Introduction
The use of industrial exoskeletons for various types of manual tasks such as manual handling, overhead work or welding has drastically increased in recent years (International Federation of Robotics/Statistical Department und VDMA/Robotik+Automation, 2017). The welding profession poses especially high physical stress due to constrained positions and the weight of the welding equipment (Shahriyari et al., Reference Shahriyari, Afshari and Latifi2020). This stress can lead to muscular fatigue, especially when working with elevated arms (Hamberg-van Reenen et al., Reference Hamberg-van Reenen, Ariëns, Blatter, van Mechelen and Bongers2007). Working with elevated arms over a prolonged period of time has been shown to result in a decrease of the quality of the weld seam (Butler and Wisner, Reference Butler and Wisner2017).
Several studies have shown the positive effect of industrial exoskeletons on perceived work effort, physical and biomechanical load as well as metabolic cost (Del Ferraro et al., Reference Del Ferraro, Falcone, Ranavolo and Molinaro2020; Bär et al., Reference Bär, Steinhilber, Rieger and Luger2021). Butler and Wisner (Reference Butler and Wisner2017) have shown in a first experiment that an exoskeleton increased the time a welder could work with acceptable outcome scores. This suggests that exoskeletons could possibly not only increase the endurance of the welder but overall increase the quality of the weld.
The EXOWORKATHLON study (Kopp et al., Reference Kopp, Holl, Schalk, Daub, Bances, Garcia, Siegert and Schneider2022) is a modular task set, which was created to assess different aspects of exoskeletons by means of different standardized parcours. The Exoworkathlon includes a welding parcours for exoskeleton assessment in manual welding under constrained body positions in front of the body and overhead. An assessment of welding quality, subdivided into five categories was conducted.
The aim of this study is to analyze whether exoskeletons which can reduce physical strain on the body subsequently can result in an increase of welding quality.
Material and Methods
Participants
A total of n = 15 subjects participated in the study. All subjects were young professional trainees with welding experience from AUDI AG in Neckarsulm, Ford-Werke GmbH in Cologne and Wilhelm-Maybach-Schule in Stuttgart. All subjects were healthy, had no contraindicating musculoskeletal or cardiological diseases and gave written informed consent to participate in the study. The average age was 23 years. Totally, 86.6% of the participants were male and 13.4% of the participants were female. Body mass index (BMI) averaged 27.7.
Ethical Approval
The ethics application with the protocol number “IFF-2021-08-01” was approved in August 2021 by the responsible commission “Kommission Verantwortung in der Forschung” of the University of Stuttgart.
Experimental Design
In order to ensure a safe experimental procedure, welding simulators “Soldamatic” from the company Seabery (Seabery Soluciones, Huelva, Spain) as well as grinding simulators designed by the main author were used. These simulators accurately mimic the task of welding a seam as well as work preparation and reworking the piece with an angle grinder under laboratory conditions. Standard DIN EN ISO 9606-1 for welding education served as the basis for the simulated workplaces, making it possible to define real processes under authentic framework conditions. DIN EN ISO 9606-1 (2017) describes and defines welding in constrained positions. Since it is the welding process with the highest industrial impact, the metal active gas (MAG) welding process was chosen for this study. The following welding positions for this experiment were defined in cooperation with SLV Nord, Hamburg:
-
• PF Position—vertical uphill (work piece located in front of the body, end position slightly below eye level; Figure 1)
-
• PE Position—overhead, back to front (work piece positioned above head, approximately 300 mm in front of the eyes; Figure 2)

Figure 1. Exemplary illustration of the Position PF during the welding sequence including first-person perspective of the subject.

Figure 2. Exemplary illustration of the Position PE during the grinding sequence.
Each subject welded a 250 mm seam in PF position followed by simulated grinding in this position. This procedure was repeated 10 times.
Directly following, each subject completed the same process in the PE position (10 times welding and grinding of the seam).
The total time for the workflow was approximately 1 hr.
Each study participant completed the defined workflow twice: once with an exoskeleton and once without an exoskeleton. The order of the two runs was randomized. A total of 53.33% of the participants started without exoskeletons, the other 46.66% with exoskeletons. The subjects were given at least 1 hr to rest in between the runs.
Equipment
Exoskeletons
Different passive industrial exoskeletons were used in this study. Since the design of the parcour strains the arms and shoulder area, all exoskeletons aimed to support the workflow in front of the upper body and overhead by supporting at the upper arm. The ones used within this study were:
-
• Airframe—Levitate Technologies, Inc., 9540 Waples St., Suite F, San Diego, CA 92121, USA
-
○ Supporting force: 1.7–4.7 kg per arm
-
-
• Paexo Shoulder—Ottobock SE & Co. KGaA, Max-Näder-Straße 15, D-37115 Duderstadt, Germany
-
○ Supporting force: 1–4.5 kg per arm
-
-
• 360 XFR—Skel-Ex B.V., Scheepsbouwweg 8, G4, 3089 JW Rotterdam, Netherlands
-
○ Supporting force: 1–4.9 kg per arm
-
The selection of exoskeletons was randomly determined. All systems were used in equal proportions in the study. In order to be market-neutral and not to create a competitive advantage, no selective evaluation by manufacturer is made.
This can be done, as the build, the point of force application at the upper arm and the supporting force of all three exoskeletons is similar.
Grinding simulator
A grinding simulator was developed to ensure appropriate force on the work piece of 35 N in z direction. This working point is based on a welding experiment that was conducted and analyzed in preparation for this study. The welding parameters defined for the Exoworkathlon in accordance with DIN EN ISO 9606-1 were physically welded in an internal test workshop and processed using an angle grinder. The forces occurring during grinding were determined and simulated using force transducers. The constructed test stand consists of a force-absorbing, linearly mounted plate, which provides visual feedback when a force of 35 N is reached in the z direction.
The operating point is not rigid and leaves space for movement of around 5 mm, as in real grinding. The counterpart is a commercially available angle grinder, of which the functionality is deactivated by isolating the power connector, combined with a dummy cutting disk manufactured of polyoxymethylene with the identical dimensions of a 125 mm cutting disk.
Welding simulators and welding quality
The welding simulators Soldmatic Augmented Training for Welding used for this study were augmented welding systems by Seabery Soluciones. SL, Calle Emilio Haya Prats Doctor, 13, 21005 Huelva, Spain. The used Hardware was Version 3.0 and the used Software was Version 4.0. These systems are educational standard internationally (Kopplin, Reference Kopplin2018). The Soldamatic software automatically performs a rating of welding quality based on the parameters work angle, travel angle, Contact to Work Distance (CTWD), travel speed and aim, rated on a scale between 0 and 100%. Each of these parameters influences the quality of the weld seam. The various parameters result in different failure patterns that may be acceptable or may lead to rejection of the weld seam.
-
• Work angle: Relationship between the axes of the electrode to the work piece (Figure 3, x direction).
-
→ High influence on welding quality/acceptance of the weld seam.
-
-
• Travel angle: Angle between the electrode and the weld seam that is parallel to the direction of travel (Figure 3, y direction).
-
→ Moderate influence on welding quality/acceptance of the weld seam.
-
-
• Contact to Work Distance: Distance between the gun and the work piece, which is the sum of the electrode length and the length of the arc.
-
→ Moderate influence on welding quality/acceptance of the weld seam.
-
-
• Travel speed: Speed in which the gun is moved along the work piece. Specified in cm per minute (Figure 3, y direction).
-
→ High influence on welding quality/acceptance of the weld seam.
-
-
• Aim: deviation of the required position of the weld seam (Figure 3, x direction).
-
→ High influence on welding quality/acceptance of the weld seam.
-
Table 1 lists the five quality parameters and shows the associated defect patterns and their influence on the resulting weld. For this study, the evaluation groups for limit values for irregularities of DIN EN ISO 5817 are used. As different applications of welding have varying levels of acceptance of error patterns (e.g., weld seams in automotive construction have very low tolerance levels while weld seams in building construction have a greater tolerance for errors), three evaluation groups exist. DIN EN ISO 5817 (2021) defines the three evaluation groups B, C, and D, where B represents class with the smallest tolerance level and D the class with the largest tolerance level. In order to increase the significance of this study as well as to reflect the highest possible precision, evaluation group B is utilized in this study.
Table 1. Defect patterns and causes, as well as strength of the influence on the weld quality and acceptance of the weld seam according to DIN EN ISO 5817

Abbreviation: CTWD, contact to work distance
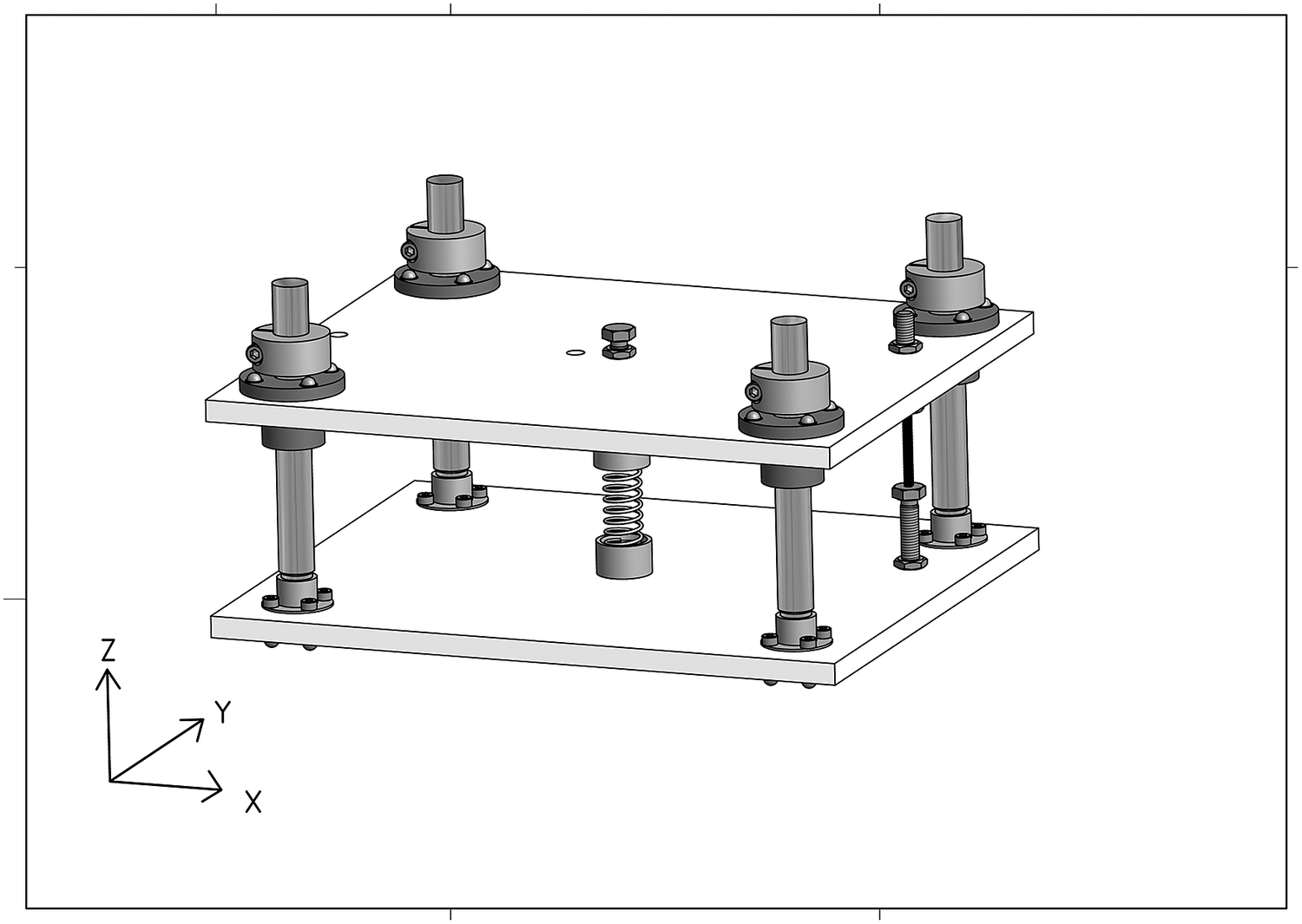
Figure 3. Grinding simulator CAD illustration.
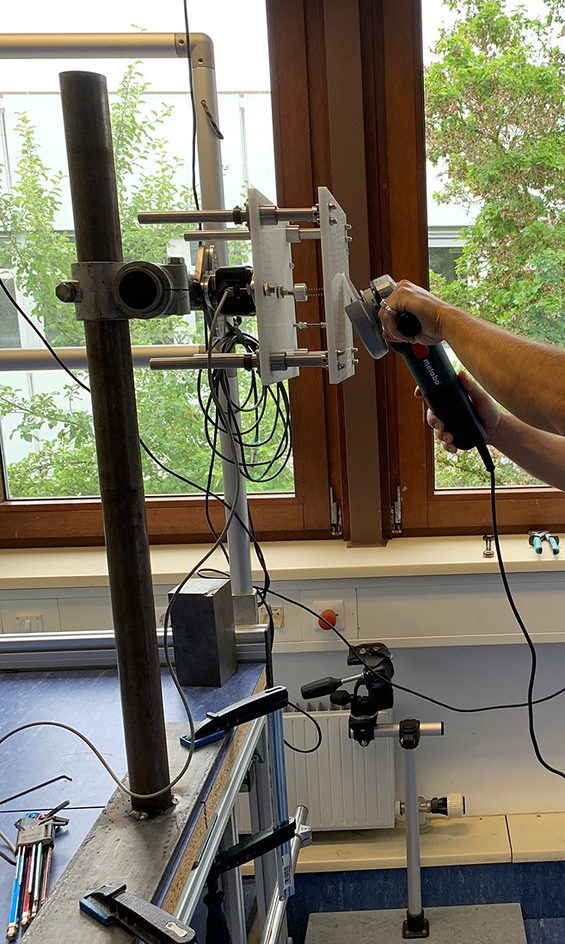
Figure 4. Setup of the grinding simulator in Position PF—force measurement in z direction.
Data Analysis
Data were analyzed using Minitab statistics software, version 20.1.2 (64 bit). N = 15 of total N = 16 participating subjects could be used for this evaluation. One series of measurements could not be taken into account due to an aborted second run. The subject had to leave the study prematurely for private reasons. For the statistical evaluation, each welded seam and all five associated welding parameters were analyzed. Each run results in n = 20 welds and thus n = 40 welds per subject. In total, n = 300 values are available for each parameter to be analyzed. Due to a general left-skewed distribution of the Soldamatic’s scale evaluation system, a natural ordinal scaling and an Anderson–Darling test resulting in nonnormal distribution of the data, a nonparametric statistical analysis was applied. For all test a confidence level of 95% was chosen.
Resulting from a nonnormal distribution, medians were used accordingly to analyze the effects that occurred. Based on a test for equal variances, a Mann–Whitney U test was used to investigate the deviation of the data series.
Results
PF Position: Vertical Uphill
Table 2 (complete table: Table A1) shows the medians of the trials with and without exoskeleton for the quality scale of the parameters work angle, travel angle, CTWD, travel speed, and aim in the position PF. The results displayed for the Mann–Whitney test show no significant influence of the exoskeleton condition on work angle, travel angle, CTWD, and aim. The statistical evaluation Table 2 shows that an exoskeleton has a significant influence on the quality score of the welding parameter travel speed in position PF with the condition “without exoskeleton” reaching a median of 86 points and the condition “with exoskeleton” reaching a median of 91 points. According to Table 1, the parameter travel speed has a strong effect on the weld quality and on the acceptance of the weld seam (Figures 5 and 6).
Table 2. Results of the statistical analysis for the entire population for Position PF

Abbreviation: CTWD, contact to work distance.

Figure 5. Results of the statistical analysis of the parameter travel speed for the entire population n = 15 (median) for Position PF.

Figure 6. 95% Confidence Interval for Median—Position PF comparison with and without Exoskeleton; total population n = 15.
If we look at the 95% confidence intervals of the medians, we can see that the scatter is lower with exoskeletons and thus narrows the interval. In addition, the location of the interval is higher with exoskeletons than without exoskeletons, which shows an improvement in quality. The median score of the quality scale is 5 points higher than the median for this score without exoskeleton. This corresponds to a descriptive increase of 5.80% of the quality score of travel speed. The duration of the respective trials, reflects the higher quality score of the Travel Speed parameter (Table 3).
Table 3. Duration and difference of the welding trials of each subject and in total—Position PF

Note. A, During the trial without exoskeletons in PF Position subject 0304 exhibited such high levels of local fatigue within the shoulder muscles that two short breaks of approximately 2 min each were required. B, During the trial without exoskeletons in PF Position subject 0306 exhibited such high levels of local fatigue within the shoulder muscles that a short break of approximately 2 min was required. C, During the trial without exoskeletons in PF Position subject 0313 complained of extremely uncomfortable shoulder and neck muscle fatigue, which is why he significantly increased his speed. This in turn is reflected in a drastic drop in the quality scale (see Table 1).
Trials with exoskeletons took an average of 10.77% longer than those without the use of an exoskeleton. This has the consequence that the quality score of the travel speed increases.
PE Position: Overhead
Table 4 (complete table: Table A2) shows the medians of the trials with and without exoskeleton for the quality scale of the parameters work angle, travel angle, CTWD, travel speed, and aim in the position PE. The results displayed for the Mann–Whitney test show no significant influence of the exoskeleton condition on work angle, travel angle, CTWD and aim. The statistical evaluation Table 4 shows that an exoskeleton has a significant influence on the quality score of the welding parameter travel speed in position PE. According to Table 1, this parameter has a strong effect on the weld quality and on the acceptance of the weld seam (Figures 7 and 8).
Table 4. Results of the statistical analysis for the entire population for Position PE

Abbreviation: CTWD, contact to work distance.

Figure 7. Results of the statistical analysis of the parameter travel speed for the entire population n = 15 (median) for Position PE.

Figure 8. 95% Confidence Interval for Median—Position PE comparison with and without Exoskeleton; total population n = 15.
If we look at the 95% confidence intervals of the medians, we can see that the scatter is marginally higher with exoskeletons and thus the interval becomes wider. In addition, the location of the interval of the data series with exoskeletons is again significantly higher than without exoskeletons. Regarding the value of the medians, a difference of the quality scale in favor of the data series with exoskeletons of 14 scale points could be found. This corresponds to a descriptive increase of 28.87%. The duration of the respective trials, reflects the higher quality scale of the Travel Speed parameter (Table 5).
Table 5. Duration and difference of the welding trials of each subject and in total—Position PE

Note. A, During the trial without exoskeletons in PE Position subject 0305 exhibited such high levels of local fatigue within the shoulder muscles that two short breaks of approximately 2 min each were required. B, During the trial without exoskeletons in PE Position subject 0306 exhibited such high levels of local fatigue within the shoulder muscles that a short breaks of approximately 2 min were required.
Trials with exoskeletons took an average of 11.63% longer than those without the use of an exoskeleton. This has the consequence that the quality score of the travel speed increases.
Discussion
In both the PF and PE constrained positions, there is a significant increase in weld quality with regard to the Travel Speed parameter. With 5.80% increase in the PF position and 28.87% increase in the PE position of the quality score, these are significant effects, which seem to be more prominent during constrained positions overhead. Taking into account DIN EN ISO 5817 and the resulting high influence of the Travel Speed on the admissibility of the weld in all evaluation classes, a positive influence of exoskeleton use during welding in constrained positions on the weld quality can be assumed. The higher rating of travel speed quality score, resulting from maintaining the ideal travel speed as well as the increased duration of the welding process with exoskeletons, support this hypothesis.
The maintenance of a constant optimal welding speed (whereas slower is better and produces less errors) when using an exoskeleton could be attributed to a lower fatigue of the subject throughout the activity. Without the supporting exoskeleton, an accelerated work process can be observed. This may indicate an earlier onset of shoulder and neck muscle fatigue, which resulted in an increase in working speed in order to complete the weld and rest the arms quicker. This results in a deterioration of weld seam quality caused by welding too fast. An increased degree of subjective muscular fatigue caused a necessary interruption of the activity in PF position for subjects 0304, 0306, and 0313 and in PE position for subjects 0305 and 0306 when an exoskeleton was not used, while no subject had to interrupt the task with an exoskeleton. This finding also suggests that exoskeletons reduce fatigue during welding in constrained positions.
Four out of five welding parameters showed no significant difference with the use of an exoskeleton. Since these parameters are primarily dependent on wrist position and fatigue and are not influenced by a faster work process, this could also be an indication of faster onset of fatigue of the shoulder and arm muscles and its influence on temporal continuity.
Limitations
In order not to emphasize any exoskeleton manufacturer and to be as market-neutral as possible, a selective evaluation of the exoskeletons was deliberately omitted. This increases the scattering of the effects, however, also enables the generalization of the used upper body exoskeletons. Since it was made sure that the used exoskeleton have a similar functionality and comparable supporting force, a generalization is possible.
A further limitation of this study is that the results are based on a study that merely simulates real welding processes. In order to substantiate these results and verify the welding quality on the basis of real workpieces, experiments have to be carried out in the field during real welding with exoskeletons.
Conclusion
The use of an exoskeleton for continuous welding activities, especially in a forced posture like in front of the body and overhead, seems reasonable. It has a significant positive influence on the quality of the weld seam independent of the manufacturer of the exoskeleton. Furthermore, there is increasing evidence that suggests exoskeletons could have a positive effect on fatigue during welding, which in turn leads to improved welding quality. These are promising results from a laboratory study, further subject trials will be realized in order to the stress the hypothesis. Field studies can follow in the next step, which would include destructive testing of the real weld.
Notations
- CTWD
-
contact to work distance
Acknowledgments
We thank Mr Heidinger, AUDI for his contributions. We thank Mrs Richter, WELDPLUS and Mrs Pohlmann, SLV NORD for their conceptional support for parcour 3 and Dr Solbrig, MEDIS for the instrumentation support.
Data Availability Statement
The data that support the findings of this study are available on request from the corresponding author, M.S. The data are not publicly available due to the privacy of research participants.
Funding Statement
This work was supported by University Stuttgart IFF and Fraunhofer IPA, Stuttgart.
Ethical Standards
This study was executed under the ethical approval from University Stuttgart as of September 21, 2021. The authors assert that all procedures contributing to this work comply with the ethical standards of the relevant national and institutional committees on human experimentation and with the Helsinki Declaration of 1975, as revised in 2008.
Competing Interests
The authors declare no competing interests exist.
Authorship Contributions
U.S. had the idea of the Exoworkathlon and coorganized planning and implementation. M.S. planned and carried out the study, performed statistical analyses, and wrote the article. I.S. supported the data gathering and writing of the article. T.B. and J.S. provided the resources and sourcing of measuring instruments. A.E. supported the second study execution and data processing.
Appendix
Table A1. Complete results of the statistical analysis for each subject as well as the entire population for Position PF

Abbreviation: CTWD, contact to work distance.
Table A2. Complete results of the statistical analysis for each subject as well as the entire population for Position PE

Abbreviation: CTWD, contact to work distance.