Graphene possesses high electrical conductivity, mechanical flexibility, and chemical and thermal stability. It offers significant advantages for a wide range of applications, including flexible electronics, sensors, supercapacitors, and batteries. For low-cost and high-throughput manufacturing of graphene-based devices, liquid-phase printing technologies provide considerable advantages in efficiency and versatility compared to conventional microfabrication methods based on photolithography and etching. Solution-based graphene inks have begun to accelerate the development of this promising two-dimensional (2D) sp 2-bonded carbon nanomaterial for practical technologies.
Pristine graphene inks commonly employ polymer additives to maintain colloidal stability and controlled viscosity. A particularly versatile polymer additive is ethyl cellulose (EC), which concurrently acts as an exfoliation aid, dispersant, viscosity modifier, and binder in addition to facilitating charge transport between graphene flakes in percolating films following thermal or photonic annealing.Reference Secor and Hersam1 Using EC, high-yield exfoliation of graphene is achieved by ultrasonication or shear mixing of graphite in inexpensive, environmentally benign solvents such as ethanol.Reference Secor, Prabhumirashi, Puntambekar, Geier and Hersam2 This exfoliation process produces few-layer graphene flakes with typical thicknesses of 1–5 nm and lateral dimensions of 100–500 nm, which are suitable for high-resolution printing methods. In contrast to oxidative exfoliation methods, EC-based exfoliation produces pristine graphene from graphite without chemically intensive processing or intermediate graphene oxides, which implies a simplified process flow, well-defined structure and chemistry, and high electrical conductivity. Furthermore, the EC stabilizer enables the exfoliated pristine graphene to be readily dispersed in diverse organic solvents with high solid content, thereby allowing control over ink rheology for a range of patterning and coating methods.
Graphene/EC inks have been developed for several printing techniques by controlling solvents and solid loading (Figure 1a); several of these inks are now available from MilliporeSigma.3 Two graphene/EC inks have been specifically developed for inkjet printing, a versatile digital, noncontact printing method, including a standard ink that requires thermal curing at 250°C,Reference Secor, Prabhumirashi, Puntambekar, Geier and Hersam2 and one tailored for rapid photonic annealing for applications involving temperature-sensitive substrates.Reference Secor, Ahn, Gao, Lewis and Hersam4 Higher viscosity graphene/EC inks have also been designed for higher throughput gravure and screen-printing methods,Reference Secor, Lim, Zhang, Frisbie, Francis and Hersam5,Reference Hyun, Secor, Hersam, Frisbie and Francis6 which offer improved scalability for additive manufacturing. In addition, a graphene/EC ink has been formulated for common laboratory coating methods such as spin coating and spray coating, providing a straightforward pathway to conductive graphene films. Table I summarizes the breadth of ink properties and deposition methods that can be used with the graphene/EC system.3 The graphene/EC system supports ink viscosities spanning four orders of magnitude and solid loadings as high as 20 wt%, demonstrating its versatility. Pristine graphene/EC inks have also been utilized for emerging scalable additive manufacturing methods, including self-aligned capillarity-assisted lithography,Reference Hyun, Secor, Kim, Hersam, Francis and Frisbie7 selective dewetting-based transfer printing,Reference Song, Mahajan, Secor, Hersam, Francis and Frisbie8 and liquid bridge-mediated transfer printing.Reference Naik, Kim, Usluer, Arellano, Secor, Facchetti, Hersam, Briseno and Watkins9

Figure 1. Properties of graphene/ethyl cellulose (EC) inks. (a) Schematic showing an atomic force microscope image of graphene flakes, a photograph of a graphene/EC ink vial (inset), and a printed graphene pattern. Adapted with permission from Reference Secor, Ahn, Gao, Lewis and HersamReference 4. © 2015 Wiley-VCH. (b) Scanning electron microscope image of a printed graphene film. Adapted with permission from Reference Hyun, Secor, Hersam, Frisbie and FrancisReference 6. © 2014 Wiley-VCH. (c–d) Electrical response of graphene patterns to mechanical stresses, showing invariant electrical resistance following (c) repeated bending cycles and (d) during bending. Adapted with permission from Reference Secor, Prabhumirashi, Puntambekar, Geier and HersamReference 2. © 2013 American Chemical Society.
Table I. Summary of graphene/ethyl cellulose ink properties.

Following deposition, the graphene/EC pattern is thermally or photonically cured, which decomposes the EC into volatile products, and a sp 2-rich amorphous carbon residue that results in a dense, conductive graphene film (Figure 1b). Conventional thermal annealing at 250°C for 30 minutes yields a high conductivity of ∼2.5 × 104 S/m (resistivity of 4.0 × 10–3 Ω·cm) and excellent tolerance to bending stresses.Reference Secor, Prabhumirashi, Puntambekar, Geier and Hersam2 For applications using thermally sensitive substrates such as poly(ethylene terephthalate) and paper, rapid photonic annealing can also be used. Photonic annealing involves irradiation with a pulsed, high-intensity light source, such as a xenon flash lamp, locally heating the strongly absorbing graphene/EC patterns while mitigating thermal damage to the underlying substrate, resulting in comparable electrical performance with millisecond processing times.Reference Secor, Ahn, Gao, Lewis and Hersam4 Graphene films printed from these inks can repeatedly withstand high bending strains of 1%, corresponding to a radius of curvature of 2.5 mm on a 50-µm-thick plastic film (Figure 1c–d).
The superlative electrical and mechanical performance of graphene/EC inks has been exploited in numerous printed electronic applications. In many cases, printed graphene structures have been utilized for high-performance electrodes and interfacial contacts. Poly(3-hexylthiophene) thin-film transistors (TFTs) have been fabricated on plastic and paper substrates on which screen printable graphene/EC inks were used to fabricate graphene electrodes (Figure 2a).Reference Hyun, Secor, Hersam, Frisbie and Francis6,Reference Hyun, Secor, Rojas, Hersam, Francis and Frisbie10 The excellent mechanical durability of the printed graphene electrodes enables reliable TFT performance even after severe substrate deformation, including bending and folding. Indium-gallium-zinc-oxide TFTs have been demonstrated using inkjet printable graphene/EC inks for source and drain electrodes.Reference Secor, Smith, Marks and Hersam11 In this case, the chemically inert graphene electrodes provide robust TFT stability at processing temperatures in excess of 300°C in addition to long-term stability in ambient conditions for more than one year. Inkjet printable graphene/EC inks have also been used to fabricate an interfacial layer to stabilize electrical contacts between eutectic gallium-indium (eGaIn) and silver electrodes (Figure 2b).Reference Secor, Cook, Tabor and Hersam12 By serving as a physical barrier, the printed graphene layer between eGaIn and silver prevents alloy formation, yielding stable electrical contacts and improved materials compatibility for eGaIn-based reconfigurable electronic applications.
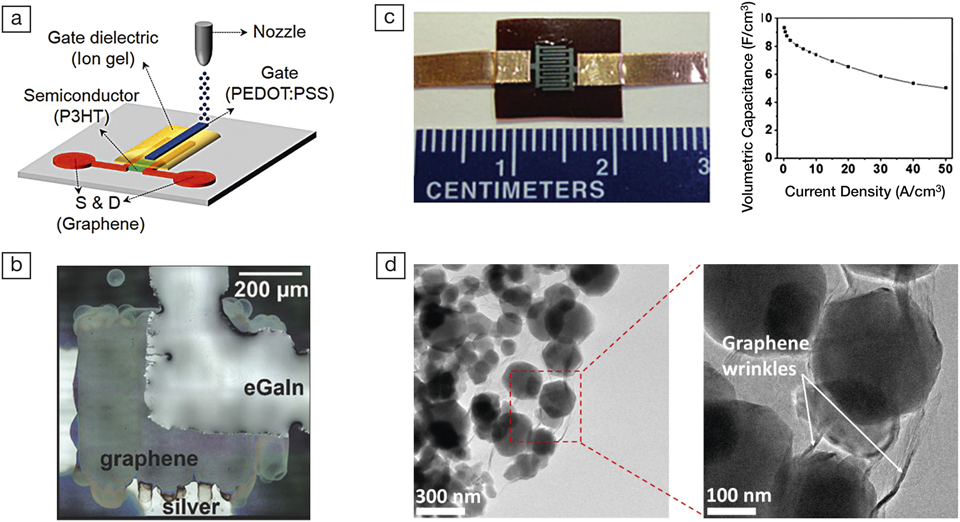
Figure 2. Applications of graphene/ethyl cellulose (EC) inks. (a) Schematic showing screen-printed graphene electrodes for organic thin-film transistors. Adapted with permission from Reference Hyun, Secor, Hersam, Frisbie and FrancisReference 6. © 2014 Wiley-VCH. (b) Optical microscope image of graphene as an interfacial barrier between eutectic gallium-indium (eGaIn) and silver. Adapted with permission from Reference Secor, Cook, Tabor and HersamReference 12. © 2017 Wiley-VCH. (c) Photograph of and capacitance-current density plot for inkjet-printed graphene microsupercapacitors. Adapted with permission from Reference Li, Secor, Chen, Zhu, Liu, Gao, Seo, Zhao and HersamReference 13. © 2016 Wiley-VCH. (d) Transmission electron microscope images of lithium manganese oxide nanoparticles coated with graphene/EC at different magnifications. Reprinted with permission from Reference Chen, Xu, Luu, Secor, Hamamoto, Li, Kim, Sangwan, Balla, Guiney, Seo, Yu, Liu, Wu, Wolverton, Dravid, Barnett, Lu, Amine and HersamReference 14. © 2017 American Chemical Society.
The high surface area and electrochemical stability of graphene also motivate applications of graphene/EC inks in energy-storage devices. Solid-state graphene microsupercapacitors have been fabricated using inkjet-printable graphene/EC inks (Figure 2c), resulting in high volumetric capacitance (9.3 F/cm3 at a current density of 0.25 A/cm3), promising energy and power densities (1.29 mWh/cm3 and 278 W/cm3, respectively), and excellent capacitance retention over 10,000 cycles.Reference Li, Secor, Chen, Zhu, Liu, Gao, Seo, Zhao and Hersam13 In addition, high performance, nanostructured lithium manganese oxide (nano-LMO) cathodes for lithium-ion batteries have been demonstrated using graphene/EC as a conductive additive.Reference Chen, Xu, Luu, Secor, Hamamoto, Li, Kim, Sangwan, Balla, Guiney, Seo, Yu, Liu, Wu, Wolverton, Dravid, Barnett, Lu, Amine and Hersam14 By conformally coating the surface of nano-LMO particles (Figure 2d), graphene/EC improves packing density and chemical stability. Due to enhanced charge transfer resulting from the highly conductive graphene coating, lithium-ion batteries employing these cathode materials possess extraordinary performance under extreme operating conditions, such as 75% capacity retention at a 20C cycling rate at room temperature and nearly full capacity retention at –20°C.
The excellent electrical, chemical, and mechanical properties of pristine graphene, coupled with EC to enhance colloidal stability, tailor viscosity, and facilitate processing, provide a favorable material system for accelerating research and device prototype development. The scalability of the graphene/EC ink production methodology in combination with the compatibility with diverse printing and coating methods provides opportunities for efficiently transitioning research developments to large-scale additive manufacturing. The likely extrapolation of the EC-based exfoliation and stabilization approach to other 2D materials (e.g., transition-metal dichalcogenides and hexagonal boron nitride) further suggests that this technology will enable a wide range of additional technologies in the future, including optoelectronics, sensors, radio-frequency identification antennas, and electromagnetic interference shielding.Reference Hu, Kang, Ng, Zhu, Howe, Jones, Hersam and Hasan15