Introduction
Since both living organisms and technical systems face different types of damage, the ability to self-seal wounds, fissures, cracks, and ruptures markedly contributes to their long-term structural integrity and functionality to achieve their expected lifetime. Longevity concepts of system functions, such as redundancy and damage repair (e.g., self-sealing and self-healing) increase the failure tolerance of living and inanimate materials systems (Mylo and Speck, Reference Mylo and Speck2023). Structural adaptivity of technical systems and initial response (e.g., streamlining under wind load) or acclimation (e.g., increase or decrease of geometric and mechanical properties) of plants to loading conditions can improve the ability of preventing damage, so that technical systems and plants can withstand higher stresses without damage. Moreover, self-sealing and self-healing principles of plants provide a treasure trove of inspiration for technical materials systems because a self-repairing function would ensure service lifetime extension (Garcia, Reference Garcia2014).
Definition and quantification of self-repair, self-sealing, and self-healing
In recent years, scientists have developed a variety of artificial materials systems with self-sealing and self-healing functions that were inspired by biological models. In this context, the term ‘self-repair’ seems to be a paradox, because ‘repair’ usually means that damage is eliminated by a craftsman with the help of tools and ‘self’ implies that the repair is autonomous. Here, we use self-repair as an umbrella term that encompasses both a self-sealing phase and a self-healing phase (Harrington et al., Reference Harrington, Speck, Speck, Wagner and Weinkamer2015). In the following, however, the generic term self-repair is only used when it is not clear from the literature whether it is self-sealing or self-healing, or when the statements refer to both equally. When aiming to incorporate self-sealing and self-healing into technical systems, we must not only define what this means in our context, but we must also quantify self-repair. However, quantifying self-repair raises a few additional questions: What size of damage can be self-repaired? How quickly should self-repair be carried out? How often can the damage be self-repaired? What is being restored? What does autonomous mean? (Speck and Speck, Reference Speck and Speck2019; Mylo and Speck, Reference Mylo and Speck2023). The size of the damage, the speed, and repeatability of the self-repair must be defined in the specifications according to the product.
With respect to the question ‘what is being restored’, we can answer that mechanical properties, structures and functions can be restored. Several equations can be found in the literature which quantitatively analyse mechanical properties. In all these equations, the properties of various states of the entire self-repairing process such as the damaged state (freshly injured), sealed state, and healed state are compared with the intact state (without damage). All equations can be used for biological and artificial samples. The beauty of the calculated dimensionless values is that they allow biological or artificial samples to be compared with each other, as well as biological samples to be compared with artificial samples, such as the intact state (without damage), damaged state (freshly injured), sealed state, and healed state. Some equations calculate the healing efficiency by comparing the intact state and healed state (Diesendruck et al., Reference Diesendruck, Sottos, Moore and White2015; Cohades et al., Reference Cohades, Branfoot, Rae, Bond and Michaud2018), other formulas additionally consider the influence caused by the injury (damaged state) (Mylo et al., Reference Mylo, Krüger, Speck and Speck2020). It is essential that the same material property is compared in different states (intact, damaged, sealed, and healed), because the repair efficiency of the individual material properties can differ considerably from each other. Restoration of structural integrity can only be qualitatively assessed by imaging techniques that show the extent to which the damage has been sealed or healed (e.g., closure of a fissure by released plant sap or newly formed tissue) and whether the same material was used in the wound area (e.g., callus formation or lignification).
With respect to ‘self-repair’ another question arises: What does autonomous mean? Fully autonomous means that no trigger other than the damage is required to initiate and promote repair. Nevertheless, artificial self-repairing materials systems often enumerate external factors such as temperature, light, humidity, mechanical compression that support repair. In order to compare the repair efficiency of different systems, the size of the damage to be repaired should also be defined, whether a single repair is sufficient or multiple repairs are necessary and how much time is available for repair.
Self-sealing and self-healing in plants
In the course of biological evolution, plants have developed a huge variety of functional principles to cope with internal and external wounds. In all plant species studied to date, two phases have been found after a damage in the form of a gap (= fissure) that separates tissues and/or cells. First, rapid self-sealing of damage takes place immediately after injury, resulting in a still present fissure that is functionally repaired, but the mechanical properties in the wound area have not yet been restored. In the case of self-sealed fissures, the wound gap may be filled by the release of plant sap or minimised by deformation of the wound area where the wound surfaces are pressed together. Second, there is a longer-lasting self-healing phase in which the fissures are structurally repaired and thus are no longer present, while the mechanical properties in the wound area are (at least partially) restored. In the case of self-healed fissures, the wound gap may be filled by the formation of new plant cells (wound periderm) (Harrington et al., Reference Harrington, Speck, Speck, Wagner and Weinkamer2015; Speck et al., Reference Speck, Schmauder, Speck and Paul-Victor2020). The division into a rapid self-sealing phase and a longer-lasting self-healing phase, however, is not only found in plants but also in animals and even in technical materials systems. Even in plants, the duration of the phases varies greatly and the underlying functional principles are highly different (Speck and Speck, Reference Speck and Speck2019). A multitude of principles exist because, on the one hand, the function of self-sealing and self-healing has developed independently several times in the course of biological evolution in the Plant Kingdom. On the other hand, functional principles of self-sealing and self-healing in plants can occur at various hierarchical levels (e.g., molecules, cells, tissues, organs, and systems) both individually and in combination. Decisively, each individual cell with its individual properties (e.g., geometry, size, shape, mechanics, etc.) is integrated into the respective tissue and further hierarchical levels and thus contributes to the reaction of the overall system.
The self-sealing principles of plants include mainly physical reactions such as (i) cell deformation (e.g., squeezing of sealing cells into fissures), (ii) tissue deformation (e.g., rolling-in of dermal tissues), (iii) deformation of entire plant organs (e.g., succulent leaves bend or contract), and (iv) discharge of plant sap such as mucilage (e.g., cacti), resin (e.g., trees), or latex (e.g., latex-bearing plants) into the wound region (Bauer and Speck, Reference Bauer and Speck2012; Anandan et al., Reference Anandan, Rudolph, Speck and Speck2018; Klein et al., Reference Klein, Hesse, Boljen, Kampowski, Butschek, Speck and Speck2018; Speck et al., Reference Speck, Schlechtendahl, Borm, Kampowski and Speck2018; Hesse et al., Reference Hesse, Kampowski, Leupold, Caliaro, Speck and Speck2020; Mylo et al., Reference Mylo, Krüger, Speck and Speck2020). During the subsequent self-healing phase, chemical reactions and more complex biological metabolic processes dominate including (i) coagulation of latex (e.g., latex-bearing plants) (Bauer and Speck, Reference Bauer and Speck2012), (ii) local lignification of tissues (e.g., flax cultivars) (Paul-Victor et al., Reference Paul-Victor, Dalle Vacche, Sordo, Fink, Speck, Michaud and Speck2017), (iii) formation of a (ligno-suberised) boundary layer in almost all studied plants (Rittinger et al., Reference Rittinger, Biggs and Peirson1987; Evert, Reference Evert2006; Anandan et al., Reference Anandan, Rudolph, Speck and Speck2018; Mylo et al., Reference Mylo, Krüger, Speck and Speck2020), and (iv) the development of a wound periderm (Evert, Reference Evert2006; Anandan et al., Reference Anandan, Rudolph, Speck and Speck2018; Mylo et al., Reference Mylo, Krüger, Speck and Speck2020).
Biomimetic approaches
In the past, materials systems with a self-sealing and/or self-healing function were found exclusively in living nature. In recent years, engineers and materials scientists have developed artificial materials systems that can autonomously seal and heal damage, some of which even have a biological model. In order to transfer functional principles from living organisms to technical systems, we use a systematic and step-by-step process called biomimetics (Speck et al., Reference Speck, Speck, Horn, Gantner and Sedlbauer2017). In the context of this study, we use the ISO guideline for biomimetics (ISO:18458, 2015), and distinguish between the biomimetic top-down approach (= technology pull process) and biomimetic bottom-up approach (= biology push process). With respect to self-repair, the aim of the technology pull process is to equip an already existing technical product with a self-sealing and/or self-healing principle found in a biological model. Whereas in the biology push process, a completely new technical product with self-repair function is developed. Both interdisciplinary biomimetic approaches consist of six steps, which differ only in the first step. In the bottom-up approach, biologists start with (1) the biological question of wound sealing and healing in biological models, whereas in the top-down approach, engineers start with a (1) technical challenge. After having (2) selected and investigated suitable biological models, (3) the functional principles of self-sealing or self-healing are (4) translated into an engineer-compatible language such as numerical or analytical models. This abstraction step (4) is the prerequisite for developing biomimetic technical products in the framework of a (5) feasibility study on a laboratory scale, prototypes, pilot series, and finally, a (6) market launch.
In general, taking the decisive step from understanding the functional principle of a biological model to applying the functional principle in technology relies on a successful abstraction. The word abstraction comes from the Latin word abstractus and can be translated as subtracted, removed, or separated. Thus, abstraction describes the thought process of omitting extraneous details and translating it into something more general or simpler. In the context of biomimetics, there have been no attempts to simply copy all of the details of the biological model, instead only aspects essential to the functional principle have been extracted and translated into a language compatible with engineering. The results of abstraction are, for example, numerical and analytical models, flow charts, circuit diagrams, simple hand models, or prototypes (ISO:18458, 2015). Choosing which type of abstraction is most suitable depends on the prerequisites of the selected model. For an analytical model, usually only a small amount of data from the biological model is needed. In contrast, numerical models require a larger amount of data, which must be collected from the biological model and usually must also be supplemented with data from the literature. This can be illustrated by the example of the self-sealing principles of Delosperma cooperi. The analytical model (Konrad et al., Reference Konrad, Flues, Schmich, Speck and Speck2013), which models the deformation of the whole leaf after a transverse, longitudinal, or circumferential injury, refers to the pre-stresses in the five leaf tissues. For the analytical model, we needed the layer thickness, elastic modulus and Poisson's ratio for each tissue layer, thus a total of 15 values. For the numerical model (Klein et al., Reference Klein, Hesse, Boljen, Kampowski, Butschek, Speck and Speck2018), which models the deformation of the entire leaf after a circumferential damage driven by shrinking and swelling, a total of 28 values were necessary. The advantage of analytical models is the generation of formulas that allow predictions and a tailored design for the respective technical application. Although numerical models offer approximate solutions, they can be applied to complex geometries (Marschik et al., Reference Marschik, Roland, Löw-Baselli and Steinbichler2020).
Aim of the study
The main aim of this review article is to establish flow charts as a common language understandable by biologists and engineers to transfer functional principles of self-sealing found in plants into programmable metamaterials. In this interdisciplinary framework, transferring information from biological research into the development of a designed materials system is challenging because researchers from various fields differ in definitions, terms, and approaches. Therefore, we picked self-sealing as a specific problem where we could test the feasibility of flow charts as common language.
In order to create a common language by means of flow charts, we had to answer three fundamental scientific questions:
-
1. How do the self-sealing principles of our selected plant models differ?
-
2. Can we use flow charts as a method of abstraction to describe self-sealing processes within specific plants?
-
3. What chances and challenges occur by transferring self-sealing from plants into programmable mechanical metamaterials by means of flow charts?
In the following sections, we will answer these fundamental questions based on three biological examples from literature, extract the underlying algorithms for self-sealing, establish flow charts representing the algorithms following by an example and last, discuss their implementation into programmable metamaterials.
The Section ‘State of the art of materials systems with self-sealing and/or self-healing function’ presents the results of our detailed literature research about biomimetic materials systems with self-sealing and/or self-healing function and a summary of the engineering solutions for self-sealing and/or self-healing principles, using different materials and mechanisms. The detailed literature review helps to clarify the difference between the definitions and understanding of biologists and engineers for self-sealing and self-healing functions. In addition, reviewing the biological and engineering solutions for the self-sealing and/or self-healing function from the same point of view, reveals the new principles from biological models and organises the available tools in engineering to be implemented in a materials systems, such as programmable mechanical metamaterials.
The Section ‘Methodology and framework’ briefly introduces the selected plant species with a self-sealing function that served as biological models in this study. The novel methodology based on structured list of questions are introduced to understand and extract detailed self-sealing processes in biological systems.
The Section ‘Self-sealing process control flow’ introduces the flow chart of self-sealing, which is the core of this article. The overall process control flows are provided to demonstrate the various functional principles of self-sealing of the three selected plant models exhibiting different self-sealing mechanisms based on hydraulics, mechanical instabilities, and sap release. The detailed flow chart containing the steps and sequences of the self-sealing process exhibited by the three plants is provided in the ‘Biological section’ of the control flow.
The Section ‘Available technical and engineering tools for designing programmable mechanical metamaterials’ illustrates the available design space of mechanical metamaterials for implementation in engineering solutions. A detailed overview of the information about the possible and available structural and functional design of mechanical metamaterials by considering their manufacturing methods and application fields are collected and categorised.
The Section ‘Example of generating mechanical metamaterial based on Aristolochia macrophylla self-sealing concept’ presents an example of generating mechanical metamaterials by following the detailed biological flow chart in Section ‘Self-sealing process control flow’ and available design space of mechanical metamaterials categorised in Section ‘Available technical and engineering tools for designing programmable mechanical metamaterials’. Based on the self-sealing concepts of Aristolochia macrophylla with sealing cells squeezing into fissures to fill the gap, unit cells for circular and rectangular patterns are designed and the behaviour of the corresponding metamaterial during the crack closure are simulated by finite element method and the manufactured samples are tested under real conditions.
The Section ‘Discussion’ discusses the available mechanisms and properties of the programmable mechanical metamaterials and the potential solutions for the described self-sealing plant models, which can be reached by using programmable mechanical metamaterials. To conclude, the difficulties of implementing the proposed methods for self-sealing by using programmable mechanical metamaterials systems for real applications will be discussed.
In view of the interdisciplinary nature of the publication between natural sciences and engineering, we provide a glossary at the end of the article defining a selection of ambiguous technical terms in the context of biology and materials science.
State of the art of materials systems with self-sealing and/or self-healing function
Biomimetic materials
In Tables 1–4, we present a compilation of current biomimetic materials with self-sealing and/or self-healing function and the associated key references on the basis of a literature research. We specify the biological model and the functional principle of self-sealing or self-healing as described in the respective key publications. Unfortunately, these details often remain very vague. We also cannot make any statements about what kind of abstraction (cf. Section ‘Biomimetic approaches’) took place in the respective biomimetic material developments, as they are not explicitly mentioned by the authors. In addition, we hypothesise the evolutionary advantage of these traits for the biological model. We have not included all those materials systems in which organisms are directly involved in self-sealing and self-healing, because according to our definitions (Speck et al., Reference Speck, Speck, Horn, Gantner and Sedlbauer2017), these would not be biomimetic but biotechnological solutions, such as bacteria in self-healing concrete (Van Tittelboom and De Belie, Reference Van Tittelboom and De Belie2013; De Belie et al., Reference De Belie, Gruyaert, Al-Tabbaa, Antonaci, Baera, Bajare, Darquennes, Davies, Ferrara, Jefferson, Litina, Miljevic, Otlewska, Ranogajec, Roig-Flores, Paine, Lukowski, Serna, Tulliani, Vucetic, Wang and Jonkers2018). Some publications even do not specify a biological model at all, as the authors consider self-sealing and self-healing to be life-like functions or capabilities. We have also not included such materials systems in our compilation (Tables 1–4).
Table 1. Overview of self-sealing and self-healing principles in biological models, the attributed evolutionary benefit and the biomimetic materials systems with self-sealing or self-healing function (adapted from Speck and Speck, Reference Speck and Speck2019).

Table 2. Overview of self-sealing and self-healing principles in biological models, the attributed evolutionary benefit and the biomimetic materials systems with self-sealing or self-healing function (adapted from Speck and Speck, Reference Speck and Speck2019).

Table 3. Overview of self-sealing and self-healing principles in biological models, the attributed evolutionary benefit and the biomimetic materials systems with self-sealing or self-healing function (adapted from Speck and Speck, Reference Speck and Speck2019).

Table 4. Overview of self-sealing and self-healing principles in biological models, the attributed evolutionary benefit and the biomimetic materials systems with self-sealing or self-healing function (adapted from Speck and Speck, Reference Speck and Speck2019).
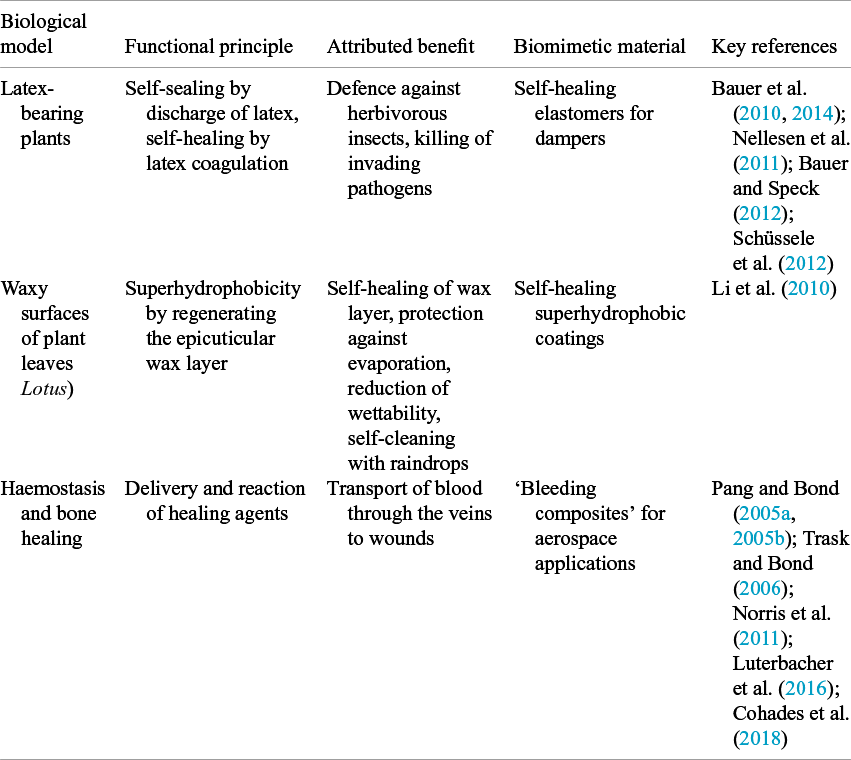
Self-sealing and/or self-healing in technology
Tables 5–10 summarise the engineers’ solution of self-sealing and/or self-healing principles, various materials, and/or technologies. As described above, the longer-lasting self-healing phase occurs after rapid self-sealing. In Tables 5–10, we attempted to summarise the result of our literature research for the self-sealing phase. In the past, engineers did not clearly differentiate between self-repair, self-sealing, and self-healing. Therefore, the authors had to interpret the published results and used the definitions provided in Section ‘Definition and quantification of self-repair, self-sealing, and self-healing’ (for details, see also Speck and Speck, Reference Speck and Speck2019) when assembling these tables. However, how to achieve further significant breakthroughs in self-sealing and/or self-healing has been a major issue for engineers to consider in recent years.
Table 5. Overview of self-sealing principle, various materials, and technologies.

Table 6. Overview of self-healing principles, various materials, and technologies.

Table 7. Overview of self-healing principles, various materials, and technologies.

Table 8. Overview of self-healing principles, various materials, and technologies.

Table 9. Overview of self-healing principles, various materials, and technologies.

Table 10. Overview of self-healing principles, various materials and technologies.

Designing self-sealing into programmable mechanical metamaterials
Studies to date reveal that all of the mechanisms of self-sealing and self-healing found in different plants are complex, coordinated, and have processes based on their hierarchical and modular organisation. This is true for both internal and external wounds (cf. Section ‘Selected plant models with a self-sealing function’). From a material scientist’s point of view, plants can be regarded as materials systems that consist of a multitude of tissues, which in turn, are composed of cells. Although the cell walls of plant cells are formed from a limited number of components (e.g., pectins, cellulose, hemicellulose, proteins and in some cases also lignin), they exhibit an astonishing range of mechanical properties and functions. However, because of this structure, plant tissues are not considered simple materials, but rather are structural materials (Wegst et al., Reference Wegst, Bai, Saiz, Tomsia and Ritchie2015). In computer science the above-mentioned processes are established in form of algorithms. In classical materials, algorithms are rather difficult to implement because there is no framework to physically encode them into the system. However, in programmable mechanical materials, this is made possible and may be the way forward towards engineering self-sealing into applications.
Mechanical metamaterials are human-made materials structured on a mesoscopic level and exhibit mechanical properties that cannot normally be found in natural or conventional materials (Rafsanjani et al., Reference Rafsanjani, Akbarzadeh and Pasini2015; Kelkar et al., Reference Kelkar, Kim, Cho, Kwak, Kang and Song2020). Such extraordinary mechanical properties include bistability, tunable stiffness, vanishing shear modulus in pentamode structures, negative compressibility, negative thermal expansion and auxetic behaviour, etc. Mechanical metamaterials are divided into the following categories: strong-lightweight, pattern transformation with tunable stiffness, negative compressibility, pentamode metamaterials, and auxetic metamaterial (Specht et al., Reference Specht, Berwind and Eberl2020). Mechanical metamaterials increase the design space of artificial materials, where the materials volume is so finely resolved, in the form of a unit cell, that the volume itself acts under static or dynamic loading like a continuum. The exceptional mechanical properties of mechanical metamaterials can be attributed to the geometry and connection of the unit cells, rather than the composition of the material (Fischer et al., Reference Fischer, Hillen and Eberl2020). From an overall view, a mechanical continuum appears to be in action through the concerted reaction of the unit cell system (Fischer et al., Reference Fischer, Hillen and Eberl2020).
Programmable materials provide a framework for implementing algorithms through mechanical or molecular mechanisms. Mechanical metamaterials with programmable functions can enable the integration of conditional behaviours into artificial functional materials systems. Programmable mechanical metamaterials will allow us to integrate tunable functions and logical conditions (e.g., if condition) into materials. Even their fabrication, properties and functionalities can still be modified (Specht et al., Reference Specht, Berwind and Eberl2020). The advantage of using programmable mechanical metamaterials is that a logical framework can be constructed to realise complex functions and mimic the reaction of living materials systems to damage. Therefore, there is a possibility that they could be designed for specific topology, nonlinearity, and geometry to drive the further realisation of programmability for self-sealing (Coulais et al., Reference Coulais, Kettenis and van Hecke2018).
In other words, mechanical metamaterials greatly support programmable mechanical metamaterials in the design space. For instance, the programmable mechanical metamaterials which have been developed thus far consist of a hierarchically auxetic unit cell with the logical condition (Berwind et al., Reference Berwind, Kamas and Eberl2018). As a result, reversible and nonlinear functions can be achieved. Therefore, we are in reach of enabling more life-like self-sealing in engineering applications through the programmable mechanical materials with built-in logical conditions, for example, flexibility to adjust strategies for dealing with damage. Biological models are able to provide inspiration to make programmable mechanical metamaterials accessible for potential applications in self-sealing and manage the damage independently and actively.
Methodology and framework
Selected plant models with a self-sealing function
We selected three plant species, which have served as models for the development of bio-inspired self-sealing products in previous studies. Delosperma cooperi N.E.Br. (hereafter D. cooperi) belongs to the Aizoaceae family and is native to highland regions in South Africa. Xeromorphic adaptations to the dry-winter climate include succulent leaves, which can store water, and rapid self-sealing of external damage by deformation of the entire leaf, which prevents dehydration (Hesse et al., Reference Hesse, Kampowski, Leupold, Caliaro, Speck and Speck2020). Aristolochia macrophylla Lam. (hereafter A. macrophylla) belongs to the plant family Aristolochiaceae and is native to eastern United States. Self-sealing of internal damage in the stems takes place by parenchymatous sealing cells that squeeze into growth-induced fissures of the ring of strengthening tissue (Busch et al., Reference Busch, Seidel, Speck and Speck2010). Euphorbia tirucalli L. (hereafter E. tirucalli) belongs to the latex-bearing family Euphorbiaceae. It is a succulent, hardy green shrub native to semi-arid regions of Africa. External damage is sealed by the discharge of latex. In some cases, the stems remained in the state of a permanent latex plug, in other cases, subsequent healing took place by the formation of a boundary layer of lipophilic substances (Anandan et al., Reference Anandan, Rudolph, Speck and Speck2018).
Structured list of questions
As noted, the greatest challenge in transferring principles and concepts between biological models and technical applications is the lack of a common language. Transferring the self-sealing ability from plants into metamaterials requires first an understanding and an ability to decipher the functions and underlying principles of self-sealing in the selected plants. Therefore, we first needed to create an intimate understanding of the biological model. To do so, we generated a list of questions to collect detailed data about the three selected plants which serve as our materials in this article. These questions were devised by engineers and were aimed towards biologists. The questions aim to uncover the data required for designing programmable mechanical metamaterials with desired functions such as self-sealing. More specifically, in the context of this study, the questions aim to interpret the geometric, anatomical and mechanical properties, and functional principles of the selected biological models before, during and after the sealing process. To have solid information about the entire detailed self-sealing process of the selected plants, the questions are divided into three main sections: ‘Inputs’, ‘Operations’ and ‘Outputs’. It is worth noting that the changes during the self-healing phase were ignored and we only considered the results which occurred during the self-sealing phase in the questions.
-
A. Inputs
The first set of questions target the most general and initial information about the geometric, anatomical, and mechanical properties of the plants. The questions in the ‘Inputs’ section aim to extract detailed information of the intact plant (before damage) from an engineering point of view. The resulting information from this set of questions would fulfil the essential information for sketching the structural characteristics of the corresponding programmable mechanical metamaterial. The questions are formulated as follows:
-
A.1 What are the structural characteristics of the plant when it is intact?
-
A.1.1 What is the dominant geometry of the inner structure?
-
A.1.2 Which tissue patterns do we find?
-
A.1.3 How is the connection between different cells?
-
A.1.4 Which material phases are involved?
-
-
A.2 What are the mechanical properties of the plant material and tissue?
-
A.2.1 How is the mechanical behaviour of the plant material and tissue?
-
A.2.2 How deformable is the plant material and tissue?
-
-
A.3 What are the size scales in the plants?
-
A.3.1 What is the size scale of the responsible structure for sealing?
-
A.3.2 What is the maximum size of damage which the plant can seal?
-
A.3.3 What is the size of the smallest part of the responsive structure?
-
-
-
B. Operations
The second line of questioning targets the ‘Operations’ of the plants. This means it focusses on the actions the plants perform to cope with the incoming damages and the corresponding mechanisms for these actions. An action in this section is considered to be everything that occurs from preparing to deal with the damage to the end of the self-sealing process. The questions in the ‘Operations’ section aim to extract the details of the changes that occur during the sealing procedure and discover what is mainly causing these changes. This detailed knowledge can be utilised to organise and program the functional behaviours of the mechanical metamaterial to produce a programmable mechanical metamaterial with self-sealing capability. The questions are formulated as follows:
-
B.1 What kind of preconditions must be created, so that the plant can react to damage?
-
B.1.1 What is the energy source that the plant uses for the self-sealing process?
-
B.1.2 How does the plant store energy for the self-sealing process?
-
B.1.3 What kind of materials does the plant use for the self-sealing process?
-
-
B.2 What changes are happening during the self-sealing process?
-
B.2.1 Are there any structural changes in the plant?
-
B.2.2 Are there any movements (change of position or transport of liquid) happening inside the plant?
-
-
B.3 What are the main reasons for the initiation of the changes for self-sealing processes?
-
B.3.1 What is the reason for local/global structural changes in the plant?
-
B.3.2 Why do the movements occur inside the plant?
-
-
-
C. Outputs
The last line of questions targets the final results and outcomes in the sealed state of the plants. In addition, it collects the time scales and speed of the whole self-sealing process from the ‘Operations’ section. The questions in the ‘Outputs’ section to evaluate the self-sealing process and observe the final results are the following:
-
C.1 What are the temporary changes after self-sealing process?
-
C.1.1 What are the results of self-sealing on the functionality of the plant?
-
C.1.2 How fast is the self-sealing process done?
-
C.1.3 What are the results of the self-sealing on mechanical properties of the plant?
-
-
C.2 What are the permanent changes after the self-sealing process?
-
C.2.1 What are the results of the self-sealing process on the structure of the plant?
-
-
The chart of the designed list of questions with examples of possible targeted answers has been presented in Figures S1–S3 of Supplementary Material.
Self-sealing process control flow
Introduction of the flow charts
The flow chart (Figure 1) illustrates the general process of the entire sealing system. It also expresses simple conditional control statements to classify the different sealing conditions while coping with inflicted damages. As the initial phase of the entire process, it is necessary to determine whether the whole system needs to close the crack. If the damaged area does not need to be closed or the damage size is too large to be closed, other concepts of dealing with damage come into play such as guiding the crack path, increasing fracture toughness, or generally preparing the materials system beforehand to resist against crack propagation and failure of the whole materials system (Cox et al., Reference Cox, Blevins, Drisko, Qi, Ding, Fiedler-Higgins, Long, Bowman and Killgore2019; Tao et al., Reference Tao, Li, Yudhanto, Alfano and Lubineau2022). For this reason, the severity of damages should be considered. In the case of severe mechanical damage, guiding crack initiation and propagation may be able to reduce the negative effects of the cracks and may even avoid catastrophic damage. On the other hand, it will follow the mainline to the next step for most of the cases with moderate mechanical damage. And then, one can determine whether or not the crack needs to be closed. When the crack closure is needed, then it starts to enter the sealing systems. The entire sealing process according to their dependency on external energy or material can be divided into the self-sealing and sealing system, which depends on whether the reaction and triggering system is spontaneous or not. The following subsection describes the flow charts for self-sealing systems and the available tools for triggering mechanisms within engineering.

Figure 1. A flow chart illustrating the general process of the entire sealing systems.
We present the results from our first fundamental question, first scientific question ‘How do the self-sealing principles of our selected plant models differ?’, in Sections ‘Delosperma cooperi’, ‘Aristolochia macrophylla’, and ‘Euphorbia tirucalli’ and in Figures 2–4.
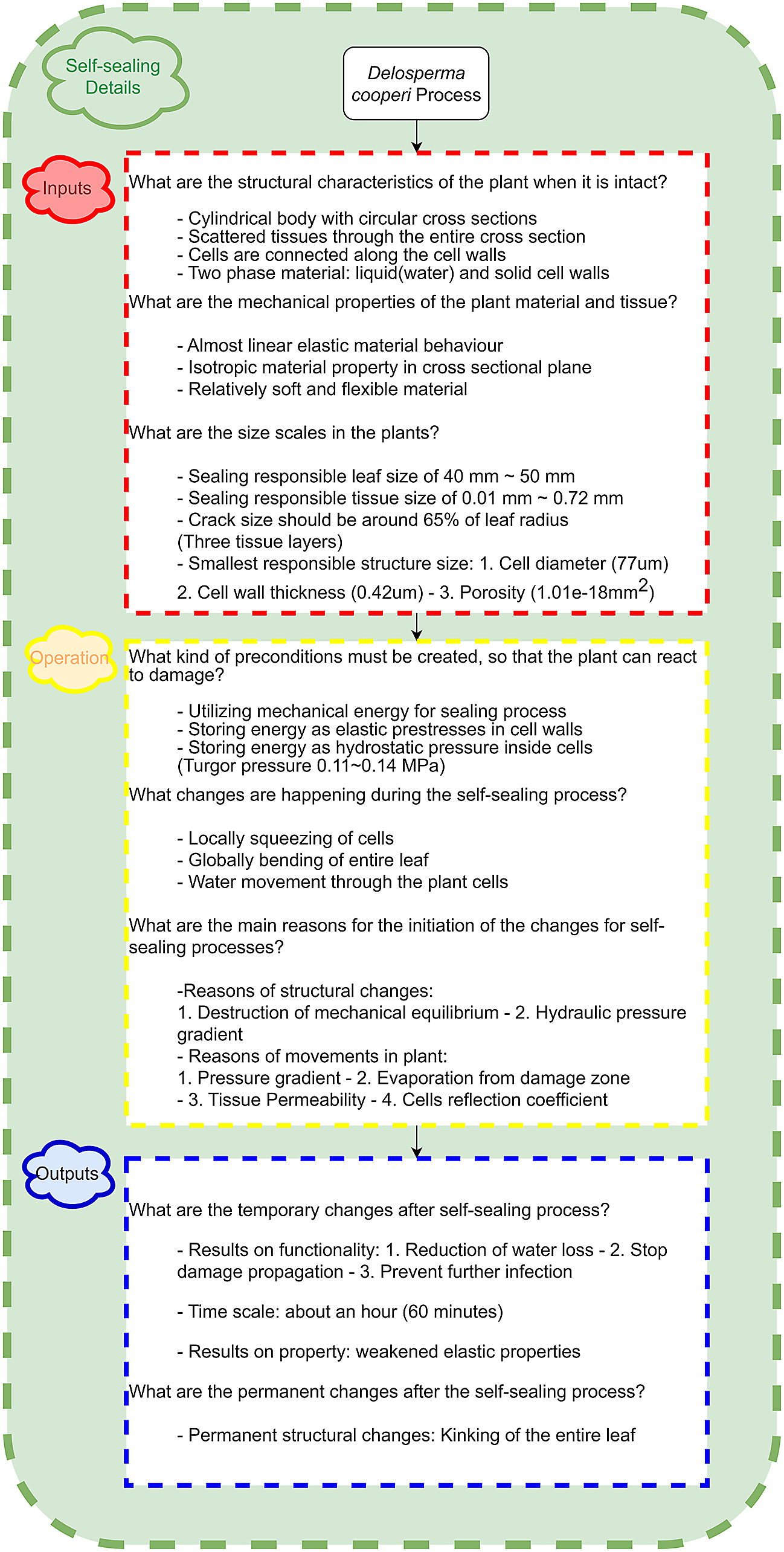
Figure 2. The answers of the questions for Delosperma cooperi plant.
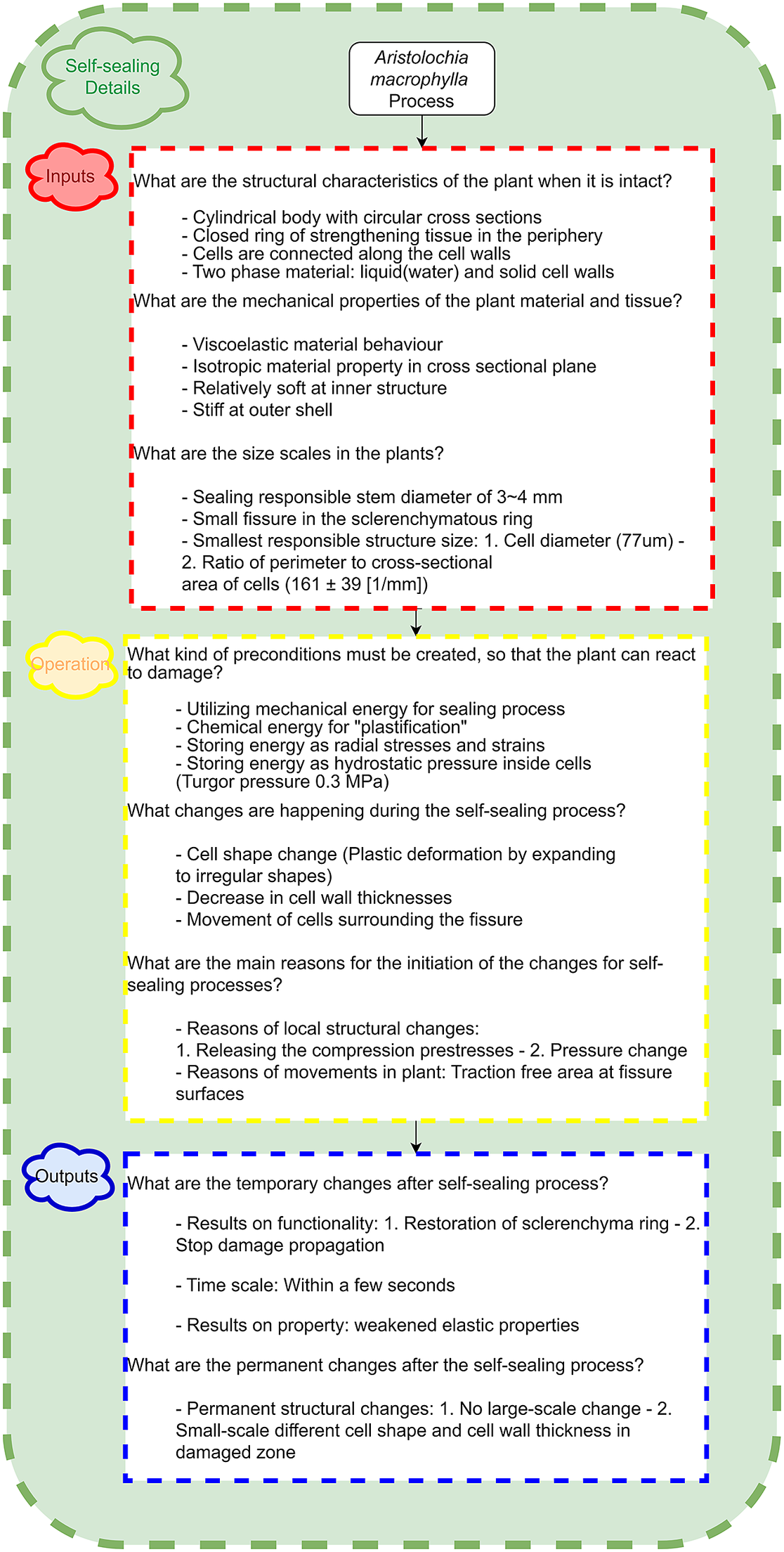
Figure 3. The answers of the questions for Aristolochia macrophylla plant.

Figure 4. The answers of the questions for Euphorbia tirucalli plant.
The list of questions, introduced in Section ‘Structured list of questions’, was implemented then to extract the detailed described three steps of the process flow chart. The questions were answered with the assistance of a biology expert and by completing a detailed literature review focussing specifically on the selected biological models. The answers for the questions are either directly extracted from the literature or inferred from the results and explanations of the research. The final detailed answers to the questions are presented in Figures 2–4 in three sequential sections: ‘Inputs’, ‘Operations’, and ‘Outputs’. The answers to the questions in the ‘Inputs’ section were mostly extracted from anatomical description and mechanical response of the corresponding plant from different size scale perspectives. These answers reveal the required qualitative and quantitative information for designing and manufacturing the corresponding programmable mechanical metamaterial. The plant material characteristics on a small scale, such as cell walls, define the mechanical properties of the base/bulk material of the corresponding mechanical metamaterial. The same material characteristics in larger scales (e.g., plant leaf) represent the metamaterial target mechanical properties which is the main aim in designing the unit cells. All of the metamaterials are based on the tessellation of periodic or non-periodic unit cells. Therefore, it is beneficial to have insight into the cellular geometry, shape, and connectivity of hierarchical cellular patterns of the inner structures of the plant. This is because it can offer inspiration for the fundamental design of the unit cells of the metamaterial so that it can provide similar mechanical characteristic as the plant. The final important aspect that the questions aim to explain is the size scale. This plays a very critical role in selecting the appropriate manufacturing technique that would be able to produce the designed mechanical metamaterial structure. The smallest and largest size scales collected from the responsible structure of the plant represents the maximum resolution and capable production volume of the manufacturing technique.
The descriptive responses to the key questions within the ‘Operations’ section are derived from the changes which happen during the gradual growth of the plant, as well as the behaviour of the plant during the self-sealing process. These answers evoke the needed actions and their underlying mechanisms that should be implemented in the designed mechanical metamaterial to program and organise it to yield the desired behaviour and function. The most important factors that allow plants to quickly and efficiently self-seal any damage are the concept of energy management, energy type, how it is stored and distributed in the plant, which includes, for example mechanical or chemical energy, the location of the stored energy, the magnitude of the energy, etc.
The biological model approach towards providing and using energy should be the same as the one implemented into the programmable mechanical metamaterial for providing energy for the required actions for the sealing mechanism. The mechanism which initiates the self-sealing process in plants is the other key factor that defines the triggering system category and its process in programmable mechanical metamaterials. After damage has been applied, the local structural changes happen during the sealing procedure, and the main causes for these changes specify the target local behaviour of the unit cells. On the other hand, the global changes in plants structure defines the global behaviour of the corresponding metamaterial, which is a result from the concerted interaction of the unit cells with each other. The structural changes and motions of the plant on all hierarchical levels have to be directly reflected in the target structural behaviour of the metamaterial and its unit cells. On the other hand, the causes of these local and global changes describe the boundary and loading conditions of the programmable mechanical metamaterials, which are also necessary for designing the corresponding unit cells.
The evaluation of the final outcomes and sealing efficiency (Mylo et al., Reference Mylo, Krüger, Speck and Speck2020), extracted from the responses to the questions within the ‘Outputs’ section, gives the opportunity to define the quality and usability of the final designed programmable mechanical metamaterial for a specific application. Comparing the final condition of the plants after completing self-sealing to their initial conditions, in terms of the mechanical properties and functionality, clarifies the effectiveness of the sealing mechanism that the selected plant models use for coping with damages. This evaluation illuminates the possible application fields for the corresponding programmable mechanical metamaterials, which is designed based on the self-sealing concept of our biological model. In addition, the temporary and permanent changes of the plants made by the sealing mechanism, add other restrictions to the application field of the designed programmable mechanical metamaterials, which needs to be considered and enhanced in the next steps of development. Not least of all, the different time scale of the sealing procedure for each biological model, which due to their specific sealing mechanisms, exhibits a huge impact on the scalability and applicability of the programmable mechanical metamaterials with equivalent sealing mechanism.
The answers from the three sections reveal some overlapping components for the selected biological models as well as some exclusive and unique factors for each plant model. The overlapping qualities are considered incommon features of the biological models, which should be implemented directly as basic components of the aimed programmable mechanical metamaterial. By looking at the ‘Input’ box, which is presented in the first row (red boxes) of the process control flow in Figures 2–4, one can see that all of the selected plant models have a similar cylindrical geometry with circular cross-sections. In addition, the plant tissues, which consist of hierarchically interconnected cells, are symmetrically distributed across the cross-section (Busch et al., Reference Busch, Seidel, Speck and Speck2010; Anandan et al., Reference Anandan, Rudolph, Speck and Speck2018; Speck et al., Reference Speck, Schlechtendahl, Borm, Kampowski and Speck2018) and generate transversely isotropic behaviour in large-scale mechanical response. Although these characteristics would directly affect the design of the mechanical metamaterial, they were not considered a limitation of the design. In general, mechanical metamaterials, due to their symmetrical unit cells in two or three dimensions, in conjunction with their periodic boundary conditions, are able to provide orthotropic mechanical properties in a different geometrical manner. On the other hand, according to the information that was collected in ‘Outputs’, which is presented in the last row (blue boxes) of the process control flow in Figures 2–4, all of the selected biological models are not able to recover the mechanical properties of the intact state and this limitation also is generally applied to the corresponding mechanical metamaterials.
The differing and individual features of the plant models were transferred to a flow chart to generate a cascade of information from the initial condition, followed by the actions which led to the final condition of the self-sealing procedure for different plant models with distinct self-sealing mechanisms. The flow chart of the self-sealing processes (otherwise called self-sealing systems), which organises the most significant elements and important factors of each process, was created from the detailed answers of the questions and presented in Figure 8. In the following subsection, the generation of blocks for the flow chart from detailed answers of questions are described for each plant model. To define these blocks, each main step (‘Inputs’, ‘Operations’, and ‘Outputs’) has been broken down into smaller and manageable sub-steps, which is achievable with the available engineering solutions especially mechanical metamaterials. It is important to mention that the sub-steps (flow chart building blocks) should be defined independently but be connected to each other in parallel, which enables different features and characteristics to work together to fulfill the aim of the corresponding main step (‘Inputs’, ‘Operations’, and ‘Outputs’). The analogy from informatics would be to identify generalisable code segments and algorithms as classes in programming languages.
Delosperma cooperi
Self-sealing in the succulent leaves of D. cooperi is secured by two functional principles: (1) hydraulic shrinking and swelling is the main driving forces and (2) growth-induced mechanical pre-stresses in the tissues that can speed up the self-sealing motion (Konrad et al., Reference Konrad, Flues, Schmich, Speck and Speck2013; Klein et al., Reference Klein, Hesse, Boljen, Kampowski, Butschek, Speck and Speck2018; Speck et al., Reference Speck, Schlechtendahl, Borm, Kampowski and Speck2018). In general, all plants store energy by creating a hydraulic over-pressure (turgor) through their cell sap inside the plant cell, whose semipermeable cell membrane is surrounded by a rigid cell wall. Since all cells are interconnected, they form tissues that store energy by being either under pre-tension (e.g., epidermis, fibres, and vascular bundles) or pre-compression (e.g., parenchymatous tissues such as chlorenchyma, specialised for photosynthesis, and hydrenchyma, specialised for water storage). Prerequisites for the self-sealing motion of the intact leaf of D. cooperi are the established equilibria of turgor-induced pressures and mechanical pre-stresses in the centripetally arranged tissues, which are destroyed by the damage (Figure 5). Starting with local effects at the wound site (e.g., rolling-in of the wound edges, loss of a water droplet), a global effect (e.g., deformation of the entire leaf) can be observed. These global effects arise from the hydraulic process resulting from both the tissue permeability to water and the relative permeability of a cell membrane to solutes (reflection coefficient) (Klein et al., Reference Klein, Hesse, Boljen, Kampowski, Butschek, Speck and Speck2018), and from the mechanical instability resulting from the continuous transitions between the individual cells of the various tissues (Konrad et al., Reference Konrad, Flues, Schmich, Speck and Speck2013).

Figure 5. Self-sealing principle of the succulent leaves of Delosperma cooperi based on mechanical pre-stresses in the five centripetally arranged tissue layers with various thickness layer. (a) Unstained microscopic image of a transversal section. (b–e) Schematic drawings showing (b) a transversal section and (c–e) longitudinal sections of adult leaves. (a–c) Sections depict intact leaves. (d) Leaf damaged in longitudinal or transversal direction (lightning arrow) resulting in a bending deformation (dark arrows). (e) Leaf damaged in circumferential direction (lightning arrows) resulting in a contraction deformation (dark arrows). Epidermis with window cells (ep), net of peripheral vascular bundles (nvb), and central strand of vascular bundles (cvb) are under pre-tension. Chlorenchyma (ch) and hydrenchyma (hy) are under pre-compression. The tissues and cells in the schematic drawings are not drawn to scale. Adapted from Konrad et al. (Reference Konrad, Flues, Schmich, Speck and Speck2013) and Speck et al. (Reference Speck, Schlechtendahl, Borm, Kampowski and Speck2018).
After the leaves of D. cooperi have been damaged, the self-sealing procedure starts and curtain actions take place sequentially resulting in a closure of the injury. The closing procedure is triggered by the disruption of both equilibria in the materials systems, which were in the stable minimum energy level in its intact state. The new condition after damage creates a hydraulic pressure gradient inside the interconnected cellular structure of the plant leaves. Immediately after the injury, a drop of water comes out of the wound. Water loss increases with higher values of tissue permeability leading to a faster and more pronounced injury closure. Furthermore, small values of the reflection coefficient lead to a more pronounced water loss, whereas high values of the reflection coefficient result in a faster and more pronounced incision closure (Klein et al., Reference Klein, Hesse, Boljen, Kampowski, Butschek, Speck and Speck2018). In addition, disrupting the mechanical equilibrium by cutting individual tissues, which are either under pre-tension or pre-compression, leads to a deformation (e.g., bending and contraction) of the entire leaf until a new equilibrium is established on the basis of the remaining undamaged tissues (Konrad et al., Reference Konrad, Flues, Schmich, Speck and Speck2013).
The final resultant conditions of the self-sealing procedure of D. cooperi can be observed as a large hydraulically and mechanically driven deformation of the entire leaf. This deformation brings the two surfaces of the crack together to close the gap in the wounded area, which prevents dehydration and protects against invading pathogens. Since the whole self-sealing process takes place within approximately an hour and the entire leaf contributes to the self-sealing mechanism, it is categorised in the ‘slow time scale’ and ‘large size scale’ categories compared to the mechanisms of the other biological models.
Aristolochia macrophylla
The initial conditions of the A. macrophylla plant show a hierarchical multi-cellular structure. One-year-old stems posses a central parenchymatous pith, separated areas of vascular tissue, and a peripheral closed ring of sclerenchyma embedded in an inner and outer parenchymatous cortical layer (Figure 6a). Energy is stored by means of turgor pressure in the parenchymatous tissues and by means of mechanical elastic energy as radial and tangential stresses and strains in the soft and strengthening tissues, respectively.

Figure 6. Self-sealing principle in the liana stems of Aristolochia macrophylla based on self-sealing cells. Panels (a) and (b) are schematic drawings. (a) Transversal section of a one-year-old stem with a closed ring of sclerenchyma tissue (sc). (b) Two-years-old stem with increased conducting tissue (ct) that results in several ruptures (ru) of the sclerenchyma ring. (c) Microscopic image showing a cortical sealing cell (asterisk, highlighted in colour) squeezing into a fissure of the sclerenchyma ring. (ru) rupture in the sclerenchyma ring, (sc) sclerenchyma ring, (pi) pith, (ct) conducting tissue consisting of phloem and xylem, (co) cortex, (ep) epidermis. The tissues in the schematic drawings are not drawn to scale.
The self-sealing process of A. macrophylla starts in two-years-old stems with an increase in vascular tissue caused by the additional growth ring, which by its location within the closed peripheral sclerenchyma ring leads to its rupture (Figure 6b). This destruction of the stress equilibrium leads to a fast internal reaction of the adjacent parenchymatous cortex cells. Since the cell walls are under high compressive stresses immediately after the formation of a fissure in the internal tissues, a stress (or strain) gradient is distributed around the damaged area. The fracture in the tissues creates a small traction area at the damaged zone (crack surfaces), which facilitates the soft cells around the crack surfaces to deform in specific directions to fill the gap of the crack (Figure 6c). As neighbouring cells deform into irregular shapes, the cell walls are stretched and their thickness decreases (Busch et al., Reference Busch, Seidel, Speck and Speck2010). The turgor pressure of the neighbouring cells accelerates the procedure of swelling and deforming of the sealing cells.
Finally, after the adjacent parenchyma cells have expanded and squeezed into the crack, they obtain irregular shapes as a result of initial elastic/visco-elastic deformation and subsequent plastic deformation that stabilises the new stress status. Subsequently, in the self-healing phase, the walls of these sealing cells are thickened and lignified, which secures the sealing and avoids crack propagation. The sealing process of A. macrophylla occurs within a couple of seconds and the size of the responsible structure is in micrometre scale, which categorises the sealing mechanism as very fast and small in terms of time and size scale.
Euphorbia tirucalli
Latex-bearing plants store the milky plant sap in laticifers under huge over-pressure (turgor) ranging from 1.5 MPa (Anandan et al., Reference Anandan, Rudolph, Speck and Speck2018) to 8 MPa (Buttery and Boatman, Reference Buttery and Boatman1966; Bauer et al., Reference Bauer, Gorb, Klein, Nellesen, von Tapavicza and Speck2014). If damaged, the laticifers, which lie in the stem periphery, are injured and the milky plant sap quickly oozes out – also because of the high over-pressure – and seals the wound (Figure 7). Similar to Hevea brasiliensis (D’Auzac et al., Reference D’Auzac, Prévôt and Jacob1995), latex particles and proteins packed in membranes float in the latex of the uninjured laticifers. Triggered by the pressure drop during the injury, the ‘membrane packaging’ bursts, so that the latex particles can cross-link with the proteins while discharging the milky latex. The coagulation becomes visible when the initially milky latex becomes transparent. The latex under over-pressure represents stored energy for the release of this particular plant sap. Moreover, we hypothesise that the high pressure in the laticifers generates high pre-stresses in longitudinal and radial directions of the plant stem. In the intact state, E. tirucalli, with multi-cellular structured stems and containing elongated tube-like network, facilitates the spreading of the high-pressure latex throughout the entire plant body.

Figure 7. Self-sealing principle of stems of Euphorbia tirucalli based on latex release. Schematic drawings showing transversal sections of (a) an intact and (b) an injured stem. (c) Transversal thin-section stained with Acridine orange that highlights lignified structures in bright yellow. (b,c) Immediately after the damage latex (la) fills the gap and can produce a permanent latex plug at the surface. (sc) sclerenchyma, (pi) pith, (ct) conducting tissue consisting of phloem and xylem, (co) cortical parenchyma with latex-bearing laticifers, (ep) epidermis. The tissues in the schematic drawings are not drawn to scale.
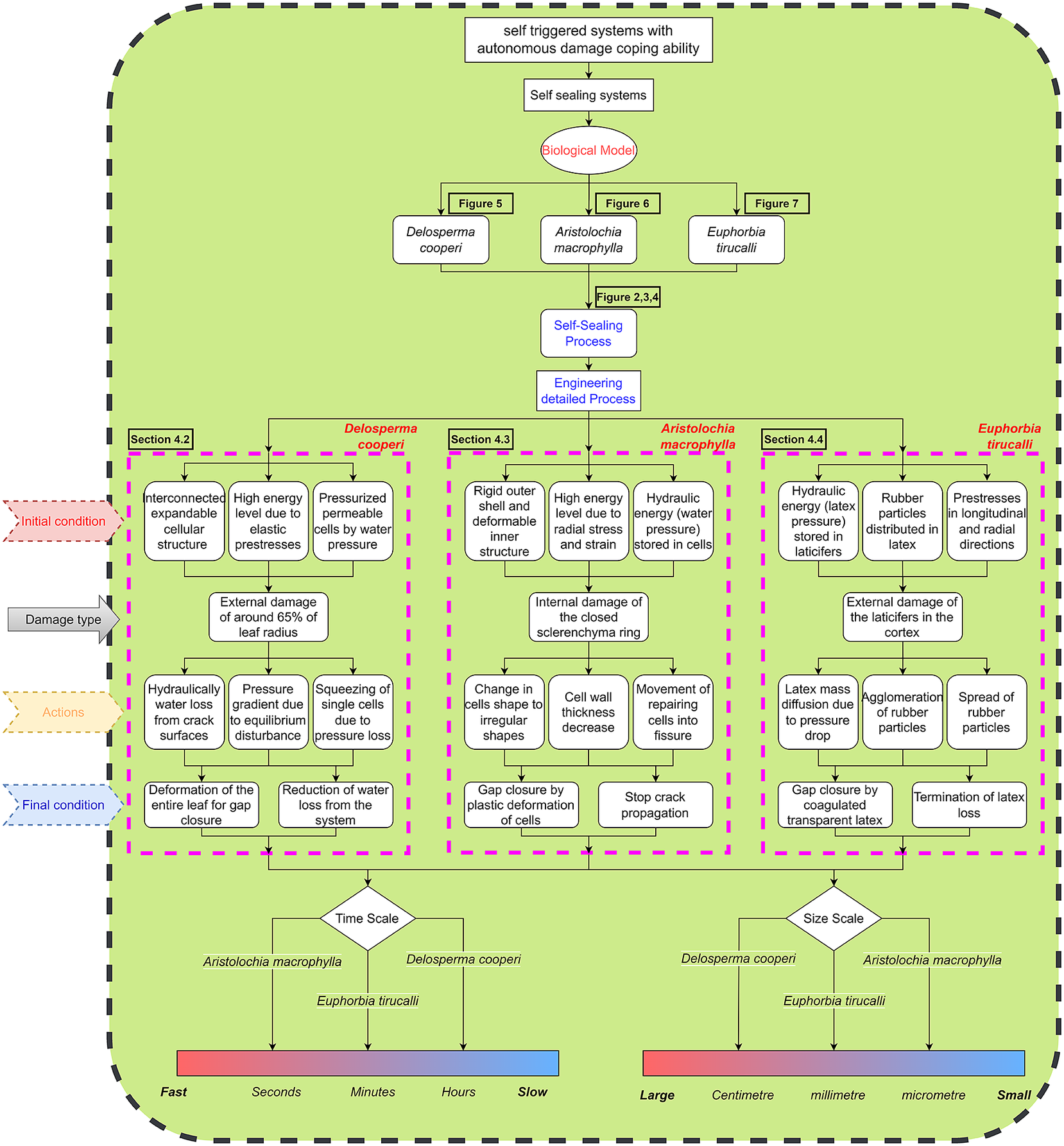
Figure 8. The flow chart of the self-sealing systems, which includes the main elements and important design factors.

Figure 9. Available technical and engineering tools for programmable mechanical metamaterials.
The wound reaction after damages to the cylindrical stems of E. tirucalli in transversal and longitudinal direction can take place in two different ways. First, the discharged latex initially seals the wound within minutes and then forms a permanent plug (Figure 7b). The size scale of self-sealing mechanism in this case is limited to a few millimetres. Bauer and Speck (Reference Bauer and Speck2012) found that in Ficus benjamina, the tensile strength of the bark in the wound area was significantly restored within 30 min. They found that the tensile strength decreased on average from
$25.1 \pm 3.8$
MPa (intact state) to
$10.6 \pm 1.3$
MPa (freshly injured state) and increased within 30 min to a significantly higher value of
$13.7 \pm 3.8$
MPa (sealed state), which is 55 % of the value obtained for uninjured bark. Second, some E. tirucalli plants loose the latex plug and start self-healing by forming a boundary layer of lipophilic substances (Anandan et al., Reference Anandan, Rudolph, Speck and Speck2018).
The discussed detailed process of self-sealing based on the comprehensive answers of the questions was illustrated as a sequential building block of the flow chart, which contains the key elements of three main steps of process (Figure 8). In Section ‘Available technical and engineering tools for designing programmable mechanical metamaterials’, we present a possible design space for exchanging these biological building blocks with engineering building blocks, by using programmable mechanical metamaterial concepts.
Available technical and engineering tools for designing programmable mechanical metamaterials
We answer our second scientific question, ‘Can we use flow charts as a method of abstraction to describe self-sealing processes within specific plants?’ in Sections ‘Structural design’, ‘Functional design’, ‘Manufacturing and application’, as well as in Figures 8 and 9. The next step in transitioning plant models into desired programmable mechanical metamaterials would be to substitute the building blocks of the developed flow chart (Figure 8) with engineering building blocks. To simplify the transfer process, these engineering blocks can be chosen to provide similar structural characteristics such as material properties, geometrical features along with the functional behaviours – namely triggering system type and target shape or geometry morphing. To achieve the flow chart with exchanged engineering blocks to get the self-sealing function in advanced engineered materials such as programmable mechanical metamaterials, first requires collecting and categorising the available tools for designing a new mechanism or materials system with the desired features. In the following, the authors attempt to categorise the three main steps of designing metamaterials based on the available examples in the literature. The categorised flow chart is shown in Figure 9. It is worth noting that successfully designing and fabricating programmable mechanical metamaterial by connecting individual building blocks would be a very challenging task. This is because it needs a large amount of tests and optimisations to see if the resultant behaves in a similar way to the target biological sample.
Structural design
From the structural point of view, the geometry of the basic elements of the metamaterials can be designed in different ways. Using repetitive unit cells with periodic boundary conditions is the most well-known method for designing the structure of the unit cells. Struts (or beams) are the simplest fundamental elements which are implemented to generate the two- and three-dimensional unit cells based on the periodic boundary conditions (Zhang et al., Reference Zhang, Qiu and Fang2008; Zheng et al., Reference Zheng, Lee, Weisgraber, Shusteff, DeOtte, Duoss, Kuntz, Biener, Ge, Jackson, Kucheyev, Fang and Spadaccini2014; Egan et al., Reference Egan, Gonella, Engensperger, Ferguson and Shea2017). The cross-sectional geometry of these struts and beams (such as circular, rectangular, or triangular geometries with solid and hollow configurations) plays a huge role on the final properties of the unit cells and their corresponding mechanical metamaterials. Plates and shells are the other fundamental elements that are utilised to generate three-dimensional repetitive unit cells. Connecting these elements could either create repetitive closed-cell structures (Kader et al., Reference Kader, Hazell, Brown, Tahtali, Ahmed, Escobedo and Saadatfar2020) or interconnected open cellular structures (Abueidda et al., Reference Abueidda, Al-Rub, Dalaq, Lee, Khan and Jasiuk2016). In addition, by folding and cutting thin-film plates, complex three-dimensional plate- and shell-based unit cells can be achieved (Zhai et al., Reference Zhai, Wu and Jiang2021). Periodically distributing holes and voids within a regular pattern is another method that provides three-dimensional repetitive unit cells as the building blocks of mechanical metamaterials (Wang et al., Reference Wang, Li and Zhou2016a). On the other hand, the metamaterial structures could also be constructed by non-periodic unit cells. One example of non-periodic metamaterials (Tarantino et al., Reference Tarantino, Zerhouni and Danas2019) would be random closed-cell porous architectures, which are created by introducing randomly distributed spherical voids with different sizes inside the bulk material. Another example would be spinodoid topologies, which are generated by inspiration of natural self-assembly processes and provide a vast design space (Kumar et al., Reference Kumar, Tan, Zheng and Kochmann2020; Zheng et al., Reference Zheng, Kumar and Kochmann2021). The large number of possible randomly generated topologies using non-periodic structures, enables the usage of machine learning methods and models to design the metamaterials with desired properties (Jiao and Alavi, Reference Jiao and Alavi2021). In the end, the gradient network and hierarchical combination of the mentioned structures expands the structural design space of mechanical metamaterials to achieve the final aimed features (Zheng et al., Reference Zheng, Smith, Jackson, Moran, Cui, Chen, Ye, Fang, Rodriguez and Weisgraber2016; Zhang et al., Reference Zhang, Wu, Fang and Zhang2021). By utilising the described design space, the target mechanical properties of the metamaterials such as stiffness (Yu et al., Reference Yu, Zhou, Liang, Jiang and Wu2018), strength (Bauer et al., Reference Bauer, Meza, Schaedler, Schwaiger, Zheng and Valdevit2017), toughness (Shaikeea et al., Reference Shaikeea, Cui, O’Masta, Zheng and Deshpande2022), Poisson’s ratio (Ren et al., Reference Ren, Das, Tran, Ngo and Xie2018) and etc. could be planed and generated.
Functional design
Most of the functions in advanced engineered materials are generated from a particular reaction of the materials system to a specific stimulus. A wide range of triggering systems have been developed by researchers by combining different materials and mechanisms within unit cells. These available triggering systems could be utilised to initiate particular predefined reactions in programmable mechanical metamaterials. Mechanical mechanisms are the most well-known and common triggers that could be built into the basic elements of a programmable mechanical metamaterial’s unit cells. Bistable beams (Che et al., Reference Che, Yuan, Wu, Jerry Qi and Meaud2017), bi-material struts (Janbaz et al., Reference Janbaz, Narooei, Van Manen and Zadpoor2020), and pressurised membranes (Chen and Jin, Reference Chen and Jin2018) are examples of mechanical triggers which are implemented in a unit cells design to react and initiate a process inside the materials system with physical interaction. The next most common triggering system is using thermal responsive actuators which react to heat exchange. Generally, these triggering systems are considered slow in terms of reaction time. Shape memory polymers and alloys (Yang et al., Reference Yang, Boorugu, Dopp, Ren, Martin, Han, Choi and Lee2019a), thermal responsive hydrogels (Ge et al., Reference Ge, Chen, Cheng, Zhang, Zhang, Li, He, Yuan, Liu, Magdassi and Qu2021), and liquid crystal elastomers (Korpas et al., Reference Korpas, Yin, Yasuda and Raney2021) are the most well-known thermal triggers that are implemented within unit cells. Moreover, chemical agents such as water, acids, and different solvents, could be applied to the design of the unit cells element to be triggered by chemical reactions (Liu et al., Reference Liu, Gu, Shan, Kang, Weaver and Bertoldi2016). One of the other popular chemical triggers are pH-responsive actuators, which also could initiate a mechanism inside a metamaterial unit cells (Bassik et al., Reference Bassik, Abebe, Laflin and Gracias2010). Using light as a trigger is another option that expands the possible triggering systems for metamaterials unit cells by connecting the optical energy to a chemical (Müller et al., Reference Müller, Zimmermann, Nyström, Burgert and Siqueira2020) or thermal (Zhao et al., Reference Zhao, Wu, Mu, Chen, Qi and Fang2017) response. Similarly, electrical triggering systems could induce various changes inside the unit cell structure (Zhu et al., Reference Zhu, Birla, Oldham and Filipov2020) via converting the electrical current to thermal, chemical, or also mechanical responses. In the end, to have faster triggering mechanisms, a mixture of magnetic particles with different elastomers, gels, and liquids, yields a magnetic responsive mechanism which can react to specific magnetic fields. The forces that result from the magnetic triggers are beneficial in terms of actuating a mechanism within the metamaterial structure (Chen et al., Reference Chen, Pauly and Reis2021). By considering the huge structural design space for metamaterials, in conjunction with the different available triggering mechanisms, designing a programmable mechanical metamaterial with specific function or ability becomes more convenient. In this regard, a lot of programmable mechanical metamaterials with different functions such as shape matching (Mirzaali et al., Reference Mirzaali, Janbaz, Strano, Vergani and Zadpoor2018), shape morphing (Neville et al., Reference Neville, Scarpa and Pirrera2016), liquid transferring (Dudukovic et al., Reference Dudukovic, Fong, Gemeda, DeOtte, Cerón, Moran, Davis, Baker and Duoss2021), wave propagation (Jin et al., Reference Jin, Khajehtourian, Mueller, Rafsanjani, Tournat, Bertoldi and Kochmann2020b), etc. are designed based on these triggering systems to react and initiate the implemented function.
Manufacturing and application
Additive manufacturing (AM) technology empowers the feasibility of manufacturing mechanical metamaterials because it carries many advantages in terms of fabricating complex geometries. One of the most commonly used additive manufacturing methods for fabricating complex architectures in metamaterials is the direct deposition of the melted material onto a substrate through a nozzle. The base materials for this method are typically made of thermoplastic materials (e.g., TPU, ABS, PLA, etc.) and the possible minimum feature size is approximately a few hundred micrometres. In addition, the filaments can be filled with different carbon, ceramic, and metallic particles/fibres to enhance the mechanical properties by creating a composite material (Farahani et al., Reference Farahani, Dubé and Therriault2016). Fused deposition modelling (FDM), direct ink writing (DIW), and ink-jet printing (IJP) are examples of the direct deposition method for fabricating metamaterials architecture (Walther et al., Reference Walther, Ortner, Meier, Löffelmann, Smith and Korvink2009; Kaur et al., Reference Kaur, Yun, Han, Thomas and Kim2017; Saadi et al., Reference Saadi, Maguire, Pottackal, Thakur, Ikram, Hart, Ajayan and Rahman2022). Other additive manufacturing techniques are also available for fabricating high-quality architected metamaterials in a wide range of sizes. Since these techniques are light-based processes, utilising the photo-polymerisation concept to create solid structures from a liquid resin, facilitates the design of micro- or nano-scale features to achieve complex structures in the order of a few hundred nanometres to several micrometres (Jang et al., Reference Jang, Meza, Greer and Greer2013; Bauer et al., Reference Bauer, Schroer, Schwaiger and Kraft2016). Stereolithography (SLA; Kodama, Reference Kodama1981), two-photon lithography (TPL; Deubel et al., Reference Deubel, Von Freymann, Wegener, Pereira, Busch and Soukoulis2004), digital light processing (DLP; Gauvin et al., Reference Gauvin, Chen, Lee, Soman, Zorlutuna, Nichol, Bae, Chen and Khademhosseini2012), and volumetric additives manufacturing (VAM; Shusteff et al., Reference Shusteff, Browar, Kelly, Henriksson, Weisgraber, Panas, Fang and Spadaccini2017) are the most well-known photo polymerisation manufacturing methods that are applied to produce metamaterials structures precisely. The powder fusion technique is another common additive manufacturing method that commonly uses a laser source to fuse powder particles by melting each layer by layer in a powder bed. This method enables the fabrication of metamaterial structures in metals and ceramics in which the shape, size, and distribution of the used powder, describe the quality and minimum printable feature size (Surjadi et al., Reference Surjadi, Gao, Du, Li, Xiong, Fang and Lu2019). Selective laser melting (SLM) (Sharma et al., Reference Sharma, Hiremath and Kenchappa2022) and electron beam melting (EBM) (Neils et al., Reference Neils, Dong and Wadley2022) are the most well-known examples of powder fusion methods that facilitate the manufacturing of metallic and ceramic based metamaterials. Besides the described possible additive manufacturing methods for fabricating designed metamaterials, some other conventional methods such as cutting and folding sheets (Silverberg et al., Reference Silverberg, Evans, McLeod, Hayward, Hull, Santangelo and Cohen2014; Tang et al., Reference Tang, Lin, Yang, Yi, Kamien and Yin2017), freeze-drying (Tian et al., Reference Tian, Yang, You, Wang, Ren, Zhang and Dong2022), interlocking assembly (Wang et al., Reference Wang, Li and Ma2016c) and etc. are also available for fabricating some metamaterial’s structures. The wide variety of aforementioned structural and functional capabilities of mechanical metamaterials in conjunction with the widely available manufacturing techniques for fabricating structures with complex architectures, make it possible to design programmable metamaterials for different applications in industrial fields such as aerospace, biomedical, etc. A programmable mechanical metamaterial with a specific function, such as self-sealing, could be achieved by selecting the appropriate structural features and combining them with the target functions with suitable triggering systems, as described in Figure 9. For generation of engineering building blocks for target programmable metamaterial with self-sealing ability, the selection of appropriate features and characteristics could be done by considering the definitions of sub-steps of the plants extracted from the list of questions and assembled into the biological flow chart (Figure 8).
Example of generating mechanical metamaterial based on Aristolochia macrophylla self-sealing concept
In this section, we attempt to design an example metamaterial and its corresponding engineering flow chart that has the self-sealing ability according to the biological models described in Section ‘Self-sealing process control flow’. We have chosen the plant model A. macrophylla for this example and focus on the self-sealing process of this plant to translate to the mechanical metamaterial system. As discussed in the previous section, the translation process should be done by replacement of the biological building blocks of the biological flow chart (Figure 8) by using the detailed process flow (Figure 3), with the appropriate available mechanical metamaterials systems features and characteristics (Figure 9). To make this translation from a biological system to an engineering system, the ‘structural design’, ‘functional design’, and ‘manufacturing’ steps of the engineering flow chart are defined as follows.
Structural design
As a general structural features for A. macrophylla, the structure of the plant consists of a circular rigid outer shell with the deformable inner scattered cellular structure. Therefore, the beam base unit cells with the similar aspect ratio of the plant cell walls are considered and interconnected to each other (Figure 10a,b). The metamaterial geometrical pattern of the metamaterial could be developed either in a circular manner (in radial and circumferential directions according to the pattern of A. macrophylla) or a general rectangular pattern (in horizontal and vertical directions), which makes it possible to implement it in various geometries. The solid peripheral ring (or square) can be designed to hold the internal structure under controlled boundary and loading conditions, similar to the ring of strengthening tissue in the plant stem. The isotropic elastic material properties are considered for the inner and outer shells based on the data of the material properties of the plants (Figure 3). The hyperelastic soft material and the elastic stiff material are selected for the inner cellular structure and the outer shell respectively to have a high relative stiffness according to the A. macrophylla plant stem (Figure 3).

Figure 10. Designed unit cell based on Aristolochia macrophylla structural characteristics. (a, b) Beam base unit cells for circular and rectangular patterns. (c, d) Corresponding metamaterial lattices for circular and rectangular unit cells by repeating in radial/circumferential or horizontal/vertical manner.
Functional design
Inspired by the pre-compressed parenchymatous tissues of A. macrophylla, in order to also have elastic energy storage ability in the inner structure of the metamaterial, we implemented a slight curvature in the beams of unit cells to have monostable beams that store the elastic energy during the compressive loading condition. Figure 11a,b shows the results of the finite element analysis of the unit cells under compressive loading. By applying the mechanical compressive load to the metamaterial structure, the whole system is energised by the deformation of the monostable beams. Figure 11c,d shows the results of the finite element analysis of the metamaterials after being energised under compressive loading. It is worth noting that only 5 % radial deformation is needed to store the energy in the whole metamaterial system. By preparing the initial conditions, the metamaterial system is being prepared to take action and deal with the damage. Figure 12a,b demonstrate the applied damage as a fissure in the internal cells of the mechanical metamaterial. After the damage is applied, the sealing process starts automatically due to the internal energy stored in the system. Based on the finite element simulations shown in Figure 12c,d, the surrounding unit cells of the damaged area are being deformed and get irregular shapes, resulting in filling the gap of fissure. This is exactly similar to the changes that occur during the self-sealing process in the stems of A. macrophylla (Figure 3, Operations).

Figure 11. The designed unit cells are prestressed in compression. Compression of the (a) circular and (b) rectangular unit cells. The prestressed (c) circular and (d) rectangular metamaterials.

Figure 12. Self-sealing procedure of the mechanical metamaterial based on the Aristolochia macrophylla concept. (a, b) Introduction of a fissure in some cells. (c, d) Self-sealing process. (e, f) Completed self-sealing procedure.
Manufacturing
To manufacture the designed metamaterial system, we selected fused filament fabrication (FFF) 3D printing (Ghavidelnia et al., Reference Ghavidelnia, Yin, Cao and Eberl2023) from the various available additive manufacturing methods to create the structure of the designed mechanical metamaterial. Two different filaments with soft hyperelastic and stiff elastic material properties (TPU 95A and PLA) are used to manufacture the inner structure and outer shell of the metamaterial. The scale of the metamaterial was chosen according to the limitation of the minimum printable feature of the 3D printer. Figure 13a,b illustrates the metamaterial in the intact form and Figure 13c,d illustrates the metamaterial in the final sealed state after the damage was introduced into the inner unit cells.

Figure 13. Manufactured metamaterials. Metamaterials with (a) circular and (b) rectangular patterns in the intact form. Metamaterials with (c) circular and (d) rectangular patterns in the final sealed state.
Finally, the summarised flow chart of the metamaterial with self-sealing function based on A. macrophylla (Meta-Aristolochia) is presented in Figure 14 to illustrate the selected blocks from the technical flow chart presented in Figure 9. It is worth mentioning that the videos from the finite element simulation and experimental demonstrations showing the self-sealing process of the design example mechanical metamaterial are available in the Supplementary Material. According to the experimental examinations of the designed mechanical metamaterial, by removing two inner unit cells as an introduction of a damage in the system, a quick response of sealing mechanism was observed causing the surrounding unit cells to be deformed and squeezed into the cracked area to fill the gap. It is worth noting that the completed sealed condition shown in Figure 13c,d was achieved after stress relaxation caused by the viscoelastic effect of the base material (TPU 95A). Hence, the overall self-sealing process of the manufactured samples could be evaluated successful as a minimal example and could be considered as a solution for applications that are vulnerable to impacts that cause local damage and loss of small parts from the materials system. The total amount of damage a system can compensate depends on the stored strain energy. The damage tolerance can be adapted during the design phase.

Figure 14. Summarised flow chart of the metamaterial with self-sealing function based on the Aristolochia macrophylla self-sealing concept.
Discussion
Evolutionary advantage of the self-sealing function for living organisms
Since damage of plants often cannot be avoided, we hypothesise a high evolutionary pressure on the development of functional principles to seal and heal wounds. Damage can be caused in many ways, for example, by growth, but also by wind, rain, snow, falling stones, flying parts, or passing animals. Since studies have shown that plants have evolved a variety of functional principles for self-sealing and self-healing wounds, it is likely that the different principles have evolved multiple times and independently in different plant groups. It can be assumed that it is evolutionarily advantageous for living organisms to rapidly self-seal wounds, thus preventing infestation of germs and/or dehydration. Additionally, a sealed wound allows more time for the subsequent long-term self-healing phase, in which metabolic substances (e.g., suberin, lignin), cells, and tissues can be formed. With respect to the body plan of the plant species (i.e., a set of morphological features common to many members of a phylum; Drost et al., Reference Drost, Janitza, Grosse and Quint2017), self-sealing can occur on various hierarchical levels. Self-sealing can range from the release of cell sap (e.g., latex in E. tirucalli, mucilage in cactus species), to the cell level (e.g., self-sealing cells of A. macrophylla) to the tissue level (e.g., rolling-in of dermal tissues at the wound edges) and the organ level (e.g., deformation of entire leaves of D. cooperi) (cf. Figure 2 in Speck and Speck, Reference Speck and Speck2019). Furthermore, self-sealing principles are also dependent on environmental conditions, such as the metal coordination-based cross-linking of proteins of byssal threads of marine mussels (Myrtilus sp.) in sea water (Krauss et al., Reference Krauss, Metzger, Fratzl and Harrington2013; Krogsgaard et al., Reference Krogsgaard, Behrens, Pedersen and Birkedal2013; Schmitt et al., Reference Schmitt, Politi, Reinecke and Harrington2015; Harrington et al., Reference Harrington, Jehle and Priemel2018) or the self-sealing of microfissures by a temperature-induced melting of waxes at the suture of the two fruit valves of Banksia follicles (Huss et al., Reference Huss, Schoeppler, Merritt, Best, Maire, Adrien, Spaeker, Janssen, Gladisch, Gierlinger, Miller, Fratzl and Eder2018a, Reference Huss, Spaeker, Gierlinger, Merritt, Miller, Neinhuis, Fratzl and Eder2018b). Moreover, the study by Anandan et al. (Reference Anandan, Rudolph, Speck and Speck2018) revealed various principles of rapid self-sealing in succulent plants that are native to semiarid or arid climates. For rapid wound closure, underlying structures must be in place prior to damage, such as the formation of pre-tension and pre-compression in tissues, turgor pressure in sealing cells, or the formation of plant sap in secretory cells that are stored under over-pressure (e.g., mucilage cells, laticifers). In contrast to physico-chemical principles of self-sealing, metabolism, that is, enzyme-catalysed chemical reactions, is a prerequisite for wound healing in plants. Plant metabolism includes photosynthesis, but also the formation of primary metabolites that are directly involved in normal growth, development, and reproduction, and secondary metabolites that are involved in ecological interactions and produced in response to stress (Rittinger et al., Reference Rittinger, Biggs and Peirson1987; Evert, Reference Evert2006; Vasyukova et al., Reference Vasyukova, Chalenko, Gerasimova and Ozeretskovskaya2011; Ikeuchi et al., Reference Ikeuchi, Favero, Sakamoto, Iwase, Coleman, Rymen and Sugimoto2019; Hoermayer et al., Reference Hoermayer, Montesinos, Marhava, Benková, Yoshida and Friml2020).
Abstraction through flow charts
Flow charts and control flows are made by systematically arranging meaningful predefined symbols to define and analyse a process or problem and its corresponding solution. Therefore, we implemented this method for abstracting data from our biological models in this work. On the other hand, because of their common language between different scientific fields, flow charts and control flows facilitate communication in interdisciplinary research and lead to effective and easy-to-understand interactions between collaborators. Hence, a biological model and its corresponding target function could be interpreted logically in a sequence of steps and described in key elements, which is defined and identified in an engineering field. Also, because of the simple structure of flow charts, possible mistakes and bugs can easily be discovered and debugged similar to how well-known programming languages operate. The history of flow charts is very old and the very first flow chart with the proper structure to describe a process flow was established by Frank and Lillian Gilbreth in 1921 (Gilbreth and Gilbreth, Reference Gilbreth and Gilbreth1921).
Although flow charts are commonly used for describing computer algorithms and computer programming, we aimed to apply them for describing the plant function ‘self-sealing’. One of the visionary goals of this article is to introduce this method as a successful technique to define new classes for the implementation of different functions in engineering and specifically in programmable mechanical metamaterials. Similar to the computer programming languages that provide a wide range of collections for different functions and classes, metamaterials with a various number of characteristics, properties and functions that can be categorised in classes to define and clarify the design space for metamaterials (Gamma et al., Reference Gamma, Johnson, Helm, Johnson and Vlissides1995). These classes aim to meaningful connect the available mechanisms in programmable mechanical metamaterials with the goal function. As an example, for these classes, the ‘self-sealing’ function could be considered as a class that provides different paths to reach this function by following the different biological models and implementing available mechanisms in programmable mechanical metamaterials. To achieve a successful class, all of the detailed basic elements, mechanisms, and their interactions in programmable mechanical metamaterials have to be clearly defined. It should be noted that from a mechanical design perspective, the definition of classes must be based on the manufacturing techniques and materials limitations. In this regard, the outcome of the class would be completely reliable in terms of functionality and productibility in real life.
Potential applications of self-sealing using programmable mechanical metamaterials inspired by plants
We discuss our third scientific question, ‘What chances and challenges occur by transferring self-sealing from plants into programmable mechanical metamaterials by means of flow charts?’ in the discussion in this section and Section ‘Programmable mechanical metamaterials framework’. In this section, we first discuss the potential applications of self-sealing using programmable mechanical metamaterials. The use of flow charts frees us from having to mimic the biological models. We can extract the critical information of the self-sealing process for the three selected plant models, which likely assist in the process of finding the available mechanisms of programmable mechanical metamaterials by using the flow charts.
For the self-sealing of D. cooperi, the deformation of the entire leaf is induced by disturbing both the turgor-driven equilibrium and the equilibrium generated by pre-stresses (cf. Section ‘Delosperma cooperi’). Several unusual deformation behaviours of programmable mechanical metamaterials have been reported (Connolly et al., Reference Connolly, Polygerinos, Walsh and Bertoldi2015; Jin et al., Reference Jin, Khajehtourian, Mueller, Rafsanjani, Tournat, Bertoldi and Kochmann2020b; Wenz et al., Reference Wenz, Schmidt, Leichner, Lichti, Baumann, Andrae and Eberl2021), which were based on the specific deformation of an element or a group of elements in a predefined sequence to achieve an outcome as a complete mechanism. The simple mechanisms are made of different deformations of basic elements such as elongation (or contraction), torsion, bending, and buckling. The bistable unit cell introduced by Jin et al. (Reference Jin, Khajehtourian, Mueller, Rafsanjani, Tournat, Bertoldi and Kochmann2020b) is an example of a simple mechanism. The release of stored energy in bent thin beams of the unit cell yields rotational rigid body motions of individual unit cells, which results in a wave propagation along with a shape change. In addition, the fibre-reinforced soft fluidic actuators developed by Connolly et al. (Reference Connolly, Polygerinos, Walsh and Bertoldi2015) can also provide a wide range of motions, including axial extension, radial expansion, and twisting by adjusting fibre angle. In addition, multi-step deformation pathways are designed by constraining angles in hierarchical rotating structures of programmable mechanical metamaterials (Li et al., Reference Li, Deng, Grinthal, Schneider-Yamamura, Kang, Martens, Zhang, Li, Yu, Bertoldi and Aizenberg2021). By applying global displacement in programmable mechanical metamaterials with different programming parameters, the target shape can be reached (Wenz et al., Reference Wenz, Schmidt, Leichner, Lichti, Baumann, Andrae and Eberl2021). These examples demonstrate that design parameters play a critical role in variable deformation and that programmable mechanical metamaterials might be able to take advantage of local programming, i.e., shape morphing in a predefined manner to close the crack based on the self-sealing principles of D. cooperi (Coulais et al., Reference Coulais, Teomy, de Reus, Shokef and van Hecke2016; Kamrava et al., Reference Kamrava, Mousanezhad, Felton and Vaziri2018; Janbaz et al., Reference Janbaz, Narooei, Van Manen and Zadpoor2020; Bonfanti et al., Reference Bonfanti, Guerra, Font-Clos, Rayneau-Kirkhope and Zapperi2020; Wenz et al., Reference Wenz, Schmidt, Leichner, Lichti, Baumann, Andrae and Eberl2021).
Inspired by self-sealing in A. macrophylla, in which the sealing cells swell into a fissure (cf. Section ‘Aristolochia macrophylla’), expandable structure design in programmable mechanical metamaterials could offer some possibilities of self-sealing. The kirigami-inspired inflatable structures established by Jin et al. (Reference Jin, Forte, Deng, Rafsanjani and Bertoldi2020a) consists of a kirigami sheet embedded into a thin layer of elastomer and the geometric parameters of the kirigami pattern can be tuned to control the expandable shape. Lipton et al. (Reference Lipton, MacCurdy, Manchester, Chin, Cellucci and Rus2018) designed the auxetic structure that enables expansion while twisting. Such expandable auxetic unit cells with a pre-strain or pre-stress state might be able to be triggered by the occurrence of cracks. As a potential solution to mechanically close the damaged location, the energy should be stored and released by using the designed bistable elements (Raney et al., Reference Raney, Nadkarni, Daraio, Kochmann, Lewis and Bertoldi2016). It is also reported that structural recovery, which is a time-dependent metastable behaviour, can be caused by stress relaxation in the bistable unit cell (Berwind et al., Reference Berwind, Kamas and Eberl2018). Additionally, negative thermal expansion metamaterials have also been designed by Wu et al. (Reference Wu, Li and Zhou2016) and Li et al. (Reference Li, Chen, Li, Cao and Wang2018). This means that filling a form into the crack by an expanded structure might be able to be implemented depending on various service environments.
Another functional principle for self-sealing is that embedded vascular networks or micro-tubules break and release the liquid sealing and healing agent stored inside. This self-sealing principle is found in stems of E. tirucalli (cf. Section ‘Euphorbia tirucalli’), which stores latex in its laticifers under a pressure of up to 8 MPa (Harrington et al., Reference Harrington, Speck, Speck, Wagner and Weinkamer2015; Anandan et al., Reference Anandan, Rudolph, Speck and Speck2018). There are generally the following ways to trigger the release of the healing agent, which applies not only to plants, as it is similar to the ‘bleeding’ mechanism in animals (Toohey et al., Reference Toohey, Sottos, Lewis, Moore and White2007; Trask et al., Reference Trask, Williams and Bond2007). To prevent further blood loss after an injury, vascular endothelial cells constrict first, and blood clots then seals the wounds (Speck and Speck, Reference Speck and Speck2019). Furthermore, inspired by human skin, a three-dimensional vascular network has been designed by Toohey et al. (Reference Toohey, Sottos, Lewis, Moore and White2007), where the repairing agent is delivered from the micro-vascular network through capillary action to close the fissure. Programmable mechanical metamaterials can also combine the advantages of their structure with the transport of materials to guide the sealing agent to reach the location of damage precisely, thus achieving a more effective sealing effect (Wu et al., Reference Wu, Su and Shi2019; Fischer et al., Reference Fischer, Hillen and Eberl2020). It is worth mentioning that guiding cracks within brittle materials is a common materials design to improve toughness and can be found in many fibre composites. For metamaterials, Pham et al. (Reference Pham, Liu, Todd and Lertthanasarn2019) showed that the principles of ‘polycrystalline’ metamaterials can improve the fracture toughness and strength by channelling the collapsing plains to meta grain boundaries. In addition, simply letting the cracks rupture the micro-encapsulation with the repairing agent embedded in it (White et al., Reference White, Sottos, Geubelle, Moore, Kessler, Sriram, Brown and Viswanathan2001) is the main method used for self-sealing and/or self-healing structural engineering materials because it is inexpensive to do so. However, such an approach is often passive and the efficiency of the repairing depends on the position of the micro-encapsulation and the sequence of the release for multiple repairing agents (Fischer, Reference Fischer2010). As a potential optimisation method, Jiang and Li (Reference Jiang and Li2018) proposed an auxetic chiral mechanical metamaterial, which could open the cell in a predefined order. Highly ordered locally deformed bistable mechanical metamaterials under quasi-static compression has also been reported by Zhang et al. (Reference Zhang, Wu, Fang and Zhang2021). This means that the opening of the cells and release of sealing or healing materials can be sequenced according to different external changes, thus improving repair efficiency.
Most of programmable mechanical metamaterials exhibit similar behaviours in one or a few procedures of sealing. However, programmable mechanical materials should make more use of its advantages; for instance, an information processing function may allow programmable mechanical metamaterials to become more proactive in self-sealing (El Helou et al., Reference El Helou, Buskohl, Tabor and Harne2021). Such a signal or information may include the type of damage, whether the self-sealing function should be activated and the selection of the optimum self-sealing method, etc. Therefore, to improve the efficiency of self-sealing for technical applications, it should not be limited to the one-to-one aforementioned correspondence. According to the application scenario, flexible combinations of different forms may create more optimised solutions for the self-sealing of technology applications based on the current manufacturing techniques and available materials.
Programmable mechanical metamaterials framework
Compared to traditional artificial functional systems, living nature can self-seal and/or self-heal repeatedly and more flexibly on multiple scale lengths. Table 11 shows a comparison of hierarchy levels in plants, animals (Speck and Speck, Reference Speck and Speck2019), and in the inanimate world. Although the details of the self-sealing mechanisms of plants and animals are different, some similarities can still be found. For the inanimate world, material classes influence the mechanical properties of the metamaterial unit cells and consequently of the metamaterial itself. With the increase in complexity of interaction (Fischer et al., Reference Fischer, Hillen and Eberl2020), a certain number of the unit cells of mechanical metamaterials are introduced to ensure that the higher level of hierarchies behave like a homogeneous continuum. In the future, the programmable behaviour will be implemented by integrating modules of programmable materials that represent various principles. As one example, topological locking can be used to integrate damage detection, information processing, and self-sealing function, etc. as modules (Kamrava et al., Reference Kamrava, Mousanezhad, Ebrahimi, Ghosh and Vaziri2017). Hence, to develop and implement programmable mechanical metamaterials with the self-sealing function effectively, the selection and design for each hierarchy level becomes critical.
Table 11. Hierarchy level in plants, animals, and programmable mechanical metamaterials systems.

Furthermore, programmable mechanical metamaterials with internal or external triggers constitute self-sealing behaviour. Although the onset of self-sealing in the above-mentioned three model plants (cf. Sections ‘Introduction of the flow charts’, ‘Delosperma cooperi’, and ‘Aristolochia macrophylla’) was mainly triggered by disturbing the equilibrium of the system in a stable minimum energy level, the potential for self-sealing triggers should not be limited to this. For example, the first opening triggered by temperature and the second opening triggered by water was reported in Banksia (Eder et al., Reference Eder, Amini and Fratzl2018; Huss et al., Reference Huss, Schoeppler, Merritt, Best, Maire, Adrien, Spaeker, Janssen, Gladisch, Gierlinger, Miller, Fratzl and Eder2018a, Reference Huss, Spaeker, Gierlinger, Merritt, Miller, Neinhuis, Fratzl and Eder2018b). Although they were not designed to trigger the closure of a crack in living nature, these principles could provide inspiration for self-sealing in engineering. Hence, various triggers, or a combination thereof, should also be adopted to allow the responses of programmable mechanical metamaterials for self-sealing. Since the electricity is relatively controllable in various environmental situations and also can be stored easily, it is one of the more feasible solutions for actuating different types of deformations, that is, it has the potential to promote the self-sealing procedure. There are a lot of possibilities in using electricity as an external or internal triggering system by implementing electro-responsive materials inside the system. Piezoelectric materials are one of the most well-known electro-responsive materials, which are capable of converting mechanical and electrical energies to each other. By implementing the piezoelectric materials inside the metamaterial’s structures, specific tunable electromechanical properties could be reached (Yang et al., Reference Yang, Li, Xin, Gao, Yuan, Wang, Yu, Wang, Zhou and Dong2019b). In addition, by utilising the piezoelectric effect in structured metamaterials, energy could be collected more efficiently than through conventional methods (Lee et al., Reference Lee, Lee, Park, Jang, Kim and Rho2022). In addition to electricity, other triggers can also be found. Zhang et al. (Reference Zhang, Guo, Wu, Fang and Zhang2018) have designed a shrinkable network by utilising the hydraulic swelling deformation of the hydrogel. In addition, Li et al. (Reference Li, Deng, Grinthal, Schneider-Yamamura, Kang, Martens, Zhang, Li, Yu, Bertoldi and Aizenberg2021) also reported a cellular structure that allows topological transformation via the capillary force. Because the programmable shape can be activated by different types of triggers, such as magnetic fields (Kim et al., Reference Kim, Yuk, Zhao, Chester and Zhao2018), pH (Ding et al., Reference Ding, Wei and Ziaie2010), temperature, and humidity (Erb et al., Reference Erb, Sander, Grisch and Studart2013), self-sealing in programmable mechanical metamaterials may occur once the predefined environmental conditions of the whole systems have changed by damage.
Nevertheless, there is a lot of room for growth in the field of programmable mechanical metamaterials that can self-seal, and still some issues that need to be addressed. For example, how much time is available for self-sealing in technical applications? Although self-sealing is relatively fast compared to self-healing in plants, even faster self-sealing is still the pursuit when considering the possible application scenarios for programmable mechanical metamaterials, such as a leaking kayak in the lake or a cracked airplane component. In addition, the auxetic unit cell with a pre-strain or pre-stress state seems to be a preferred choice for self-sealing inspired by A. macrophylla. However, we still urgently need to solve the problem of long-term storage of energy. Also, as the programmable mechanical metamaterial system for self-sealing becomes more complex, cost will increase accordingly. Selecting the appropriate processing module, that is, information processing for different applications, is also a question worth considering in the future. But we believe that with the improvement of manufacturing methods and the design of different forms of structure, the toolbox of programmable mechanical metamaterials will become more and more abundant; in turn, this will bring us one step closer to achieving widespread application of programmable mechanical metamaterials that can self-seal.
Conclusion
In order to accelerate the transfer of biological principles in general, and in particular, self-sealing, into the inanimate engineering world, we require common understanding of concepts between biology and technology. The authors have therefore agreed, that self-sealing occurs immediately after damage, resulting in a fissure that is functionally repaired but still present and the mechanical properties in the damage area have not yet been restored.
With respect to possible evolutionary advantages of self-sealing in plants, we can only hypothesise, because there is no experiment to verify an advantage. We assume that rapid wound sealing prevents dehydration, protects against invading pathogens, and extends the lifetime of individual plants; and thus increases the number of offspring. During biological evolution a variety of self-sealing functional principles have been developed that, for example, depend on the body plan of the plants (e.g., presence of latex or mucilage) or the environmental conditions (e.g., melting of wax above a certain ambient temperature). Consequently, the self-sealing process and the underlying functional principles are very diverse in the plant species studied so far. For simple geometries, the principles of self-sealing can be described with analytical models that not only represent the behaviour acquired from experiments but also predict the behaviour for different circumstances. For complex geometries, numerical models have proven to be successful, but require that a large amount of experimental data to be available (e.g., well resolved cell structures, local mechanical properties, or turgor). While such models are very useful to describe specific plant models in a realistic way, they lack the ability to formally describe the underlying principles and mechanisms. Therefore, transferring principles from biological models into technological applications requires another level of abstraction. Describing the functions of biological models and their underlying functional principles as process flow diagrams, allows us to convert detailed biological insights into sequential step-wise algorithms, which turns the focus on building blocks necessary to achieve specific functions. Furthermore, the individual and independent blocks and steps of the algorithms allow additional features to be inserted or unnecessary features to be removed from the design process without having to redo the complete procedure from scratch. Nevertheless, there are some challenges for the future. Since each discipline has its own terminology and also its own way of thinking, it is necessary for scientists to collaborate in an open-minded way. The interface between biology and engineering can be the joint development of flow charts, analytical and numerical models, which will not only allow engineers to innovate, but also will allow biologists to gain a deeper understanding of their biological models (reverse biomimetics). However, the level of detail to which algorithms must be described in order to transfer knowledge between the two fields must, at least at the beginning, be negotiated on a case-by-case basis. For the engineering community, it is clear, that translating bio-inspired algorithms into a sequence of (physical or mechanical) mechanisms is still a rather tedious and difficult task. Therefore, our review of potential applications shows rather individual solutions for singular problems. As discussed, a framework that classifies metamaterial mechanisms in terms of their participation as a subset of the algorithm (depending on boundary conditions, e.g., processing limitations) would simplify the development of such systems tremendously.
The digital transformation of science is also paying into this effort, as it strongly builds on semantic techniques to connect the various scientific disciplines. The different domains, for example, biology and materials science, need to (further) develop their own taxonomy and concepts to build up domain ontologies. Such strong semantics will benefit from a shared understanding at the interface so that neighbouring ontologies can be mapped onto each other. While in biology, (too) many application ontologies are known and need to be joined, in engineering, ontologies are still being developed. Nevertheless, both disciplines will benefit from a shared taxonomy and concepts.
Glossary
-
• Acclimation: Acclimation of individual plants to environmental constraints takes place over a time period of days and weeks resulting in changes of their morphological, anatomical, and mechanical properties (Badel et al., Reference Badel, Ewers, Cochard and Telewski2015).
-
• Adaptation: In a biological context, adaptation is the result of genetic change in populations over an evolutionary time (Lambers et al., Reference Lambers, Chapin and Pons2008).
-
• Adaptive system: Adaptive means having the ability to control the system’s adaptation to different situations, that is, the correlation between structure, function or behaviour and its environment, to increase its efficiency to achieve its goals (Martín H et al., Reference Martín H, de Lope and Maravall2009).
-
• Algorithm: A step-by-step procedure for solving a problem or accomplishing some end (Merriam-Webster Online Dictionary, 2022a)
-
• Auxetic: Auxetic structures or materials exhibit a negative Poisson’s ratio. When auxetic structures or materials are stretched (or compressed), they become thicker (or thinner) perpendicular to the applied force (Berwind et al., Reference Berwind, Kamas and Eberl2018).
-
• Bio-inspiration: Transfer of an idea derived from living organisms into a technical application (Speck et al., Reference Speck, Speck, Horn, Gantner and Sedlbauer2017).
-
• Biomimetics: Transfer of a functional principle derived from living organisms into a technical application (ISO:18458, 2015; Speck et al., Reference Speck, Speck, Horn, Gantner and Sedlbauer2017).
-
• Function: In a technical context being understood in the sense of a specific process, action or task (Achinstein, Reference Achinstein1977) and in a biological context being understood in the sense of traits evolved to contribute to fitness (Walsh, Reference Walsh1996).
-
• Functionality: The quality or status of being functional (Merriam-Webster Online Dictionary, 2022b).
-
• Geometry: Examples for 2D or cross-sectional geometry are circle, ellipse, square, and triangle. Examples for 3D geometry are cylinder, cube, sphere, pyramid, and cone (Niklas, Reference Niklas1994).
-
• Mechanism: In biology, the concept of mechanism has three distinct meaning, which ‘may refer to a philosophical thesis about the nature of life and biology (mechanism), to the internal workings of a machine-like structure (machine mechanism), or to the causal explanation of a particular phenomenon (causal mechanism)’ (Nicholson, Reference Nicholson2012). In a technical context, mechanism is a process or system that is used to produce a particular result (Ross et al., Reference Ross, McEvilley and Oren2016).
-
• Metamaterials: Human-made materials structured on a mesoscopic level with exceptional properties attributable to the geometry and connection of the unit cells (Rafsanjani et al., Reference Rafsanjani, Akbarzadeh and Pasini2015; Kelkar et al., Reference Kelkar, Kim, Cho, Kwak, Kang and Song2020).
-
• Programmable materials: Human-made materials with integrated tunable functions and logical conditions (e.g., if) (Wenz et al., Reference Wenz, Schmidt, Leichner, Lichti, Baumann, Andrae and Eberl2021).
-
• Response: Immediate response of plants such as wind-induced reconfiguration of leaves, branches, or entire plants occurs within seconds to days (Telewski, Reference Telewski2021).
-
• Self-healing: Longer-lasting self-healing phase (after self-sealing), in which the fissures are structurally repaired and thus no longer present, while the mechanical properties in the damage area are (at least partially) restored (Harrington et al., Reference Harrington, Speck, Speck, Wagner and Weinkamer2015; Speck et al., Reference Speck, Schmauder, Speck and Paul-Victor2020).
-
• Self-repair: Generic term that encompasses self-sealing and self-healing in biological and technical systems (Harrington et al., Reference Harrington, Speck, Speck, Wagner and Weinkamer2015; Speck et al., Reference Speck, Schmauder, Speck and Paul-Victor2020).
-
• Self-sealing: Self-sealing takes place immediately after the damage, resulting in a still present fissure that is functionally repaired, but the mechanical properties in the damage area have not yet been restored (Harrington et al., Reference Harrington, Speck, Speck, Wagner and Weinkamer2015; Speck et al., Reference Speck, Schmauder, Speck and Paul-Victor2020).
-
• Shape: A natural variable that has a magnitude but lacks a unit (Niklas, Reference Niklas1994). Examples for this dimensionless quantity are the aspect ratio, the tapering mode or the ratio of axial and polar second moment of area.
-
• Size: A substantial variable that has a magnitude and can be expressed in units of a physical quantity (e.g., height, diameter, mass) or in units of a derived physical quantity (e.g., volume) (Niklas, Reference Niklas1994).
-
• Spinodoid topologies: Spinodoid topologies are characterised by smooth, non-intersecting surfaces with virtually zero mean curvature (Kumar et al., Reference Kumar, Tan, Zheng and Kochmann2020).
-
• Unit cell: A unit cell is a fundamental repeating building block in mechanical metamaterials that exhibits specific mechanical properties or functionalities (Berwind et al., Reference Berwind, Kamas and Eberl2018).
Supplementary material
The supplementary material for this article can be found at https://doi.org/10.1017/pma.2023.11.
Acknowledgements
We thank Laura Mahoney for providing proofreading and editing.
Funding statement
This article is partly funded by the Deutsche Forschungsgemeinschaft (DFG, German Research Foundation) under Germany’s Excellence Strategy – EXC-2193/1 – 390951807. C.E. acknowledges partial funding provided by the Fraunhofer Cluster of Excellence Programmable Materials. N.G. acknowledges partial funding by the Zeiss Cluster Scharf.
Author contributions
B.C.: Writing – original draft; N.G.: Writing – original draft, visualisation, exemplary implementation through simulations and experiments; O.S.: Supervision, writing – original draft of plant models and biomimetic applications, writing – review and editing of the entire manuscript; C.E.: Conceptualisation, funding acquisition, supervision.