DISCUSSION POINTS
• Hydrogen is already an important feedstock supporting the chemical industry, and this makes the transition away from fossil fuels challenging.
• Green hydrogen could help decarbonize the chemical industry and beyond transform the industry toward “green” products manufacturing.
• What is the current status, and which technologies could support such a transition? What is the role of policy in this?
Introduction
Hydrogen in the chemical industry
Hydrogen (H2) is an important component of the universe with an enormous extent of applications. However, it does not exist in free form in nature, but rather is bonded inside ubiquitous compounds such as water and hydrocarbons. As a key building block in chemical processes, a huge fraction of current hydrogen production is used in industrial processes such as the synthesis of ammonia and petrochemicals. The global demand for hydrogen, which has tripled since 1975, is growing every year with no signs of slowing down (Fig. 1). As of 2018, the worldwide annual hydrogen production is estimated to be ~74 Mt, with up to ~96% used in the chemical industry, ~42% alone for ammonia production, and ~52% in different refineries.1 The remaining hydrogen (~6%) is used in other sectors such as glass production and reduction of iron ores (Figs. 1 and 2).
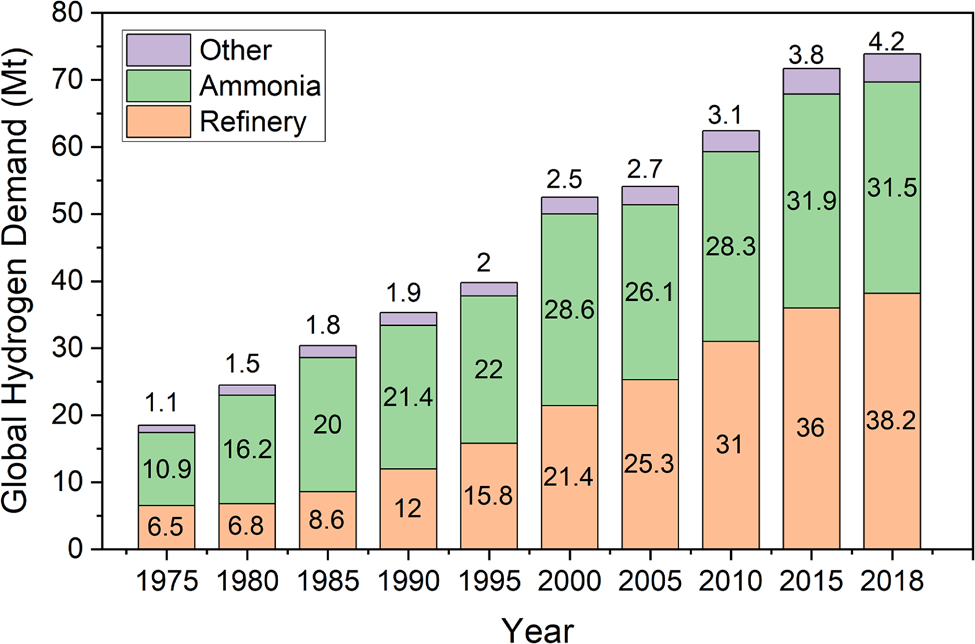
Figure 1. Global demand of pure hydrogen in refinery, ammonia, and other sectors for the period 1975–2018. Source: IEA. All rights reserved.1

Figure 2. The flow of the global hydrogen production, supply, and demand in 2018 – units in Mt, Mtoe (Million tons of oil equivalent), and DRI (Direct Reduction of Iron). Source: IEA. All rights reserved.1
In the chemical industry, ammonia is globally produced through the well-known Haber–Bosch process, in which hydrogen and atmospheric nitrogen are passed over a catalyst at elevated temperatures and pressures. Ammonia is used extensively in agriculture, explosives, and cleaning streams. Common nitrogen-rich fertilizers including urea and ammonium nitrate are produced directly from ammonia. Urea is obtained after reacting ammonia with CO2 originating from the steam reforming, while ammonium nitrate is produced through the catalytic oxidation of ammonia with nitric acid. As a carbon-free commodity, ammonia has been touted as a promising alternative to conventional hydrogen storage systems.Reference Klerke, Christensen, Nørskov and Vegge2 However, most of the hydrogen for its production comes from fossil fuels through reforming – which collectively accounts for 830 Mt CO2/yr globally.1,Reference Navarro, Peña and Fierro3 The chemical industry, with 10% of the global energy consumption and 7% of the greenhouse gas emissions,4 is also the largest user of energy in the industry sector. Enabling the use of renewable hydrogen could thus have a significant impact in decarbonizing the industry sector. Renewables for green hydrogen production include solar and wind coupled with water electrolysis, solar–thermal, and in a distant future direct photochemical hydrogen generation. However, at the moment, the amount of renewable hydrogen is far from meeting the global needs for hydrogen (Fig. 2).
In the refinery sector, which is one of the biggest consumers, hydrogen is used in upgrading the hydrocarbons. Hydrogen is used to remove sulfur, halides, oxygen, metals, and/or nitrogen impurities, and cracking of heavier to lightweight hydrocarbons to produce many value-added chemicals. Most of these processes need careful conditions with suitable catalysts, which dictate the efficiency of the process.
Many chemical industries also use hydrogen extensively to reduce the degree of unsaturation, taste, and/or odor in fats and oils via a hydrogenation process carried out in the presence of nickel catalysts.Reference Veldsink, Bouma, Schöön and Beenackers5,Reference Allen6 This process increases the melting point and enhances the resistance to oxidation with prolonged preservation. In the hydrogenation process, the amount of hydrogen consumed depends on the oil and the degree of hardness (measured by the reduction in iodine number – that is the amount of hydrogen gas equivalent to iodine absorbed), the purity of hydrogen, and the equipment. Assuming that high-quality hydrogen is used, the actual amount of gas required is often ~110% higher than the theoretical values.Reference Wurster7
The hydrogenation of fats produces trans fats, which have adverse health effects,Reference Dhaka, Gulia, Ahlawat and Khatkar8 but recently, new chemistry has revealed that the formation of trans fats could be avoided by carefully manipulating the selectivity of the catalysts.Reference Lee, Delbecq, Morales, Albiter and Zaera9 It is expected that such selective catalytic hydrogenation processes will be further developed in the future and could help to lower the pernicious effects of saturated fats.Reference Philippaerts, Jacobs and Sels10
At the moment, for all of the mentioned applications, most of the hydrogen is obtained through steam reforming of fossil fuels. In steam reforming, hydrocarbons are converted to carbon monoxide (CO) and H2, commonly known as synthesis gas or syngas, using steam at high temperature (700–1000 °C). Reference Demirbas11

However, if hydrogen is to become the fuel of the future, extensive development in advanced technologies for the production of green hydrogen and enabling energy policies are essential to shift our dependence from fossil fuels toward renewables and sustainable hydrogen.
Technologies for renewable hydrogen production
Hydrogen is often described as a clean and sustainable energy vector but in order to live up to this description, renewable methods using sustainable sources need to be the backbone of hydrogen production.Reference Hosseini and Wahid12 In this section, renewable methods to produce H2 from water and biomass, along with their associated costs – in USD across the manuscript (Fig. 3), are reviewed in comparison to the production cost of hydrogen from steam methane reforming (1.9–2.6 $/kg H2) and the 2020 U.S. Department of Energy (DOE) target (2 $/kg H2).Reference Lemus and Martínez Duart13,Reference Kayfeci, Keçebaş, Bayat, Calise, D'Accadia, Santarelli, Lanzini and Ferrero14

Figure 3. Average hydrogen production cost from various methods. The black dotted line represents the 2020 DOE target of 2 $/kg H2.
For a more in-depth analysis, El-Emam and Ozcan published a comprehensive review on the technological, economic, and environmental aspects of renewable hydrogen production.Reference El-Emam and Özcan15
Making hydrogen from biomass
Biomass currently covers 14% of the total primary energy consumptionReference Granados-Fernández, Cortés-Reyes, Poggio-Fraccari, Herrera, Larrubia and Alemany16 due to its abundance and ease of accessibility across many countries.Reference Resasco, Wang and Sabatini17 Nowadays, as a CO2 neutral precursor, biomass is considered as an important renewable resource for hydrogen production,Reference Navarro, Sanchez-Sanchez, Alvarez-Galvan, del Valle and Fierro18 although the carbon foot print associated with the use of biomass for hydrogen production may not be neutral. For example, 8.99 × 10−2 CO2 eqv. g/s is emitted to produce 0.484 MJ/s H2 from an annual consumption of 2.53 × 106 kg of biomass.Reference Kalinci, Hepbasli and Dincer19 The use of biomass for energy production is often a great concern with respect to land use. However, alternatives likes lignocellulosic waste and crops waste have the potential to address this issue to some extent.Reference Arregi, Amutio, Lopez, Bilbao and Olazar20 Other types of “low cost” biomass to produce hydrogen include bio-waste, biogas, industrial organic waste, sewage sludge, bio-oil, and biochar;Reference Dou, Zhang, Song, Zhao, Jiang, He, Ruan, Chen and Xu21–Reference Zheng, Ying, Wang and Chen23 and the usual hydrogen content in biomass is ~5–7 wt%.Reference Pandey, Prajapati and Sheth24
Currently, the two main routes to produce hydrogen from biomass are through the thermochemical and biochemical process (Fig. 4).Reference Formica, Frigo and Gabbrielli25,Reference Cao, Yu, Xiong, Tsang, Zhang, Clark, Hu, Ng, Shang and Ok26 Thermochemical processes include pyrolysis, gasification, steam reforming, and supercritical gasification,Reference Dou, Zhang, Song, Zhao, Jiang, He, Ruan, Chen and Xu21 whereas biochemical processes include bio-photolysis, bio-fermentation, and dark fermentation.Reference Mahidhara, Burrow, Sasikala and Ramana27 In the biochemical route, biomass can be converted into biofuels through various processes including anaerobic or aerobic digestion, fermentation, and acid hydrolysis.Reference Hallenbeck and Benemann28 Recently, emerging technologies like bio-electrochemical systems have also been used to convert waste treatment into energy production. In this method, electrochemically active micro-organisms (e.g., Shewanella oneidensis and Geobacter sulfurreducens) are grown under electrochemical interactions with electrodesReference Hirose, Kasai, Aoki, Umemura, Watanabe and Kouzuma29,Reference Hirose, Kasai, Koga, Suzuki, Kouzuma and Watanabe30 to catalyze and oxidize organic matter to generate CO2, electrons, and protons.Reference Hirose, Kasai, Koga, Suzuki, Kouzuma and Watanabe30 The electrons are transferred to the anode, while the protons move through a membrane to the cathode, where they combine to release H2.Reference Kadier, Simayi, Abdeshahian, Azman, Chandrasekhar and Kalil31 An example of such system produced ~4.5 l H2/day from waste water.Reference Baeza, Martínez-Miró, Guerrero, Ruiz and Guisasola32

Figure 4. Hydrogen production by different methods from various types of biomass.
Apart from bio-electrochemical systems, hydrogen production from biomass can be light-driven. Light-dependent processes include bio-photolysis and photofermentation. In bio-photolysis, water is split to produce hydrogen by some green algae under anaerobic conditions. Photofermentation is done by using a purple non-sulfur bacteria converting organic acids into H2 and CO2. In light-independent processes, i.e., dark fermentation, organic substrates are converted to H2 in anaerobic condition (Table 1).Reference Sun, He, Yang, Sun and Sage33 With a cost of hydrogen production ranging from 1.4 to 2.8 $/kg H2, biological routes to process biomass are promising but are currently at a very early experimental stage.
Table 1. Biological processes to produce hydrogen from biomass.

Relative to biological routes, thermochemical methods are more flexible and provide a simpler approach as there is no need for additional chemicals but instead heat and pressure are used to generate biofuels.Reference Saghir, Rehan, Nizami and Yun43 This can be done by pyrolysis and/or gasification (Table 2).Reference Gai, Guo, Liu, Peng and Liu44,Reference Shahbaz, Yusup, Inayat, Patrick and Ammar45 Gasification is a well-developed process where hydrogen-rich fuel gas (CO, H2, and CH4) is produced at 700–1200 °C using gasification agents (O2, CO2, steam, and air).Reference Granados-Fernández, Cortés-Reyes, Poggio-Fraccari, Herrera, Larrubia and Alemany16,Reference Arregi, Amutio, Lopez, Bilbao and Olazar20 Gasification with air produces a low-quality gas (4–7 MJ/m3 HHV), whereas higher quality gas (~10–18 MJ/m3 HHV) can be obtained under more oxidative conditions, i.e., pure O2.Reference Schuster, Löffler, Weigl and Hofbauer50 The gasification process using fluidized bed reactors have demonstrated high biomass conversion with H2 content in gas ~55 vol.% and H2 production of ~6.9 wt%.Reference Arregi, Amutio, Lopez, Bilbao and Olazar20,Reference Gil, Corella, Aznar and Caballero51 The cost of H2 production by gasification from biomass is estimated to be ~1.77–2.05 $/kg H2,Reference Kayfeci, Keçebaş, Bayat, Calise, D'Accadia, Santarelli, Lanzini and Ferrero14 and the process can be generalized in the following equation:Reference Balat52

Table 2. Hydrogen production strategies from pyrolysis and the gasification process.

H2 can also be obtained via the pyrolysis of biomass at lower temperatures of 300–650 °C,Reference Arregi, Amutio, Lopez, Bilbao and Olazar20,Reference Balat52,Reference Anca-Couce53 but, at such temperatures, the hydrogen yield is lowered and of ~18 vol%.Reference Balat52 However, with suitable catalysts, e.g., Ni/Al2O3,Reference Arregi, Amutio, Lopez, Bilbao and Olazar20 and elevated temperatures, the amount of produced H2 can be increased to yields ~38 vol% at 600 °C and ~70 vol% at 900 °C. Recently, an effective two-staged pyrolysis process has been proposed,Reference Duman and Yanik54 where the biomass is initially heated to 950 °C to produce pyrolysis gases, and then further heated at 950 °C again. With a 10 wt % Ni-dolomite catalyst, the amount of hydrogen obtained in this two steps process was 59.14 vol%.Reference Waheed and Williams55 The cost of H2 production from biomass pyrolysis has been calculated as 1.25–2.20 $/kg H2,Reference Kayfeci, Keçebaş, Bayat, Calise, D'Accadia, Santarelli, Lanzini and Ferrero14 and the process is generalized in the following equation:Reference Balat52

Recently, other feedstocks like bioethanol, glycerol, sorbitol, and glucose have also been investigated as a potential source of hydrogenReference He, Yang, Chen and Gandia56 through the conventional approach of steam reformingReference Demirbas11:

In this approach, the hydrogen content in syngas varies according to the gasification operating conditions, i.e. temperature, steam-to-biomass ratio, and catalysts. Steam gasification is prone to the formation of tar, which may affect the maintenance and operation cost due to pipeline blockage.Reference Qiu, Du, Liu and Chen57 Therefore, catalysts are often used to promote tar cracking and reduce the operating temperature as well as increase the hydrogen selectivity from biomass.Reference Cao, Chen, Tsang, Luo, Hao, Zhang and Chen58 Some of the common catalysts are alkaline earth catalysts (e.g., KOH, KHCO3, Na3PO4, MgO, and NaOH),Reference Cao, Yu, Xiong, Tsang, Zhang, Clark, Hu, Ng, Shang and Ok26,Reference Ebadi, Hisoriev, Zarnegar and Ahmadi59 metal-based catalysts (e.g., Ni/Al2O3. Ni/Al, Ni/Zn/Al, Cu/Zn/Zr, Rh/Zr/Ce, Pt/Co/CeO2, and Ru/SrO-Al2O3),Reference Bobadilla, Álvarez, Domínguez, Romero-Sarria, Centeno, Montes and Odriozola60–Reference Iida, Noguchi, Numa, Igarashi and Okumura67 and mineral catalysts (dolomite and olivine).Reference Basu and Pradhan68,Reference Ma, Zhao, Gu and Shi69 The activity of the metal-based catalysts supported on Al2O3–MgO is in an order of Ru > Rh > Ir > Ni > Pt.Reference Wu, La Parola, Pantaleo, Puleo, Venezia and Liotta70 Although the noble metals such as Ru and Rh can effectively promote gasification, these remain expensive. Traditional alkali metal catalysts have also been used effectively; however, challenges remain due to the high loading, easy scaling, blockage, and difficult recovery. As a result, Ni-based catalysts have been widely used especially due to their synergy with other metals.
For example, 100% carbon conversion and ~70 vol% H2 yield have been reported with a Pt–Ni/CeO2–SiO2 catalyst.Reference Palma, Ruocco, Meloni and Ricca71 With an estimated cost of H2 production up to ~5.5 $/kg H2,Reference Marcoberardino, Vitali, Spinelli, Binotti and Manzolini72 more scientific advancement is needed before biomass gasification technologies can be used at an industrial scale. The future efforts are expected to be on tar treatment, cost-effective catalysts, condition optimization, and large-scale implementation.
Making hydrogen by splitting water
Even though water is an abundant hydrogen source, water electrolysis accounts for only a small fraction of the global hydrogen production.Reference Ewan and Allen73 Depending on the energy source used, water electrolysis can be a completely sustainable and a clean way to generate hydrogen since no greenhouse gas is emitted.Reference Chi and Yu74 Hydrogen production from water splitting can be done by using various methods including electrolysis and photocatalysis.Reference Safari and Dincer75 However, the latter is far from mature. During the photocatalysis process, a light excited semiconducting electrode with a suitable excitation bandgap, e.g., TiO2, is used to split water into hydrogen and oxygen.Reference Colón76 Unfortunately, TiO2 strongly absorbs light in the UV spectrum (λ < 350 nm) only, and not in the visible light range (350 nm < λ < 700 nm), and this results in a poor photocatalytic activity under sunlight. The development of high-performing photocatalysts under sunlight is therefore critical for photocatalysis to become a key method to produce H2.Reference Ismail and Bahnemann77 To date, many semiconductor photocatalysts and co-catalysts have been studied including doped TiO2,Reference Samokhvalov78 perovskites,Reference Castelli, Landis, Thygesen, Dahl, Chorkendorff, Jaramillo and Jacobsen79 graphitic C3N4,Reference Cao and Yu80 BiVO4,Reference Li, Han, Zhang, Wang and Li81 and NiS.Reference Ran, Zhang, Yu and Qiao82 Although this approach is reported to have less environmental impact, the poor efficiency (10–18%)Reference Young, Steiner, Döscher, France, Turner and Deutsch83 and relative high cost are not attractive.Reference Miller84 Early estimation would suggest a hydrogen production cost between 1.6 and 10.4 $/kg H2.Reference Pinaud, Benck, Seitz, Forman, Chen, Deutsch, James, Baum, Baum, Ardo, Wang, Miller and Jaramillo85
Exotic methods including sonolysis, where a sound wave between 20 and 40 kHz is used to split water through cavitation effects, have been reported.Reference Rashwan, Dincer, Mohany and Pollet86 Thermochemical water splitting from solar concentrators (>2000 °C) have also been proposed with relatively high efficiency (49% solar-to-fuel energy conversion efficiency).Reference Bhosale, Kumar and Sutar87 Depending on the type of thermochemical cycles used (where heat sources and chemical reactions are combined to split water into hydrogen and oxygen),Reference Safari and Dincer75 the cost of H2 production varies considerably from 2.8–4.1 $/kg H2 for the hybrid sulfur cycle,Reference Graf, Monnerie, Roeb, Schmitz and Sattler88 to 8.0–14.7 $/kg H2 for the ZnO/Zn cycle,Reference Charvin, Stéphane, Florent and Gilles89 and 2.2 $/kg H2 for the Cu-Cl cycle.Reference Safari and Dincer75
Electrolysis is a general term describing the process of driving a non-spontaneous electrochemical reaction by applying a voltage difference between two electrodes. In water electrolysis, gaseous hydrogen and oxygen are generated from water in the following equation:

This is an energy-demanding reaction with a change in Gibbs free energy of 237.2 kJ/mol at standard conditions.Reference Millet, Mbemba, Grigoriev, Fateev, Aukauloo and Etiévant90,Reference Selamet, Becerikli, Mat and Kaplan91 If this reaction is done in an electrochemical cell, a potential difference of 1.23 V is required at room temperature and standard pressure.Reference Yin, Wang, Zhang, Shangguan and Qin92 Various electrochemical cell configurations and chemistry have been investigated to generate hydrogen through water electrolysis. These technologies are at various stages of maturity and include the proton exchange membrane (PEM),Reference Carmo, Fritz, Mergel and Stolten93,Reference Grigoriev, Porembsky and Fateev94 alkaline water (AW),Reference Phillips and Dunnill95,Reference Rashid, Al Mesfer, Naseem and Danish96 anion exchange membrane (AEM),Reference Leng, Chen, Mendoza, Tighe, Hickner and Wang97,Reference Pavel, Cecconi, Emiliani, Santiccioli, Scaffidi, Catanorchi and Comotti98 solid oxide electrolysis (SOE),Reference Moçoteguy and Brisse99 and microbial electrolysis cell (MEC)Reference Kadier, Kalil, Abdeshahian, Chandrasekhar, Mohamed, Azman, Logroño, Simayi and Hamid100 technologies.
Table 3 summarizes the characteristics of these different approaches, and to date, AW electrolysis remains the most cost effective approach to generate hydrogen.Reference Bose, Karuppasamy, Rajan, Velusamy, Kim and Alfantazi104–Reference He, Feng, Liao, Hu, Wu and Sun106 PEM systems lead to the highest H2 purity but unfortunately suffer from several limitations such as electrolyte contamination,Reference Siracusano, Van Dijk, Backhouse, Merlo, Baglio and Aricò107,Reference Frensch, Fouda-Onana, Serre, Thoby, Araya and Kær108 and deterioration,Reference Ferriday and Middleton109 and slow oxygen evolution reaction (OER) kinetics.Reference García-Osorio, Jaimes, Vazquez-Arenas, Lara and Alvarez-Ramirez110 To speed up the OER kinetics, various catalysts have been tested including Pt on carbon, ruthenium-based materials,Reference Yu, He, Yang, Zhou, Shao and Ni111 and non-noble metal catalystsReference Wang, Song, Zhang, Yan and Guo112
Table 3. Materials, components, and characteristics of different electrolysis systems.

PAMa: polysulphone-bonded polyantimonic acid; PPS: ZrO2 on polyphenylsulphone; Sb2O5-PS: polysulphone impregnated with Sb2O5 polyoxide;PFSA: perflurosulfonated acid; QAPS: quaternary ammonia polysulfone; OER: oxygen evolution reaction; HER: hydrogen evolution reaction; NA: not available.
The price and source of electricity to power the electrolysis reaction are additional factors to consider. Several projects have demonstrated the technological viability of renewable hydrogen from wind and solar. However, advancements in direct and more efficient water electrolysis processes from renewable sources are needed to reduce cost and facilitate the uptake of renewable hydrogen.Reference Pareek, Dom, Gupta, Chandran, Adepu and Borse113
Over the past decades, there has been a rapid increase in installed capacity of wind energy coupled with a decrease in the associated costs.Reference Weigt114 It is therefore of little surprise that researchers around the planet are looking into the utilization of wind energy to produce hydrogen.Reference Greiner, Korpas and Holen115–Reference Nadaleti, Borges dos Santos and Lourenço118 The calculated costs involved with H2 production from wind energy vary widely based on several factors including if the wind-mills are grid-connected or isolated systems, the type of electrolysers used, and wind penetration scenarios.Reference Jørgensen and Ropenus119 For example, a Norwegian study calculated prices between 2.0 and 4.5 $/kg H2,Reference Greiner, Korpas and Holen115 a Danish study predicted a price of around 3.5 $/kg H2,Reference Jørgensen and Ropenus119 whereas a South African study listed values between 1.4 and 39.5 $/kg H2.Reference Ayodele and Munda116 The annual hydrogen production volume also varies considerably based on the country's available wind energy capacity and the mean wind speed. In Fayzabad, Afghanistan, a 100 kW wind turbine system could produce up to 8.7 × 106 kg H2/year,Reference Rezaei, Naghdi-Khozani and Jafari117 in South Africa, between 6.5 × 103 and 2.3 × 105 kg H2/year could be generated,Reference Ayodele and Munda116 while in Brazil the projected hydrogen production from the surplus wind electricity was predicted to be of 2.2 × 1011 kg H2/year.Reference Nadaleti, Borges dos Santos and Lourenço118
Producing hydrogen from photovoltaics (PV) was once the most expensive method (up to 78.6 $/kg H2) due to the high cost of the PV system.Reference Mueller-Langer, Tzimas, Kaltschmitt and Peteves120 However, installed solar capacity has increased drastically due to the recent sharp drop in price of solar PV systems.Reference Bazilian, Onyeji, Liebreich, MacGill, Chase, Shah, Gielen, Arent, Landfear and Zhengrong121 To date, solar is the most cost-competitive way to produce clean renewable hydrogen.Reference Lagorse, Simões, Miraoui and Costerg122 In 2007, a study calculated that a PV electrolysis plant of 260 km2 would be enough to provide an annual H2 production of 2.2 × 108 kg at a cost of 6.5 $/kg H2,Reference Mason and Zweibel123 and since then, the cost of solar hydrogen has fallen to less than 3 $/kg H2.Reference Kikuchi, Ichikawa, Sugiyama and Koyama124 Solar hydrogen production capacity and the cost of course depend on multiple factors including the country and location (solar irradiation level), the type of electrolysers, and the nature of the PV systems, i.e., grid-connected or autonomous.Reference Lagorse, Simões, Miraoui and Costerg122 For example, it has been predicted that a 20 kW PV system receiving 299 MW/h of solar radiation would produce 3.73 × 105 kg H2/year,Reference Fereidooni, Mostafaeipour, Kalantar and Goudarzi125 while a Japanese study projected a low production cost of 1.7–2.8 $/kg using a PV and battery-assisted electrolysers.Reference Kikuchi, Ichikawa, Sugiyama and Koyama124 As compared with solar, wind energy has the advantage of being a “dual-use” technology where the land can still be used for other important activities such as farming and agriculture, or even solar farms. Hybrid wind–solar systems could be one solution in order to maximize the use of land and minimize the problem of intermittent solar irradiation.Reference Al-Sharafi, Sahin, Ayar and Yilbas126–Reference Dagdougui, Ouammi and Sacile128 Floating systems could also provide alternatives to produce hydrogen while minimizing land impact.Reference Temiz and Javani129
Alternatives including hydropower and geothermal may also have the potential to be used to produce hydrogen. Hydropower is often considered expensive due to the upfront capital cost of building huge dams. However, a Canadian study found that despite the initial capital costs, hydropower H2 production is cost competitive as compared with steam methane reforming at 2.4 $/kg H2, and if the upfront investments are excluded (by using existing hydropower plants), the hydrogen cost goes down to 1.2 $/kg H2.Reference Olateju and Kumar130 Geothermal energy is another source of sustainable energy, and a recent study demonstrated that geothermal powered electrolysis is a viable method for hydrogen production (1.1 $/kg H2) with a payback period of only 4–5 years.Reference Yilmaz, Koyuncu, Alcin and Tuna131
Storage and distribution of hydrogen
Effective methods to store hydrogen are essential to enable its widespread utilization in particular for industrial use where plants require a constant feedstock input. The main problem with storing hydrogen is its low volumetric density. Hydrogen is the lightest element, and at ambient condition, it is a gas with a low density of 0.0899 kg/m3.Reference Hsu, Chang, Tseng, Chan, Chao, Wu, Wen, Hsieh, Wang and Chen132 Even when liquefied at −253 °C, the density of H2 is only 70.8 kg/m3, which is one-fifteenth of water's density. Hydrogen is also a very small highly diffusive molecule and thus hydrogen leaks can easily occur.Reference Sherif, Barbir and Veziroglu133 Besides, the use of hydrogen is associated with difficulties in terms of materials’ compatibility. In particular, the dissociation of hydrogen molecules at the surface of metals and further hydrogen diffusion at metallic interstitial sites can lead to piping embrittlement and accidental fracture as a result of the reduced ductility and weakening of metals subjected to high purity/pressure hydrogen.Reference Louthan134–Reference Zheng, Liu, Xu, Liu, Zhao and Yang136 The storage of hydrogen is also more delicate than other fuels, because hydrogen has higher laminar burning, buoyant, and propagation velocities that results in higher flammability than other fuels. In addition, hydrogen is also very sensitive to detonation due to its wide volume fraction range of ignition (4–74%) and detonation (18–59%).Reference Alazemi and Andrews137–Reference Mazloomi and Gomes140
Existing methods to store hydrogen are summarized in Fig. 5. Storing hydrogen in high pressure vessels (up to 700 bar in lightweight composite cylinder) is the most common method so far, but the resulting low volumetric storage density, high cost of the composite vessels (~$13/KWh for 100,000 vessels per year),Reference Villalonga, Nony, Magnier, Yvernes, Thomas, Delmas and Mazabraud141 and their maintenance/safety are still a concern.Reference Mazloomi and Gomes140 Cryogenic tanks are designed to store liquid hydrogen at −253 °C under ambient pressure (the pressure can increase to 104 bar in a closed storage system due to the low critical temperature (−239.95 °C) of hydrogen).Reference Züttel142 As a general observation and depending on the vessel design, conventional cryogenic tanks can store twice more hydrogen per volume as compared to 700 bar hydrogen gas tanks.Reference Züttel142 However, with such a storage technology, it is inevitable to avoid the loss of hydrogen even with a perfect insulation because of heat leakage.Reference Bossel143,Reference Zhou144 The boiling losses of 0.4% per day for a 50 m3 double-walled vacuum-insulated spherical Dewar vessel have been reported.Reference Züttel145 In addition, hydrogen liquefaction is a very energy intensive process with at least 30% of the energy stored lost through the liquefaction of hydrogen.Reference Li, Chen, Zhang, Tan and Ding146

Figure 5. Hydrogen storage methods with their respective volumetric densities.
Hydrogen can also be stored by materials physically or chemically. This includes microporous materials, interstitial metal hydrides, and complex hydrides. Microporous materials, including carbon materials,Reference Schlapbach and Zuttel147–Reference Mohan, Sharma, Kumar and Gayathri152 zeolites,Reference Weitkamp, Fritz and Ernst153–Reference Xu, Liu, Li, Wang, Xu, Chen and Wang158 and metal organic frameworks (MOFs),Reference Suh, Park, Prasad and Lim159–Reference Bobbitt and Snurr163 can absorb molecular hydrogen in their porous structures at low temperature.Reference Mohan, Sharma, Kumar and Gayathri152,Reference Lim, Kazemian, Yaakob and Daud164,Reference Ramimoghadam, Gray and Webb165 The hydrogen storage capacity then depends upon the specific surface areas and the applied pressure.Reference Züttel142,Reference Mohan, Sharma, Kumar and Gayathri152 Typically, the adsorption capacity of MOFs is <2 wt% at room temperature.Reference Lai, Sun, Wang, Modi, Cazorla, Demirci, Ares Fernandez, Leardini and Aguey-Zinsou166 The advantage of porous materials is that they allow for hydrogen storage at higher temperatures, e.g., −150 °C, than feasible with cryogenic tanks for the similar volumetric hydrogen densities.Reference Bossel143
An alternative method to store hydrogen is in the use of materials storing hydrogen within their structure to form a hydride. Metal hydrides are usually formed by the reaction between metals or intermetallic compounds with hydrogen by the reversible reaction belowReference Zhang, Zhao, Niu and Maddy167:

where M is either a metal, an alloy, or an intermetallic compound, MH is the metal hydride formed, and Q is the heat generated during the reaction.Reference Zhang, Zhao, Niu and Maddy167
Interstitial metal hydrides are capable of absorbing large amounts of hydrogen (i.e., the volumetric density of LaNi5 is 123 kg H2/m3 of material; that is 1.74 times more than that of liquid hydrogen). In this process, hydrogen is stored in an atomic form after dissociation of molecular hydrogen at the surface of the interstitial metal.Reference Schlapbach and Zuttel147
Generally, existing binary hydrides along the periodic table of elements are too unstable or too stable to be relevant for practical application. However, it has been found that intermetallic compounds, e.g., TiFe, ZrV2, and LaNi5,Reference Lai, Sun, Wang, Modi, Cazorla, Demirci, Ares Fernandez, Leardini and Aguey-Zinsou166,Reference Sujan, Pan, Li, Liang and Alam168,Reference Kumar, Kojima and Dey169 formed by alloying at least two elements (one unstable with one stable hydride) can facilitate the hydrogen storage properties. Generally, the element forming a stable hydride are transition metals or rare earths like Ti, Zr, Y, and La. The unstable hydride elements (often absorbing hydrogen at high hydrogen pressure only) are transition metals including Cr, Mn, Fe, Co, and Ni. The formation of intermetallic alloyed by these two elements can lead to intermediate hydrogen sorption properties with reversibility. Interstitial metal hydrides show excellent and practical hydrogen storage properties since they can uptake and release a large amount of hydrogen safely at ambient temperature and moderate hydrogen pressures.Reference Broom170 However, one of the major limitations of these interstitial hydrides is their weight, because their composition involves heavy elements, and this results in low gravimetric hydrogen storage capacities.
Better hydrogen storage materials, i.e., of higher gravimetric storage capacities, may exist in the form of complex hydrides. Complex hydrides are ionic compounds that release hydrogen when they decompose.Reference Broom170 Complex hydrides are usually formed through the combination of alkali or alkaline earth metals, e.g., Li, Na and Mg, and [AlH4]−, [NH2]−, and [BH4]− groups. The theoretical gravimetric and volumetric densities of some of the complex hydrides are high, for example, the theoretical gravimetric capacity of LiBH4 is 18.5% and the volumetric capacity is 121 kg H2/m3 (70% more than the volumetric capacity of liquid hydrogen).Reference Dalebrook, Gan, Grasemann, Moret and Laurenczy171–Reference Benzidi, Lakhal, Abdellaoui, Garara, Benyoussef, Loulidi, Hamedoun and Mounkachi173 However, the multiple steps of hydrogen desorption, the release of impurities in the form of B2H6 from borohydrides or NH3 from amides, and the poor hydrogen reversibility of these materials remain the main barrier for their practical applications. The poor reversibility is generally due to the formation of stable intermediate decomposition products during decomposition and extensive elemental disproportion.Reference Lai, Sun, Wang, Modi, Cazorla, Demirci, Ares Fernandez, Leardini and Aguey-Zinsou166 Different strategies including those based on the potential to alter the properties of hydrogen in nano-hydride materials are under current investigations to tackle these challenges.Reference Lai, Sun, Wang, Modi, Cazorla, Demirci, Ares Fernandez, Leardini and Aguey-Zinsou166
Currently, hydrogen is delivered from production sites to the end-users including refueling stations by road or pipeline depending on the application, volume, and distance.Reference Sinigaglia, Lewiski, Martins and Siluk174 For small volumes, transport by road remains the most favorable option. In this case, hydrogen is compressed to 180–200 bar and delivered by tube trailers. Delivering liquid hydrogen is more economical over long distances due to the higher volumetric density. A 40 ton truck can carry 350 kg of gaseous hydrogen or 3500 kg liquid hydrogen,Reference Bossel143 and the delivery cost of compressed hydrogen gas is $1/kg/100 km by tube trailers and $0.1/kg/100 km for liquid hydrogen by trucks in the USA.Reference Li, Allen, Stager and Ku175 Hydrogen is also noncorrosive; therefore, this facilitates the design and construction of tank trailers. However, because of the extreme low temperature, additional space for safety and suitable thermal insulation must be considered.Reference Dagdougui, Sacile, Bersani and Ouammi138,Reference Bossel143
Gaseous hydrogen can also be transported in pipelines like natural gas, especially when large volumes are to be transported over long distances. In this case, the cost of hydrogen transport is estimated to be of $0.1/kg H2 over 100 km.Reference Dagdougui, Sacile, Bersani and Ouammi138 However, this does not take into account the need to retrofit exiting gas network. Conventional pipelines for natural gas are made of steel with a typical diameter of 25–30 cm and the operation pressure is 10–20 bar.Reference Züttel142 Using such an infrastructure to transport hydrogen is not feasible in many cases without substantial modifications to reduce diffusion losses in sealing areas as well as materials and seals embrittlement.Reference Bossel143 In addition, the minimum power required to pump a gas through the pipe follows the equation below:

where l is the length of the pipe, and υ and η are the velocity and dynamic viscosity of the gas. The volumetric density of hydrogen is 36% of the density of natural gas at the same pressure, and the viscosity of hydrogen is 80% of that of natural gas. Therefore, to pump the same amount of hydrogen, the power needed is 2.2 times that for natural gas.Reference Züttel142
The role of enabling policies
Today, hydrogen is mainly used for the production of ammonia and hydrocracking processes, with only a small portion used in the transport sector including in the nascent fleet of fuel cell vehicles. Uncertainties in technological development and price advantage of fossil fuel present a major challenge for the growth of renewable hydrogen at the industrial scale. Industry faces national and international competitive pressures, and existing economic models are highly sensitive to feedstock prices. Projections from the International Partnership for the Hydrogen Economy (IPHE) assume that hydrogen will continue to be produced from cheaper fossil fuels before renewable hydrogen can play a significant role. However, continuing declining prices of wind turbines,Reference Wiser, Jenni, Seel, Baker, Hand, Lantz and Smith176 solar PV,Reference Comello, Reichelstein and Sahoo177 and electrolysersReference Felgenhauer and Hamacher178 suggests that the production of hydrogen via power-to-gas (PtG) may become economically favorable in the next decade.Reference Glenk and Reichelstein179 For example, case studies have found that renewable hydrogen is already cost competitive in small- and medium-scaled applications combining renewable wind energy with a PtG facility.Reference Glenk and Reichelstein179 In this transition, it is often envisaged that carbon capture and storage may assist the production of low-carbon emission hydrogen from natural gas and coal, although currently not competitive.180 Solutions still remain to be found to effectively capture and store carbon dioxide, without mentioning the social licence aspects of such a solution.180
Additionally, non-economic barriers hindering the deployment of hydrogen technologies and infrastructures have also been identified.Reference Garcia181 This includes (i) complex procedures and lack of information and assistance to enable projects, (ii) lack of public knowledge and awareness of the renewable hydrogen, (iii) social acceptance of the safety of hydrogen-related technologies and infrastructures, and (iv) lack of government initiatives to facilitate the use of hydrogen technologies and infrastructure construction. Existing safety regulations along hydrogen production, distribution, and storage are also limiting factors.Reference Dolci, Thomas, Hilliard, Guerra, Hancke, Ito, Jegoux, Kreeft, Leaver, Newborough, Proost, Robinius, Weidner, Mansilla and Lucchese182
In recent years, many countries have announced ambitious initiatives and visions to utilize renewable hydrogen as an energy carrier and achieve the greenhouse gas emission targets following the Paris Agreement in November 2016.Reference Rogelj, Den Elzen, Höhne, Fransen, Fekete, Winkler, Schaeffer, Sha, Riahi and Meinshausen183 However, implementation toward an hydrogen economy is still distant and in the light of the COVID-19 pandemic lobbying toward business as usual is more than ever prevalent. Currently, there are more than 19 hydrogen strategies and roadmaps around the world.Reference Kosturjak, Dey, Young and Whetton184 However, many countries aim to focus on hydrogen use across the transport sector and existing gas distribution and transmission networks, with little understanding of the potential of hydrogen in the industrial sector. The EU, France, and Norway in contrast have identified hydrogen as an industrial feedstock, and aims to focus their strategy in this area,Reference Kosturjak, Dey, Young and Whetton184 while the transport sector is to remain mainly battery-driven.
Policy and pilot projects that could enable the use of renewable hydrogen in industry are still lacking because of the relativity high cost of renewable hydrogen (approximately 5.30 $/kg H2).Reference Mohsin, Rasheed and Saidur185 Only a few countries offer subsidies, tax incentives, and rebates for investments in renewable hydrogen production. For example, in Norway, electricity used to electrolyse water for hydrogen production is tax exempt, and in the Netherlands, a subsidy of up to €750,000 supports hydrogen-related projects.Reference Dolci, Thomas, Hilliard, Guerra, Hancke, Ito, Jegoux, Kreeft, Leaver, Newborough, Proost, Robinius, Weidner, Mansilla and Lucchese182
Many of the current demonstration and commercialization projects along renewable hydrogen plants are initiated by industry only, with the private sector expected to invest more than $50 billion in hydrogen projects by 2030. For example, Shell and ITM Power planned to install a 10 MW electrolyser in its refining industry site in Germany in 2017. In many countries like the USA, Japan, and China, primary hydrogen investments remain toward the deployment of fuel cell vehicles and hydrogen refuelling stations. While the heavy industry sector is the largest consumer of hydrogen, this sector is more closely bound to emission reduction regulations, renewable energy mandates, and carbon markets, compared with other light industries.186
Currently, there is no standard for low-carbon hydrogen, and green hydrogen is not recognized as a renewable fuel in many countries and thus not accountable toward the renewable target set in the mobility sector. It is therefore essential for organizations and policymakers to develop appropriate national and international standards, regulations, and relevant hydrogen certifications. This will allow renewable hydrogen to be supported by climate policies, in the same way as renewable technologies. The system “CertifHy” proposed in Europe to evaluate the environmental value of hydrogen could be a starting model to trade certified hydrogen. In this system, CO2 emission levels (91 g CO2/MJ H2) of hydrogen produced from reforming natural gas are used as a reference point. Hydrogen produced with a 60% reduction from this level (i.e., 36.4 g CO2/MJ H2) is defined as “Premium Hydrogen,” while Premium hydrogen produced from renewable energy is defined as “Green Hydrogen.”Reference Abad and Dodds187
Government policies need to be designed as a long-term and fair competition platform for the hydrogen sector, introducing both incentives and regulations. When designing regulations relating to greenhouse gases reduction for industry, it is essential to acknowledge the significance and feasibility of clean hydrogen. It is conceivable to make use of a certain percentage of clean hydrogen in industrial processes mandatory with targeted reductions in use of steam methane-reforming hydrogen. Meanwhile, long-term high-risk mitigation implementations and incentives, such as the subsidy of a percentage of the high capital expenditure or compensation via products, could be effective in stimulating the large-scale production and supply of clean hydrogen. This can possibly reduce the cost of clean hydrogen for consumers, accelerating its mass deployment across industry.
Finally, public awareness and acceptance toward hydrogen are also important factors. It is apparent that many citizens are not educated on the potential of renewable hydrogen and its benefits for the environment.Reference Garcia181 Even though the social acceptance of new technologies is considerably high in many European countries, hydrogen is still considered dangerous due to its high flammability. It is therefore important to demonstrate and implement a production of hydrogen that is safe to gain an increase in public support.
Summary and perspectives
As a crucial reactant for the chemical industry, the demand for hydrogen has grown considerably and will continue to rise in the foreseeable future. However, with most of the industrial hydrogen being sourced from fossil fuels, it is imperative that we start looking into sustainable production methods for hydrogen to succeed as a clean chemical feedstock and an energy carrier. Currently, only a small fraction of hydrogen is produced from renewable sources due to slow technological advances, lack of mass scale manufacturing of hydrogen technologies, and thus a high cost of green hydrogen relative to fossil fuels, and the lack of environmental government policies promoting the use of clean hydrogen. A few emerging technologies look promising based on the 2020 DOE target and even appear cost competitive to steam methane reforming for hydrogen production. However, the calculated production costs often do not tell the whole story; for example, electrolysis via geothermal and hydropower has a low cost of 1.1–2.4 $/kg H2 but unfortunately their use is restricted by the geographic location of the energy source. Biochemically processed biomass also appears cost competitive at 1.4–2.8 $/kg H2, but as an emerging technology, its reliability and actual cost at an industrial scale still remains to be determined. So far, wind-powered water electrolysis appears to have the best chance to play a major role in renewable hydrogen production due to the maturity and decreasing cost of wind technology. Once produced, the last hurdle for hydrogen is its storage and transport due to the low density of the gas. Until new methods like solid-state storage become more established, conventional methods (compressed gas cylinders and liquefied hydrogen) will remain the norm to get hydrogen to its end applications. Advancements in technological processes, cost, and policies still need to be conjointly progressed before renewable hydrogen can become the mainstream.