Introduction
Paper is ubiquitous in our daily life and it is a renewable, abundant, and cheap flexible substrate material. Although it was originally invented for writing and recording purposes, with the fast technological development over the past century, the usage of paper has been broadly extended. For instance, paper has been employed as an effective platform for medical devices [Reference Martinez, Phillips, Carrilho, Thomas, Sindi and Whitesides1, Reference Martinez, Phillips, Whitesides and Carrilho2, Reference Pollock, Rolland, Kumar, Beattie, Jain, Noubary, Wong, Pohlmann, Ryan and Whitesides3], electronics [Reference Yang, Zhang, Staiculescu, Wong and Tentzeris4, Reference Andersson, Nilsson, Svensson, Chen, Malmström, Remonen, Kugler and Berggren5, Reference Zschieschang, Yamamoto, Takimiya, Kuwabara, Ikeda, Sekitani, Someya and Klauk6, Reference Lim, Douglas, Norton, Pearton, Ren, Heo, Son and Yuh7], energy sources [Reference Jabbour, Bongiovanni, Chaussy, Gerbaldi and Beneventi8], etc. There are clear advantages when using paper as a substrate for these aforementioned applications, including low cost, scalability, manufacturability, degradability, and recyclability, compared with using other common candidates such as plastics and metal foils.
In particular, the past decade has witnessed extensive use of paper for various electronic devices and systems, such as diagnostic instruments [Reference Martinez, Phillips, Carrilho, Thomas, Sindi and Whitesides1, Reference Martinez, Phillips, Whitesides and Carrilho2, Reference Pollock, Rolland, Kumar, Beattie, Jain, Noubary, Wong, Pohlmann, Ryan and Whitesides3], physical and chemical sensors [Reference Yang, Rida, Vyas and Tentzeris9, Reference Vyas, Lakafosis, Rida, Chaisilwattana, Travis, Pan and Tentzeris10, Reference Lakafosis, Rida, Vyas, Yang, Nikolaou and Tentzeris11, Reference Nery and Kubota12], circuits [Reference Kim, Kim, Wu, Liu, Song, Kim, Huang, Hwang and Rogers13, Reference Martins, Nathan, Barros, Pereira, Barquinha, Correia, Costa, Ahnood, Ferreira and Fortunato14], displays [Reference Andersson, Nilsson, Svensson, Chen, Malmström, Remonen, Kugler and Berggren5, Reference Kim, Park, Jeong, Bae, Song, Lee, Han, Jung and Yu15], and energy sources [Reference Jabbour, Bongiovanni, Chaussy, Gerbaldi and Beneventi8]. Because of the compatibility and similarity between paper manufacturing and device manufacturing, the associated low cost has been one of the driving forces in paper-based device development. For instance, Pollock et al. developed paper-based transaminase sensors for monitoring drug-induced liver injury [Reference Pollock, Rolland, Kumar, Beattie, Jain, Noubary, Wong, Pohlmann, Ryan and Whitesides3]. Yang et al. developed a fully inkjet-printed gas sensor on a paper substrate [Reference Yang, Zhang, Staiculescu, Wong and Tentzeris4]. Martins et al. developed complementary metal oxide semiconductor electronics on a flexible fiber-based paper substrate [Reference Martins, Nathan, Barros, Pereira, Barquinha, Correia, Costa, Ahnood, Ferreira and Fortunato14]. Andersson et al. fabricated an electrochromic display on a polymer-coated paper [Reference Andersson, Nilsson, Svensson, Chen, Malmström, Remonen, Kugler and Berggren5]. Hu et al. fabricated supercapacitors using paper composites inked with single-walled carbon nanotubes [Reference Hu, Choi, Yang, Jeong, La Mantia, Cui and Cui16].
Among various electronic devices, the transistor is a fundamental building block for circuits and integrated systems to allow the functions of switching, interfacing, reading out, signal processing, etc. Paper-based transistors, in the format of thin-film transistors (TFTs), are therefore indispensable toward integrated paper electronic systems. Paper-based TFTs have been reported before [Reference Zschieschang, Yamamoto, Takimiya, Kuwabara, Ikeda, Sekitani, Someya and Klauk6, Reference Lim, Douglas, Norton, Pearton, Ren, Heo, Son and Yuh7, Reference Shin, Roh, Song, Roh, Kang, Lee, Park, An, Kim, Kim and Kwak17, Reference Grau, Frazier and Subramanian18]. For instance, Zschieschang et al. developed an organic field effect transistor (OFET) on banknotes [Reference Zschieschang, Yamamoto, Takimiya, Kuwabara, Ikeda, Sekitani, Someya and Klauk6]. However, in the TFTs, paper was used solely as a supporting substrate, thus in a passive fashion for transistor-on-paper. Fortunato et al. and Lim et al. demonstrated paper transistors, where the papers were used not only as substrates but also as the gate dielectric [Reference Fortunato, Correia, Barquinha, Pereira, Gonçalves and Martins19, Reference Martins, Barquinha, Pereira, Correia, Gonçalves, Ferreira and Fortunato20, Reference Lim, Douglas, Kim, Norton, Pearton, Ren, Shen and Chang21]. However, the TFTs operated at relatively high voltages (tens of volts), which limits their potential practical applications, such as biomedical devices. The high operational voltage of paper TFTs is mainly due to the relatively low specific capacitance of the paper dielectric.
Here, we a present a flexible paper transistor in the format of transistor-in-paper with low operational voltage. Such a low operational voltage is a consequence of harnessing paper as the unique dielectric material in addition to its role as a natural substrate. Specifically, by taking advantage of the cellulose fiber microstructures of paper, we created an ion gel/cellulose fiber composite that serves as a dielectric once ion gels are added on the paper. The ion gel/cellulose fiber composite exhibits significantly increased specific capacitance, thus resulting in a much lower operational voltage of 1.8 V. The transistor-in-paper shows a high on/off current ratio of ∼104 and retains transistor function even when it is bent. We further developed paper-based logic gates and a multiplexed active matrix tactile sensing mat device to show the capabilities and usages of the transistor-in-paper in electrical circuits. Detailed materials preparation, device fabrication, integration, and characterization illustrate the key aspects of the low-voltage transistor-in-paper and its potential usages in integrated paper electronic systems.
Results and discussion
One of the key steps for the transistor-in-paper fabrication involves the preparation of the ion gel/cellulose fiber composite. Figure 1(a) shows an optical image of the ion gel solution in a vial and the chemical compounds involved in its material preparation. Specifically, poly(vinylidene fluoride-co-hexafluoropropylene) [P(VDF-HFP)] and 1-ethyl-3-methylimidazolium tri(fluoromethanesulfonate) amide (EMIM-Otf) serve as the polymer matrix and ionic liquid, respectively. The ion gel preparation involves mixing the polymer matrix and the ionic liquid within acetone to first form a solution phase gel. The solution phase gel can be solidified upon thermal curing as described below. The detailed material preparation is described in the Materials and methods section. It is noted that the ion gel has poor adhesion with most substrates, such as plastics and metal foils. By taking advantage of the porous cellulose structure of paper (28 lbs, white, and brightness rating of 100 for sharp, Hammermill Paper Company, Pennsylvania), ion gel in liquid phase can first diffuse into paper and then solidify to form the composite of ion gel/cellulose fiber. It is noted that other papers with different porous cellulose architectures or different thickness could be used and their ion gel/cellulose fiber composite can be fabricated and optimized for low-voltage transistors. By using a stencil printing technique, ion gel can be selectively deposited onto the paper and the thickness of the composite after diffusion can be controlled. Figure 1(b) shows the cross-sectional image of the cellulose paper after stencil printing the ion gel solution onto the paper. A thin layer of ion gel diffused into the cellulose paper to form a ∼30-μm-thick composite. The specific capacitances of the paper with and without loaded ion gel after solidification were characterized as a function of frequency. The imaginary impedance of the samples was first measured (Multi Autolab Cabinet, Metrohm, Herisau, Switzerland) by fixing the samples in between two parallel metal plates. The specific capacitance was calculated using the following equation:

where A is the sample surface area, f is frequency, and Z″ is the imaginary impedance. It should be noted that to form good contact with the metal plates, the samples were also coated with a thin layer of gold on the surfaces. The specific capacitance of the paper with ion gel increased from 0.34 to 21.5 nF/cm2 at 1 Hz, as shown in Fig. 1(c). The specific capacitance increase of the paper after enhancement by the ion gel solution can be attributed to the high capacitance of the ion gel [Reference Hammock, Chortos, Tee, Tok and Bao22, Reference Cho, Lee, Xia, Kim, He, Renn, Lodge and Frisbie23, Reference Lee, Kang, Zhang, Gu, Lodge and Frisbie24]. It is noted that the specific capacitance of the ion gel/cellulose fiber composite is lower than that of an ion gel dielectric. The reason is because the ion gel does not fully penetrate across the thickness of the paper. Figure 1(d) shows the frequency-dependent specific capacitance of the ion gel/cellulose fiber composite under different bending radii. The specific capacitance of the composite increases as the bending radius decreases, and the specific capacitance at f = 1 Hz increased from 21.5 nF/cm2 at the flat state to 69.9 nF/cm2 at a bending radius of 3.2 mm, as shown in Fig. 1(e). The increased specific capacitance is attributed to the plastic deformation of the cellulose fibers and the reduced thickness of the fibers when they are bent. Figure 1(f) presents the frequency-dependent dielectric loss of the ion gel/cellulose composite.

Figure 1: Characterization of the ion gel/cellulose fiber composite. (a) Optical image of the ion gel solution and its chemical compounds. (b) Optical image of the cross-sectional ion gel/cellulose fiber composite. (c) Specific capacitance of the paper and ion gel/cellulose fiber composite at different frequencies. Specific capacitance of the ion gel/cellulose fiber composite (d) under different frequencies and (e) under different bending radii at f = 1 Hz. (f) Dielectric loss of the ion gel/cellulose fiber composite under different frequencies.
The fabrication process of the flexible TFTs based on an ion gel/cellulose fiber composite is schematically illustrated in Fig. 2(a). Specifically, the process started with depositing the patterned indium gallium zinc oxide (IGZO) active layer, and Cr/Au source and drain electrodes through shadow masks, followed by stencil printing the ion gel and conductive rubber through shadow masks to serve as the dielectric and gate electrodes, respectively. The shadow masks were made of Kapton film, patterned by photolithography and dry etching, as reported in our prior work [Reference Gao, Zhang, Wang, Sim, Liu, Chen, Feng, Xu and Yu25]. The preparation of the shadow masks is described in the Materials and methods section. Figure 2(b) shows the optical image of the bendable transistor-in-paper. The transistor was devised into a back gated structure. The schematic structure is shown in Fig. 2(c). The channel length and width of the TFTs are 50 µm and 2 mm, respectively. Figures 2(d) and 2(e) show the SEM images of the cellulose paper before and after IGZO deposition. As can be seen, the fibers are covered with the IGZO film that remains continuous even after bending, which ensures that the transistor retains its electrical functions.
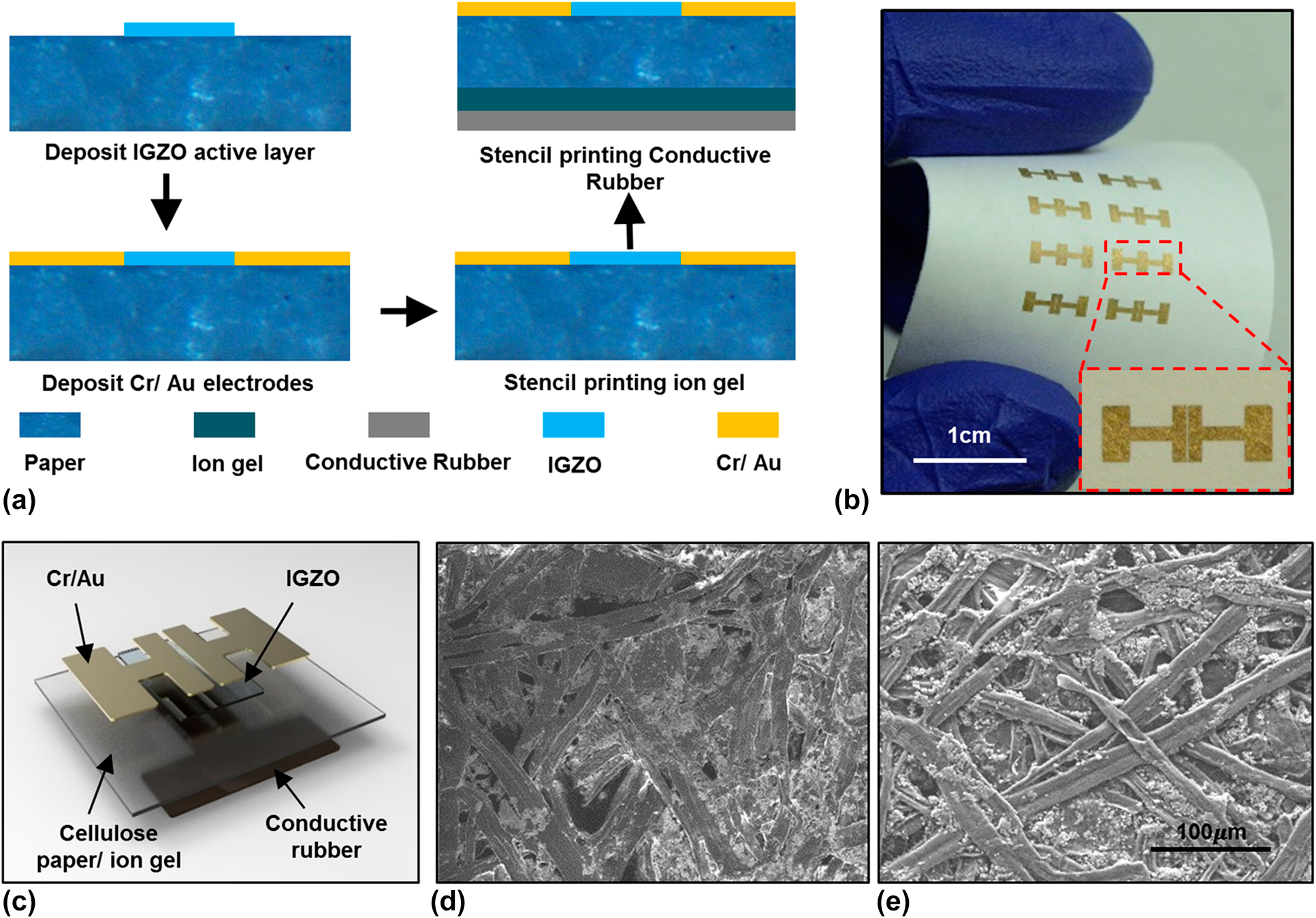
Figure 2: Flexible low-voltage transistor-in-paper. (a) The fabrication process, (b) optical image, and (c) schematic structure of the transistors based on ion gel/cellulose fiber composite. SEM images of cellulose paper (d) before and (e) after depositing the IGZO semiconductor layer.
The forward and backward swept transfer characteristics (I D − V GS, in black) of the ion gel/cellulose fiber composite–based transistor-in-paper are shown in Fig. 3(a). The drain current was measured while sweeping V GS from −0.6 to 4 V at a constant V DS of 1 V. The transistor operated in the enhancement mode with a low drain current at V GS = 1.2 V and showed a reasonable on/off current ratio of ∼104, which is comparable to that of IGZO-based TFTs on paper substrates [Reference Lim, Douglas, Norton, Pearton, Ren, Heo, Son and Yuh7, Reference Grau, Frazier and Subramanian18, Reference Fortunato, Correia, Barquinha, Pereira, Gonçalves and Martins19]. The field effect mobility of the transistor was calculated from the slope in the saturation regime of the square root of the drain current versus the gate voltage [Fig. 3(a), red]. The mobility was then calculated based on the following equation [Reference Brotherton26, Reference Lee, Chang, Koo and Lee27, Reference Yabuta, Sano, Abe, Aiba, Den, Kumomi, Nomura, Kamiya and Hosono28] for the transistor working in the saturation region:

where C i (21.5 nF/cm2) is the specific capacitance chosen at the frequency of 1 Hz, W (2 mm) is the channel width, L (50 µm) is the channel length, and V T is the threshold voltage. It is noted that the specific capacitance at low frequencies was used to avoid overestimation of the mobility due to the low capacitance at high frequencies. The saturation mobility was calculated to be 9.1 cm2/(V s). As a comparison, the transfer curve of a paper transistor without the addition of ion gel is shown in Fig. 3(b), where the operation voltage is about 10 V, much higher than that of the transistor-in-paper. The calculated mobility of the transistor without the addition of ion gel is 8.7 cm2/(V s). These calculations suggest comparable results for the IGZO thin-film transistor [Reference Lim, Douglas, Norton, Pearton, Ren, Heo, Son and Yuh7, Reference Fortunato, Correia, Barquinha, Pereira, Gonçalves and Martins19, Reference Lim, Douglas, Kim, Norton, Pearton, Ren, Shen and Chang21]. It is noted that the ion gel/cellulose fiber–based device does not show any transistor characteristics at low gate voltage <5 V. Figure 3(c) shows the output characteristics (I D–V DS) of the transistor-in-paper at different gate voltages (V GS), ranging from 2 to 5 V with a voltage step of 0.3 V. The drain voltage was increased from 0 to 1 V. The output characteristics indicate an increase in channel conductance with increased V GS. Saturation in the drain current was observed in the high drain voltage regime. A saturation current as high as 20 µA was obtained at V GS = 5 V and V DS = 1 V. The threshold voltage decreased to 1.8 V, compared with V T = 10 V for transistor-on-paper without ion gel as mentioned previously. Such a significant decrease in the threshold voltage is due to the larger capacitance of the ion gel/cellulose fiber composite.

Figure 3: Characterization of the low-voltage transistor-in-paper. (a) Forward and backward transfer curves of TFTs based on ion gel/cellulose fiber composite. The red curve corresponds to the forward transfer curve. (b) Transfer curve of TFTs based on cellulose fiber paper. (c) Output curves of TFTs on ion gel/cellulose fiber composite. (d) Transfer curves of the TFTs on ion gel/cellulose fiber composite under different bending radii.
The device performance upon mechanical bending was also characterized. The set of transfer curves, shown in Fig. 3(d), indicate that there was no significant performance degradation for the TFTs of which the bending radii are larger than 5.1 mm. The bending direction was aligned with the channel length direction to achieve the maximum applied mechanical strain on the device. As the bending radius decreased to 3.2 mm, only a slight decrease in the on-current was observed. These results suggest that the flexible low-voltage transistor-in-paper is robust to bending.
We further developed a flexible ion gel/cellulose fiber composite–based inverter to illustrate digital logic gate functions. The inverter is a basic component for various digital and integrated circuits. Two types of inverters, including a diode-load inverter and a zero-V GS inverter, were constructed [Reference Huang, Fukuda, Lo, Yeh, Sekitani, Someya and Cheng29]. Figures 4(a) and 4(b) show the schematic structure and equivalent circuit diagram of the diode-load inverter. The transistors in the inverter had a channel length of 50 µm. The channel width of the driving TFT in the diode-load inverter and that of the loading TFT in the zero-V GS inverter was 2 mm. The channel width ratio of the loading TFT and the driving TFT in the diode-load inverter was 1/3. Figure 4(c) shows the measured voltage transfer curves (VTCs) and gains of the diode-load inverter while V DD was kept at 2 V. Figures 4(d) and 4(e) show the schematic structure and equivalent circuit diagram of the zero-V GS inverter, respectively. The channel length of the transistor was 50 µm. The channel width of the loading TFT in the zero-V GS inverter was 2 mm. The channel width ratio of the loading TFT and the driving TFT in the zero-V GS inverter was 3/1. Figure 4(f) shows the measured VTC curve and gain of the zero-V GS inverter. Both types of inverters showed adequate voltage transfer. The gain of the diode-load inverter and that of the zero-V GS inverter were about 0.7 and 1.3, respectively, which are comparable to those of IGZO-based inverters on plastic substrates [Reference Huang, Fukuda, Lo, Yeh, Sekitani, Someya and Cheng29].

Figure 4: Characterization of paper transistor–based inverters. (a) Schematic structure, (b) equivalent circuit diagram, and (c) VTC of the diode-load inverter. Channel width ratio β1 = (W 1/W 2) ∼ (1/3). (d) Schematic structure, (e) equivalent circuit diagram, and (f) VTC of the zero-V GS inverter. Channel width ratio β2 = (W 3/W 4) ∼ (3/1).
Transistors are the basis for multiplexed active matrix arrays which are useful for many applications, such as pixel addressing and spatial and temporal sensing. Flexible transistor-in-paper offers the multiplexing capabilities in paper integrated devices. We developed a flexible tactile sensing mat with multiplexing readout capabilities based on a 5 × 5 array of ion gel/cellulose fiber composite–based transistors. The tactile sensing mat was composed of a piece of pressure-sensitive rubber (PSR) and an array of transistor-in-paper, where the PSR served as a pressure-sensitive component and the transistors were multiplexing units, respectively. Figure 5(a) shows the schematic structure of the pressure sensing mat in layered exploded view. Figure 5(b) presents the optical image of the top side of the device. The mat was accomplished through integrating the PSR onto the prefabricated transistor array. The detailed fabrication process of the mat is described in the Materials and methods section. Figure 5(c) depicts a photo of the mat device. Since every component, including the transistor and PSR, is soft and flexible, the entire mat device is also flexible. The detailed multiplex array is schematically illustrated by the circuit diagram in Fig. 5(d). The PSR acts a variable resistor upon different applied pressures. Each tactile sensing node was connected through an ion gel/cellulose dielectric–based paper transistor in the array. The gate electrodes of each line were connected to a word line (V WL), whereas the drain electrodes of each line were connected to a bit line (V BL) [Reference Someya, Sekitani, Iba, Kato, Kawaguchi and Sakurai30].

Figure 5: Design and structures of active matrix based multiplexed tactile sensing mat. (a) Schematic structure and (b) optical image of the tactile sensing mat. (c) Optical image of the flexible transistor array for building the active matrix multiplexed sensing mat. (d) Circuit diagram of the 5 × 5 tactile sensing mat.
The electrical resistance of the PSR changed under applied pressure. The PSR had a threshold pressure of ∼94 kPa. As a pressure higher than 94 kPa was applied on the mat, the resistance of the PSR varied from several GΩ at a nonpressed state to several Ω at a pressed state [Reference Sim, Rao, Kim, Thukral, Shim and Yu31]. The circuit diagram of each sensing node of the pressure sensing mat is shown in Fig. 6(a). The drain current (I D) dependence on the gate voltage (V GS) at different states is shown in Fig. 6(b). A pressure map therefore can be obtained by multiplexed readout of the output current of the channels with applied voltages of V DS = 1 V for each bit line and V GS = 4 V for each word line. Figure 6(c) shows the current output of the mat upon applying pressure using triangular and rectangular objects. The pressed sensors have a high drain current output of up to 10−5 A, whereas nonpressed sensing nodes have a relatively low drain current output of around 10−11 A. These results indicate that the array of ion gel/cellulose dielectric–based transistor-in-paper can successfully serve as a multiplexing readout circuit. It is noted that the resolution of the tactile sensing mat can be further improved through optimizing the design of the transistor array.

Figure 6: Characteristics of the tactile sensing mat. (a) Circuit diagram of each sensing node. V BL, bit line; V WL, word line; V DD, supply voltage. (b) Transfer curves of a single pixel in the matrix at a pressed state and at a nonpressed state. (c) Current mapping of the tactile sensing mat with applied pressure using triangular-shaped (left) and rectangular-shaped (right) objects.
Conclusions
In conclusion, we developed a flexible low-voltage transistor-in-paper, where the paper served as the substrate and also the dielectric in a format of an ion gel composite. Owing to the porous cellulose structure of the paper, ion gel was partially embedded into the paper and formed composite with very high specific capacitance (21.5 nF/cm2). Such an ion gel/cellulose fiber composite substrate gave rise to the low-threshold voltage of the transistor. By taking advantage of the various additive manufacturing means for semiconductors and conductors, a flexible transistor was simply constructed and retained robust performance. The flexible low-voltage transistor-in-paper was utilized to build digital logic circuits and integrated electronics functions. As demonstrated in this work, inverters and active matrix multiplexing arrays were developed. An active matrix array based on the ion gel/cellulose fiber composite could be immediately used for arrayed sensing readout, as exemplified by the tactile sensing mat. All the results show that the ion gel–modified paper renders a class of promising, flexible, low-voltage transistors and circuits that can be potentially integrated toward the development of integrated paper electronic devices and systems, medical devices, human–machine interfaces, etc. Modification of the paper cellulose structures sheds light on future development of various paper devices.
Materials and methods
Preparation of ion gel dielectric solution
The ion gel dielectric solution was obtained by mixing P(VDF-HFP) (M w ∼ 400,000, Sigma-Aldrich, Missouri), ionic liquid EMIM-Otf (>98%, Sigma-Aldrich, Missouri), and acetone (>99.9%, Sigma-Aldrich, Missouri) at a weight ratio of 1:4:7 at 70 °C.
Preparation of the ion gel/cellulose fiber composite
The ion gel/cellulose fiber composite was prepared by stencil printing the ion gel solution on the cellulose paper (28 lbs, white, and brightness rating of 100 for sharp, Hammermill Paper Company, Pennsylvania), using a razor blade, followed by curing in a vacuum oven at 70 °C for 12 h to solidify.
Shadow mask preparation
The shadow masks were made of Kapton film (25.4 μm thick, Dupont, Delaware). The preparation of shadow mask began with spin-coating (1000 rounds per minute for 30 s, Brewer Cee 200 spin coater, Brewer Science Inc., Missouri) a thin layer of PDMS on a cleaned glass slide and curing to form an adhesive layer. A piece of Kapton film was laminated onto the PDMS surface and dehydrated at 90 °C for 10 min after cleaning the film surface. Then, a layer of 500-nm-thick Cu was deposited on top of the Kapton film using electron-beam evaporation (Thermionics, Washington), followed by patterning the Cu through photolithography and wet etching. Reactive ion etching (oxygen: 40 standard cubic centimeter per minute; power, 250 W; Oxford plasma lab 80 plus, Oxford Instruments, Abingdon, United Kingdom) was performed for 8 h to etch through the Kapton film. Then the completed shadow mask was peeled off from the PDMS adhesive.
Fabrication of the ion gel/cellulose fiber composite–based flexible TFTs
The ion gel/cellulose fiber composite–based TFTs were fabricated by first depositing IGZO (30 nm, Kurt J. Lesker, Pennsylvania) on the cellulose paper by DC sputtering (20 W; 50 mtorr, 10% of oxygen partial pressure to argon, with source to substrate distance of around 17 cm, AJA ATC 2200 UHV sputtering system, AJA International Inc., Massachusetts) through shadow masks. Then, the Cr/Au (5 nm/60 nm) source and drain electrodes were formed by e-beam evaporation through the shadow mask, followed by stencil printing the ion gel. Finally, conductive rubber (Zoflex, FL45) was stencil-printed on the ion gel/cellulose fiber composite substrate as the bottom gate.
Fabrication of the ion gel/cellulose fiber composite–based tactile sensing mat
The fabrication process of the pressure sensor matrix involved fabricating the TFT array on an ion gel/cellulose fiber composite substrate, covering the source electrodes of the TFT array using polydimethylsiloxane (PDMS, Dow-Corning, Michigan), and laminating the PSR covered by conductive rubber onto the TFT array. The TFT array was fabricated in the same way as that of the TFTs on the ion gel/cellulose fiber composite substrate. Then, a PDMS insulating layer was scratch-coated on the TFT array through shadow masks followed by coating conductive rubber on the source electrodes of the TFTs. Finally, the PSR (Zoflex, ZL45.1) coated with the conductive rubber paste (Zoflex, FL45) was laminated on top of the device.
Material characterization and device measurements
An optical microscope (Eclipse LV100ND, Nikon, Tokyo, Japan) was used to capture the optical images of the cross-sectional structure of the ion gel/cellulose fiber composite. The frequency-dependent specific capacitances of the cellulose paper and ion gel/cellulose fiber composite were measured by an impedance analyzer (Multi Autolab Cabinet, Metrohm, Herisau, Switzerland). The electrical properties of the transistors, inverters, and pressure sensor matrix were characterized by a semiconductor analyzer (4200SCS, Keithley Instruments Inc., Ohio).
Acknowledgments
C.Y. would like to acknowledge the funding supports from the NSF ECCS award (No. 1509763), Doctoral New Investigator grant from American Chemical Society Petroleum Research Fund (56840-DNI7), 3M nontenured faculty award, and the startup fund from University of Houston.