives generally has to do with the degree of technical co-specificity of these complementary goods with respect to the focal product. The greater such specificity, the greater the need to design the two together and – therefore – the less likely that this will occur without vertical integration or a very tight alliance. At the same time, a higher degree of vertical integration requires the financial clout to sustain the related investment and the organizational capability to manage such a complex setting.
When the technology lifecycle shifts from the fluid phase to the transition and then the specific phases, vertical integration problems may become less critical. The stability provided by the dominant design and the increasing demand arising from the diffusion process allow for specialization and a lesser degree of vertical integration, both upstream and downstream. Of course, this is simply a possibility and not an obligation, since the firm will be likely to keep on working on subsystems and/or suprasystems if it recognizes that this will allow to reap superior profits. However, should vertical integration decrease, this will also lead to a reallocation of innovation and of the role of conceptual design along the reconfigured value chain.
4 The impact of flexibility and new research directions
The framework that has been previously introduced is based on the structuring of conceptual linkages between substantial and widely accepted literatures on Innovation Management on the one side and Engineering Design on the other. These strands of literature are based on empirical observations and practical applications that pertain to many different cases throughout history and across industries. As such, the framework can be considered to be broadly applicable and quite safe to be generalized. However, there are some significant emerging trends, which recently have been enabling completely new approaches to design and innovation, and these should therefore be then included in the discussion.
The major trend that can be observed is that of flexibility, which is becoming a key element enabling new approaches to the management of product development (e.g., lean, Ward (Reference Ward2009); or agile, Beck et al. (Reference Beck, Beedle, van Bennekum, Cockburn, Cunningham, Fowler, Grenning, Highsmith, Hunt, Jeffries, Kern, Marick, Martin, Mellor, Schwaber, Sutherland and Thomas2001)). We can define flexibility as the possibility of enacting design changes at low cost (Thomke Reference Thomke1997) or, following Krishnan, Eppinger & Whitney (Reference Krishnan, Eppinger and Whitney1997), flexibility occurs when sensitivity of downstream parameters to upstream design changes results low. Nowadays, this flexibility is made possible because of number of factors, the main ones being:
– digitalization of services, by which producers can continuously adapt their offering in real time. This not only allows rapid adaptation to customers’ evolving needs, but also allows a continuous experimentation and exploration of these needs. Web-based services allow producers to overturn the traditional product-development process, by avoiding preliminary market research, and progressing from initial Minimum Viable Products (or MVPs) to fully fledged and then continuously evolving services. Following the lean development approach, real-time market research (Sanchez & Sudharsan Reference Sanchez and Sudharsan1993) is inflated in its relevance and the MVP is continuously tested, revised, and improved according to a rigorous monitoring of marketing and financial metrics. In turn, this allows a continuous and deep interaction with the different customer segments that progressively appear along the diffusion curve and who ask for better performance and/or different features or performance mix. In this way, each product-development iteration simultaneously incorporates the elicitation and satisfaction of customer needs and the validation of corresponding performance;
– digitalization of physical artifacts, whose functions and performance can be affected by downloading new applications and updating firmware (a paradigmatic example is represented by Tesla cars, which have allowed the addition of new self-driving functions and product ‘recalls’ to be entirely managed via Internet downlinks). In this case, the hardware component of the product becomes the ‘physical interface’ that will enable a bundle of digital functions to address customer needs. Since the hardware component has a longer useful lifecycle than the digital one, product development changes dramatically. On the one side, development of the hardware will be carried out by conceiving the product as a platform enabling a future stream of continuously adapted and improved services, and will therefore occur by striking a tradeoff between production cost and openness and flexibility of the architecture (which could also lead to unused or redundant components). Conversely, the development of the digital side will follow the same approach outlined above for digital services;
– manufacturing equipment, such as flexible manufacturing systems, soft tooling and additive manufacturing, which can in principle allow the efficient production of smaller production runs. Such technology may allow producers to increase the frequency of design changes in order to explore emerging customer needs, or to adapt to evolving ones. This type of flexibility will obviously not be as dramatic as the one granted by digital products and services, but might nonetheless prove to be strategically important for producers of ‘traditional’ products (a typical example can be found in ‘fast fashion’ apparel producers, who use NC machines and digital printers for cutting and printing fabric). Within this trend, the potential of additive manufacturing of impacting product development has not been fully researched. However, this impact is likely to be quite significant both in terms of limited lot sizes and production runs, and in terms of product architecture (i.e., thanks to the shapes that can be produced via additive manufacturing, designers will be able to increase the degree of function sharing, significantly reduce of component count, and shift toward a higher number of products characterized by integral architectures).
While flexibility allows rather effortless design changes to be carried out, one might wonder what drives the possibility and need of introducing such changes at all. This element is fundamentally related to the huge amount of data to be extracted and required by a rigorous real-time observation of customer behavior, both ‘as is’ and in response to the design changes that are introduced. This possibility of collecting ‘big data’ from the field and of cheaply adapting products and services makes it impossible – but also irrelevant – to develop a reliable and complete set of product specifications, and product development becomes a never-ending story of experimentation and adaptation. The value and potential of ‘big data’ is fairly obvious in the case of digital services, but also can occur by harvesting data from Internet-enabled products in current use, thus obtaining previously unachievable insights on products’ mission profiles. Continuously improving products based on real-time data can be viewed as a potentially disruptive change on the product-development process, since it leads to forgo the traditional separation between ex ante development and ex post use of products. This may be viewed as a potentially interesting avenue for further research.
Moreover, producers have the option of managing new value-added services through the use of these same data (e.g., providing preventive maintenance plans) therefore shifting their offering from the traditional sale of a product to the provisioning of a service. Therefore, the traditional distinction between the fields of product and service innovation (and that of product and service development) may become ever more blurred. Given the relatively crisp boundaries that have kept these fields apart in the past – at least in academic circles – this might too lead to an interesting direction for future research.
Conclusions
The paper has provided an original unifying framework linking the main concepts of Innovation Management to Engineering Design. The main consequence underlying such framework is that design activities are not all alike, and that they strongly depend on the phase of the technology lifecycle and on the position within the innovation process. This appears to be particularly true for conceptual design, which the design literature considers being central to the design process, but whose actual role and scope can indeed vary quite significantly.
The paper presents multiple contributions. For the Engineering Design community, including both academics and practitioners, this framework may prove to be valuable in understanding the different ‘innovation situations’ that may occur and the contribution that Design (including its individual methods and tools) can provide to the different phases and steps of the innovation process. The framework may also prove to be helpful to those interested in Innovation Management by ‘opening the black box’ of Design – including its epistemological foundations and methodological support – viewed as the cognitive activity that ultimately ‘makes the wheels of Innovation turn’.
The paper can also be viewed as a conceptually elaborate – yet relatively synthetic – tutorial that is based on a thorough analysis of established contributions in both strands of literature. Of course, further research work could be carried out in order to explore each innovation situation and validate the insights suggested either from a conceptual perspective, or using empirical observations from firms.